Quel est le rôle de la fabrication additive en Formule 1 ?
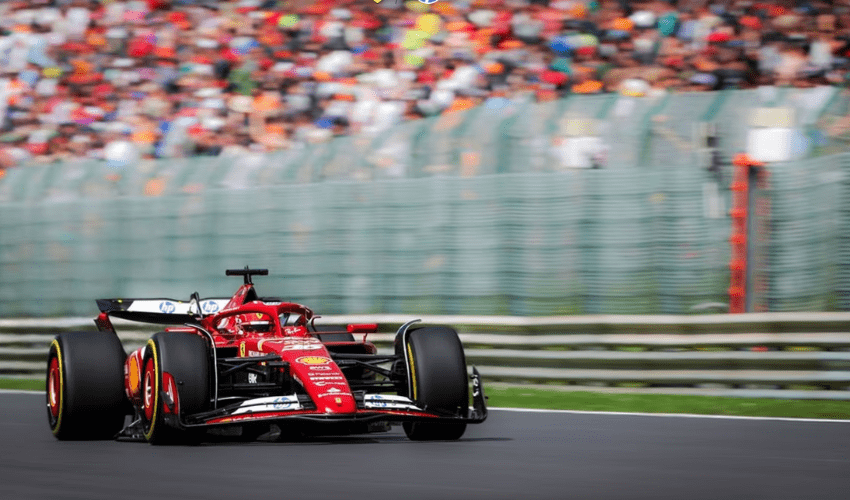
La Formule 1, sport automobile par excellence, est un domaine exigeant où la recherche de performance et de vitesse est essentielle. Mais derrière chaque sensation offerte aux spectateurs, chaque fraction de seconde compte. Par ailleurs, la performance ne repose pas uniquement sur les compétences du pilote, mais également sur l’optimisation technique de la voiture. Au cœur de cette recherche constante, l’impression 3D s’est imposée comme une technologie révolutionnaire. Les voitures de ces dernières années illustrent bien cette avancée, utilisant de plus en plus l’impression 3D pour maximiser leur performance. Introduite dans le sport automobile au début des années 2000, la fabrication additive permet de créer des pièces à la fois légères et performantes tout en respectant les strictes réglementations de la FIA (Fédération Internationale de l’Automobile).
La Formule 1 ne cesse d’évoluer, adoptant des méthodes de prototypage rapide et de production de pièces complexes grâce à l’impression 3D. Les équipes de F1 l’intègrent de plus en plus. Au fil des années, des partenariats se sont établis entre les écuries et les pionniers de l’impression 3D. Quels sont les usages concrets de l’impression 3D en Formule 1 ? Quels avantages et défis cette technologie présente-t-elle ? Et quelles perspectives d’avenir offre-t-elle dans ce domaine si exigeant ? Attachez vos ceintures et découvrez-le dans cet article.
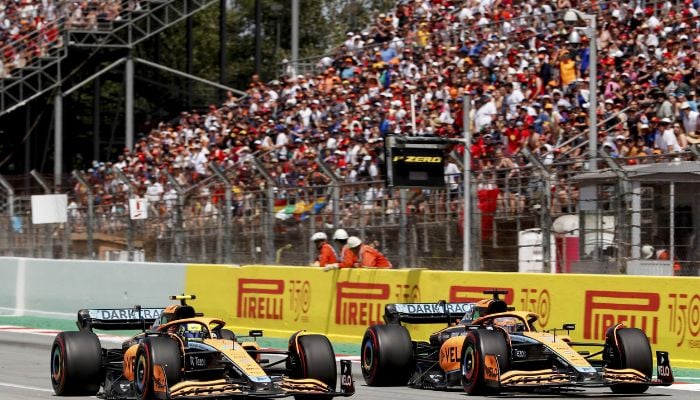
Mclaren est une des écuries qui utilise le plus l’impression 3D pour ses monoplaces (crédits photo : Stratasys)
Des écuries tournées vers l’impression 3D
Le sport automobile est connu pour son innovation constante, et la Formule 1 est souvent en tête en matière de nouvelles technologies. En effet, l’impression 3D assure le développement des voitures de Formule 1, avec des écuries qui se tournent de plus en plus vers les leaders de cette technologie pour optimiser leurs performances. Voici quelques exemples : Red Bull Racing, champion constructeur depuis 2022, collabore avec Hexagon Manufacturing Intelligence depuis 18 ans. Ce partenariat a permis à l’équipe de tester et d’adopter des technologies innovantes tout en assurant la sécurité et la fiabilité de ses voitures, gagnant ainsi des fractions de seconde sur le circuit. Red Bull Racing utilise notamment des jumeaux numériques et des simulations pour concevoir et tester virtuellement leurs voitures avant de créer des prototypes physiques.
McLaren F1 Racing utilise 20 imprimantes 3D Stratasys pour produire plus de 9 000 pièces par an, exploitant l’impression 3D pour créer des prototypes. Visa Cash App RB a également collaboré avec ROBOZE pour repenser la conception et la production de composants essentiels pour leurs monoplaces. De son côté, Alpine bénéficie du soutien de 3D Systems depuis plus de 20 ans, en disposant de nombreuses machines SLA et LPBF. Pat Warner, ADM Manager chez Alpine, explique : « 3D Systems est notre partenaire principal pour tous nos équipements et matériaux internes, que nous externalisons ensuite auprès de diverses entreprises selon les besoins. »
Ainsi, l’usage de l’impression 3D en Formule 1, bien que présent depuis un certain temps, se généralise de plus en plus. Selon Pat Warner, l’ancienne écurie de Formule 1 Renault F1 Team avait acquis sa première imprimante 3D dès 1998. Toutefois, l’importance de l’impression 3D a véritablement augmenté au cours des années 2010.
Quelles sont les applications concrètes et les technologies de fabrication additive utilisées en Formule 1 ?
Dans le domaine des applications, l’impression 3D se distingue par son efficacité en matière de prototypage rapide, une caractéristique particulièrement bénéfique pour les écuries de Formule 1. Cette technologie permet de concevoir, de fabriquer et de tester de nouvelles pièces, accélérant ainsi le cycle de développement d’innovation. De plus, l’impression 3D n’est pas seulement réservée aux prototypes : elle est également utilisée pour produire des composants fonctionnels qui sont directement intégrés aux véhicules de course.
Concernant les technologies employées, le dépôt de matière fondue (FDM) est largement utilisé pour le prototypage rapide et la production d’échantillons en Formule 1. Les polymères, notamment les nylons, sont fréquemment choisis en raison de leurs propriétés mécaniques. Par ailleurs, les thermoplastiques haute performance comme le PEKK et le PEEK sont couramment utilisés. Ces matériaux sont privilégiés pour leur grande résistance à la chaleur, essentielle dans un environnement où les températures peuvent dépasser les 1 000 degrés, comme c’est souvent le cas pour certaines parties d’une monoplace. En 2014, McLaren a innové en introduisant la première pièce imprimée en 3D pour ses voitures de course : un couvercle de soupape pour le moteur, fabriqué grâce à la technologie FDM. Plus tard, l’écurie a élargi son utilisation de l’impression 3D en produisant un support structurel pour fixer la conduite hydraulique sur la voiture de course MCL32. Ce support, conçu avec la technologie FDM et réalisé en nylon renforcé en fibres de carbone, a été imprimé en seulement quatre heures.
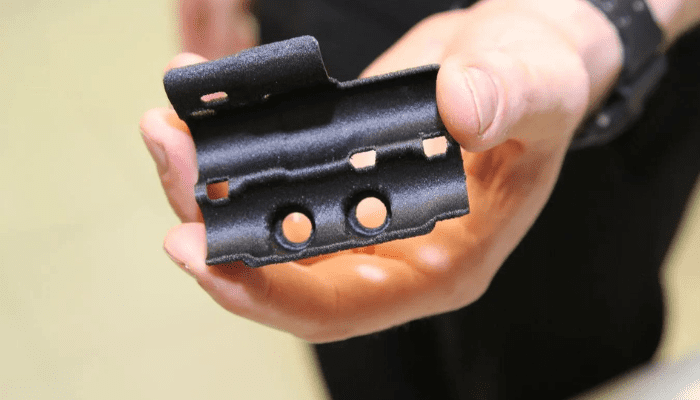
Le support de conduite hydraulique imprimé en 3D pour la monoplace MCL32 grâce à la technologie FDM. (crédits photo : Mclaren)
« La stéréolithographie (SLA) est largement utilisée pour fabriquer les éléments visibles de notre soufflerie chez Alpine, » indique Pat Warner. « Tant la carrosserie que de nombreuses structures internes sont produites avec les technologies SLA et SLS. » Contrairement à la technologie FDM, le SLA permet de réaliser des pièces avec des géométries complexes et un haut niveau de détail, répondant souvent à des exigences spécifiques. Patrick Warner souligne que les tests en soufflerie requièrent la fabrication de 600 pièces par semaine via la fabrication additive, un volume que seule une équipe de cinq ingénieurs spécialisés peut assurer. Il précise : « Les méthodes de fabrication traditionnelles ne pourraient pas répondre à cette demande. »
Les technologies de fabrication additive utilisant un lit de poudre, telles que le frittage sélectif par laser (SLS) et la fusion laser (DMLS), sont couramment employées en Formule 1. Par exemple, en 2017, Ferrari a utilisé la technologie DMLS pour créer un élément aérodynamique pour sa voiture. Contrairement aux méthodes FDM ou SLA, l’impression 3D par fusion sur lit de poudre présente plusieurs avantages, comme la capacité de produire des pièces plus isotropes, souvent sans nécessiter de structures de soutien, ce qui diminue le temps de post-traitement. Les pièces métalliques fabriquées incluent fréquemment des échappements, des composants de moteur et des suspensions.
Quels sont les avantages de la fabrication additive en Formule 1 ?
La fabrication additive présente de nombreux avantages par rapport aux méthodes de fabrication traditionnelles, notamment en Formule 1, où les exigences sont particulièrement élevées. En Formule 1, l’une des priorités est de diminuer le poids des véhicules, ce qui se traduit par une série d’améliorations : une accélération plus rapide, une vitesse de pointe accrue, une meilleure maniabilité, un freinage plus efficace, une consommation de carburant réduite et une moindre sollicitation des pneus. L’impression 3D s’avère être une solution idéale pour atteindre cet objectif, en permettant la fabrication de composants plus légers. La rapidité de production des pièces est également importante pour rester compétitif. Si une pièce casse ou doit être modifiée de toute urgence pendant une course, l’impression 3D offre une solution immédiate. Elle permet de concevoir, produire et installer des pièces en un temps record, aidant ainsi les équipes à résoudre rapidement les problèmes sur le circuit ou à intégrer des améliorations pour les courses suivantes.
Elle offre aussi une grande flexibilité de conception. Les ingénieurs peuvent expérimenter avec des géométries complexes et des matériaux innovants sans les contraintes des méthodes de fabrication traditionnelles, comme le moulage ou l’usinage. Il est possible de créer des composants avec des structures internes complexes, telles que des treillis ou des structures en nid d’abeille, qui sont impossibles à réaliser avec les méthodes traditionnelles.
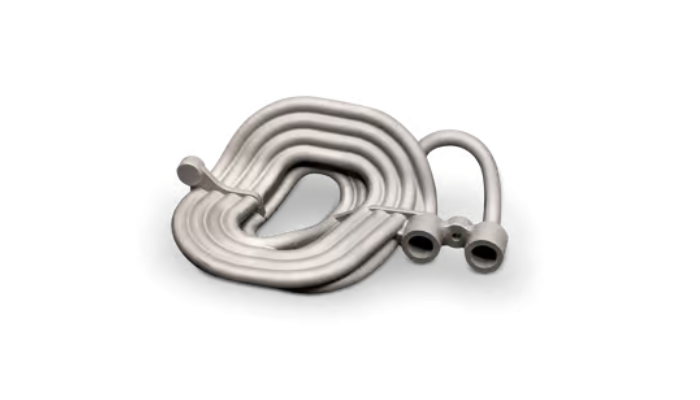
La fabrication additive a permis à Alpine F1 Team d’optimiser la longueur des ressorts d’amortisseur tout en intégrant toutes les fonctionnalités nécessaires dans un espace compact. (crédits : 3D Systems)
Bien que la fabrication additive offre de nombreux avantages, elle ne remplace pas les méthodes de fabrication traditionnelles, mais les complète. En effet, la synergie entre les deux techniques peut grandement optimiser le processus de production. Par exemple, les pièces essentielles ou nécessitant une grande résistance peuvent être produites par des méthodes classiques, tandis que l’impression 3D peut être employée pour des composants complexes ou pour des prototypes rapides. Cela permet de tirer parti des atouts spécifiques de chaque technique. Par exemple, pour les pièces en plastique, le moulage par injection reste souvent la méthode privilégiée en raison de sa maturité technologique et de la variété de matériaux qu’il propose. Néanmoins, l’impression 3D possède un avantage distinct : elle ne requiert pas de moules, ce qui facilite la création de pièces complexes. Souvent, c’est le moule lui-même qui est fabriqué par impression 3D avant de procéder à l’usinage de la pièce finale. Comme le souligne Pat Warner : « La fabrication additive ne remplace pas le moulage par injection ni l’usinage, mais constitue un outil supplémentaire dans l’arsenal de production. Chaque technologie a son rôle et s’harmonise pour réaliser la pièce désirée. »
Vers une Formule 1 écologique ?
Sur le plan environnemental, l’adoption croissante de l’impression 3D s’inscrit dans l’objectif de la Formule 1 de parvenir à des émissions nulles d’ici 2030. Des changements significatifs seront également mis en place dès 2026, incluant des exigences de durabilité sur les monoplaces. McLaren illustre cette tendance à travers son partenariat avec Stratasys, en utilisant des matériaux recyclés en guise de filaments pour réduire les déchets. Cependant, l’intégration de l’impression 3D dans la Formule 1 n’est pas sans défi. Pat Warner explique : « Nous disposons d’une liste de matériaux autorisés pour la voiture, établie par la FIA. Bien que nous puissions proposer l’ajout de nouveaux matériaux à cette liste, cela nécessite l’accord de tous les membres. En conséquence, nos options sont quelque peu limitées. »
Que pensez-vous du rôle de la fabrication additive en Formule 1 ? Selon vous, cette technologie est-elle suffisamment présente ? Partagez votre avis dans les commentaires de l’article. Retrouvez toutes nos vidéos sur notre chaîne YouTube ou suivez-nous sur Facebook ou LinkedIn !
*Crédits photo de couverture : Ferrari
2600° autour du moteur c’est chaud un peu non ? L’alu ça fond vers 600/700 deg et le PEEK à un TG à 140°. N’y aurait-il pas un 0 de trop ?