Fraunhofer IAPT réduit poids et coûts d’une pièce automobile grâce à l’impression 3D
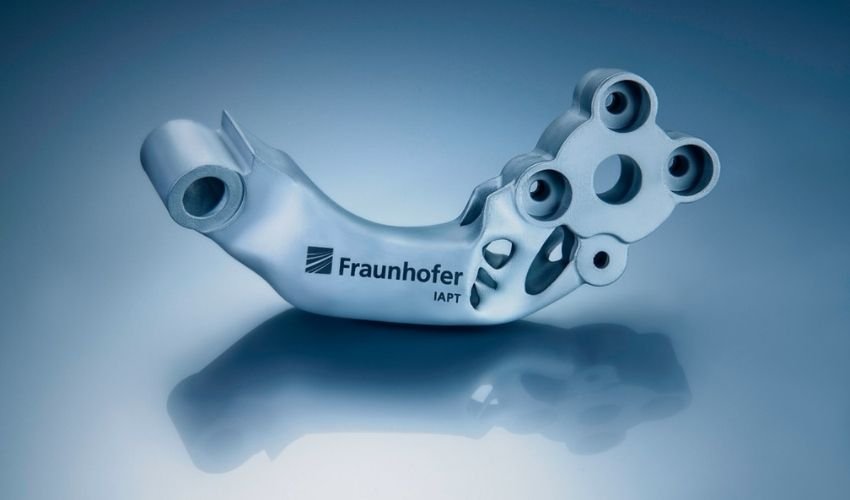
L’institut Fraunhofer for Additive Production Technologies (Fraunhofer IAPT) a récemment démontré l’importance des paramètres d’impression et des mesures d’optimisation aujourd’hui employées sur le marché. Grâce à une optimisation continue de la chaîne de valeur de l’impression 3D, il est possible d’influencer aussi bien les propriétés techniques que les coûts de la pièce finie. Fraunhofer IAPT a ainsi déterminé, étape par étape, les facteurs qui influencent le coût et le poids d’une charnière de porte automobile, plus particulièrement pour une voiture de sport. Il a utilisé une approche « Design to Cost ».
On le sait, la fabrication additive fait désormais partie intégrante du processus de production dans de nombreux secteurs, notamment l’automobile qui s’appuie sur de meilleurs géométries, une réduction du poids des composants, mais aussi des coûts et des délais de production. Toutefois, pour exploiter pleinement le potentiel des technologies d’impression 3D, il faut pouvoir maîtriser leurs paramètres, chaque procédé et chaque machine étant différents. C’est ce que le Fraunhofer IAPT a tenté de faire avec ce nouveau cas d’usage automobile.
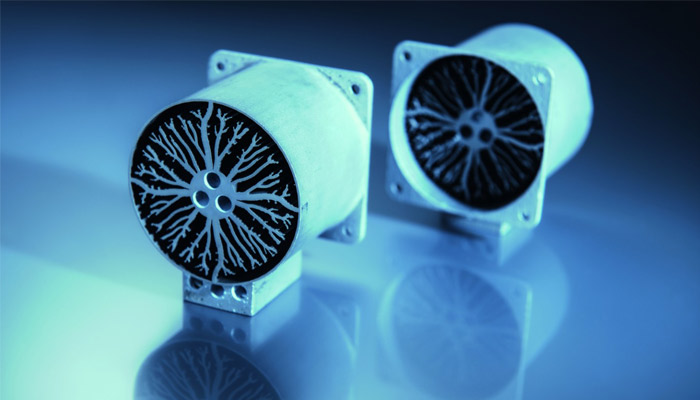
Le Fraunhofer IAPT maîtrise depuis quelques années déjà différents procédés d’impression 3D, notamment ceux basés sur le métal (crédits photo : Fraunhofer IAPT)
Un processus optimisé ouvre la porte à la production en série
Dans un premier temps, les experts ont analysé la pièce à l’aide de l’outil logiciel de 3D Spark et ont déterminé l’orientation de la pièce optimale en termes de coûts pour l’impression 3D lors de la phase de design. Le résultat a été comparé à la pièce fabriquée par fabrication additive sans optimisation. L’équipe a constaté une économie de coûts de 15%, qui résulte de l’utilisation optimale du plateau d’impression et d’une réduction du post-traitement. L’équipe de chercheurs ne voulait toutefois pas se contenter de ce résultat. La géométrie du bras articulé a donc été optimisée en renforçant uniquement les sections de la pièce requises par le flux de force simulé, réduisant ainsi le besoin en matériau de 20% et donc par conséquent le poids de 35%. Le temps d’impression a quant à lui été diminué de 20% supplémentaires.
Ce cas d’application va plus loin et suggère que les paramètre d’impression comme l’épaisseur de couches, la vitesse de balayage ou encore la déformation du profil du laser, contribuent à la réalisation d’économies potentielles. En réalité, ces paramètres influent sur le temps d’impression total ce qui a forcément une incidence sur le coût d’impression.
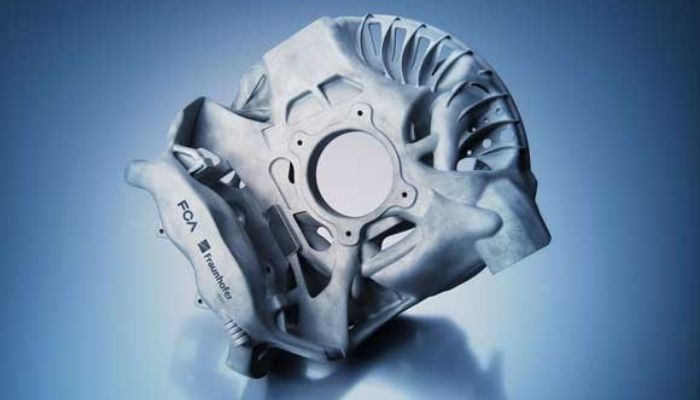
Le Fraunhofer IAPT a également utilisé cette approche pour fabriquer un étrier de frein pour Fiat Chrysler. (Image : Fraunhofer IAPT / Fiat Chrysler)
Ce bras articulé optimisé serait donc 80% moins cher à produire que via une méthode que d’impression 3D non optimisée. Ce pourcentage doit être compris comme il suit : l’optimisation de l’orientation et de la structure ainsi que la réduction des supports pourraient réduire les coûts de 45% ; tandis que le choix optimisé des matériaux et des paramètres d’impression 3D pourraient réduire les coûts de 35%. Avec cette étude de cas, l’institut veut démontrer que l’utilisation de la fabrication additive peut déjà être mise en œuvre de manière rentable pour de grandes séries allant jusqu’à 5 000 pièces. Les résultats de la réduction systématique des coûts pour le bras articulé devraient pouvoir être appliqués à un grand nombre de composants automobiles. Retrouvez plus d’informations dans le communiqué de presse officiel ICI.
Que pensez-vous du nouveau projet du Fraunhofer IAPT ? N’hésitez pas à partager votre avis dans les commentaires de l’article. Retrouvez toutes nos vidéos sur notre chaîne YouTube ou suivez-nous sur Facebook ou Twitter !
*Crédits photo de couverture : Fraunhofer IAPT