Les implants imprimés en 3D : découvrez quelques projets innovants
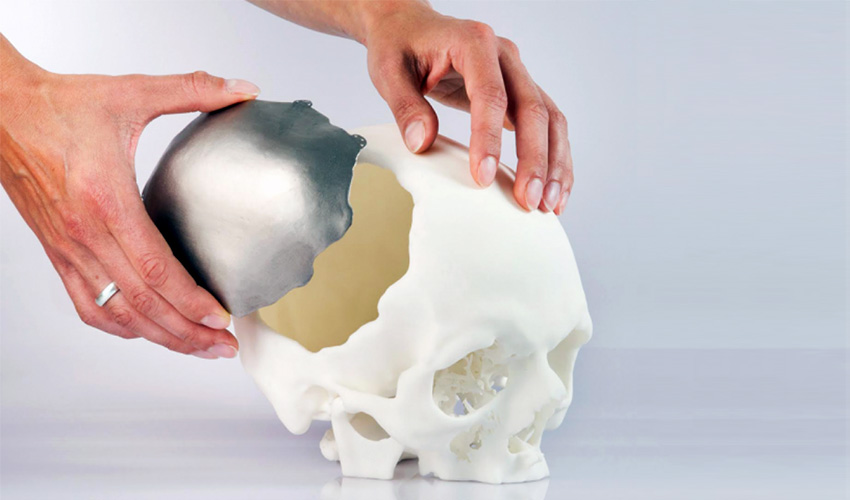
Le secteur médical tire grandement profit des avancées en fabrication additive. Grâce à la possibilité de créer des modèles uniques pour chaque patient, la médecine personnalisée devient enfin une réalité. Les implants médicaux représentent un domaine particulièrement sensible, car ils impliquent l’introduction d’un élément externe dans le corps pour remplacer une fonction défaillante ou traiter une maladie. Pour assurer une compatibilité optimale, ces implants doivent être conçus sur mesure, ce qui explique pourquoi la fabrication additive est devenue indispensable dans ce domaine. Afin de mieux comprendre l’état actuel du développement des implants, l’équipe de 3Dnatives a compilé une sélection des implants fabriqués grâce à l’impression 3D. Ce classement inclut des implants déjà approuvés ainsi que d’autres encore en phase de recherche, illustrant ainsi le potentiel et les progrès continus de cette technologie dans le secteur médical.
Un implant imprimé en 3D pour l’oreille
Le marteau, l’enclume et l’étrier sont trois os situés dans notre oreille, les plus petits de notre corps humain car ils ne poussent pas après la naissance. Leur forme, taille et position sont donc très importantes pour assurer le bon fonctionnement de l’oreille. Or, il arrive que ces os se cassent et qu’il faille les remplacer. C’est ce qu’il s’est passé en Afrique du Sud où un patient s’est fait implanté des osselets imprimés en 3D en titane suite à un accident de voiture. Après une numérisation 3D de son oreille moyenne, l’équipe de chirurgiens à l’origine de l’opération, a pu modéliser un implant sur-mesure, imprimé par la suite sur une machine de fusion laser sur lit de poudre. Le titane a été privilégié dans ce cas-là pour sa biocompatibilité et sa solidité.
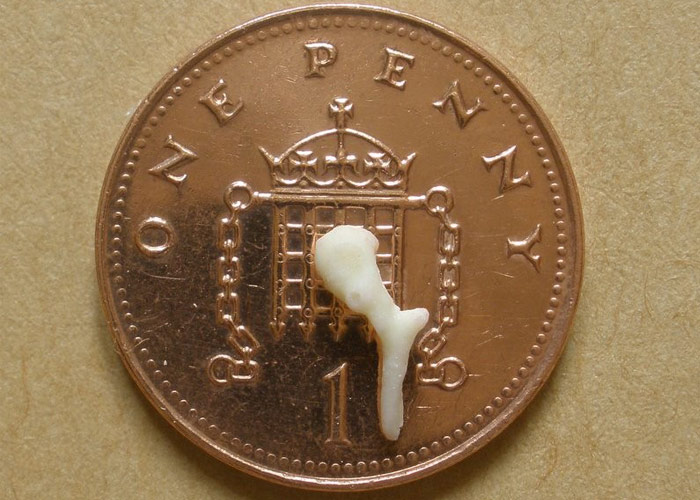
Les osselets font partie des plus petits os du corps humain. La photo montre un véritable osselet et non l’implant
L’impression 3D d’un implant de mâchoire après le retrait d’une tumeur
Anelia Myburgh est une patiente australienne dotée d’un implant mandibulaire imprimé en 3D qui lui a permis de reconstruire son visage. Elle souffrait d’une tumeur maligne logée dans sa mâchoire et ses dents que les médecins ont dû enlever ; ce faisant, ils ont du retirer une partie du visage de la patiente ce qui a entrainé une déformation importante du visage. Ce cas a conduit le chirurgien maxillo-facial George Dimitroulis à explorer les possibilités de la fabrication additive pour la création de modèles personnalisés. Il a créé un implant de mâchoire avec un cadre en titane capable d’incorporer des greffons osseux. Après plus de 5 heures d’opération et plusieurs mois de convalescence, nous pouvons dire que l’opération a été un succès.
La cage thoracique de Renishaw
En raison d’une tumeur à la poitrine, le gallois Peter Maggs, âgé de 71 ans, a dû retirer trois côtes et une partie de sa cage thoracique. Il avait une tumeur de la taille d’une balle de tennis dans le cartilage des côtes, qui a été enlevée après une intervention chirurgicale de 8 heures. Ces parties manquantes de la cage thoraciques ont été remplacées avec succès par un implant sur mesure. Les médecins ont choisi l’impression 3D métal comme méthode de fabrication et se sont tournées vers les solutions de Renishaw, capables de créer des pièces de qualité en titane.
Des valves cardiaques en silicone imprimées en 3D
Bien entendu, les implants ne se limitent pas aux os, bien que ceux-ci soient plus faciles à créer et donc plus fréquents sur le marché. Par exemple, une prothèse de valve cardiaque a été fabriquée à l’aide de silicone. Créées dans le cadre d’une collaboration entre une équipe de chercheurs de l’ETH Zurich et l’entreprise sud-africaine Strait Access Technologies, ces valves cardiaques artificielles imprimées en 3D ont été conçues pour remplacer les valves des personnes âgées ou souffrant de pathologies. Si les chercheurs se sont orientés vers ce matériau, c’est parce qu’il est compatible avec le corps humain. De plus, l’impression 3D permet de fabriquer une valve parfaitement adaptée au patient. Il convient de noter que, bien que les premiers résultats soient prometteurs, les chercheurs estiment qu’il faudra encore 10 ans avant que ces valves cardiaques imprimées en 3D puissent être commercialisées.
AB Dental et l’utilisation de la fabrication additive
AB Dental utilise le frittage sélectif par laser (SLS) pour créer des implants personnalisés et innover en matière de technologie et d’application dans le domaine bucco-maxillo-facial. Le système de la société permet aux médecins de planifier les traitements de restauration dentaire et faciale avec plus de précision que les méthodes traditionnelles. L’entreprise propose aux patients plusieurs implants restaurateurs imprimés en 3D, notamment pour l’augmentation du toit des sinus, la réparation de l’os orbital et un implant sous-périosté pour les mâchoires résorbées.
Une rétine artificielle en carbone imprimée en 3D
Un ingénieur australien a mis au point une rétine artificielle en carbone imprimée en 3D pour aider les gens à retrouver la vue. Le Dr Matthew Griffith, de l’université de Sydney, a commencé à se faire connaitre lorsqu’il a réalisé que, à l’image d’un ordinateur, le corps humain n’est qu’un semi-conducteur à base de carbone. Fort de cette connaissance, il a déterminé qu’il pouvait reproduire un œil en créant un dispositif en carbone (et donc entièrement biocompatible) qui absorbe la lumière et crée ensuite une charge électronique, exactement comme un œil. D’autant plus que, grâce au faible cout de fabrication offert par l’impression 3D, il lui a été tout à fait possible de concevoir lui-même cette rétine artificielle. Bien que le dispositif ne soit pas encore achevé et qu’il ne fasse pas l’objet d’études cliniques avant trois à cinq ans, M. Griffith espère qu’il sera utile aux patients qui ont perdu la vue, et qu’il pourra même restaurer la vision des couleurs, ce qui n’est pas possible actuellement.
Particle3D et les implants osseux
Particle3D a été lancé en 2014 par deux étudiants en ingénierie médicale et leur professeur dans le but de développer une nouvelle solution pour remplacer les os détruits ou retirés par chirurgie. Aujourd’hui, Particle3D poursuit le développement d’implants osseux spécifiques aux patients, basés sur leur propre scanner/IRM, ce qui permet d’obtenir des implants imprimés en 3D qui présentent une architecture interne unique, semblable à celle d’un os, contenant des micro- et macroporosités, exactement comme un véritable os.
Un implant de cartilage imprimé en 3D pour lutter contre l’arthrose
Chez l’homme et chez le chien, une minuscule couche de cartilage préserve les surfaces articulaires et permet aux os de glisser les uns contre les autres correctement. Malheureusement, au fil du temps, ce cartilage se dégrade, ce qui entraîne de l’arthrose et donc des douleurs articulaires. Pour y palier, des chercheurs de l’université d’État de Caroline du Nord ont développé un implant à base de textile contenant du cartilage dérivé de cellules souches du patient. En partie imprimé en 3D, ce type d’implant a été testé avec succès sur un groupe de chiens souffrant de la hanche. Ce groupe était divisé en deux, et une partie a reçu l’implant, et l’autre non. Comme vous vous en doutez, les chiens ayant reçu l’implant ont retrouvé toutes leurs capacités 4 mois après l’opération.
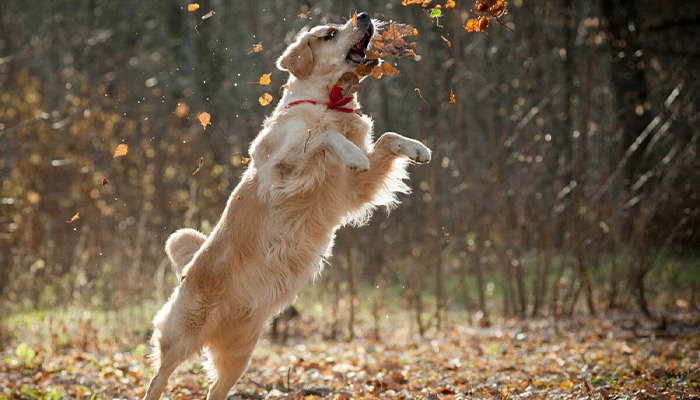
Crédits photo : Deposiphoto
Le plus grand implant crânien du monde imprimé en 3D
La startup Arcomedlab a réalisé un exploit en créant le plus grand implant crânien au monde grâce à l’impression 3D. Depuis ses débuts, Arcomedlab a traité plus de 600 cas cliniques concrets, se spécialisant principalement dans la reconstruction crânienne avec des implants personnalisés, ainsi que dans les reconstructions faciales sur mesure. De plus, ils ont réalisé diverses planifications chirurgicales complexes. Actuellement, cette entreprise est capable de reconstituer intégralement le crâne de patients de tous âges, ainsi que toute structure osseuse faciale, en utilisant les technologies d’impression 3D FDM et SLA à des fins médicales. Grâce à ces avancées technologiques, ils repoussent les limites de la médecine reconstructive et offrent des solutions innovantes et adaptées aux besoins spécifiques de chaque patient.
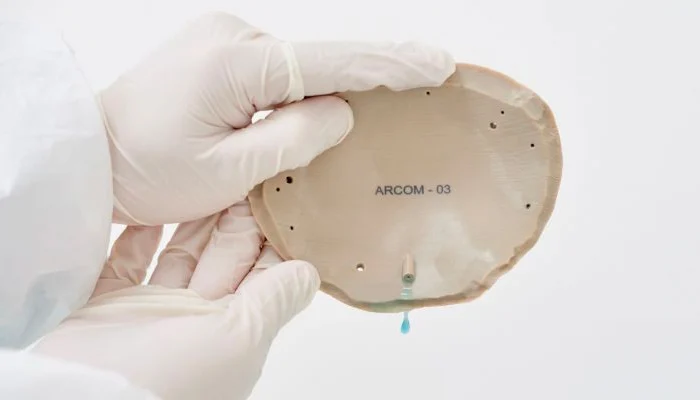
crédits photo : Arcomedlab
Le projet de recherche ELAINE
Dans le cadre du projet de recherche ELAINE (Electrically Active Implants), des chercheurs de l’université de Rostock s’emploient à développer des structures bioactives pour le remplacement osseux. Actuellement, les implants en titane sont couramment utilisés, mais ils présentent des limites : leur adaptation aux conditions anatomiques du corps est imparfaite, et ils peuvent se desserrer avec le temps, causant des problèmes à long terme. Pour surmonter ces défis et améliorer le traitement des défauts osseux, les scientifiques explorent les possibilités offertes par la fabrication additive. Ils travaillent sur des implants électriquement actifs qui imitent le comportement des structures osseuses naturelles, en s’inspirant de la physiologie des os. Le matériau choisi est le titanate de baryum, capable de libérer des ions au contact des fluides corporels. La technologie employée pour créer ces implants est la LCM, une technique de photopolymérisation. Ce procédé implique l’utilisation de polymères chargés de particules piézocéramiques, qui sont ensuite placés dans une imprimante pour créer une structure fine par photodurcissement, conférant ainsi au matériau sa biocompatibilité. L’impression 3D présente l’avantage supplémentaire de permettre la fabrication d’implants sur mesure, adaptés à chaque patient. Bien que ce projet soit encore en phase de recherche, il est envisagé que ces implants pourraient être utilisés en milieu clinique d’ici une dizaine d’années.
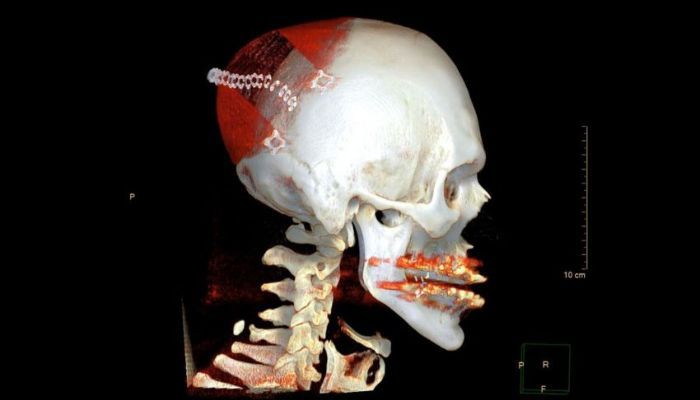
À l’avenir, les implants de plus grande taille, comme ceux utilisés pour la reconstruction du crâne, pourraient provenir d’une imprimante 3D.
La greffe de nez « MyBone »
En 2022, une collaboration entre le CHU de Toulouse, l’Institut Claudius Regaud et la société belge CERHUM a permis de reconstruire avec succès le nez d’un patient atteint de cancer en utilisant l’impression 3D. La procédure innovante a impliqué la création d’un implant biocéramique personnalisé, nommé « MyBone », qui reproduit les caractéristiques de l’os humain et favorise à la fois l’ostéointégration et l’ostéoconductivité. Tout a commencé par un scan détaillé du visage du patient, à partir duquel l’implant a été imprimé en 3D via stéréolithographie. L’implant a d’abord été placé dans l’avant-bras de la patiente pour favoriser la vascularisation et la colonisation cellulaire, un processus crucial où les cellules envahissent et se développent dans la structure de l’implant. Une fois cette étape achevée, le nez a été transplanté sur le visage de la patiente et connecté à ses vaisseaux sanguins grâce à la microchirurgie. Cette méthode a permis d’obtenir un haut niveau de biocompatibilité et de durabilité, tout en minimisant les risques d’infection et la nécessité de futurs remplacements. La procédure a abouti à la transplantation réussie d’un nez entièrement fonctionnel et esthétiquement satisfaisant, démontrant ainsi le potentiel immense de l’impression 3D dans le domaine de la chirurgie reconstructive majeure.
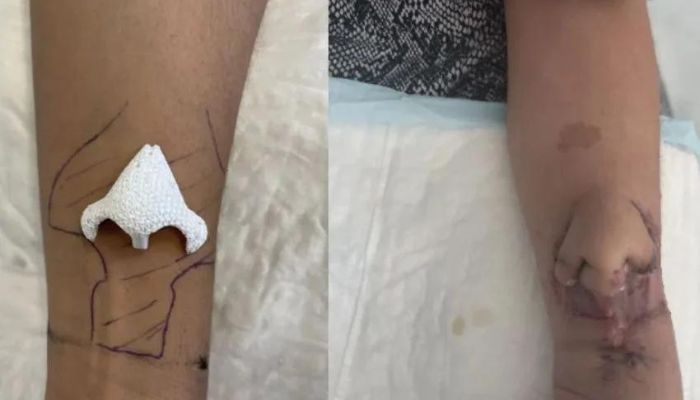
crédits photo : Hôpital universitaire de Toulouse
BellaSeno : implants mammaires imprimés en 3D
L’entreprise BellaSeno fabrique des implants mammaires en polycaprolactone, un matériau de suture couramment utilisé dans le secteur de la santé, en utilisant l’impression 3D. Ces implants imprimés en 3D sont destinés aux personnes atteintes de cancer du sein ou d’autres maladies mammaires et sont conçus pour être utilisés en chirurgie reconstructive et plastique. BellaSeno a mis au point une solution d’impression 3D qui supporte des matériaux cliniquement compatibles. Ces implants sont conçus pour se résorber complètement en cinq ans, période au cours de laquelle ils sont remplacés par des cellules graisseuses naturelles dans le corps. Les dix premiers tests effectués sur des patients ont montré des résultats prometteurs, avec des évaluations positives des patients et un bon profil de sécurité des implants 3D. Les chirurgiens ont également donné des avis favorables sur l’utilisation de ces implants imprimés en 3D.
Un implant pour réparer le cartilage du genou
Nanochon se fixe pour mission de faciliter le remplacement et la réparation du cartilage chez les patients souffrant de lésions au genou. Pour atteindre cet objectif, l’entreprise utilise la technologie d’impression 3D, en particulier la technique d’extrusion, afin de créer un implant destiné à remplacer le cartilage abîmé ou perdu. Ce dispositif, appelé Chondrograft™, est fabriqué à partir d’un matériau composite biocompatible innovant qui favorise la régénération tissulaire. Le Chondrograft™ est produit de manière additive par le procédé de fabrication de filament fondu, en utilisant le matériau composite exclusif de Nanochon. Ce qui distingue cet implant est sa structure unique : en plus de sa microstructure visible, il possède une porosité submicronique. Cette caractéristique, après un post-traitement, rend l’implant plus souple et malléable, tout en maintenant son intégrité structurelle.
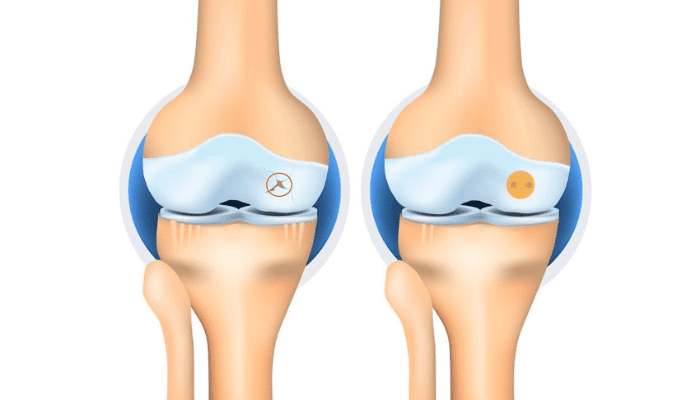
Crédits photo : Nanochon
L’implant de moelle osseuse Matricelf
En 2022, la société israélienne de médecine régénérative Matricelf a réalisé avec succès des tests d’implants de moelle épinière imprimés en 3D. Ces implants ont été évalués sur des souris souffrant de paralysie chronique prolongée, et les résultats ont révélé un taux de réussite de 80 % dans la récupération de la capacité de marcher. La technologie développée par Matricelf commence par une biopsie du tissu omental du patient. Ce tissu est ensuite soumis à un processus exclusif de décellularisation, produisant un hydrogel résistant à la chaleur. Simultanément, des cellules souches pluripotentes induites (CSPi) sont reprogrammées à partir des cellules matures du patient. Les tests des CSPi dans l’hydrogel aboutissent à la création d’implants neuronaux fonctionnels et spécifiques au patient, capables de réparer les tissus de la moelle épinière lésée. Bien que ces implants n’aient été testés que sur des souris pour l’instant, les scientifiques sont optimistes quant à leur potentiel à transformer la vie de milliers de personnes souffrant de lésions de la moelle épinière, souvent causées par des accidents de la route, des chutes et des activités sportives. Les recherches se poursuivent et des demandes de brevet ont été déposées aux États-Unis et en Europe pour l’utilisation de ces implants chez l’homme.
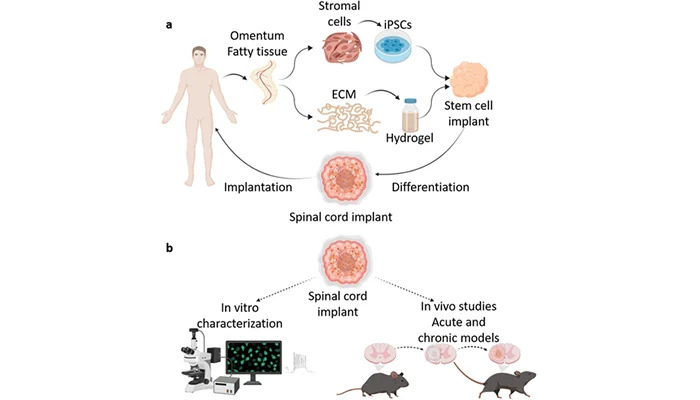
crédits photo : Matricelf
Des prothèses de cheville imprimées en 3D
Le centre de reconstruction des membres de l’Université Macquarie a amélioré la chirurgie de remplacement de la cheville grâce à l’utilisation d’implants imprimés en 3D. Ces avancées offrent un soulagement et une mobilité aux patients souffrant d’arthrite sévère de la cheville ou de dégradations articulaires causées par des traumatismes. Fabriqués à partir de matériaux synthétiques comme l’hydroxyapatite, ces implants imitent la structure osseuse naturelle et facilitent l’ostéointégration, assurant ainsi une durabilité à long terme et réduisant le risque de complications post-opératoires. Contrairement aux fusions et aux prothèses de cheville traditionnelles qui limitent la mobilité et peuvent entraîner d’autres problèmes articulaires, ces implants imprimés en 3D préservent le mouvement de l’articulation tout en soulageant la douleur. Depuis 2022, les chirurgiens orthopédiques Dr Tim O’Carrigan et Dr Mustafa Alttahir réalisent cette procédure, qui requiert beaucoup moins l’insertion de vis de cheville et l’ablation du cartilage articulaire, permettant ainsi une récupération plus rapide et une mobilité accrue.
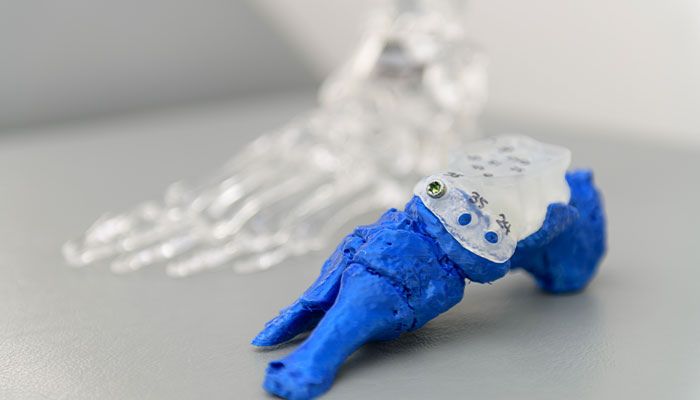
crédits photo : Macquarie University
Première calotte crânienne imprimée en 3D pour un enfant
À la fin de l’année 2023, Felix, 10 ans, a été victime d’un accident au cours duquel un morceau de métal a frappé sa tête, pénétrant son crâne. Cet incident a entraîné une perte de vision et, malgré une opération d’urgence, une grande partie de sa calotte crânienne restait détruite. Les médecins de l’hôpital régional de Salzbourg ont alors réimprimé la calotte en 3D. Le défi principal était de recréer la calotte sans disposer de son état antérieur, en se basant uniquement sur des images de scanner. En seulement cinq jours, ils ont réussi à fabriquer un implant en PEEK pour la boîte crânienne et à l’implanter lors d’une opération. C’est la première fois qu’un implant imprimé en 3D est utilisé sur un enfant. Le PEEK ne devrait pas poser de problèmes à Felix et devrait rester dans son corps pendant de nombreuses années, nécessitant un remplacement par un modèle plus grand uniquement lorsque sa croissance l’exigera.
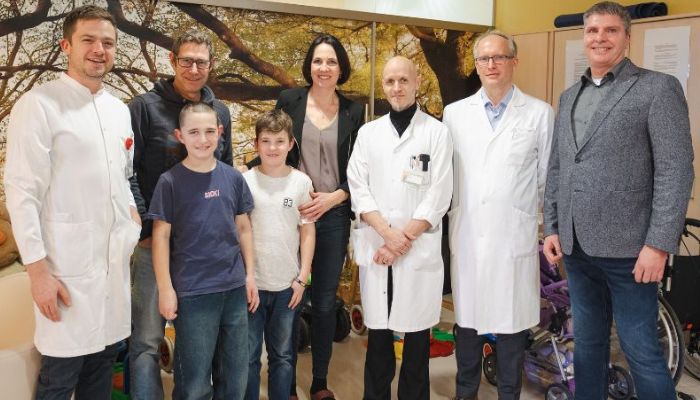
Felix (en T-shirt bleu), entouré de sa famille et des médecins de SALK, a reçu une calotte crânienne en PEEK imprimée en 3D après un accident. (Photo : Salk / Leon Bernhofer)
Que pensez-vous de l’usage de la fabrication additive dans le secteur médical ? N’hésitez pas à partager votre avis dans les commentaires de l’article ou avec les membres du forum 3Dnatives. Retrouvez toutes nos vidéos sur notre chaîne YouTube ou suivez-nous sur Facebook ou Twitter !
Bonjour
Je cherche à imprimer une trachée humaine en silicone.
Pouvez vous m’aidez
merci