Fabrication additive et soustractive : rivalité ou complémentarité ?
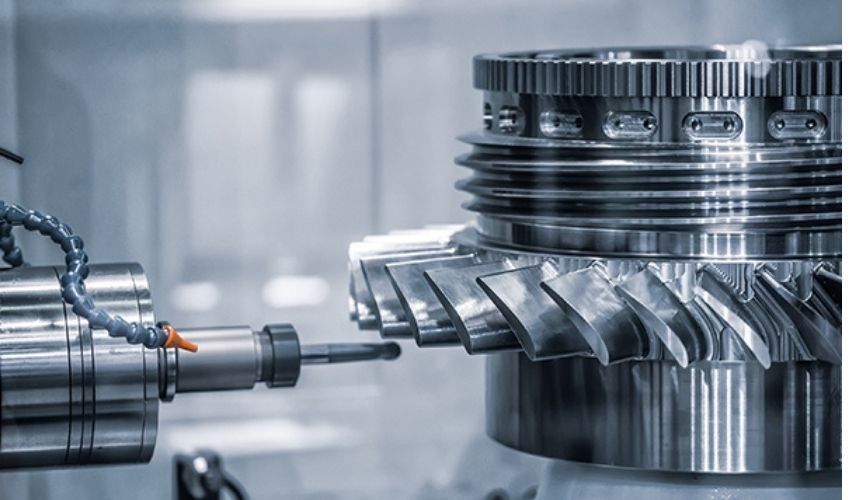
Alors que de plus en plus d’entreprises optent pour la fabrication additive, la fabrication dite soustractive reste tout de même la plus utilisée à ce jour par l’industrie. À l’heure actuelle, l’impression 3D est d’ailleurs principalement employée pour compléter les méthodes de fabrication soustractive. Comme leur nom l’indique, à l’inverse de la fabrication additive, ces techniques consistent à retirer de la matière afin de produire une pièce de la dimension souhaitée. Elles sont aujourd’hui déployées dans de nombreuses industries, comme l’aéronautique, l’automobile, auprès des métallurgistes, etc.
Tout comme la fabrication additive et ses multiples procédés, de nombreuses méthodes de fabrication soustractive existent – vous avez sûrement dû entendre le terme « usinage CNC ». Acronyme de Computer Numerical Control, il regroupe les techniques d’enlèvement de matière, techniques qui sont basées sur un programme numérique qui vient commander les machines outils. On parle ici de perçage, tournage, fraisage ou encore d’alésage. L’usinage CNC est aujourd’hui compatible avec une large gamme de matériaux, des plastiques aux métaux. Les techniques de fabrication soustractive ne font pas toutes appel à un programme numérique – on reviendra donc dans un second temps sur quelques méthodes de découpage.
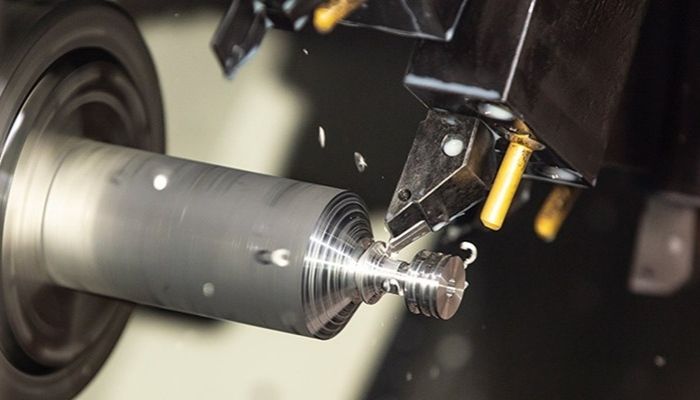
Crédits photo : Protolabs
Mieux comprendre les processus d’usinage CNC
Comme expliqué ci-dessous, l’usinage CNC regroupe plusieurs procédés ; on commencera par le tournage et l’alésage. Ces derniers utilisent une pièce mobile sur un axe rotatif. L’énergie nécessaire à l’usinage de la pièce est apportée par le mouvement même de celle-ci. Ces méthodes permettent de fabriquer toutes les pièces modélisées par rotation. Concrètement, il s’agit d’un dessin 2D qui se réplique à l’infini selon un axe de rotation formant ainsi un modèle 3D. Malgré leurs noms différents, le tournage et l’alésage sont très similaires puisqu’ils utilisent tous deux le même principe. La différence principale est que l’alésage agit à l’intérieur de la pièce tandis que le tournage intervient à l’extérieur. Permettant de concevoir des pièces à partir de bois, de métaux et de certains plastiques, les tourneuses et aléseuses sont aujourd’hui présentes dans de nombreuses industries, à l’image des secteurs automobile, aérospatial, médical ou encore de la décoration.
Passons maintenant à une autre technique, le fraisage. De par sa précision, sa possibilité de créer des pièces avec des cavités internes et sa capacité à usiner une pièce, le fraisage est un véritable atout au sein d’un processus de fabrication. Cette technique emploie des fraises permettant de découper de la matière latéralement. Ainsi, lorsque la fraise est dans le matériau, elle peut se déplacer de manière perpendiculaire et enlever de la matière selon son tracé. Le fraisage est compatible avec de nombreux matériaux grâce à une variété d’outils interchangeables adaptée à diverses tâches et matériaux. Néanmoins, cette méthode dispose de certains inconvénients pouvant la rendre difficile d’accès. Par exemple, l’usinage d’une pièce est souvent divisé en plusieurs étapes/opérations et celles-ci nécessitent régulièrement un changement d’outil.

Le procédé de fraisage
Le perçage et le fraisage utilisent des outils très similaires, mais qu’il ne faut pas confondre. Le perçage sert uniquement à effectuer des trous ronds à l’aide d’une mèche. Alors que le fraisage offre une plus grande liberté de fabrication, notamment grâce à la possibilité de réaliser des trous ou formes d’un diamètre supérieur au sien, le perçage, lui, permet de percer des trous d’un diamètre égal à celui de la mèche. Malgré ses multiples avantages, le fraisage est beaucoup plus lent que le perçage lorsqu’il s’agit de percer des trous, c’est pour cette raison que ce dernier est plus adapté pour effectuer plusieurs mêmes découpes à la suite.
Alors que l’usinage CNC englobe de nombreuses techniques, la fabrication soustractive ne se résume pas uniquement à celles-ci. D’autres méthodes, comme celles de découpage, sont également utilisées par de nombreux secteurs.
Une variété de techniques de découpage
Quand certains ont recours à la découpe laser, comme l’industrie manufacturière automobile qui utilise un laser pour fabriquer des pièces précises telles que des plaquettes de frein, d’autres optent pour l’électro-érosion. Aussi appelée EDM, pour Electrical Discharge Machining, cette technique se décline selon 3 formes : l’électroérosion par fil, l’électroérosion par enfonçage et le perçage rapide, qui se distingue du perçage classique par sa capacité à réaliser des trous plus fins et plus profonds grâce à une électrode. Si ces différentes méthodes sont relativement lentes, elles se distinguent des autres par leur précision. Fonctionnant par décharges électriques, l’EDM peut fabriquer des pièces à partir de matériaux conducteurs.
À l’Electrical Discharge Machining, s’ajoute la découpe laser. Elle permet de découper rapidement et précisément plusieurs matériaux grâce à un laser d’une puissance de plusieurs centaines de watts – par exemple des pièces allant jusqu’à 1 mm² avec une tolérance de plus ou moins 20 microns. En plus de la découpe, les machines lasers sont également capables de graver. Les découpeuses lasers sont présentes sous deux formes : les lasers CO2 et les lasers fibrés, utilisés pour la découpe et la gravure des métaux. Malgré leurs avantages, les découpeuses lasers présentent quelques inconvénients ; lors de l’opération d’une telle machine, des fumées nocives peuvent être dégagées. De plus, les lasers coupant la matière par chaleur, les lasers eux-mêmes peuvent surchauffer. Il est donc nécessaire de les refroidir, ce qui nécessite souvent des machines supplémentaires.
Enfin, parmi les principaux procédés de fabrication soustractive et plus précisément de découpage, on retrouve la découpe par jet d’eau. Ce processus repose sur l’utilisation d’un jet d’eau, accompagné d’un abrasif, qui vient frapper la surface du matériau à grande vitesse. Ce phénomène entraîne un retrait de la matière et sa séparation afin de dessiner la forme finale souhaitée. Un compresseur haute pression est nécessaire pour générer ce jet d’eau. La nature du jet et le matériau en question viendront influencer la profondeur et la vitesse de coupe. Cette technique est prisée par les industries de l’aéronautique, de l’automobile ou de la mécanique. Elle offre notamment une grande précision, une compatibilité avec de nombreux matériaux et a contrario de différents procédés soustractifs, elle n’est pas nocive. Tandis que d’autres procédés génèrent des copeaux, de la poussière ou de la fumée, la découpe par jet d’eau élimine tous ces déchets puisque le jet d’eau les emporte sur son chemin.

Le procédé de découpe par jet d’eau (crédits photo : Fogepack Systèmes)
Inconvénients et avantages comparés à la fabrication additive
Comme énoncé précédemment, le principal avantage des techniques de fabrication soustractive réside probablement dans leur capacité à offrir une grande précision dimensionnelle. Contrairement à la plupart des procédés d’impression 3D qui reposent sur la chaleur pour fonctionner, la fabrication soustractive permet de construire des pièces à température ambiante évitant ainsi des problèmes de précision dimensionnelle, liés au travail (contraction/rétraction) des matériaux.
Pour assurer la précision dimensionnelle de la fabrication soustractive, il convient de maîtriser l’environnement. Par exemple, si l’on souhaite concevoir une pièce à partir d’un bloc d’acier, il est obligatoire de ramener le matériau dans la pièce où se déroulera la découpe au moins 3 jours en amont, sinon elle changera de dimension (travail) en fonction de la température et de l’humidité.
Les procédés de fabrication soustractive bénéficient également d’un plus grand panel de matériaux compatibles. Si l’on compare à l’impression 3D, où il est nécessaire de posséder plusieurs imprimantes basées sur différents procédés si l’on souhaite utiliser des matériaux différents, il est possible de créer des pièces en métal, en plastique ou en bois sur la même machine.

La fabrication soustractive offre une grande précision dimensionnelle
Cependant, les procédés de fabrication soustractifs ont d’importants inconvénients. Tout d’abord, a contrario de l’impression 3D, les différentes méthodes de production laissent derrière elles d’importantes quantités de déchets, quand la fabrication additive séduit par sa faculté à n’utiliser que la quantité de matière nécessaire. En usinage notamment, il convient d’aspirer les copeaux et autres poussières pendant le processus de fabrication pour limiter l’excédent de matière inutile pouvant gêner le processus de découpe. En plus de la poussière engendrée par la fabrication soustractive, il arrive également que celle-ci dégage de la fumée pouvant se révéler très nocive pour les opérateurs, fait très fréquent lorsque l’on utilise un laser ou un procédé EDM.
De plus, la fabrication soustractive n’offre pas la même liberté de fabrication que l’impression 3D – une pièce imprimable en une fois nécessitera parfois plusieurs opérations, l’utilisation de différentes machines et une scission en plusieurs parties à assembler pour être répliquée par fabrication soustractive.
Enfin, il est plus difficile de réaliser des géométries complexes avec des procédés d’enlèvement de matière. La fabrication additive permet une liberté plus importante lors de la conception. Autrement dit, le designer n’aura pas à se poser la question des contraintes imposées par les machines-outils utilisées et sera donc en mesure de laisser libre cours à son imagination, n’étant pas limité par les capacités de fabrication.
La complémentarité de la fabrication soustractive et de la fabrication additive
Si les deux technologies sont régulièrement mises en opposition, elles ont pour le moment des applications bien distinctes. Et c’est d’ailleurs pour cette raison qu’elles sont la majorité du temps utilisées de manière complémentaire. Depuis le début de sa forte croissance, l’impression 3D est le plus souvent employée à des fins de prototypage. De par les bénéfices qu’elles offrent, les technologies 3D permettent de fabriquer rapidement et à faible coût plusieurs pièces et offrent donc la possibilité de réaliser différentes itérations. Une fois la forme, les matériaux et pièces déterminés, il est possible de la fabriquer en grande série grâce aux méthodes de fabrication soustractive. Plusieurs procédés, à l’image de la découpe laser et de la découpe par jet d’eau, permettent de concevoir un important nombre de pièces en peu de temps. Cependant, d’autres méthodes, comme l’usinage CNC, peuvent prendre énormément de temps. Cette technique demande notamment une importante étape de programmation ainsi qu’une présence humaine quasi nécessaire. Aujourd’hui, l’usinage CNC est principalement utilisé dans la fabrication de moules servant à l’injection, une technique de fabrication formative.
De plus, si la fabrication soustractive permet de réparer des objets, l’impression 3D offre plus de possibilités dans ce domaine. On pense notamment au procédé de dépôt de matière sous énergie concentrée (DED) qui permet entre autres de réparer des pièces métalliques sans avoir à les changer. Concrètement, la technologie est capable d’ajouter de la matière à une pièce déjà existante, évitant ainsi d’avoir à réaliser des assemblages ou de remplacer de larges pièces inutilement. Plus globalement, les technologies 3D permettent de reproduire des pièces défaillantes ou usées par le temps, le tout à la demande et en petite série. Au lieu de jeter, l’utilisateur peut réparer sa pièce et minimiser son impact environnemental.
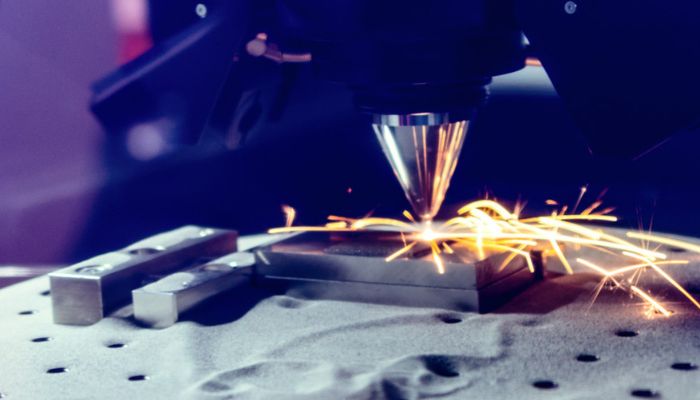
La technologie DED permet de réparer des pièces. (Crédits photo : AdvancedPowders)
Malgré leurs différences et leurs procédés, la fabrication soustractive et la fabrication additive vont souvent de pair. De par leurs caractéristiques respectives, ces deux types de fabrication forment une complémentarité permettant de créer rapidement des pièces précises jamais imaginées auparavant. Afin de mêler ces techniques de fabrication, certains projets de consortium ont d’ailleurs été imaginés, à l’image de l’organisation Hybrid Advanced Manufacturing – Integrating Technologies, qui a pour objectif d’offrir aux entreprises la liberté de conception de la fabrication additive et la précision de la fabrication soustractive.
Que pensez-vous des procédés de fabrication soustractive ? N’hésitez pas à partager votre avis dans les commentaires de l’article. Retrouvez toutes nos vidéos sur notre chaîne YouTube ou suivez-nous sur Facebook ou Twitter !
Article co-écrit par Philippe Girardie et Elliot Saldukaite
*Crédits photo de couverture : Turcon
EDM pour des matériaux non conducteurs (pierre, béton)… vous êtes sûr ?
Bonjour Rémi.
Merci de votre vigilance – L’EDM est un processus fonctionnant par décharges électriques entre deux électrodes et est donc seulement compatible avec des matériaux conducteurs (métaux). Il ne fonctionne effectivement pas avec la pierre ou le béton.
Quelques remarques:
Si la problématique soulevée est juste, le déroulé survole le sujet avec des oublis:
– l’usinage, quelle que soit la technique employée impose des efforts de coupe aux pièces (variable selon les conditions de coupe utilisées) qui peuvent de déformer d’une part et qu’il faut donc brider d’autre part en ajoutant des efforts mécaniques supplémentaires. Autre point important dans l’usinage, les conditions d’accès de l’outil à la géométrie à enlever, d’où l’usage de machines agiles (multi axes, robots par exemple)
– les précisions atteintes concernent autant les dimensions et les respect des formes géométriques souhaitées que les états de surfaces. Sur ces 3 points les technologies additives pour les métaux sont incapables d’atteindre les qualités nécessaires au bon fonctionnement des mécanismes courants, alors ne parlons pas de domaines exigeants. Pour aller plus loin on utilise des technologies d’enlèvement de matière par abrasion qui conjuguent précision (dimensionnelle et d’états de surfaces) avec peu d’efforts de coupe.
– Les technologies additives pour les métaux fonctionnent toutes avec des traitements thermiques soit en cours de cycle « d’impression » soit pendant les post-traitements. Cela implique des déformations des géométries et des états de surfaces dégradés qui vont donc réclamer des opérations d’enlèvement de matière localisées pour finaliser les pièces.
Il ne faut pas raisonner en terme de concurrence entre procédés additifs et les autres mais en processus complexes qui en les combinant permettent d’obtenir des pièces capables de remplir le plus efficacement et avec des coûts acceptables des fonctions plus exigeantes.
Les défis sont ailleurs, par exemple commet réaliser une pièce légère et résistante avec des structures lattices localement et des zones d’assemblage ou de guidage ?
Il faut savoir concevoir et dimensionner avec les bons outils numériques, puis créer un processus partant du matériau pour finir par le montage de l’élément. A chacune des étapes les défis techniques sont importants et vont bien au delà de savoir qui de l’enlèvement de matière ou de l’additif est le meilleur. Chacun a sa fenêtre d’usage, l’art de l’ingénierie est de les connaitre, les combiner, parfois les pousser au delà des usages connus pour arriver à la bonne performance.
La réparation de pièces complexes par dépôt localisé de matière est connue depuis très longtemps (soudure par exemple) et nécessite obligatoirement une opération de finition…en usinage ou rectification (enlèvement de matière)
Pour finir, une gomme dans une main experte permet de corriger et d’affiner un trait dessiné avec un crayon même le plus fin, mais elle ne sert à rien sans le tracé initial du crayon…