Finition de surface en impression 3D : quelles sont les méthodes disponibles ?
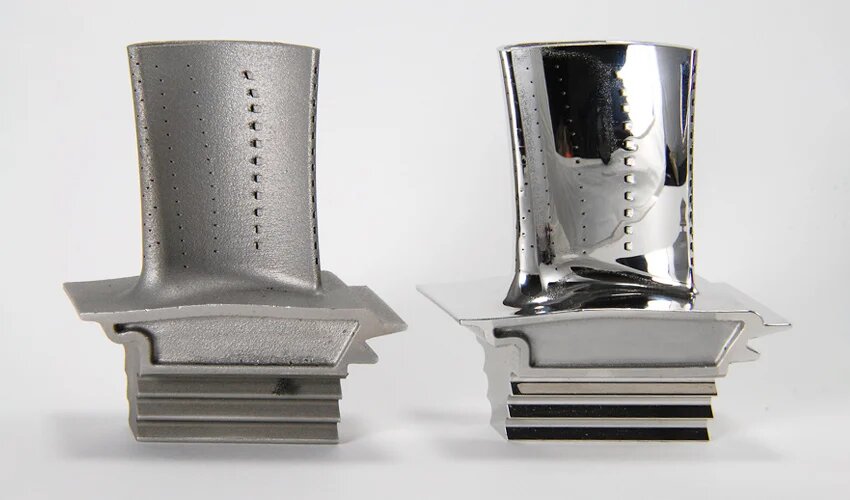
La fabrication additive a connu une croissance considérable ces dernières années, passant d’une technologie de niche à une méthode de prototypage et de production de pièces finales. Cependant, malgré la tendance de l’impression 3D vers la liberté de conception et la production personnalisée, la technologie seule n’est pas capable de créer des pièces finies de qualité professionnelle. Souvent, des étapes de post-traitement sont nécessaires pour obtenir des modèles finaux de haute qualité. Par exemple, on vous parlait récemment de l’importance du nettoyage des pièces imprimées en 3D. Un autre procédé essentiel consiste à traiter la surface de ces pièces, en fonction du matériau et de la technologie utilisés. C’est pourquoi nous vous proposons aujourd’hui un guide complet sur la finition de surface en impression 3D. Ce traitement peut également être nécessaire pour modifier l’apparence de la pièce brute, lisser sa surface, ajuster la taille et la forme, ou améliorer sa durée de vie.
Le ponçage, une finition de surface manuelle ou automatique
Sur les pièces imprimées en 3D, en particulier celles créées via un procédé d’extrusion, des lignes correspondant à vos couches successives de matériaux et autres imperfections éventuelles sont souvent visibles. Pour éliminer ces défauts de surface, l’une des méthodes les plus couramment utilisées est le ponçage. Ce système implique l’utilisation d’un matériau rugueux tel que du papier de verre de différentes granulométries pour éliminer les lignes de revêtement et obtenir une finition uniforme sans imperfections. Cette méthode est très utile si l’on souhaite appliquer un revêtement ultérieur sur la surface, car celle-ci doit être lisse pour une application optimale.
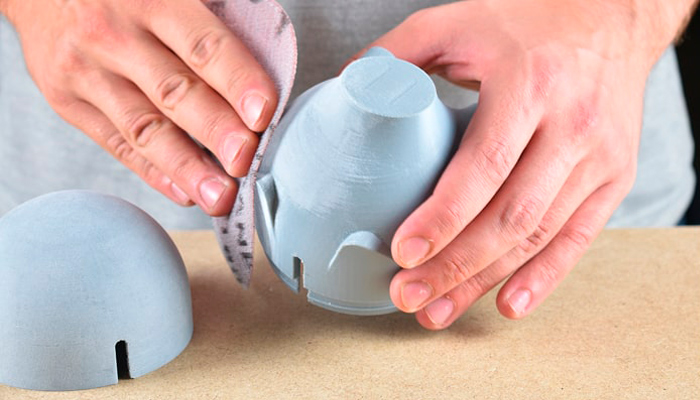
Le ponçage des pièces peut être effectué manuellement, mais il existe également des outils automatiques
Le ponçage s’effectue généralement en commençant par du papier de verre à gros grain et en progressant vers un plus fin afin d’obtenir une surface de plus en plus lisse. Il est important de faire attention lors du ponçage afin de ne pas endommager la géométrie du modèle. L’inconvénient de cette méthode est qu’il peut être difficile d’atteindre certains points des pièces, en particulier les petits trous et les zones creuses. Le ponçage peut être effectué manuellement, mais cela peut prendre beaucoup de temps. C’est pourquoi des outils et des machines de ponçage automatique sont également disponibles sur le marché.
Méthodes de sablage : grenaillage et microbillage
Le grenaillage de précontrainte et le microbillage sont des techniques utilisées pour la finition de surface en impression 3D. Elles sont généralement utilisées sur une grande variété de pièces métalliques, y compris les alliages d’aluminium, l’acier, le titane, le cuivre et d’autres métaux. Ces deux procédés permettent d’améliorer la résistance et la durabilité des pièces, mais il existe des différences essentielles entre les deux.
Le grenaillage de précontrainte implique l’utilisation de petites sphères métalliques ou céramiques qui sont projetées par de l’air comprimé à grande vitesse contre la surface de la pièce. Cet impact génère une déformation contrôlée dans la couche superficielle de la pièce, ce qui augmente la résistance à la fatigue et réduit la probabilité de fissures et de ruptures. Le grenaillage de précontrainte peut également améliorer la résistance à la corrosion et l’adhérence des revêtements ultérieurs. D’autre part, le grenaillage de précontrainte implique l’utilisation de petites billes de verre, de métal, de plastique ou d’autres matériaux abrasifs pour nettoyer, polir ou texturer la surface de la pièce. Contrairement au grenaillage de précontrainte, qui provoque une déformation de la surface, le microbillage n’enlève que la couche supérieure de matériau, ce qui peut améliorer l’aspect esthétique de la pièce, éliminer la saleté et la corrosion et préparer la surface à recevoir les revêtements ultérieurs.
En résumé, la principale différence entre le grenaillage de précontrainte et le microbillage est très simple. La première méthode génère une déformation à la surface de la pièce, ce qui améliore sa résistance et sa durabilité finales. La seconde ne fait que lisser la couche supérieure du matériau, ce qui améliore l’aspect esthétique et prépare la surface pour les revêtements ultérieurs. Ces techniques de post-traitement sont particulièrement utiles pour les pièces qui seront soumises à des contraintes mécaniques, telles que les engrenages, les ressorts, les composants de turbines et les pièces structurelles d’avions et de véhicules.
Méthodes de polissage au tambour : vibration et culbutage
Contrairement aux méthodes mentionnées précédemment, dans lesquelles les pièces sont traitées une par une, les systèmes de polissage au tambour sont utilisés pour traiter plusieurs objets imprimés en 3D en même temps. Ce groupe comprend deux techniques qui, bien qu’elles semblent similaires à première vue, présentent des différences substantielles à prendre en compte. Il s’agit de la finition par vibration et du culbutage (également appelé « tumbling » ou « rumbling »). Ces deux technologies consistent à placer des pièces imprimées en 3D dans un tambour ou un tumbler contenant un média abrasif qui, grâce au mouvement de tumbling ou de vibration, génère la friction nécessaire pour que les pièces obtiennent une finition optimale. Toutefois, le choix entre l’une ou l’autre méthode dépend des exigences spécifiques de la pièce et du résultat souhaité.
Bien que les deux méthodes permettent d’obtenir des finitions de qualité, le système vibratoire est généralement plus adapté pour obtenir une surface plus lisse et plus homogène en créant une distribution plus uniforme du matériau sur les pièces. La vibration est donc idéale pour les pièces de grande taille ou les pièces aux bords arrondis qui ne présentent pas un niveau de détail élevé. En revanche, le culbutage est basé sur un système de cylindres centrifuges qui appliquent un mouvement plus doux, ce qui le rend plus adapté aux pièces plus petites, plus délicates et plus détaillées. La vitesse est un autre aspect qui différencie les deux méthodes. Alors que la finition vibratoire est une technique plus rapide, le culbutage nécessite généralement plus de temps pour obtenir des surfaces de haute qualité. En fonction de la finition souhaitée et des matériaux utilisés, le culbutage peut prendre de quelques heures à plusieurs jours. La finition vibratoire, en revanche, permet d’obtenir les mêmes résultats en une fraction du temps, souvent en quelques heures.
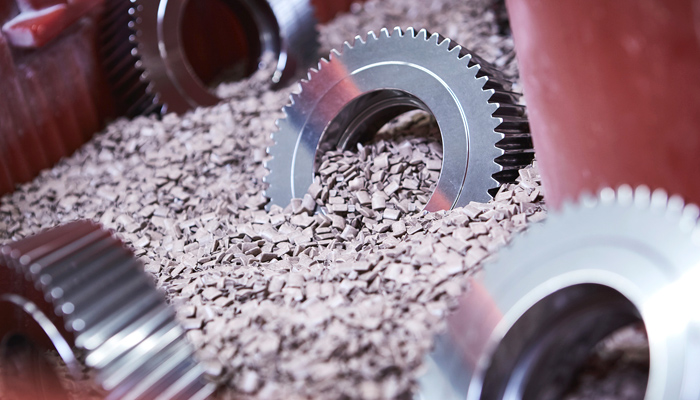
Cette technique de post-traitement peut être utilisée sur des pièces en métal ou en plastique
En résumé, la finition vibratoire et le culbutage sont des méthodes efficaces pour le post-traitement des pièces métalliques et plastiques, mais elles diffèrent par leur mouvement, leur vitesse, leur finition de surface et leur adaptation à différentes géométries de pièces. En outre, il convient d’être prudent lorsque l’on mélange différents types de médias abrasifs, car certaines combinaisons provoquent un déséquilibre et entraînent une finition inégale ou des dommages aux pièces.
Finition de surface et lissage à la vapeur
Le lissage à la vapeur est une autre méthode permettant d’obtenir une surface lisse de l’objet imprimé, à la différence que la finition sera brillante au lieu d’être mate. Pour ce faire, un solvant gazeux est utilisé pour faire fondre la surface du composant jusqu’à ce qu’elle soit uniforme. Une fois que les pièces sont exposées au solvant dans la chambre à vapeur, elles sont placées directement dans une chambre de refroidissement pour arrêter la liquéfaction. La liquéfaction est le processus par lequel une substance à l’état solide ou gazeux passe directement à l’état liquide, en raison d’un changement radical de ses conditions physiques. Ce refroidissement garantit que seule la surface est fondue et que la forme souhaitée de l’objet est maintenue.
Ce processus de lissage à la vapeur permet également de remplir les pores à l’extérieur de l’objet et de sceller la surface, ce qui rend les pièces aptes à contenir des liquides ou des gaz. Bien que cette technologie soit compatible avec une large gamme de thermoplastiques, il convient de noter qu’elle ne peut pas être utilisée avec certains matériaux, car elle peut provoquer une réaction chimique nocive. Les plastiques incompatibles sont le polycarbonate (en fonction de la machine de post-traitement), le polyphénylsulfone (PPSF), l’ULTEM 1010 et l’ULTEM 9085.
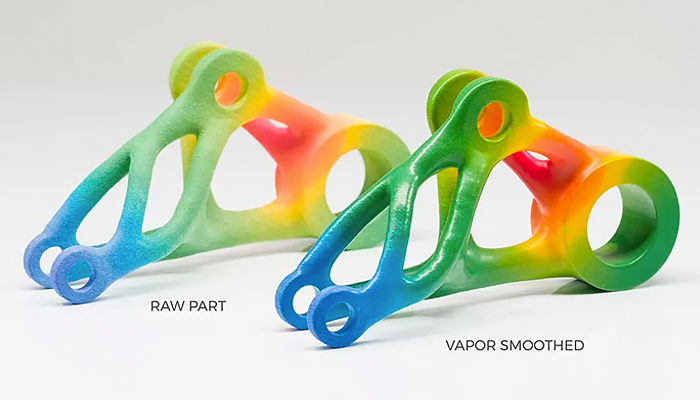
Comparaison entre la pièce brute et la pièce après lissage à la vapeur (crédits photo : AMT)
Une alternative au lissage à la vapeur est de tremper les pièces dans un solvant. Comme son nom l’indique, il s’agit d’immerger les pièces imprimées en 3D dans un solvant plutôt que de les exposer au produit chimique vaporisé. Bien que les résultats soient assez similaires à ceux du lissage à la vapeur, il est plus difficile de maintenir la précision dimensionnelle car le solvant est plus rapide et plus agressif. Cette méthode est souvent utile si les pièces sont plus grandes que la chambre à vapeur.
Utilisation des résines époxy : revêtement et infiltration
Les résines dites époxy sont une classe de polymères réactifs, contenant des groupes époxydes (éthers cycliques à trois chaînons contenant deux atomes de carbone et un atome d’oxygène). Lors du traitement des pièces imprimées en 3D, ces résines permettent d’obtenir une finition de surface scellée, rendant la pièce étanche à l’air, tout en augmentant sa résistance aux températures élevées et à certains produits chimiques. Cette méthode est idéale pour les composants soumis à des conditions d’utilisation difficiles. Pour l’application de ce type de résine, il existe deux méthodes : le revêtement et l’infiltration.
Le revêtement époxy est généralement appliqué à la main. Cette méthode permet de réduire les coûts en évitant l’achat d’équipements chers, mais elle augmente le temps et la quantité de travail nécessaires à l’application. En outre, cette technique convient mieux aux petites séries, aux petits composants ou aux objets qui ne doivent être étanchéifiés que sur une partie de leur surface. Toutefois, certaines zones ne sont pas accessibles avec cette technique, comme les canaux internes et les zones creuses. Enfin, ce n’est peut-être pas le choix idéal pour les pièces nécessitant des dimensions précises, car le revêtement époxy augmente légèrement l’épaisseur de la pièce.
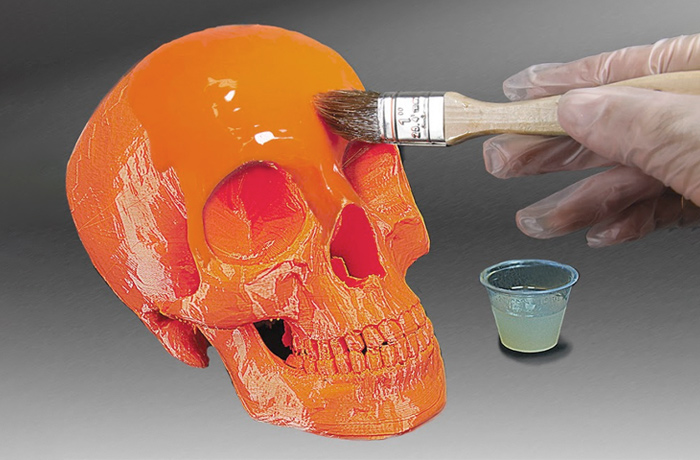
Exemple de revêtement manuel de résine époxy
D’autre part, le système d’infiltration de l’époxy permet de remédier à bon nombre des limitations rencontrées lors de l’application manuelle. Via cette méthode, la pièce est immergée dans l’époxy et une chambre à vide est utilisée pour introduire la résine dans l’objet, remplissant ainsi les pores. Ce processus dure environ trois heures et nécessite moins de main-d’œuvre, ce qui le rend plus pratique et plus rapide à appliquer sur des pièces de grande taille. Toutefois, son principal inconvénient par rapport au revêtement à la main est son coût plus élevé. Il nécessite une chambre à vide, un four pour préchauffer et durcir la résine, le tout en plus du coût de la résine époxy elle-même.
Le rôle de l’usinage CNC pour la finition de surface
Comme nous le savons, les technologies additives et soustractives peuvent être utilisées de manière complémentaire pour combiner les avantages des deux méthodes. Parmi les systèmes de fabrication soustractive les plus connus figure l’usinage CNC qui, bien qu’il ne s’agisse pas à proprement parler d’une méthode de post-traitement, peut être utilisé comme ressource pour obtenir une finition de surface de qualité dans le cadre de l’impression 3D. Ceci est particulièrement intéressant dans le cas de procédés tels que le dépôt de matière sous énergie concentrée (DED). Dans ce cas, on obtient des ébauches dont la surface est très rugueuse, car le métal est fondu directement pendant le processus d’extrusion. Par conséquent, l’usinage CNC est toujours nécessaire pour obtenir une surface lisse et définie. Il existe sur le marché des solutions de fabrication hybrides qui intègrent les deux processus afin d’accélérer les étapes de production.
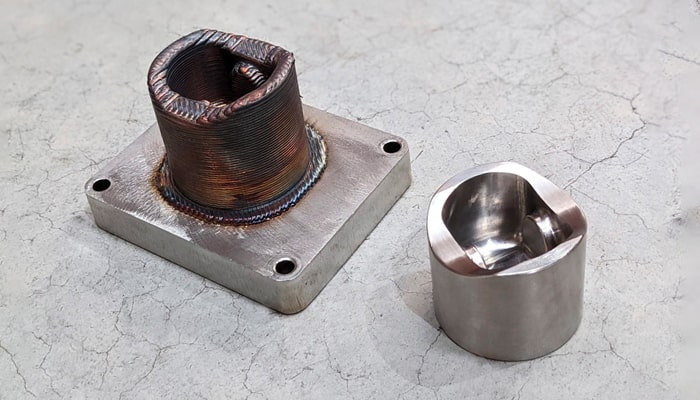
À droite, la pièce après usinage CNC (crédits photo : Meltio)
Quelle méthode de traitement de surface utilisez-vous en impression 3D ? Partagez votre avis dans les commentaires de l’article. Retrouvez toutes nos vidéos sur notre chaîne YouTube ou suivez-nous sur Facebook ou Twitter !
*Crédits photo de couverture : EOS