L’impression 3D au service de l’aéronautique
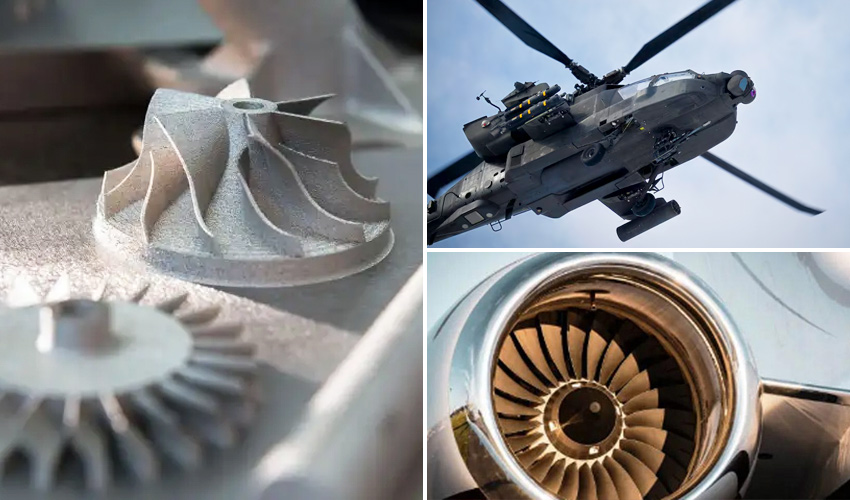
La fabrication additive permet de produire des pièces légères, solides et géométriquement complexes. Cette technologie est donc particulièrement appréciée dans le secteur aéronautique, où l’optimisation de la résistance et du poids est essentielle. L’aéronautique est la science et la pratique de la conception, de la construction et du pilotage de tous les aéronefs, à l’exception de ceux qui vont dans l’espace. Ce secteur a été l’un des premiers à adopter la fabrication additive, l’utilisant initialement pour le prototypage rapide. Aujourd’hui, cependant, ses applications se sont étendues pour inclure des pièces d’utilisation finale dans les avions, les hélicoptères, les drones et bien plus encore. Pour illustrer la polyvalence et l’impact des technologies 3D dans ce domaine, nous avons choisi quelques applications aéronautiques qui ont recours à l’impression 3D, la liste n’étant évidemment pas exhaustive.
Norsk Titanium fournit des pièces pour le Boeing 787
Norsk Titanium US Inc, une entreprise leader dans le domaine de la fabrication additive de titane et active dans l’industrie aérospatiale, a déjà fourni des pièces pour le Boeing 787 Dreamliner en 2021. Norsk est surtout connue pour sa technologie brevetée Rapid Plasma Deposition®, qui améliore la résistance et la durabilité de la pièce finie et fonctionne de manière similaire au dépôt de matière sous énergie concentrée (DED). Mais contrairement à cette dernière, Norsk utilise un faisceau d’électrons qui permet de chauffer la poudre à plusieurs endroits en même temps. Parmi les pièces produites figuraient des composants en titane imprimés en 3D, qui ont été certifiés par la FAA (Federal Aviation Administration). L’entreprise a maintenant conclu un accord pour fournir directement des pièces de production en série à The Boeing Company, ce qui marque le début d’une relation de fournisseur direct. Norsk Titanium prévoit de fournir des centaines de pièces structurelles d’ici 2025.
ITP Aero obtient la certification EASA pour des composants 3D
Basée en Biscaye, ITP Aero a obtenu la certification de l’Agence européenne de sécurité aérienne (EASA) et de l’Agence nationale espagnole de sécurité aérienne (AESA) pour des composants structurels imprimés en 3D. L’entreprise est la première de l’industrie des moteurs aéronautiques à recevoir ces approbations pour des pièces fabriquées par frittage sélectif par laser (SLS), appliquées aux pales arrière du moteur TP400. Ce processus industriel de fabrication additive permet de créer des composants complexes en utilisant moins de matériaux et d’énergie, ce qui contribue à la durabilité du secteur. En outre, ITP Aero a développé ses propres normes et spécifications de fabrication additive pour les composants de moteurs aéronautiques à haute température. L’entreprise dispose d’une cellule de fabrication dédiée et construit le centre de recherche « ADMIRE » pour faire progresser les technologies de fabrication numérique et durable.
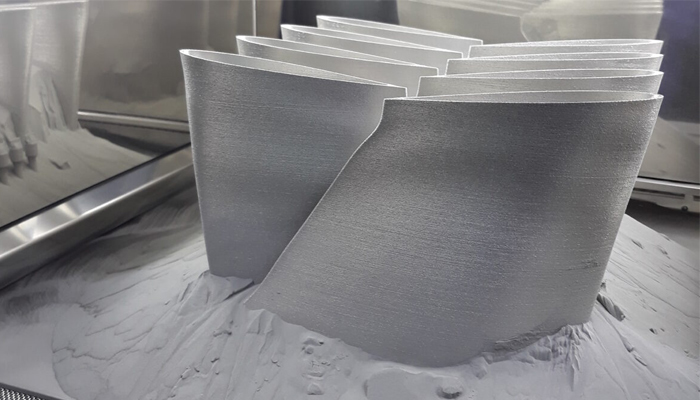
Crédits photo : ITP Aero
Safran a investi 80 millions d’euros dans son campus d’impression 3D
Ce n’est pas vraiment une application de l’impression 3D dans l’aéronautique mais il était difficile de passer à coté du groupe Safran. Opérant dans les secteurs de l’aéronautique, de l’espace et de la défense, le géant français a investi 80 millions d’euros pour ouvrir un centre dédié à la fabrication additive au Haillan, près de Bordeaux. L’objectif est de créer un grand centre d’excellence pour la fabrication additive. Le campus, qui accueille environ 200 employés spécialisés dans l’impression 3D, s’étend sur environ 12 500 mètres. Il abrite au moins huit imprimantes 3D utilisant la fusion sur lit de poudre, des équipements de finition, deux fours de traitement thermique, un microscope électronique à balayage, un laboratoire métallurgique et un laboratoire de poudres. L’objectif de Safran est d’intégrer la fabrication additive dans les composants de ses moteurs dans une proportion de 1 à 25 %. La société a déjà produit plus de 1 000 pièces imprimées en 3D et prévoit de produire plus de 4 000 pièces avec cette technologie en 2022 et plus de 8 000 en 2023.
Materialise développe des solutions de cabines imprimées en 3D avec ses partenaires
Materialise a élargi son rôle dans le secteur de la maintenance, de la réparation et de la révision (MRO) de l’industrie aérospatiale et travaille désormais avec Proponent, le plus grand distributeur mondial de produits aérospatiaux, et Stirling Dynamics, une organisation de conception de premier plan certifiée EASA 21.J, pour développer des solutions de cabine imprimées en 3D. Auparavant, Materialise avait déjà produit avec succès des pièces imprimées en 3D pour l’avion A350, dont une centaine de pièces ignifugées, dans le cadre d’un partenariat avec Airbus et EOS. L’objectif du nouveau partenariat est maintenant de fournir des pièces de rechange imprimées en 3D certifiées pour l’industrie aéronautique. Stirling Dynamics se concentre ici sur l’amélioration des designs des pièces intérieures de cabine, tandis que Materialise utilise ses capacités de production certifiées. « Grâce à notre expertise combinée, nous réduisons les obstacles à l’introduction de la fabrication additive dans l’aéronautique et proposons des solutions certifiées pour le marché des pièces de rechange », explique Jurgen Laudus, vice-président de Materialise Manufacturing. La collaboration a déjà donné naissance à plusieurs solutions de réparation de cabine visant à résoudre des problèmes spécifiques dans les cabines d’avion. Proponent, en particulier, a joué un rôle clé à cet égard en travaillant avec les OEM pour proposer ces solutions dans le monde entier.
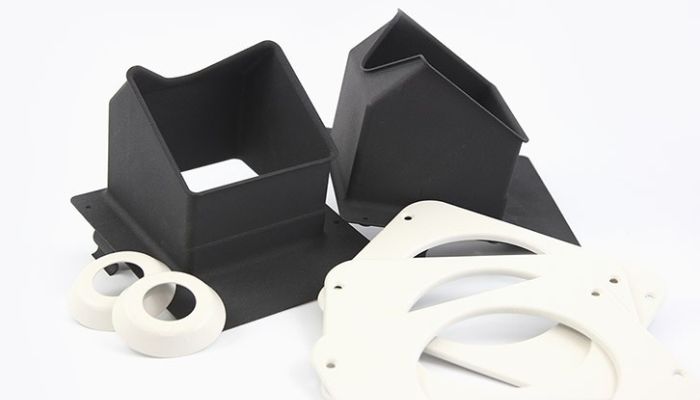
Pièces adaptées au vol imprimé avec un matériau ignifugé PA 2241 FR, proposé par Materialise et certifiée Airbus (crédits photo : Materialise)
Lufthansa utilise l’impression 3D pour créer des pièces de cabine pour ses avions
Lufthansa Technik, l’un des principaux fournisseurs de services de maintenance, de réparation, de révision et de modification d’avions civils, a déclaré qu’il utilisait la fabrication additive polymère à la fois pour redessiner des pièces de cabine spécifiques et pour reproduire des pièces d’avion conventionnelles. En fait, Lufthansa utilise l’impression 3D pour personnaliser les cabines des passagers VIP. L’impression 3D est également utilisée pour renforcer ou alléger les composants des cabines d’avions de ligne classiques. Lufthansa a déjà amélioré la fonction des grilles de ventilation, des clips et des couvercles de ses avions. Lufthansa prévoit d’utiliser de plus en plus la fabrication additive, notamment tout ce qui touche à la conception bionique. Il s’agit en fait de l’application de méthodes biologiques aux technologies d’impression 3D. Selon la compagnie, les ajustements apportés à la conception de la cabine et la réduction du poids grâce à la fabrication additive peuvent contribuer de manière significative aux efforts de l’industrie aéronautique en faveur d’une plus grande durabilité et d’une réduction de l’empreinte carbone.
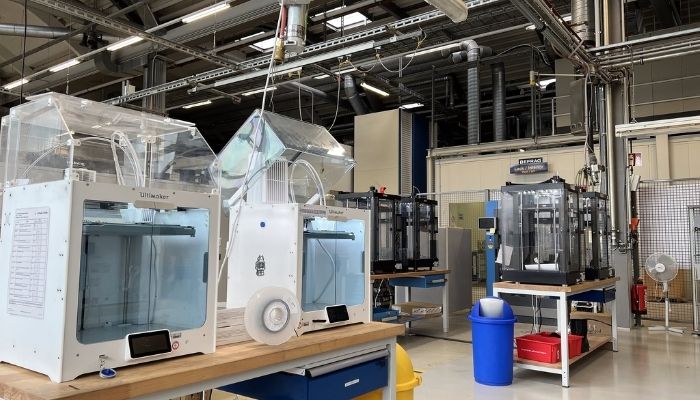
Le centre d’impression 3D de la compagnie aérienne (crédits photo : Lufthansa)
Le centre d’impression 3D d’Airbus Helicopters
Airbus n’est pas étranger à l’impression 3D, puisque la société intègre des pièces imprimées en 3D dans ses avions depuis des années. Souvent, elle a externalisé des services de fabrication additive, mais fin 2023, Airbus Helicopters a ouvert son propre centre d’impression 3D sur son site de Donauwörth, en Allemagne, élargissant ainsi ses capacités internes en matière de fabrication additive. Le centre dispose de trois machines pour les pièces en titane, quatre pour le plastique et une pour l’aluminium. Airbus Helicopters utilise cette technologie pour créer des pièces de série, ainsi que des pièces pour des prototypes tels que CityAirbus NextGen eVTOL et l’hélicoptère expérimental à grande vitesse Racer. Stefan Thomé, directeur général d’Airbus Helicopters pour l’Allemagne, a expliqué les avantages de l’utilisation de l’impression 3D : « Entre autres avantages, elle peut réduire le poids des composants d’un aéronef, ce qui se traduit par une diminution de la consommation de carburant. Un tel potentiel peut apporter des avantages financiers et contribuer à réduire les émissions de CO2 pendant les opérations. »
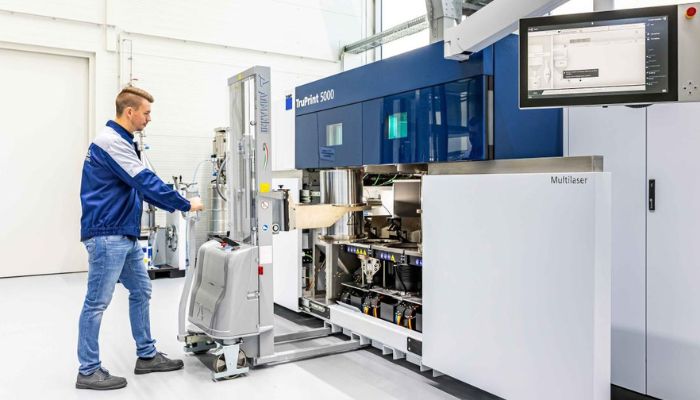
Crédits photo : Airbus
Rotors 3D pour les hélicoptères Apache de Boeing
Boeing a commencé à tester un système complet de rotor principal imprimé en 3D pour l’hélicoptère d’attaque AH-64 Apache. Ce projet vise à réduire les délais et à améliorer les chaînes d’approvisionnement pour les pièces normalement forgées. Lors de la conférence annuelle de l’Association of the US Army, Boeing et ASTRO America ont dévoilé leur premier composant imprimé en 3D. Il s’agit d’une tringlerie de rotor principal, fabriquée sur une imprimante 3D métal grand format. La société ASTRO, financée par le gouvernement, a travaillé sur un contrat de 95 millions de dollars visant à développer des capacités de fabrication additive pour des pièces de grande taille, telles que des coques de chars d’assaut. Un composant de rotor principal imprimé en 3D a été produit en huit heures, alors qu’il faudrait normalement un an pour le forger. Boeing souhaite réaliser des essais de fatigue à grande échelle sur ces pièces, ce qui pourrait accélérer la réparation des avions et optimiser la fabrication des pièces.
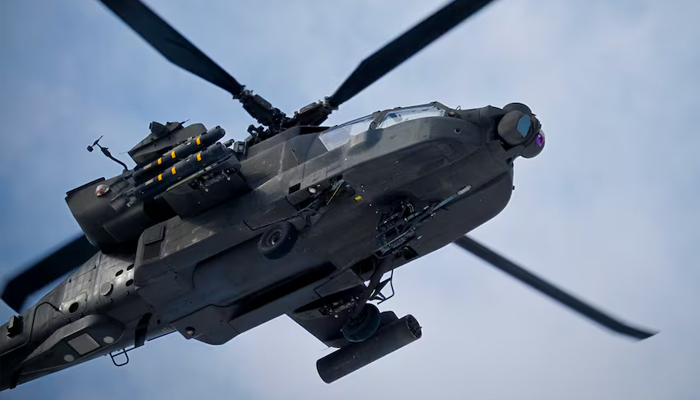
Crédits photo : Boeing
Finnair utilise des pièces imprimées en 3D dans ses avions A320
Vous souvenez-vous des moniteurs vidéos rabattables présents dans certains avions ? De nombreuses compagnies aériennes, dont la compagnie finlandaise Finnair, les suppriment progressivement. La compagnie les a récemment remplacés par des panneaux d’obturation imprimés en 3D (panneaux utilisés pour couvrir les « trous » de l’espace inutilisé) dans les cabines de ses Airbus A320, afin d’offrir une alternative légère aux lourds lecteurs vidéo. La société de fabrication additive AM Craft a créé plus de 300 panneaux d’obturation pour moderniser 17 des avions A320 de Finnair. Selon la compagnie aérienne, l’impression 3D des panneaux a permis de minimiser les stocks excédentaires et de réduire les coûts associés à la chaîne d’approvisionnement traditionnelle. De plus, Aviation Week rapporte que les panneaux ont été conçus pour fonctionner avec les rails de montage existants afin de faciliter l’installation. Enfin, toute compagnie aérienne possédant des avions A320 pourrait bénéficier de ce projet d’impression 3D, car les panneaux d’obturation sont disponibles dans le catalogue numérique d’AM Craft.
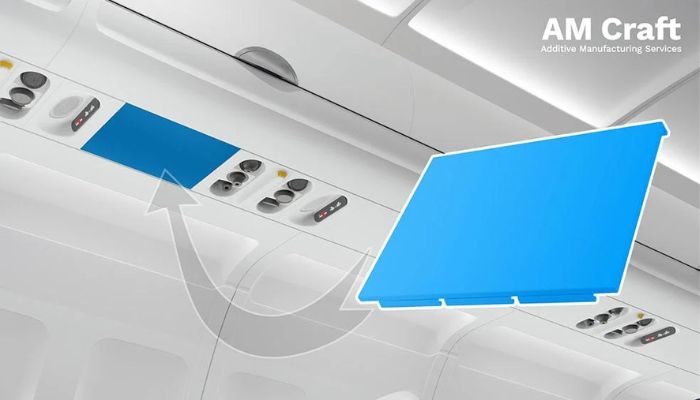
Crédits photo : AM Craft
Liebherr-Aerospace Lindenberg GmbH produit un arbre flexible imprimé en 3D
Liebherr-Aerospace Lindenberg GmbH, une entreprise qui fabrique des systèmes intégrés pour l’industrie aéronautique, vient de développer un arbre flexible pour des applications aéronautiques en utilisant la fabrication additive. Traditionnellement, celui-ci se compose de sept éléments qui doivent être reliés entre eux par des processus complexes. L’utilisation de l’impression 3D simplifie ce processus, ce qui réduit les besoins en maintenance et rend la production moins complexe. L’arbre flexible imprimé en 3D à partir de poudre de titane, dont la production en série a été approuvée par Airbus et l’AESA, doit être intégré dans l’engrenage différentiel du système de volets de l’Airbus A350. Il transmet ici les mouvements de rotation à un capteur de position et aide à compenser les erreurs d’angle et d’axe entre le réducteur et le capteur. L’approbation de l’arbre flexible imprimé en 3D souligne que la fabrication additive est une technologie fiable pour améliorer la durabilité dans l’aviation. « L’arbre flexible montre comment différentes fonctions peuvent être intégrées efficacement dans une pièce, ce qui ouvre la voie à des applications aéronautiques conçues par impression 3D plus complexes à l’avenir », explique Svenja Pestotnik, responsable de la fabrication additive chez Liebherr-Aerospace Lindenberg GmbH.
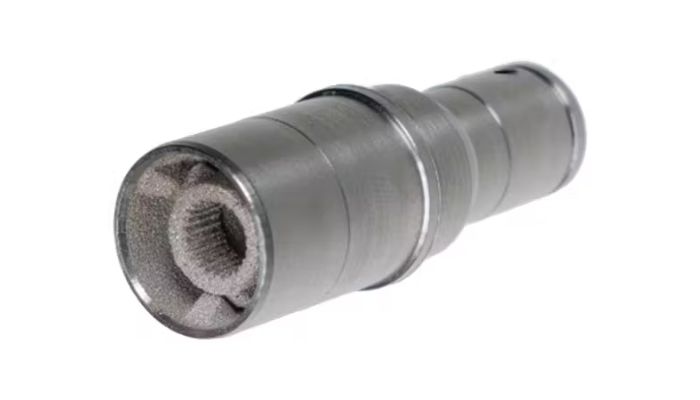
L’arbre flexible présente une construction plus complexe et est produit à partir de poudre de titane déposée couche par couche (crédits photo : Liebherr-Aerospace)
LEAP et la fabrication additive
Difficile de passer à côté de LEAP quand on parle d’aéronautique et d’impression 3D. Conçu par CFM International, une société commune entre GE Aerospace et Safran Aircraft Engines, il s’agit d’un système de propulsion pour avions commerciaux (comme le Airbus A320neo ou le Boeing 737 MAX) qui a été lancé en 2016. Ses objectifs premiers étaient de réduire le rendement énergétique, les émissions de CO2 ainsi que le bruit. A l’aube de ses 10 ans, LEAP a tenu ses promesses selon CFM. Mais ce qui nous intéresse est bien évidemment la partie impression 3D. Le système de propulsion a effet été conçu en partie grâce à la fabrication additive, notamment les carénages de turbine, les embouts de tuyère ou encore les injecteurs de carburant. Un procédé de fusion laser sur lit de poudre a été privilégié.
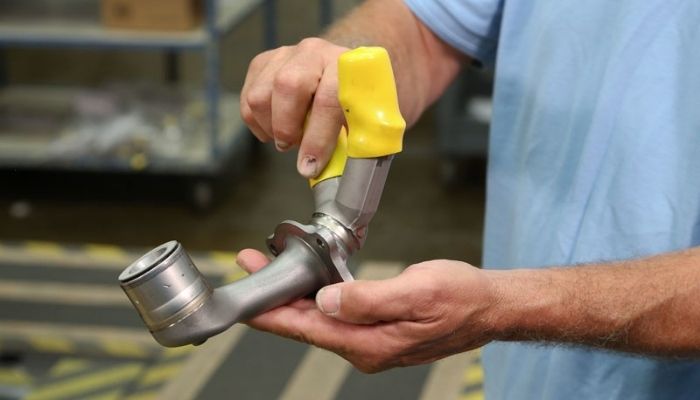
Crédits photo : GE
Les Marines améliorent l’efficacité de la maintenance de l’alésoir du F-35B Lightning II
L’objectif du Marine Aviation Logistics Squadron 13 est de fournir un soutien logistique au Marine Aircraft Group, tel que l’approvisionnement en personnel et en pièces détachées. Cependant, en juillet 2024, le MALS-13 a dû faire face à une grave pénurie d’alésoirs pour les escadrons du F-35B Lightning II. Il s’agit d’outils de coupe de précision essentiels pour la maintenance aéronautique. Les alésoirs conventionnels étaient coûteux et MALS-13 ne disposait pas de quantités suffisantes en raison des longs délais d’approvisionnement. Grâce à la fabrication additive, ils ont créé une solution à la demande en développant des alésoirs haute performance. Ce faisant, ils ont non seulement réduit les coûts de maintenance de plus de 50 %, mais aussi les délais d’approvisionnement. Les pièces sont passées d’une disponibilité de trois mois à une production le jour même. Pour recréer les alésoirs manquants, deux imprimantes 3D industrielles Markforged X7 ont été achetées, ce qui a permis à MALS-13 de produire les composants de qualité aérospatiale en interne, éliminant ainsi la dépendance à l’égard des fournisseurs externes.
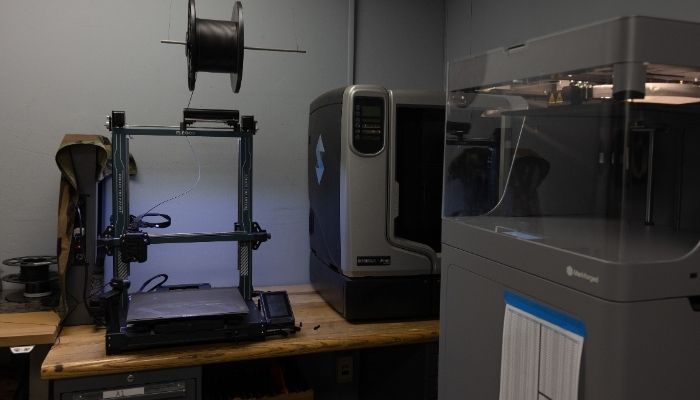
Crédits photo : Lance Cpl. Elizabeth Gallagher
Titan Falcon, le drone conçu par impression 3D
Quand on parle d’aéronautique, on ne peut pas passer à côté des véhicules aériens sans pilote, plus communément appelés drones. Quelle que soit leur utilisation – exploration, militaire, recherche, etc. – ils sont de plus en plus nombreux et peuvent intégrés des pièces imprimées en 3D. C’est le cas du Titan Falcon développé par Titan Dynamics. Il a une autonomie de 6 heures et un rayon d’action de 400 kilomètres ce qui lui permet de couvrir une large zone. Équipé d’une caméra, c’est une solution idéale pour surveiller des champs de bataille – il a d’ailleurs été utilisé lors du conflit opposant l’Ukraine et la Russie. En ce qui concerne la fabrication additive, l’entreprise reste mystérieuse quant aux matériaux et à la technologie employés mais ce qui est sûr, c’est qu’elle a permis de réduire les délais et de faciliter les itérations.
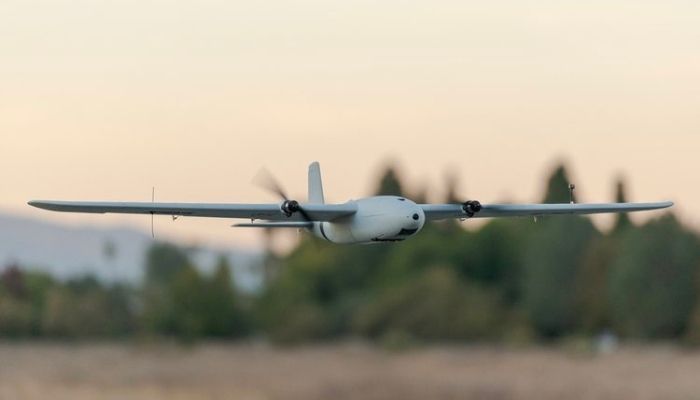
Crédits photo : Titan Dynamics
Conflux fabrique des échangeurs de chaleur par impression 3D métal
Conflux s’est donné pour mission de contribuer à l’aviation moderne par le biais de l’impression 3D. Celle-ci est confrontée à la nécessité d’améliorer les performances et la fiabilité. Conflux fabrique des échangeurs de chaleur pour avions par impression 3D métal afin de réaliser des géométries plus complexes et d’optimiser ainsi les performances des échangeurs de chaleur. Cela contribue à la performance globale de l’avion. D’une part, le poids total peut être réduit grâce à des composants légers, d’autre part, une gestion thermique efficace se répercute directement sur les performances et l’autonomie d’un avion.
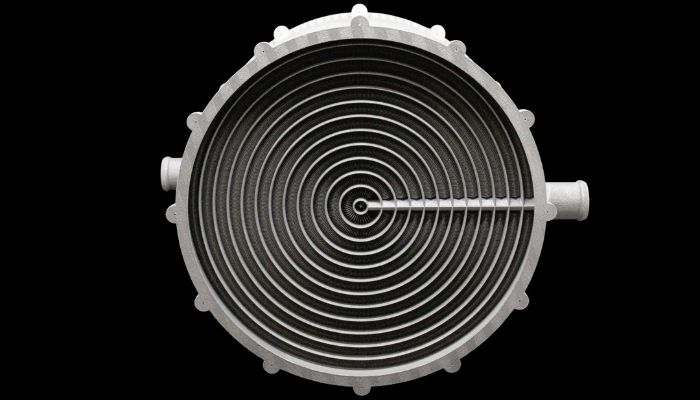
Crédits photo : Conflux
Cockpit d’hélicoptère imprimé en 3D pour un simulateur de vol intégral
En 2024, Murtfeldt Additive Solutions a imprimé un cockpit d’hélicoptère modulaire pour le compte de Reiser Simulation and Training GmbH. Pour ce faire, Murtfeldt a utilisé l’imprimante 3D grand format Queen 1 de Q.BIG 3D. Grâce au procédé VFGF (variable fused granulate fabrication), les différents composants ont pu être imprimés en 3D et assemblés rapidement. Le temps d’impression le plus long pour un seul composant a été de 100 heures et la production totale d’un peu plus d’un mois. Avec ses dimensions de 2 260 mm x 1 780 mm x 17,05 mm, le cockpit ne pèse « que » 200 kilogrammes. L’impression 3D de granulés s’est révélée précieuse dans ce projet pour atteindre des objectifs de construction légère et pour produire de manière plus économique. Étant donné que la fabrication traditionnelle d’un tel projet nécessite de nombreux outils, l’impression 3D a permis de diminuer les coûts.
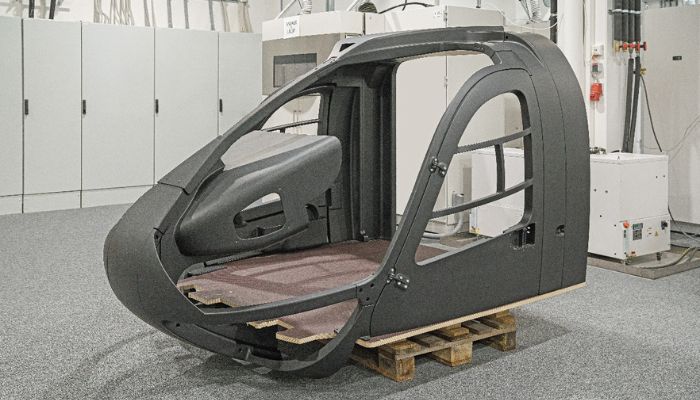
Crédits photo : Q.BIG 3D
Partenariat entre BEAMIT et Leonardo Aircraft pour la production de masse par fabrication additive
Le groupe italien Leonardo est l’un des principaux acteurs internationaux dans la réalisation d’hélicoptères, opérant également dans les secteurs de l’aérospatiale, de la défense et de la sécurité. L’entreprise est un partenaire technologique des gouvernements, des administrations de la défense, des institutions et des entreprises. L’utilisation de la fabrication additive dans les activités de Leonardo est bien connue depuis longtemps. Ces dernières années, dans la division Aircraft en particulier, Leonardo a renouvelé un partenariat avec le service BEAMIT pour la production en série de divers composants avec la technologie de fabrication additive métal, qui sera actif jusqu’en 2028 au moins. À ce jour, Leonardo Aircraft dispose de plus de 100 pièces qualifiées BEAMIT qui sont actuellement installées sur des avions clés tels que le M345, le M346 et le C27J.
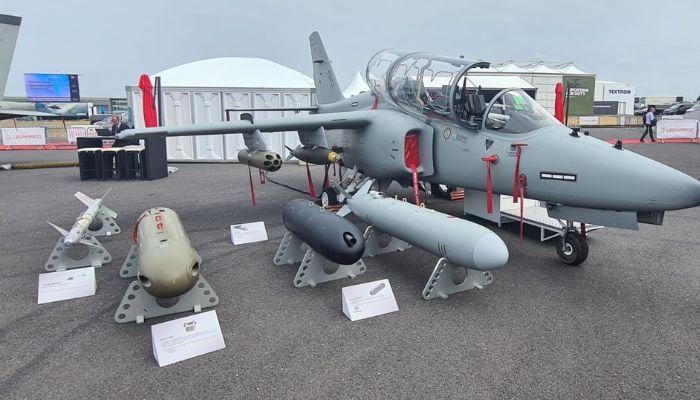
Le Leonardo M-345 (crédits photo : Italia Vola)
Le projet MIMOSA pour optimiser les avions grâce à l’impression 3D
Le projet européen MIMOSA, impliquant divers partenaires institutionnels et corporatifs, a été lancé en 2022 et vise à transformer la construction aéronautique grâce à l’utilisation conjointe de matériaux composites et de métaux imprimés en 3D. Le projet a pour objectif de soutenir les prochaines générations d’avions, qui devront nécessairement suivre des critères de production avec un impact environnemental réduit et un besoin moindre en matières premières. L’étude est basée sur la réalisation de structures multi-matériaux composées d’alliages métalliques et de matériaux composites sans éléments intermédiaires, grâce à l’intégration de la fabrication additive métallique, des traitements de surface au plasma et des fibres de carbone. Les structures réalisées avec la technologie MIMOSA peuvent être régénérées grâce à un processus d’« atomisation », réduisant ainsi les déchets et devenant une matière première « secondaire » pour les processus de fabrication additive eux-mêmes.
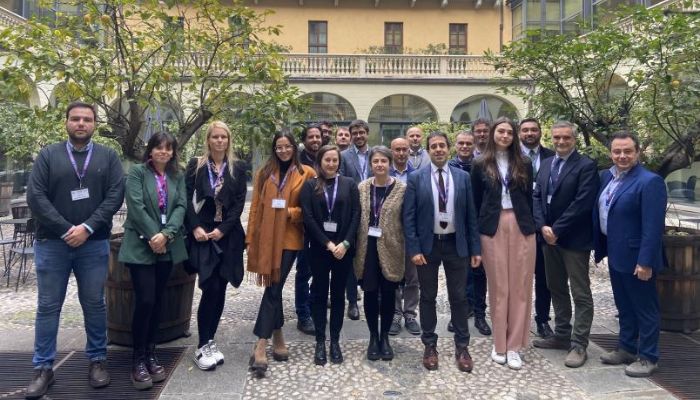
L’équipe du projet (crédits photo : Institut Polytechnique de Turin)
Que pensez-vous de l’usage de l’impression 3D dans l’industrie aéronautique ? N’hésitez pas à partager votre avis dans les commentaires de l’article. Vous êtes intéressés par l’actualité de l’impression 3D dans l’aérospatiale et la défense ? Cliquez ICI. Vous pouvez aussi nous suivre sur Facebook ou LinkedIn !