D-Shape imprime en 3D des récifs coralliens pour les environnements sous-marins
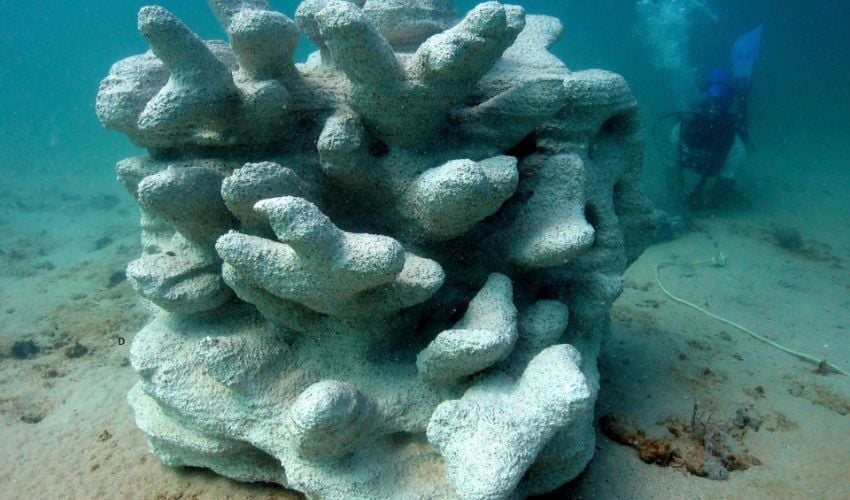
D-Shape est né de l’intuition d’Enrico Dini de Pise, ingénieur, inventeur et PDG de l’entreprise qui vise à proposer et créer des technologies pour des constructions moins chères et plus “belles“. La société est également une marque et un procédé additif qui utilise une imprimante 3D Binder Jetting pour l’architecture. Leur projet le plus important ? Imprimer en 3D un récif artificiel pour sauver la planète ! Ce sont des modules bio-attractifs pour les milieux sous-marins, déjà imprimés pour divers projets à travers le monde, qui sont utilisés pour la protection et la restauration des côtes. Dans notre interview, Enrico Dini nous raconte l’histoire exemplaire de la naissance de D-Shape et leurs projets en cours pour sauvegarder la beauté de la planète.
3DN : Bonjour ! Pouvez-vous vous présenter et nous présenter D-Shape ?
Bonjour ! Je m’appelle Enrico Dini, je suis ingénieur et aussi inventeur. J’ai passé les quinze premières années de ma vie professionnelle dans l’automatisation et la robotique avant de retourner dans mon domaine de formation, l’ingénierie, avec l’idée des maisons en impression 3D. Je viens d’une famille pisane qui a de profondes racines dans les domaines académiques et industriels. Mon ancêtre Ulisse Dini était un mathématicien distingué et recteur de la Scuola Normale Superiore de Pise. Mon père Egisto était chef du département de calculs de Piaggio à Pontedera et bras droit de mon parrain, l’ingénieur Corradino D’Ascanio, célèbre inventeur de l’hélicoptère et de la Vespa. Je leur dois ma capacité à inventer. D-Shape est la marque avec laquelle mes entreprises transmettent la technologie de mon invention connue dans le monde académique sous le nom d’impression 3D à lit de particules. Elle désigne à la fois un procédé de fabrication, une machine, et surtout un projet ayant une mission dans le domaine de l’architecture. Autant D-Shape fabrique des imprimantes 3D, aujourd’hui, elle se concentre entièrement sur la fabrication de modules bio-attractifs et régénératifs pour milieux sous-marins, communément appelés récifs artificiels. Le siège social est à Londres, mais les unités de production sont en Toscane. Nous avons récemment ouvert une spin-off à Hong Kong, D-Shape Limited, qui a l’intention d’étendre la marque en Asie.
3DN : Comment est né D-Shape ? Quel est son objectif principal ?
Le projet est né en 2004. Lors d’une démonstration d’une petite imprimante 3D à poudre aux techniciens de Piaggio, j’ai eu l’idée qu’en mettant à l’échelle le processus de deux ordres de grandeur, il aurait été possible de créer un bâtiment. En 2005, encouragé par Moreno Chiarugi et Roberto Nannini, deux compagnons aventuriers qui avaient défendu l’idée, j’ai déposé un premier brevet. Initialement, il s’appelait « Monolith » à partir de l’idée d’imprimer des maisons « d’une seule pièce ». Après plusieurs tentatives infructueuses pour faire financer le projet en Italie, j’ai finalement décidé de déménager en Angleterre, où j’ai fondé en 2006 « Monolite UK limited », la première entreprise née avec l’intention de promouvoir la construction numérique de manière additive au monde de la construction.
En effet, à l’époque, le Contour Crafting, une méthode de construction additive par extrusion inventée par le Pr Behrokh Khoshnevis aux Etats-Unis, était réservé au domaine de la recherche universitaire. En 2007, j’ai déposé un deuxième brevet qui a résolu certains problèmes liés à la faisabilité effective d’un bâtiment. C’est ainsi que j’ai créé ma première imprimante que j’ai testée en 2008 en créant, avec mon associé et frère Riccardo, The Radiolaria Pavillon : un concept proposé par l’architecte Andrea Morgante du studio londonien Shiro Studio. L’entreprise est apparue dans divers magazines du secteur comme « La première structure au monde imprimée en 3D ». Je peux dire avec fierté que tout ce que vous voyez aujourd’hui dans le domaine des entreprises d’impression 3D à l’échelle architecturale est né de cette première entreprise. Le monde de la construction, extrêmement conservateur par nature, a reconnu que si quelqu’un avait créé une société d’automatisation des bâtiments, il devait y avoir un fonds d’avenir et des perspectives derrière. Lorsque les premiers exemples de nos créations sont devenus viraux sur le web dans le domaine de l’architecture, notre société de communication a proposé un rebranding du projet en proposant D-Shape®. C’est aujourd’hui la marque avec laquelle Monolite UK et les différents concessionnaires et spin-offs promeuvent la technique d’impression 3D de mon invention.
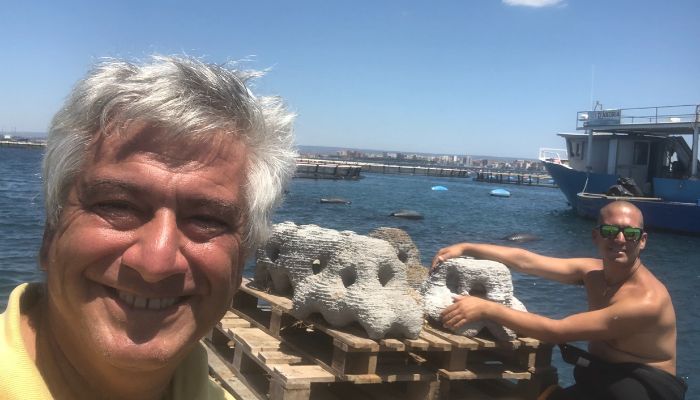
Crédits photo : D-Shape
L’objectif principal de D-Shape est celui d’offrir aux nouvelles générations d’architectes un outil pour matérialiser la beauté à un coût abordable en l’incluant dans le coût de construction d’un bâtiment. À l’époque, je me souviens bien de mon effort pour décrire en une phrase courte cet objectif éthique, qui est notre mission, dans les premières brochures que nous avons diffusées. C’était écrit en anglais, mais en français ça ressemblait plus ou moins à ça : « Vivre dans un endroit agréable augmente notre estime de soi. La beauté ne devrait pas être facultative, mais incluse dans le coût de la construction. D-Shape entend contribuer à façonner un monde meilleur ». Certains de vos collègues l’ont appelé la démocratisation de la beauté.
3DN : Selon vous, quel est le plus grand avantage de la fabrication additive ?
En moi, je me suis toujours senti architecte. Enfant, il y avait dans la maison une carte postale illustrant la Sagrada Familia à Barcelone. Ces formes organiques me fascinaient et ce genre d’architecture était celle que je rêvais de faire un jour. Mais lorsque j’ai suivi le cours d’architecture technique à la faculté d’ingénierie des décennies plus tard, j’ai réalisé qu’il y avait très peu de place pour ces idées bizarres. Des moules et des coffrages droits et plats, sans fioritures, sinon les coûts grimpent en flèche. Fin de l’histoire. Lorsque les premiers modeleurs de surface, y compris Rhinocéros (années 1990) et les premiers systèmes de « prototypage rapide » (le nom « impression 3D » avait à l’époque) ont commencé à se répandre dans l’industrie du design une décennie plus tard, j’ai commencé à réaliser que dans le domaine de la construction, il y avait un fossé entre les nouvelles possibilités de créer des formes géométriques complexes en CAO et la possibilité réelle de les réaliser.
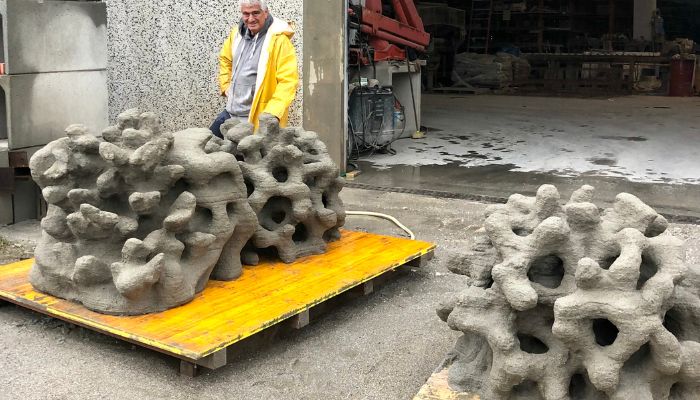
Crédits photo : D-Shape
C’est pourquoi j’ai décidé de développer un système d’impression 3D à l’échelle de l’architecture : parce qu’il permet la fusion de l’ingénierie et de l’architecture. Bien des années plus tard, j’ai réalisé que l’œuvre conçue par Antoni Gaudi était le premier exemple de recherche de forme et d’optimisation topologique. Une fonction statique et un conglomérat de béton optimisés dans une forme que seule l’impression 3D peut réaliser physiquement à un coût abordable.
3DN : Comment utilisez-vous l’impression 3D pour produire des récifs coralliens artificiels ? Avec quels matériaux sont-ils fabriqués ?
Pour être réellement efficaces, en termes de pouvoir bio-attractif, les récifs coralliens artificiels doivent se caractériser par un rapport élevé entre surface et volume. Ils doivent être pleins de cavités pour accueillir différentes espèces de poissons et doivent être très rugueux pour permettre aux coraux, aux gorgones et à une grande variété de biomasses de s’enraciner en surface. Nous générons ces formes principalement à l’aide d’applications de géométrie générative telles que Grashopper. Nous collaborons avec de brillants architectes numériques, dont certains ont donné naissance à des cabinets d’architectes spécialisés dans la conception de récifs artificiels. Pour n’en citer que quelques-uns : parmi les Australiens, James Gardiner, David Lennon, Alex Goad ; en Espagne, Under Water Gardens; en Italie, Rossella Siani qui conçoit pour nous des formes vraiment merveilleuses. Nous avons été les premiers à les fabriquer avec la technologie D-Shape, mais notre exemple a été repris par de nombreuses entreprises à travers le monde.
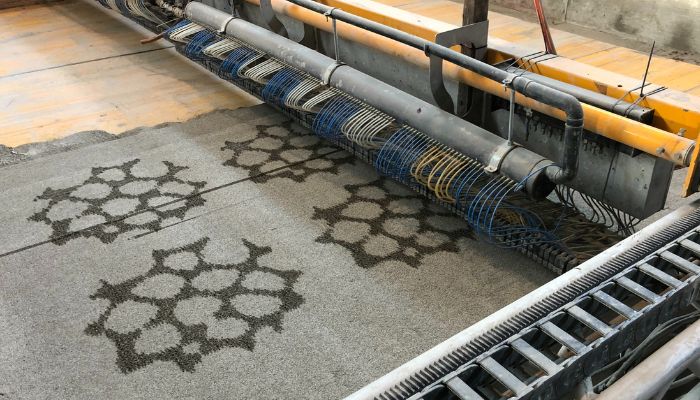
Crédits photo : D-Shape
Les matériaux que nous utilisons sont des granulats de carrière et des liants cimentaires pouzzolaniques ou magnésiens. Au départ, mon idée était d’utiliser des coquillages issus de procédés aquacoles. Nous avons expérimenté avec succès et j’espère que bientôt nous produirons également des récifs artificiels en utilisant ce matériau recyclé, ce qui serait parfait en termes d’économie circulaire, de bio-compatibilité et de durabilité.
3DN : Quels sont les projets sur lesquels D-Shape travaille actuellement ?
D-Shape est actuellement impliqué dans le projet Ocean Citizens, un projet Horizon2020 financé par l’Union européenne dans lequel notre rôle est de produire environ 400 modules qui seront expédiés à Tenerife, Terragone, la Norvège et le Danemark. Nous avons également expédié 20 récifs en Albanie dans le cadre d’un projet de coopération internationale. Nous sommes également impliqués dans des projets financés avec des fonds du PNRR (Plan national de relance et de résilience) et d’autres avec des interventions dans les Marches, les Pouilles, la Sardaigne et la Toscane. Aux Pays-Bas et au Danemark, nous coopérons avec le WWF local. Enfin, à Hong Kong, nous sommes impliqués dans des projets de régénération de la baie de la région.
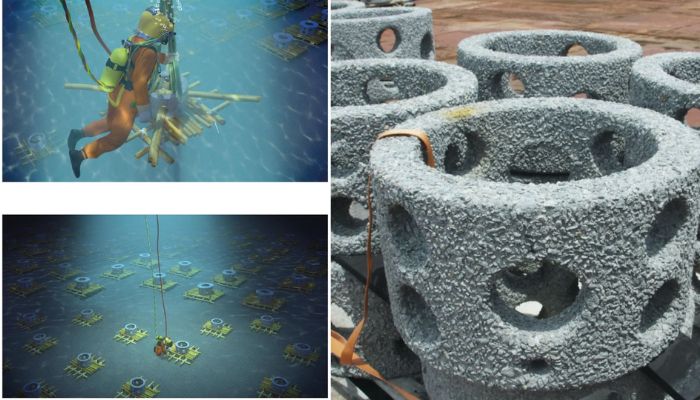
Opérations sous-marines pour l’installation de récifs dans la baie de Hong Kong. (Crédits photo : DFA Design for Asia Awards)
3DN : Quels sont les plus grands défis auxquels vous faites face dans votre entreprise ?
Le défi quotidien est de maintenir l’approche holistique qui a caractérisé le projet D-Shape au cours des vingt dernières années. Il s’agit de développer et de perfectionner les matériaux et les formes, mais aussi d’optimiser nos moyens de production pour rendre les coûts de production accessibles et les délais de livraison raisonnables. De plus, l’objectif est essayer d’industrialiser les procédés, tout en conservant la vocation artisanale et artistique de nos produits. Nous devons continuellement apprendre des interactions avec les biologistes marins, les experts en matériaux, les architectes et les concepteurs sur comment intégrer tous les besoins pour fabriquer des produits fonctionnels. Tout cela, sans jamais perdre de vue notre rêve de beauté qui anime nos initiatives. En bref, continuer à produire un effort de synthèse entre technologie, éco-durabilité et créativité.
3DN : Un dernier mot pour nos lecteurs ?
Nous voulons continuer à faire de bonnes choses dans la restauration côtière pour aider à sauver la planète. L’idée reste d’imprimer de belles maisons en 3D, des fondations au faîtage du toit, en passant par les combles, les escaliers, les bas-reliefs et les motifs biomimétiques. Cela va arriver? Peut être ! Nous attendons qu’un constructeur éclairé jette son cœur par-dessus l’obstacle et nous soutienne dans l’effort de construire une imprimante D-Shape 12x12x12 adaptée à nos besoins ! Notre devise : « Imprimez grand, pensez plus grand ! »
Pour plus d’informations, le site D-Shape : ICI.
Que pensez-vous de notre interview avec D-Shape ? Partagez votre avis dans les commentaires de l’article. Retrouvez toutes nos vidéos sur notre chaîne YouTube ou suivez-nous sur Facebook ou Twitter !
Crédits photo de couverture : D-Shape