Le procédé DLP pour créer de meilleures pièces en caoutchouc
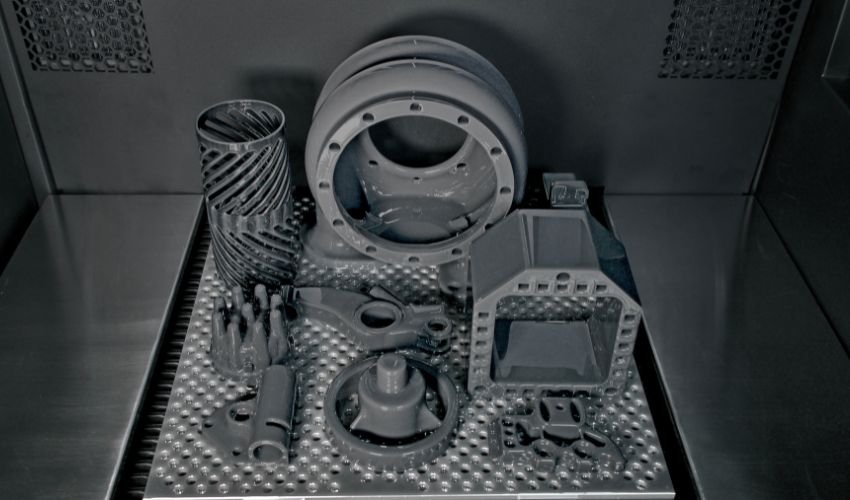
Digital Light Processing (DLP) est l’une des principales technologies d’impression 3D disponibles aujourd’hui. Il s’agit d’un procédé de photopolymérisation, qui consiste essentiellement à utiliser un vidéo-projecteur pour polymériser des résines photosensibles. Cette technologie est populaire à la fois pour sa vitesse et sa précision et peut être utilisée dans un grand nombre d’industries. Et elle ne cesse de s’améliorer.
La première société à commercialiser la technologie, EnvisionTEC, a beaucoup évolué au fil des ans. Et depuis son acquisition l’année dernière par Desktop Metal, qui a scindé la société en deux Desktop Health et ETEC, elle a présenté ses innovations les plus passionnantes dans le domaine, notamment le DLP « top-down », le développement de nouveaux matériaux tels que le caoutchouc, etc. Mais comment fonctionne le DLP ? Quelles sont exactement les innovations apportées par ETEC dans ce secteur ? Et surtout, quelles sont les applications de cette technologie ?
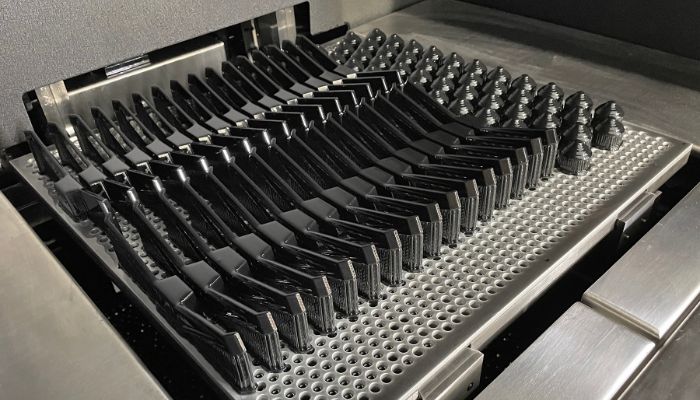
Le plateau de l’imprimante 3D DLP Extreme 8K d’ETEC (crédits photo : ETEC)
Comment ça marche ?
La photopolymérisation, ou le durcissement de résines photosensibles via une lumière UV, peut être considérée comme le parent de la fabrication additive. Comme vous le savez peut-être, la toute première technologie d’impression 3D a été la stéréolithographie, inventée dans les années 80. Cependant, peu de temps après, de nouvelles technologies ont commencé à apparaître pour résoudre les problèmes inhérents à la SLA. Il s’agit notamment du DLP qui a vu le jour en 1999.
Grâce à l’utilisation d’une puce DLP, le digital light processing a permis d’exploiter la lumière d’un projecteur pour polymériser des résines photosensibles dans le cadre d’une impression 3D à grande échelle. La technologie est plus rapide que la SLA, car elle permet d’exposer tout le plateau d’impression à la lumière UV au lieu d’un seul point de polymérisation comme avec un laser, tout en permettant une finition de surface de haute qualité et des bords définis. Cela en a fait une référence parmi les méthodes de polymérisation en cuve.
Une machine DLP traditionnelle fonctionne de bas en haut, avec un projecteur situé sous la cuve. C’est ce procédé qui a été utilisé avec la toute première imprimante DLP commerciale, la Perfactory d’EnvisionTEC. Grâce à son emplacement sur la face inférieure, la lumière du projecteur peut être transmise à travers le fond du plateau dans la résine, ce qui permet de contrôler rapidement et étroitement la hauteur de la couche. Le plateau est conçu avec un fond transparent permettant la transmission de la lumière et ensuite, comme pour les autres technologies résine, le plateau d’impression se déplace de haut en bas sur l’axe z dans la cuve de résine, créant une fine couche qui peut être durcie.
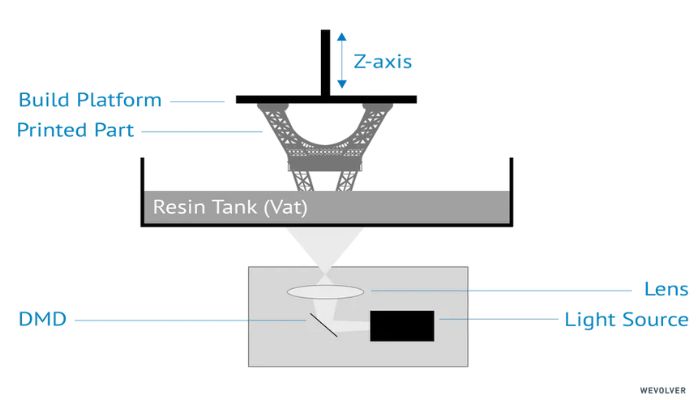
Le procédé DLP traditionnel, initialement commercialisé par EnvisionTEC (crédits photo : Wevolver)
Depuis cette première imprimante, de nombreuses avancées ont été réalisées dans le domaine. En 2015, le procédé CLIP, qui comprenait une couche d’oxygène délivrée par un film perméable à l’oxygène, a éliminé la nécessité de séparer chaque couche durcie, augmentant ainsi considérablement la vitesse. L’application de cette « zone morte » a été lancée par EnvisionTEC en 2016 dans un nouveau procédé appelé CDLM, ou continuous digital light manufacturing.
En 2021, après l’acquisition d’EnvisionTEC par Desktop Metal, une autre nouvelle technologie a été lancée, Hyperprint, qui élimine le besoin de couches d’oxygène. Selon Desktop Metal, Hyperprint utilise la chaleur pour diminuer la viscosité des résines et accélérer l’impression. Elle inclut également l’impression en boucle fermée, avec des capteurs CLP, pour détecter le moment où la couche de la pièce a été entièrement séparée du film de la cuve de résine.
La dernière avancée de la société a été réalisée dans le domaine du DLP « top-down ». Bien que le DLP ascendant ait été la norme au cours des 20 dernières années, ETEC a lancé l’imprimante DLP « top-down » Xtreme 8K pour remédier à un certain nombre de limitations. Cette toute nouvelle machine présente un certain nombre d’avantages pour les utilisateurs, notamment un portefeuille de matériaux élargi pour encore plus d’applications, et représente le dernier cri de la technologie DLP.
Quels sont les avantages de l’imprimante DLP Xtreme 8K d’ETEC ?
Les utilisateurs peuvent s’attendre à un certain nombre d’avantages lorsqu’ils utilisent l’imprimante 3D DLP Xtreme 8K d’ETEC, au-delà des avantages généraux de la technologie DLP tels que la vitesse et les géométries complexes. Par exemple, auparavant, en utilisant la DLP « bottom-up », les utilisateurs étaient confrontés à des restrictions sur le nombre de pièces pouvant être imprimées, car il y avait une limite sur le poids pouvant être soutenu verticalement à partir du plateau d’impression et un besoin d’une grande quantité de supports pour assurer l’adhésion. En outre, les types de résines utilisables étaient soumis à de sérieuses contraintes, car le recouvrement nécessitait des résines à faible viscosité. Cela limitait donc le débit et les propriétés du matériau final.
L’imprimante DLP Xtreme 8K est capable de surmonter ces obstacles, offrant la plus grande zone d’impression DLP (450 x 371 x 399 mm – 166 950 mm2) parmi les imprimantes DLP commerciales de production, grâce à la DLP « top-down ». Elle est capable d’imprimer de grandes pièces ou des volumes élevés avec de nouveaux matériaux qui, selon Desktop Metal, peuvent concurrencer directement les thermodurcissables utilisés dans le moulage par injection de plastique traditionnel.
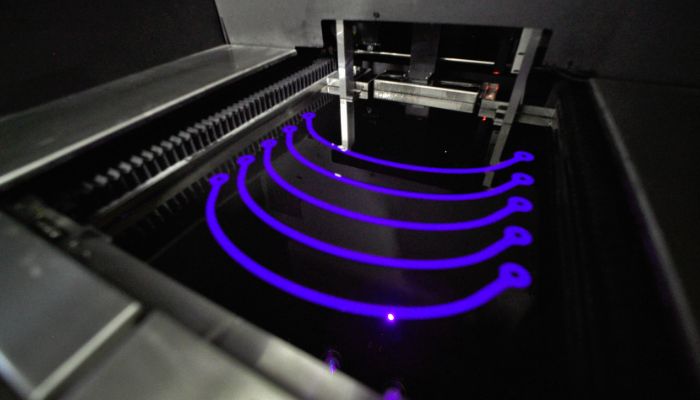
Zoom sur l’imprimante 3D DLP Xtreme 8K (crédits photo : ETEC)
Ces avancées en matière de matériaux ont notamment été rendues possibles grâce aux travaux de recherche et de développement de Deskop Metal par le biais de sa filiale Adaptive 3D. Cette société a réussi à créer une nouvelle famille de matériaux, les photopolymères DuraChain. Il s’agit de photopolymères à un seul composant, ayant subi une synthèse monotope, et qui utilisent la séparation de phase induite par la photopolymérisation, ou Photo PIPS. Les mousses et les matériaux en caoutchouc en sont des exemples. Cette caractéristique, parmi d’autres, a ouvert les imprimantes utilisant la technologie DLP à de nombreuses nouvelles applications dans une variété d’industries.
Le DLP est utilisé pour révolutionner les pièces en caoutchouc
L’une des applications les plus intéressantes du DLP top-down d’ETEC concerne la fabrication de pièces en caoutchouc. Aerosport Additive, un bureau de service basé dans l’Ohio qui produit des prototypes et des modèles de travail pour des clients dans des secteurs tels que l’automobile, l’aérospatiale, l’électronique et bien d’autres, a découvert que la technologie DLP d’ETEC et l’imprimante DLP Xtreme 8K étaient la clé de la création de meilleures pièces en caoutchouc.
Avant d’adopter la technologie DLP, Aerosport Additive devait recourir au moulage d’uréthane pour le prototypage et la production en petites quantités, et au moulage par injection pour la production de masse de pièces en caoutchouc. En effet, la création de pièces en caoutchouc a toujours été un défi pour la fabrication additive, car il était presque impossible de créer des matériaux ayant l’aspect, le toucher et les performances du vrai caoutchouc. Aujourd’hui, ce n’est plus le cas.
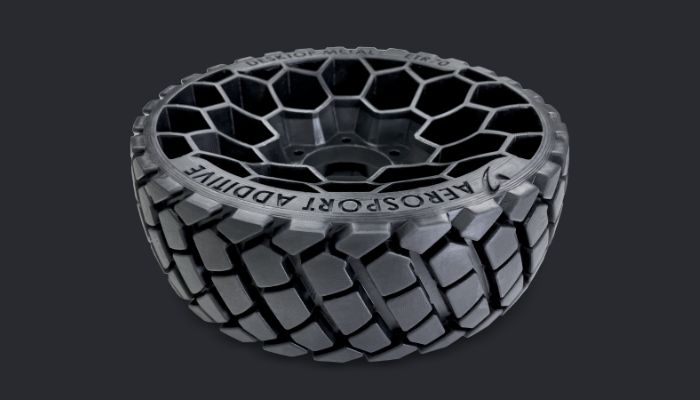
Grâce à l’imprimante 3D DLP top-down Xtreme 8K et à de nouveaux matériaux, Additive Aerosport est capable de produire des pièces en caoutchouc (crédits photo : ETEC)
En utilisant la Xtreme 8K et le Elastic ToughRubber d’Adaptive3D, l’entreprise a pu produire rapidement et à moindre coût des pièces en caoutchouc d’une dureté Shore A70. Par exemple, elle a créé des commutateurs à quatre positions qui sont fixés aux manches de commande des avions, essentiels pour effectuer des réglages précis des commandes de compensation de l’avion.
Comme vous pouvez l’imaginer, ces pièces sont généralement fabriquées en petites quantités, mais se tourner vers le moulage en uréthane était un processus lent et coûteux. Avec l’ETEC Xtreme 8K, Aerospace Additive peut désormais produire jusqu’à 150 commutateurs en une seule fabrication de 2.5 heures, ce qui permet de gagner du temps et de réduire les coûts. La fabrication additive offre en outre la possibilité de modifier ou d’affiner la conception pour répondre aux besoins de différents clients. Cette application, parmi d’autres, montre comment les processus DLP d’ETEC pourraient continuer à avoir un impact sur encore plus d’industries dans les années à venir. Pour en savoir plus sur ETEC et ses solutions DLP, cliquez ICI.
Que pensez-vous de la technologie d’ETEC ? Partagez votre avis dans les commentaires de l’article. Retrouvez toutes nos vidéos sur notre chaîne YouTube ou suivez-nous sur Facebook ou Twitter !