Fibres courtes vs fibres longues : quel type de renfort choisir en impression 3D ?

Lorsque l’on souhaite conférer des propriétés spécifiques et supérieures à des pièces imprimées en 3D, on se tourne souvent vers les composites. Ceux-ci peuvent être encore plus résistants que certains métaux et offrir des performances élevées. Les composites sont constitués d’au moins deux matériaux qui sont combinés pour obtenir des propriétés nouvelles ou améliorées par rapport aux matériaux de départ. Comme on peut l’imaginer, il en existe de nombreux. Nous nous concentrerons ici sur les matériaux composites formés d’une matrice polymère et d’un renfort en fibres. Dans l’industrie de l’impression 3D, la fibre de carbone, la fibre de verre et le Kevlar sont les trois types de fibres les plus couramment utilisées pour les composites.
Dans cet article, nous nous intéresserons plus particulièrement aux différences qui existent entre les fibres courtes et les fibres longues qui constituent le renfort même. Selon le choix que vous faites, vous obtiendrez des résultats différents et aurez recours à des technologies différentes – on s’intéressera plus particulièrement aujourd’hui à l’extrusion car il s’agit de la plus courante. Quelles sont donc les similitudes et les différences entre ces deux techniques et comment choisir le type de renforcement le plus approprié pour une application spécifique ?
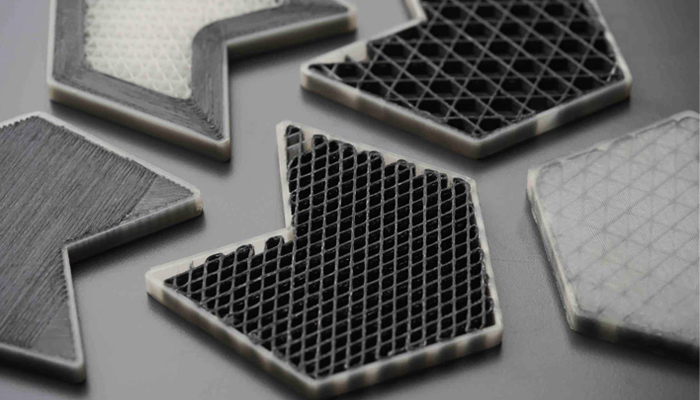
Crédits photo : Anisoprint
Caractéristiques des composites à fibres courtes et longues
Par fibres courtes, nous entendons des morceaux de matériau fibreux plus petits, dont la longueur peut varier de quelques centimètres à quelques millimètres, voire moins. Il s’agit d’un processus similaire à celui utilisé pour renforcer le béton avec des morceaux d’armature. Les fibres sont dispersées dans la matrice plastique et agissent comme un renfort dans l’ensemble du matériau. Les fibres longues, ou continues, quant à elles, sont de longs brins qui s’étendent sur toute la longueur de la pièce imprimée. Ces fibres sont intégrées dans une matrice plastique pendant le processus d’impression 3D, créant ainsi un matériau composite qui combine les propriétés des deux. Avant d’aborder le processus de fabrication additive lui-même et les points à prendre en compte lors de la création de ces pièces, il est important de connaître les caractéristiques des deux renforts.
Dans les deux cas, on retrouve la même composition : un renfort (fibre) et une matrice (polymère). Le premier apporte les propriétés mécaniques, tandis que la seconde joue le rôle de contenant et, à l’aide d’une résine, assure la cohésion des deux éléments, c’est-à-dire l’adhérence de la fibre au matériau lors de la production. Une fois les composés de la matrice (les polymères les plus courants sont le PLA, l’ABS, le polypropylène, le HIPS, le PETG, etc.) et les fibres de renforcement (verre, carbone ou aramide) choisis, ils sont combinés en un seul matériau.
Les fibres courtes peuvent être obtenues par un processus d’extrusion : le mélange de fibres et de matrice est fondu et extrudé pour former un filament unique. Au cours de ce processus, la température et la vitesse peuvent être contrôlées afin d’assurer une bonne répartition des fibres. Les fibres continues, quant à elles, lorsqu’elles forment des filaments, peuvent être coextrudées avec une résine spéciale par un procédé dans lequel le mélange est mixé, polymérisé et solidifié avec la résine. Dans certains cas, il existe des systèmes de production qui moulent directement la matrice et le renfort en même temps pendant le dépôt des couches successives, mais nous y reviendrons plus tard. Dans les deux cas, les fibres courtes et longues doivent être propres et exemptes de contaminants pour garantir une bonne adhérence à la matrice polymère.
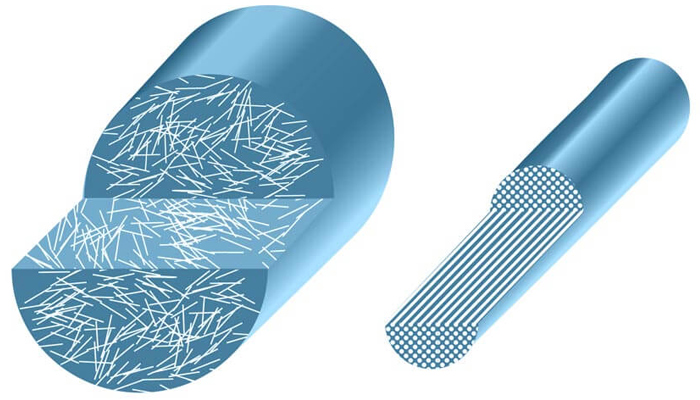
Différence dans la disposition des fibres courtes et longues dans la matrice (crédits photo : Coperion)
Si nous nous concentrons sur les propriétés des matériaux renforcés eux-mêmes, nous constatons qu’elles diffèrent considérablement en fonction du polymère utilisé comme matrice et du choix du type de fibre. Il est évident que si la matière plastique de base est un technopolymère, le composite aura des propriétés plus avancées que celles des plastiques à matrice standard. Par exemple, si un composite a pour matrice le polypropylène, il aura une bonne résistance de base à l’usure, une bonne capacité d’absorption des chocs et une plus grande ténacité et flexibilité. En revanche, si l’on utilise du PLA, le composite sera plus facile à imprimer, mais aura une plus grande tendance à se casser en raison de la faible résistance du matériau.
Comme nous l’avons mentionné, il existe trois principaux types de fibres, courtes et continues : le carbone, le verre et l’aramide (Kevlar). Les fibres de carbone sont les plus utilisées dans l’industrie manufacturière, en raison de la résistance et de la rigidité élevées qu’elles confèrent aux pièces finales. Les renforts en fibres de verre sont généralement plus accessibles et offrent également une bonne résistance, même si elle n’est pas aussi élevée que celle du carbone. Enfin, les fibres de Kevlar sont souvent utilisées dans les gilets pare-balles pour leur grande résistance aux chocs et aux impacts. Dans tous les cas, l’objectif de l’utilisation de fibres est d’obtenir des pièces solides et légères.
Procédés d’impression 3D
La plupart des imprimantes 3D capables de traiter des matériaux composites sont basées sur l’extrusion. En ce qui concerne l’impression 3D FFF de fibres courtes, le processus est classique. Des fibres courtes coupées en petits morceaux sont mélangées à une matière plastique pour former une bobine de filament utilisable avec les machines 3D FFF. Dans ce cas, les fibres sont simplement suspendues dans le thermoplastique, qui est chauffé et extrudé pour former la pièce couche par couche, comme n’importe quelle autre pièce fabriquée avec cette technologie. Toutefois, une buse en acier sera nécessaire pour résister aux brins de fibres abrasifs.
L’impression 3D de composites à fibres longues est en revanche plus complexe ; dans le processus d’extrusion du matériau, une deuxième buse est souvent nécessaire pour déposer séparément la matrice et la fibre. Une alternative consiste à avoir une tête d’impression unique capable de mélanger la fibre à la matrice. Le procédé consiste à placer des fibres continues avec une direction spécifique à l’intérieur de la matrice. Cette dernière agit comme une enveloppe contenant les fibres de renforcement. Pour assurer l’adhésion des fibres à la matrice, on utilise généralement une résine thermodurcissable. Celle-ci est ensuite polymérisée à l’aide d’une lumière UV ou d’une source de chaleur afin de fusionner les couches et les matériaux. La description du processus est délibérément générique, car il existe de nombreuses technologies propriétaires pour l’impression 3D de composites à fibres longues.
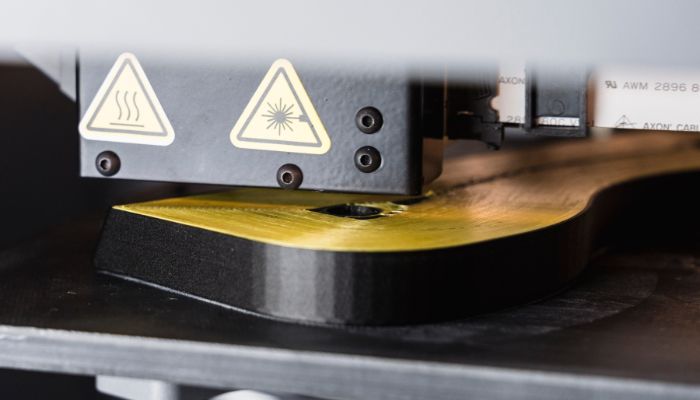
Impression 3D d’une matrice polymère et d’un renfort en fibres de Kevlar (crédits photo : Markforged)
Un aspect important de l’impression avec des fibres, en particulier des fibres continues, est l’utilisation d’un logiciel d’analyse par éléments finis (FEA), qui est une méthode informatisée permettant de prédire comment un produit réagira à des forces et à des stimuli externes. Cela permet d’analyser les caractéristiques des matériaux et de définir précisément le modèle selon lequel les fibres longues doivent être disposées dans la matrice. D’autre part, cela implique également de respecter certaines limites de conception afin de privilégier le positionnement correct des fibres et donc la performance de la pièce. Les propriétés spécifiques du matériau seront donc définies selon un processus contrôlé. Cela est différent pour les fibres courtes car on ne peut pas contrôler la quantité et la position des fibres déposées, puisqu’elles ne font qu’un avec la matrice.
Avantages et limites des fibres courtes et des fibres longues
Comme nous le savons, parmi les principaux avantages de l’impression 3D composite figurent une plus grande flexibilité et vitesse de production, ainsi que la possibilité de créer des pièces complexes par rapport aux méthodes plus traditionnelles. En outre, comme nous venons de le mentionner, un avantage important de cette technologie, à condition d’utiliser des fibres continues, est qu’elle permet de contrôler le processus de dépôt et de décider où et comment placer les renforts pour les pièces finales.
Les deux types de fibres offrent une résistance mécanique supérieure à celle des plastiques non renforcés. Elles améliorent notamment la rigidité du matériau et augmentent sa résistance à la fatigue et aux chocs. En outre, les fibres telles que les fibres de carbone sont très légères, ce qui permet de réduire le poids des pièces. De même, les fibres courtes et longues présentent certaines limites. Par exemple, la nécessité d’un équipement d’impression 3D spécifique pour les produire. De nombreux aspects doivent être pris en compte lors de la transformation des matériaux composites, comme l’adhérence entre la fibre et la matrice plastique, qui peut constituer un défi.
La principale limite des fibres courtes par rapport aux fibres longues est qu’elles fournissent un renforcement moins efficace. En effet, l’orientation et la distribution des fibres courtes le long du composite sont plus aléatoires, alors que les fibres continues sont constantes. Par conséquent, l’effet de renforcement des fibres courtes est moins prononcé, ce qui peut s’avérer insuffisant pour les applications nécessitant une résistance élevée. Toutefois, l’un des principaux avantages des composites à fibres courtes est qu’ils sont plus faciles à mettre en œuvre et généralement moins chers que les composites à fibres continues. Enfin, les fibres courtes peuvent être utilisées avec une plus grande variété de matériaux plastiques, ce qui permet une grande souplesse de conception.
Applications
Le choix de la fibre et de la matrice polymère dépend bien évidemment de l’application et des performances requises. Les fibres longues sont idéales pour les applications nécessitant une résistance et une rigidité élevées, tandis que les fibres courtes conviennent mieux aux projets nécessitant une facilité de traitement et des coûts moindres. C’est pourquoi les fibres continues sont le plus souvent utilisées pour les composants structurels dans les secteurs de pointe, tels que l’automobile (renforts de châssis ou composants intérieurs) ou l’aérospatiale (structures de soutien et composants d’aéronefs). Elles peuvent également être utilisées dans des produits de consommation nécessitant une grande résistance, comme les vélos ou les équipements sportifs. D’autre part, les composites à fibres courtes imprimés en 3D sont également couramment utilisés pour produire des prototypes. Ils sont aussi souvent utilisés pour des pièces dans l’industrie de l’emballage, la robotique, les produits de consommation et d’autres composants qui ne nécessitent pas une grande résistance à la traction.
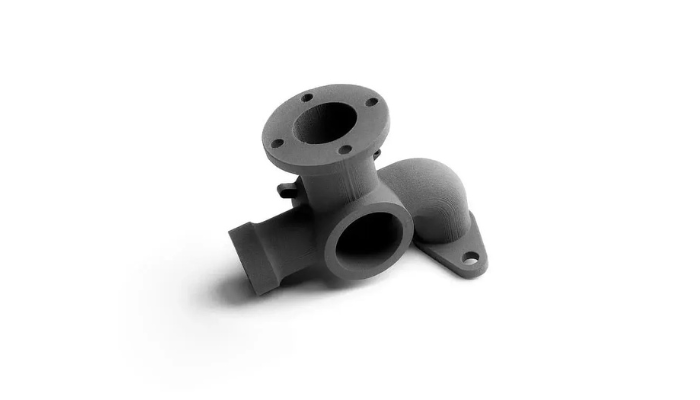
Pièce en PEEK renforcée en fibres de carbone (crédits photo : Weerg)
Fabricants et prix
Les solutions d’impression 3D pour les composites à fibres courtes et longues, bien qu’elles ne soient pas aussi nombreuses que celles pour les polymères et les métaux standard, sont très variées, allant des bras robotisés aux imprimantes industrielles en passant par les solutions de bureau. Parmi les fournisseurs de solutions d’impression 3D à fibres continues, Markforged propose la technologie CFF (Continuous Fibre Fabrication) et une gamme de solutions industrielles et de bureau. Celles-ci sont capables d’imprimer des composites PLA, TPU, Nylon blanc, Onyx™ et ULTEM renforcés par de la fibre de carbone, du Kevlar ou de la fibre de verre. Anisoprint propose également des solutions pour l’impression 3D avec des fibres continues en utilisant la technologie de coextrusion de fibres composites (CFC). Les solutions de bureau offrent une grande flexibilité dans le choix des matériaux grâce à un système ouvert, tandis que la solution industrielle ProM IS 500 est compatible avec les plastiques à haute performance tels que le PEI, le PEEK, le PEKK et d’autres. D’autres entreprises proposant des solutions d’impression 3D à fibres continues sont Continuous Composites ou CEAD, qui offre une solution LFAM.
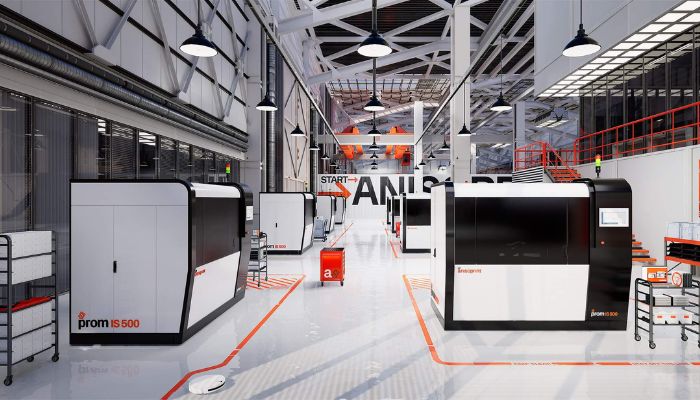
Crédits photo : Anisoprint
De plus en plus de jeunes entreprises étudient et brevettent de nouveaux procédés d’impression 3D pour les composites à fibres continues, notamment Moi Composits, SphereCube, Fabheads, 9T Labs et Arevo.
Sachez qu’il n’existe pas seulement des technologies de renforcement qui ont lieu pendant le processus de production. Par exemple, la start-up espagnole Reinforce 3D a conçu la technologie CFIP (Continuous Fibre Injection Process) pour renforcer les pièces avec des fibres continues dans la phase de post-traitement, après la fabrication additive.
En ce qui concerne les fabricants d’imprimantes 3D composites à fibres courtes, on trouve principalement des fabricants de machines FFF capables de traiter des matériaux de haute performance renforcés par des fibres de carbone ou d’autres fibres. Il s’agit notamment de Roboze, Stratasys, 3ntr, miniFactory, BigRep, WASP ou Creality (la liste n’est pas exhaustive).
Enfin, si on regarde les prix, la principale différence est liée au type de machine utilisé. Pour l’impression 3D de fibres courtes et longues, le prix est généralement élevé pour les solutions industrielles car il s’agit de matériaux qui nécessitent des conditions d’impression particulières, telles que des températures élevées pour la buse, la chambre, etc. Les machines de bureau pour l’impression 3D de composites à fibres courtes peuvent être vendues à partir de 400 euros, tandis que celles pour l’impression 3D de fibres continues commencent à environ 9 000 euros. En ce qui concerne les solutions industrielles, les fabricants ne communiquent pas toujours les prix, qui peuvent atteindre plusieurs milliers d’euros selon le procédé et la taille. Dans ce cas, il est possible de demander des devis directement sur leurs sites.
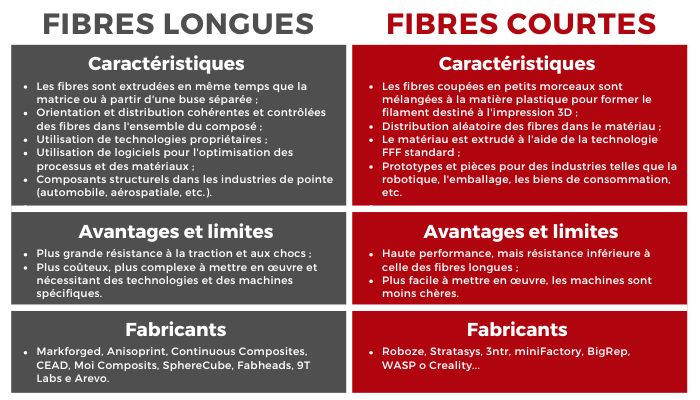
Crédits photo : 3Dnatives
Utilisez-vous des fibres courtes ou longues en impression 3D ? Lesquelles préférez-vous ? Partagez votre avis dans les commentaires de l’article. Retrouvez toutes nos vidéos sur notre chaîne YouTube ou suivez-nous sur Facebook ou LinkedIn !