Un écran OLED flexible imprimé en 3D : vers une nouvelle technologie d’affichage ?
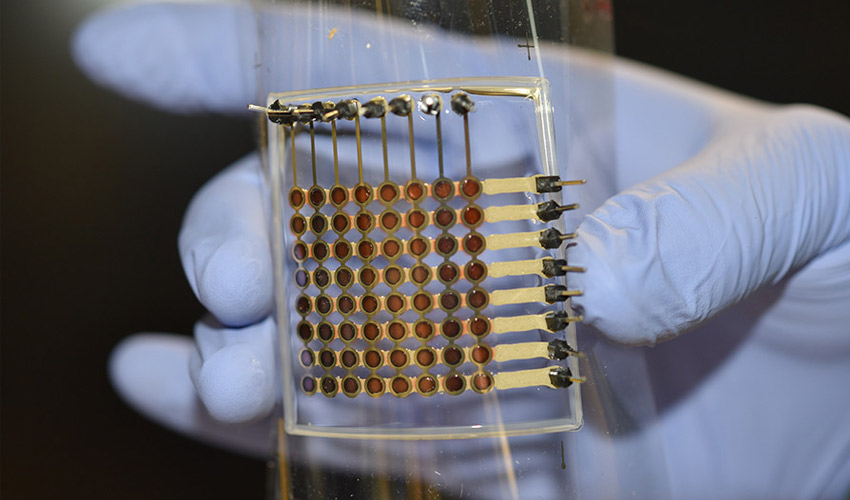
A l’université du Minnesota, une équipe de chercheurs a imprimé en 3D un prototype d’écran qui utilise des diodes électroluminescentes organiques (OLED). Mesurant 3,8 centimètres par 3,8 cm, il intègre 64 pixels fonctionnels, affichant de la lumière. Un développement particulièrement intéressant car c’est un écran flexible qui pourrait être utilisé dans nos futurs écrans pliables des smartphones ou téléviseurs, le tout à un coût plus abordable. Deux méthodes de fabrication additive ont été employées, le tout sur une machine sur-mesure.
Les diodes à électroluminescentes organiques s’appuient sur des matériaux organiques pour émettre de la lumière – à l’inverse des LCD qui utilisent des semi-conducteurs cristallins inorganiques. Les OLED sont donc une alternative aux LCD et présentent plusieurs caractéristiques intéressantes comme une meilleure efficacité énergétique car elles ne nécessitent pas de rétroéclairage ; un rapport de contraste élevé ; une flexibilité mécanique ; un angle de vision plus large ; ou encore une meilleure résistance à la rupture.
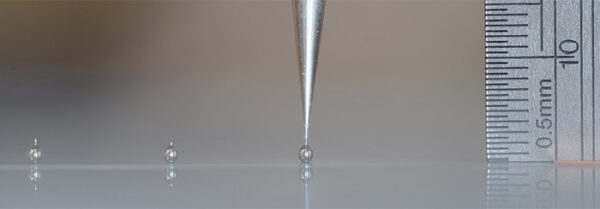
Une méthode d’extrusion et un procédé de pulvérisation ont été utilisés (crédits photo : McAlpine Group, University of Minnesota)
L’impression 3D de ce type de diodes représentait jusqu’ici de nombreux défis. En effet, la technologie d’affichage OLED est basée sur la conversion de l’électricité en lumière à l’aide d’une couche de matériau organique. Or, la création de cette couche est difficile car elle nécessite une parfaite uniformité, plus compliquée à obtenir par fabrication additive. Les liaisons polymère-métal sont aussi plus instables via impression 3D.
Six couches imprimées en 3D pour former l’écran OLED
L’équipe s’est donc appuyée sur deux procédés d’impression 3D pour surmonter ce challenge et ainsi créer les 6 couches de l’écran. A partir d’une machine basée sur l’extrusion, elle a conçu les électrodes, l’isolation, les interconnexions et l’encapsulation. La même imprimante 3D a ensuite été utilisée pour créer les couches actives via un processus de pulvérisation. Plus concrètement, les couches ont été imprimées successivement à partir de matériaux divers selon la fonction de la couche en question. Par exemple, la première a été déposée sur un film souple en PET et est constituée d’encres à nanoparticules d’argent ; la quatrième est une couche de silicone qui permet de couvrir les matériaux conducteurs sous-jacents. Enfin, le dispositif a été encapsulé avec un polymère coulé dans un moule en silicone imprimé par extrusion.
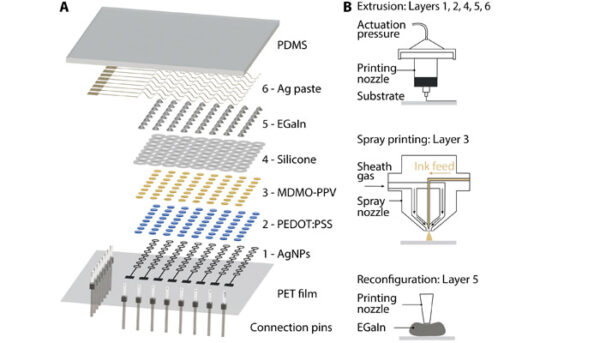
L’écran est composé de 6 couches différentes (crédits photo : McAlpine Group, University of Minnesota)
L’équipe explique : “Nous avons exploité une méthode d’impression par pulvérisation pour déposer le MDMO-PPV, un polymère semiconducteur, afin d’améliorer l’uniformité des couches actives. La buse de pulvérisation a été intégrée à notre système d’impression, l’encre étant atomisée au niveau de l’orifice lorsqu’une vitesse relative élevée est créée entre l’encre quasi statique et le gaz pressurisé. Les gouttelettes atomisées avaient des diamètres de l’ordre de 30 à 50 μm et se sont rapidement évaporées après avoir touché le substrat.” Le résultat est l’obtention d’un prototype flexible de 3,8 centimètres de côté, doté de 64 pixels capables d’afficher de la lumière.
Les chercheurs précisent que la machine employée a été développée sur-mesure et intègre donc différentes buses à changer selon la couche à déposer. Celle-ci sont montées sur un système de portique robotisé. Au total, la machine imaginée aurait un coût se rapprochant de celui d’une Tesla Model S. La méthode d’impression devrait être amenée à évoluer et à se démocratiser si on en croit les dires de Michael McAlpine, professeur titulaire à l’université du Minnesota au département d’ingénierie mécanique : « L’avantage de nos recherches est que la fabrication est entièrement intégrée. Nous ne parlons donc pas d’une vision du futur dans 20 ans. C’est quelque chose que nous avons fabriqué en laboratoire, et il n’est pas difficile d’imaginer que l’on pourrait transposer cela à l’impression de toutes sortes d’écrans chez soi ou en déplacement en quelques années seulement, sur une petite imprimante portable. »
En attendant de voir ce que nous réserve l’avenir en termes de technologies d’affichage, vous pouvez retrouver l’ensemble de l’étude ICI. Que pensez-vous de l’utilisation de la fabrication additive pour produire des écrans OLED ? N’hésitez pas à partager votre avis dans les commentaires de l’article ou avec les membres du forum 3Dnatives. Retrouvez toutes nos vidéos sur notre chaîne YouTube ou suivez-nous sur Facebook ou Twitter !
*Crédits photo de couverture : McAlpine Group, University of Minnesota