Formnext met en avant les applications et le potentiel de l’impression 3D dans le domaine aérospatial
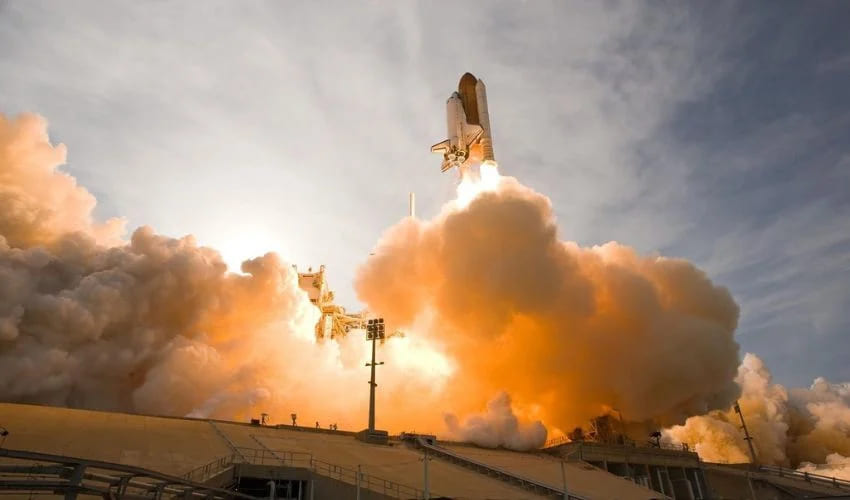
Formnext 2024 a une fois de plus offert un aperçu des tendances de l’industrie de la fabrication additive et des dernières innovations. Sur l’édition précédente, nous avions observé de nombreuses applications dans le secteur automobile mais aussi des initiatives en faveur d’une meilleure durabilité. Cette année a été marquée par une montée en puissance des technologies d’impression 3D métallique et des innovations liées aux applications spatiales. Cette évolution s’est reflétée directement sur les stands des exposants, où de nombreux cas d’utilisation concrets et des imprimantes 3D dédiées ont été présentés. Elle a également été largement abordée dans le programme du salon, avec plusieurs conférences et présentations dédiées au traitement du métal et à la fabrication additive pour le secteur spatial. Nous avons déjà exploré les applications métalliques mises en avant à Formnext. Il est temps de s’intéresser au rôle croissant de l’impression 3D dans l’aérospatiale et de présenter certains enseignements tirés du salon.
Dans le domaine spatial, l’impression 3D joue un rôle clé dans la production de composants pour les engins spatiaux. Elle est particulièrement utilisée pour concevoir des pièces essentielles telles que les éléments de propulsion des fusées, les chambres de combustion, les têtes d’injecteurs et les systèmes de pompage. Un autre champ d’application majeur réside dans la fabrication de structures directement dans l’espace. Celles-ci sont parfois réalisées à partir de matériaux disponibles sur place, comme le régolithe martien ou lunaire.
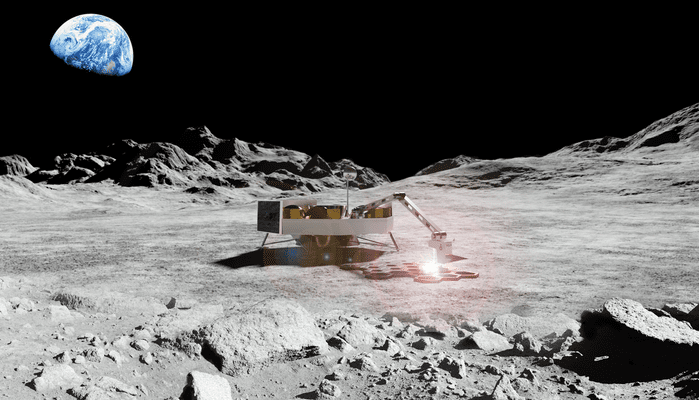
Crédits photo : ICON
L’impression 3D offre la possibilité de concevoir des designs complexes et enchevêtrés. Dans le cas des moteurs de fusée, elle permet par exemple d’intégrer des canaux de refroidissement en une seule étape de fabrication. De nombreuses applications démontrent que les pièces produites par impression 3D peuvent améliorer les performances, notamment grâce à l’utilisation de matériaux sur mesure dotés de propriétés spécifiques, répondant précisément aux exigences de l’industrie. Ces avantages ne se limitent pas aux composants des engins spatiaux, mais s’étendent également aux structures fabriquées directement dans l’espace.
Procédés d’impression 3D pour l’espace et les défis existants
Le DMLS reste actuellement le procédé d’impression le plus couramment utilisé, bien que le DED gagne de plus en plus en popularité de par sa capacité à réparer des pièces existantes. Par exemple, The Exploration Company se concentre actuellement sur la fusion sur lit de poudre, tout en planifiant d’adopter le DED d’ici 2025. De son côté, l’entreprise allemande Ponticon fabrique des systèmes industriels DED à grande vitesse. Son procédé de dépôt dynamique de matériaux a d’ailleurs été employé pour le revêtement du moteur d’Ariane 6. Cette technique consiste à faire fondre la poudre en suspension dans l’air, ce qui permet d’obtenir une précision exceptionnelle.
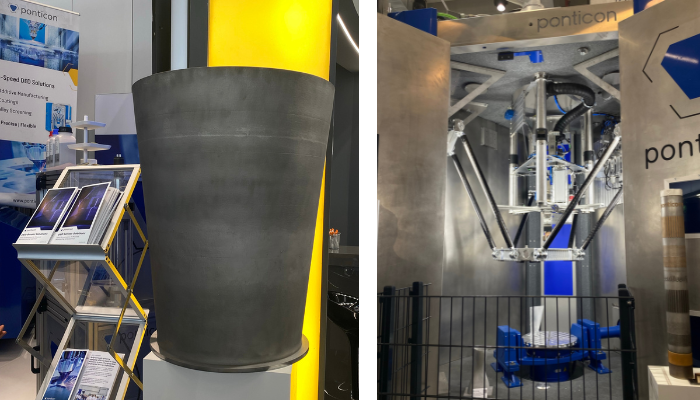
Exemple de pièce pour l’aérospatiale imprimée en 3D sur le stand de Ponticon (crédits photo : 3Dnatives)
De plus, avec le procédé DED, les utilisateurs s’affranchissent du dépoudrage de la pièce qui s’avère particulièrement complexe quand on intègre des canaux internes. Si de la poudre reste coincée à l’intérieur, elle empêche la circulation des liquides, ce qui pourrait entraîner la fonte voire l’explosion du moteur. De plus, la complexité des pièces reste un défi majeur. « Imprimer 100 canaux de refroidissement dans une pièce avec une épaisseur de paroi de seulement 4 mm, c’est un véritable défi », explique Maximilian Strixner, de The Exploration Company, une entreprise à l’origine de Nyx, une capsule spatiale modulaire et réutilisable.
Un autre défi majeur est le coût. Celui-ci résulte principalement du prix élevé des matériaux, qui doivent posséder des caractéristiques spécifiques. Lors de son intervention, Tobias Stiggen de Ponticon GmbH a indiqué que près de deux tiers du coût total du carénage du moteur d’Ariane 6, étaient attribués aux matériaux. En revanche, le coût du système d’impression de Ponticon utilisé dans cet exemple s’est révélé relativement modéré.
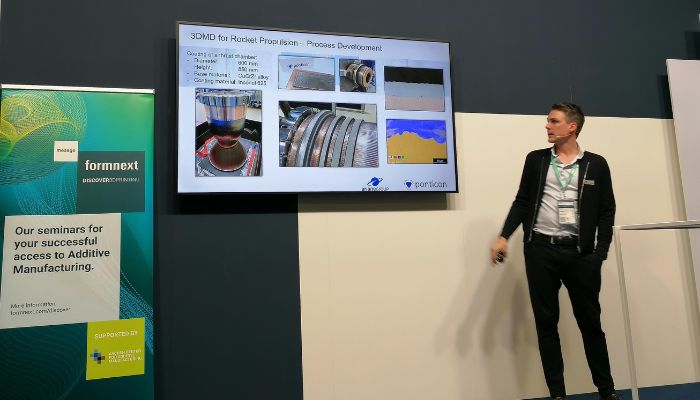
Tobias Stiggen explique les avantages de la technologie DED pour la propulsion des fusées (crédits photo : 3Dnatives)
Une autre explication des coûts élevés réside dans l’accent mis sur la production de pièces performantes et légères. Lors de sa conférence sur la « Qualification des matériaux pour la production de pièces imprimées en 3D en série pour l’aérospatiale et l’automobile », Bill Bihlman de SAE International a souligné que les pièces destinées à l’aérospatiale coûtent environ dix fois plus cher que celles utilisées dans l’automobile.
Une diversité de matériaux performants pour les applications spatiales
Bien que le coût soit un facteur déterminant, la performance et la résistance des matériaux restent des priorités absolues. C’est pourquoi une large gamme de métaux et d’alliages, ainsi que de nouveaux matériaux et composites, sont utilisés dans le secteur spatial. Par exemple, The Exploration Company privilégie les alliages de cuivre pour leur conductivité thermique et les alliages à base de nickel pour leurs qualités de résistance mécanique et chimique. De son côté, SAE fait appel à des alliages, mais aussi à de l’aluminium et du titane pour la production de pièces en petites séries.
Pour la fabrication dans l’espace, on utilise principalement des matériaux classiques ou des matériaux composites. Par exemple, le Concordia Aerospace Robotics Lab recommande un composite à base de PEEK et de régolithe. Ce matériau répond aux exigences de la NASA concernant les émissions de gaz d’échappement et offre une bonne résistance aux radiations et aux produits chimiques. De plus, l’intégration du régolithe dans le PEEK a permis de réduire les coûts, comme l’indiquent les résultats. En incorporant 50 % de régolithe dans le PEEK, les coûts ont été réduits de moitié.
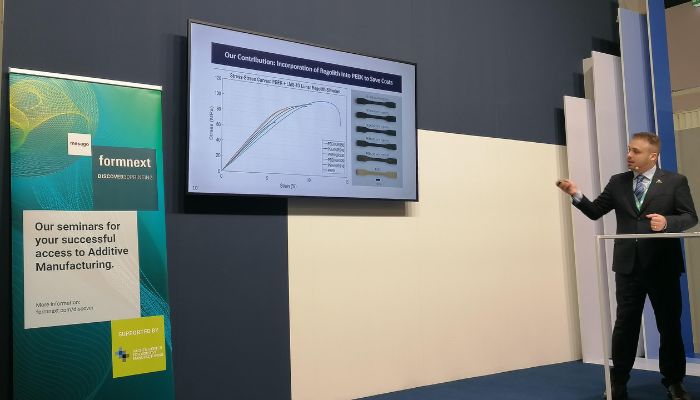
Mohammad Azami de Concordia Aerospace Robotics Lab
Le silicone commence également à faire son apparition dans le domaine aérospatial. À cet égard, une présentation dédiée intitulée « Transformer l’aérospatiale grâce à l’impression 3D de silicone et de composites souples », a été proposée lors du salon cette année. Julien Barthes de 3Deus Dynamics a présenté son procédé d’impression 3D utilisant de la poudre de silicone et a expliqué comment l’entreprise développe de nouveaux matériaux composites souples tout au long du processus d’impression.
Un des principaux avantages de cette méthode est que le silicone traditionnellement moulé par injection peut aussi être utilisé pour l’impression 3D, et ce, sans générer de déchets, car la poudre recyclée peut être réutilisée. Julien Barthes a également souligné qu’il est possible de changer de matériau pendant l’impression, ce qui permet de fabriquer une pièce avec deux textures distinctes et des propriétés mécaniques spécifiques, tout en intégrant des géométries complexes. « Vous pouvez ajouter de la poudre au cours du processus d’impression, manipuler le matériau et créer des composites directement pendant la production », a-t-il conclut.
Un regard sur l’avenir
Cette année, nous avons également pu voir des innovations intéressantes, telles que le lancement d’Ariane 6 ; le plus grand moteur de fusée imprimé en métal au monde par Eplus3D et LEAP 71, et bien d’autres encore. Cependant, comme nous l’avons mentionné précédemment, certains défis persistent.
La fabrication additive dans le secteur spatial offre un potentiel immense qui reste encore largement inexploité. Au-delà de la fabrication légère, des géométries complexes et de l’utilisation de nouveaux matériaux performants qui rendent les fusées plus rapides, efficaces et durables, il est certain que l’on entendra de plus en plus souvent parler de l’impression 3D, y compris dans l’espace, dans un avenir proche.
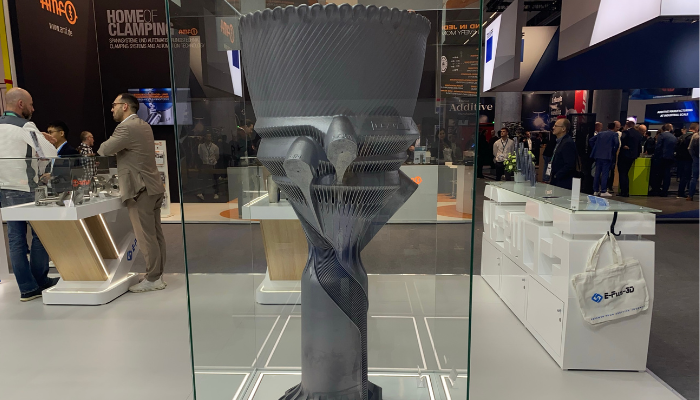
Dans le cadre de Formnext 2024., Eplus3D et LEAP 71 ont présenté le plus grand moteur de fusée imprimé en métal au monde à ce jour. (Crédits photo : LEAP 71)
Que pensez-vous de ces application pour l’aérospatiale ? Partagez votre avis dans les commentaires de l’article. Retrouvez toutes nos vidéos sur notre chaîne YouTube ou suivez-nous sur Facebook ou LinkedIn !