Quel est le rôle de la fabrication additive dans le secteur automobile ?
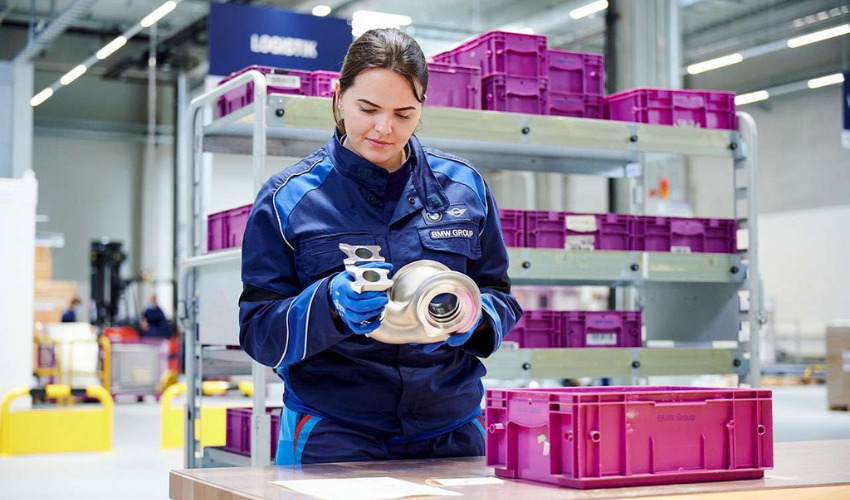
Dans l’industrie automobile, les équipementiers ont historiquement utilisé la fabrication additive pour le prototypage rapide. Cependant, ces dernières années, les progrès en matière de technologies ont lentement transformé la manière dont les pièces d’utilisation finale sont conçues, fabriquées et distribuées. L’étude de Deloitte sur l’opportunité de la 3D dans l’industrie automobile explique que dans la « voie standard actuelle de la fabrication additive », les entreprises ne cherchent pas à modifier radicalement les chaînes d’approvisionnement ou les produits. La technologie est adoptée pour créer des itérations de conception, pour améliorer la qualité par le biais d’un prototypage rentable et pour créer des pièces d’outillage spécifiques. Néanmoins, il existe d’autres voies pour l’impression 3D dans le secteur automobile, qui transforment les produits et les chaînes d’approvisionnement de manière plus radicale. C’est ce que nous allons explorer dans l’aperçu suivant de l’impact de la fabrication additive l’industrie automobile. D’ailleurs, le rapport de SmarTech Analysis a révélé que d’ici 2029, l’impression 3D automobile aura généré 9 milliards de dollars de revenus provenant de la seule production de pièces finies, contre 1,39 milliard de dollars en 2019. Alors, vers où la fabrication additive se dirige-t-elle dans ce secteur ?
Avantages de la pré-production
L’accélération de la phase de conception pendant le développement d’un nouveau produit est essentielle dans tout secteur. Heureusement, l’impression 3D peut remplacer la production CNC coûteuse et particulièrement longue à développer. Plus précisément, elle permet aux concepteurs de passer par plusieurs itérations de manière rentable avant de décider du produit final. Le processus est le suivant : une fois que les concepteurs ont identifié un besoin de l’utilisateur et ont généré des idées pour répondre à ce besoin, ils développent un prototype. L’étape suivante consiste à tester ce prototype afin d’en améliorer la conception. Ce processus itératif est aussi ce que nous appelons le prototypage rapide.
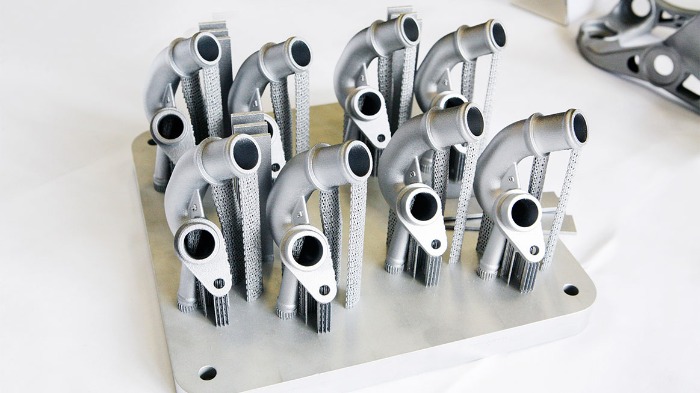
Exemple de connecteurs à eau métalliques imprimés en 3D pour le moteur de l’Audi W12 (crédits photo : Volkswagen AG)
Volkswagen, par exemple, travaille avec des technologies d’impression 3D depuis 25 ans. L’année dernière, le constructeur automobile a notamment investi dans deux autres imprimantes 3D Stratasys. Peter Bartels, responsable du centre de présérie de Volkswagen, a déclaré que ces investissements représentent « des capacités supplémentaires qui renforcent les opérations d’impression 3D et permettent d’optimiser davantage le processus de conception. » De plus, la conception des outils (poignées, gabarits et fixations) peut également être optimisée et produite à moindre coût. L’outillage joue un rôle important sur la chaîne de montage pour fabriquer des produits répétables et de haute qualité. Ces applications sont ce que Deloitte appelle la « voie standard actuelle de la fabrication additive » dans le secteur automobile.
Le segment croissant des pièces finies
Plusieurs OEM se sont intéressés à l’impression 3D pour développer des pièces d’utilisation finale, allant au-delà des applications de prototypage rapide. Il y a de nombreuses raisons à cela, qui peuvent être résumées comme une quête d’innovation produit dans un secteur concurrentiel comme l’automobile. Une façon d’accélérer ce caractère innovant est d’augmenter considérablement la performance d’une pièce, en réduisant son poids par exemple. L’innovation produit qui passe par la personnalisation présente également un grand intérêt, en particulier pour les constructeurs de voitures de luxe.
En effet, un avantage de l’utilisation de la fabrication additive est la production potentielle de composants plus légers, pour créer des véhicules qui consomment moins de carburant. Le rôle des logiciels de conception industrielle est donc central. Au fil des ans, les solutions de CAO et de FAO se sont considérablement améliorées, notamment pour la fabrication additive. Elles comprennent souvent des outils de conception générative, d’optimisation topologique et de génération de treillis, qui réduisent le poids total des pièces tout en maintenant ou en améliorant leur fonction. Les pièces plus légères sont souvent plus complexes. Mais comme l’impression 3D n’est pas limitée en termes de liberté de conception, contrairement aux méthodes conventionnelles, la complexité ne constitue pas un défi. Il convient de noter que la simplification des pièces est également possible grâce aux technologies 3D, par la consolidation de plusieurs pièces en une seule conception. Plus besoin de longues étapes d’assemblage, souvent complexes et chronophages.
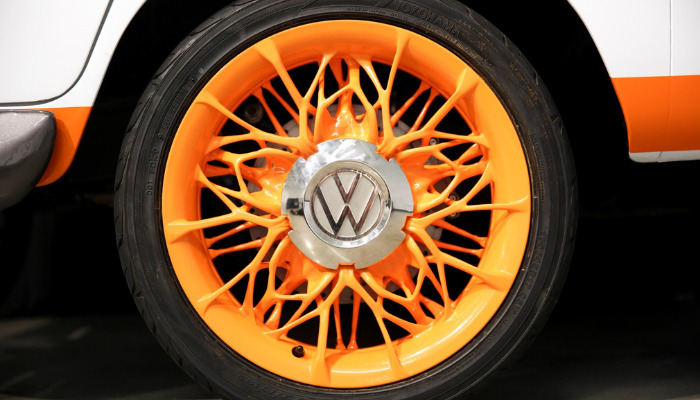
Les outils de conception générative d’Autodesk ont permis de concevoir des roues plus légères sur un Microbus Volkswagen 1962 Type 2 à 11 fenêtres (crédits photo : Volkswagen)
La fabrication additive signifie également de plus grandes possibilités de personnalisation. Certains constructeurs de voitures de luxe utilisent déjà la technologie pour fournir des designs spécialisés en fonction des besoins des clients. Les méthodes de fabrication traditionnelles telles que la CNC ou le moulage par injection ne permettraient pas de livrer des pièces uniques dans des délais compétitifs. Le coût de production de ces pièces serait également très différent. En outre, la personnalisation peut également être utilisée pour livrer des pièces de rechange, pour réparer un modèle de voiture plus ancien par exemple.
On peut prendre ici l’exemple d’application de cas d’utilisation finale qu’est le collecteur d’admission en aluminium imprimé en 3D de Ford (partie du moteur qui fournit le mélange carburant/air aux cylindres), qui a été installé dans un Hoonitruck de 1977. Selon le fabricant, cette pièce de rechange était la plus grande pièce automobile imprimée en 3D jamais produite. Il a fallu cinq jours pour l’imprimer en utilisant la machine Concept Laser X LINE 2000R de GE Additive. Historiquement, Ford est l’une des entreprises qui a mené le plus de recherches en matière d’industrialisation de la fabrication additive. En 1986, elle avait déjà investi dans une SLA 3 (la première imprimante 3D jamais fabriquée). La société a déclaré dans un communiqué de presse officiel : « Il n’a pas fallu longtemps pour voir que l’impression 3D pouvait être utilisée pour créer de nouveaux prototypes de pièces plus rapidement et plus efficacement que jamais« . Aujourd’hui, la société a imprimé plus de 500 000 pièces et « a économisé des milliards de dollars et des millions d’heures de travail« . Dans son centre de fabrication avancée de Detroit, elle a notamment investi dans des imprimantes FDM et SLS.
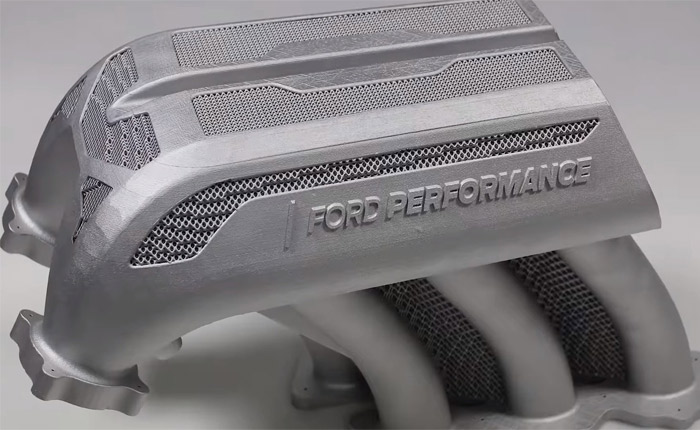
Le collecteur d’admission imprimé en 3D par Ford (crédits photo : Ford)
Un autre exemple est le groupe BMW, qui a ouvert en 2020 le Additive Manufacturing Campus, non loin de Munich. La construction de ce campus a coûté environ 15 millions d’euros. Aujourd’hui, il exploite une cinquantaine d’installations industrielles pour le traitement des métaux et des plastiques. La production de prototypes, de pièces de série, la R&D et la formation associée à la fabrication sans outillage se déroulent sur le site. Cet investissement démontre la confiance du groupe BMW dans les technologies d’impression 3D. Le groupe a initialement investi dans la fabrication additive en 1991 pour fabriquer des prototypes de voitures concept. Plus tard, de petites séries de pièces ont été produites pour les voitures de course DTM, la Rolls-Royce Phantom, la BMW i8 Roadster et la MINI, entre autres. En un an, 300 000 pièces ont été imprimées en 3D. Membre du conseil d’administration, Milan Nedeljković a commenté : « La fabrication additive fait déjà partie intégrante de notre système de production mondial aujourd’hui, et constitue un élément établi de notre stratégie de numérisation. À l’avenir, les nouvelles technologies de ce type rendront la production encore plus rapide et nous permettront de profiter encore plus pleinement du potentiel de la fabrication sans outillage. »
La chaîne d’approvisionnement change
L’étude de Deloitte souligne également que les changements mentionnés ci-dessus auront finalement un impact sur les chaînes d’approvisionnement. Aujourd’hui, les équipementiers externalisent la plupart de leurs pièces ; le rapport l’explique : « Lorsque les OEM adopteront la voie de l’évolution des produits, le résultat final sera double : des chaînes d’approvisionnement plus petites et une plus grande contribution des OEM en termes de valeur. Un effet important de la fabrication additive pourrait être de raccourcir et de simplifier les énormes chaînes d’approvisionnement automobile actuellement en place. Les équipementiers travaillent avec des milliers de fournisseurs pour se procurer les différents composants des voitures [et] recherchent constamment des moyens de réduire leurs chaînes d’approvisionnement« . Les entreprises peuvent donc tirer parti de la fabrication additive automobile pour transformer les chaînes d’approvisionnement, en produisant sur place et en réduisant les stocks de pièces.
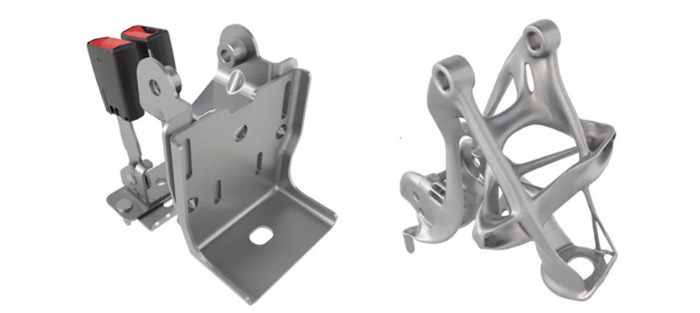
En utilisant la conception générative et la fabrication additive, General Motors a pu consolider les huit différents composants d’un support de siège en une seule pièce imprimée en 3D (crédits photo : GM)
Le développement des matériaux pour la fabrication additive automobile
Au fil des annnées, les améliorations apportées à la technologie ont permis de qualifier davantage de matériaux pour le processus de fabrication additive. Les pièces automobiles sont généralement fabriquées à partir de polymères haute performance, de thermoplastiques renforcés de fibres de carbone et de métaux. Les équipementiers ont activement cherché à incorporer des matériaux plus légers tels que la fibre de carbone et l’aluminium dans la carrosserie du véhicule. Par conséquent, les matériaux adaptés à la fabrication additive automobile peuvent permettre d’intégrer un plus grand nombre de propriétés dans les produits finaux, mais sont également essentiels dans le développement de prototypes fonctionnels.
Par exemple, BASF Forward AM travaille aux côtés de ses clients et des fabricants de machines pour développer des produits innovants. Forward AM a ainsi travaillé avec Daimler pour concevoir un nouveau support moteur permettant de réduire la transmission des vibrations afin de maximiser le confort des passagers. Au cours de la dernière décennie, les supports moteur ont été principalement fabriqués en polymères renforcés en fibres et moulés par injection. Cependant, la nécessité de raccourcir les cycles de développement et de réduire les coûts a mis sous pression ce processus de conception et ces matériaux traditionnels. BASF Forward AM a éliminé la nécessité très coûteuse de nouveaux moules à chaque modification de la conception en s’appuyant sur les technologies 3D. Le défi était le suivant : répondre aux exigences strictes de performances thermiques et mécaniques dans des conditions d’essai. Ils avaient besoin d’un matériau très rigide et thermiquement stable. La solution idéale était l’Ultrasint PA6 MF (un polyamide 6 chargé de minéraux qui surpasse le PA11 et le PA12), qui a permis de produire des prototypes prêts à être testés en moins de 48 heures (au lieu de plusieurs semaines avec le moulage par injection). Bien que la conception de la pièce imprimée en 3D ait été différente, elle a pu être utilisée comme l’original comme un prototype pleinement fonctionnel au stade du développement, lorsqu’aucune pièce moulée par injection n’était disponible. Il était donc essentiel de trouver le bon matériau de remplacement pour reproduire les performances de la pièce moulée par injection.
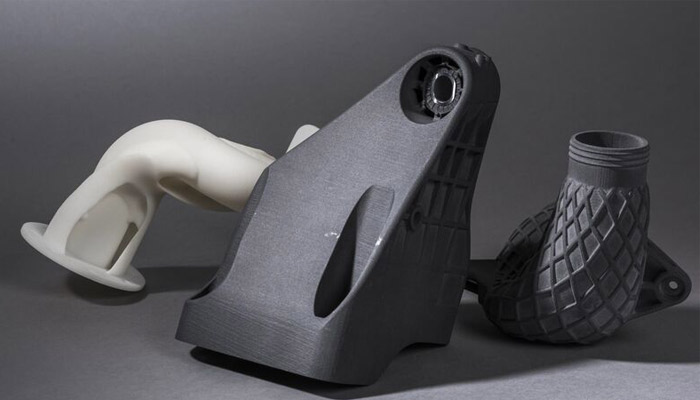
Crédits photo : BASF pour Daimler
Quel est l’avenir des applications de la fabrication additive automobile ?
Ces dernières années, les constructeurs automobiles ont dû explorer de nouveaux modèles commerciaux pour assurer leur croissance. Dans le rapport de Jabil sur les tendances de l’industrie automobile, vous pouvez lire que 71 % des entreprises automobiles ont un délai de mise sur le marché inférieur à 2 ans. Beaucoup se tournent vers les nouvelles technologies, y compris la fabrication additive, pour maintenir des cycles de développement courts et pour obtenir des coûts plus bas. L’électrification des véhicules est également intéressante, environ 50 % des constructeurs automobiles ayant pour objectif de devenir les leaders du marché des véhicules entièrement électriques (VE) dans un avenir proche. Alors que l’industrie s’éloigne des moteurs à combustion interne, l’impression 3D s’impose comme une solution susceptible d’accélérer le développement de pièces plus légères pour les véhicules électriques. En effet, l’allègement est essentiel pour les véhicules électriques car il a un impact direct sur la durée de vie des batteries.
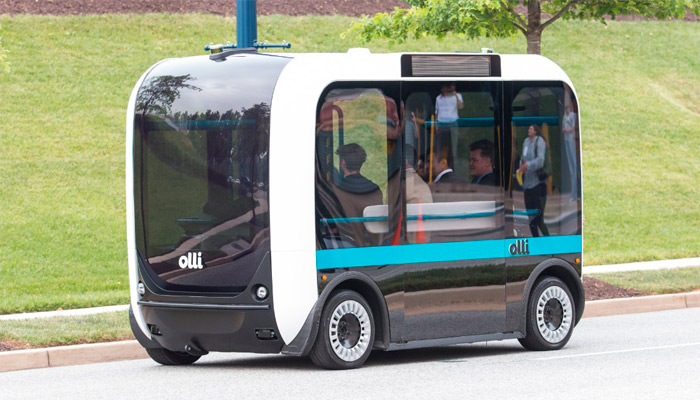
The 3D printed minibus Olli
Dans le secteur des véhicules électriques justement, vous avez peut-être entendu parler d’Olli, un minibus électrique autonome imprimé en 3D et conçu par Local Motors en 2016. Le fabricant affirme qu’environ 80 % des pièces ont été imprimées en 3D, ce qui a réduit le temps de production global de 90 %. La vitesse est limitée à 40km/h, ce qui rend Olli adapté aux centres urbains, aux campus universitaires et aux hôpitaux. Avant cela, Local Motors avait présenté le roadster Strati, un biplace électrique dont 75% des pièces étaient imprimées en 3D.
De plus, comme les véhicules connectés sont de plus en plus demandés, le besoin d’appareils électroniques, comme les capteurs et les antennes à l’intérieur du véhicule, augmente également. Cette hausse s’accompagne d’un besoin accru de concevoir et de produire des appareils électroniques plus petits et plus complexes. Grâce aux technologies d’impression 3D à micro et nano-échelle, il est possible de concevoir en interne des composants électroniques plus complexes qui peuvent être directement intégrés au véhicule. L’impression 3D électronique peut réduire les coûts et le temps de développement pour la création de ces dispositifs.
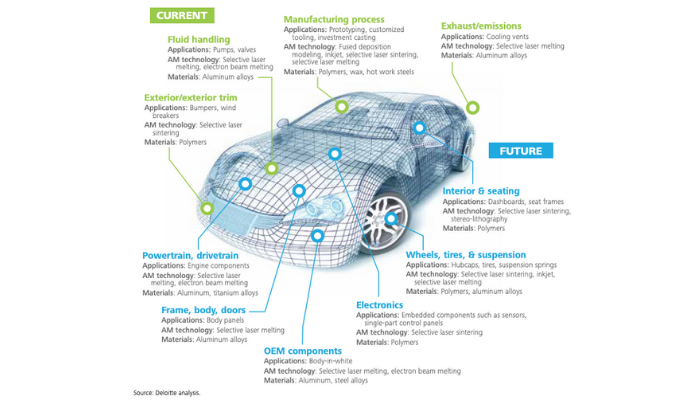
Applications actuelles et futures tirées de l’étude de Deloitte (crédits photo : Deloitte)
Plus globalement, presque tous les acteurs du marché investissent dans les technologies d’impression 3D pour passer à la production de pièces plus complexes et plus performantes. Kevin Quinn, directeur de la conception et de la fabrication additive chez General Motors, explique : « En moyenne, il y a 30 000 pièces dans chaque véhicule. Nous ne cherchons pas à imprimer la totalité des 30 000 pièces. Au lieu de cela, nous sommes très réalistes. Nous nous concentrons sur les opportunités de production qui peuvent apporter une valeur commerciale à GM et au client« .
Par conséquent, au-delà de l’amélioration des capacités globales de fabrication et de la réduction des coûts, qui a été la principale application dans le secteur, les OEM commencent à tirer parti de la fabrication additive pour créer de nouveaux produits et permettre la transformation de la chaîne d’approvisionnement.
*Crédits photo de couverture : BMW Group
Que pensez-vous de la fabrication additive automobile ? Partagez votre avis dans les commentaires de l’article ou avec les membres du forum 3Dnatives. Retrouvez toutes nos vidéos sur notre chaîne YouTube ou suivez-nous sur Facebook ou Twitter !