Conseils d’experts : pourquoi miser sur le liage de poudre ?
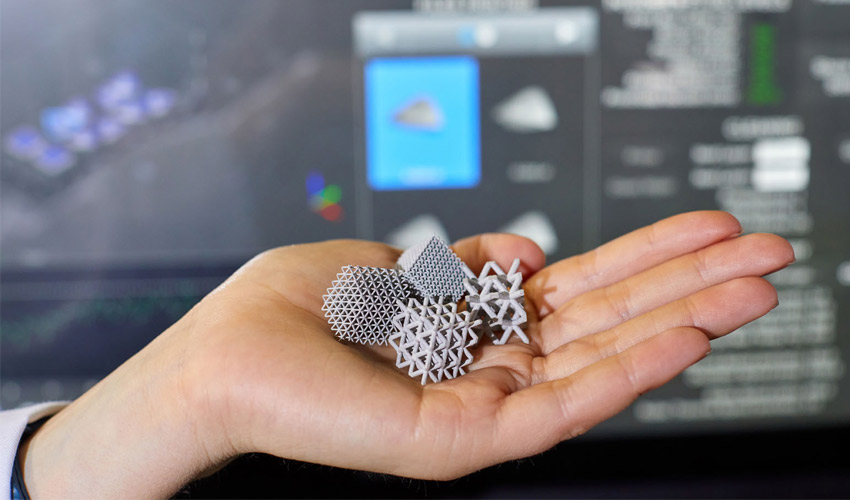
Le liage de poudre, plus communément connu sous le nom anglais Binder Jetting, fait partie des procédés de fabrication additive actuellement disponibles sur le marché. Son fonctionnement est bien évidemment similaire aux autres méthodes d’impression 3D mais il se base sur l’utilisation d’un liant liquide qui se présente sous la forme de micro gouttelettes et de particules de poudre. Ces dernières peuvent être du métal, du sable, de la céramique ou encore des composites. Couche par couche, la pièce souhaitée est fabriquée et, selon le liant et la poudre employés, des étapes de post-traitement seront nécessaires comme le frittage par exemple. C’est un procédé d’impression 3D réputé pour sa flexibilité en termes de matériaux mais aussi de design, et pour sa capacité à produire de larges pièces. Cela en fait une technologie clé pour beaucoup d’industriels. Mais justement, que faut-il prendre en compte lorsqu’une entreprise souhaite intégrer le liage de poudre ? Quels sont les points forts et les challenges du Binder Jetting ? Nos experts ont répondu à quelques questions pour vous éclairer !
Notre premier expert est Andreas Müller, Product Manager chez ExOne. Il se concentre principalement sur le développement et l’amélioration des capacités des machines d’impression 3D de sable, ExOne était l’un des principaux fabricants d’imprimantes 3D basées sur le liage de poudre, tout particulièrement des systèmes employant du sable. Notre second expert est Lefteris Havouzis, Directeur Général de Lino3D. L’entreprise grecque accompagne aujourd’hui les entreprises et industriels dans leurs projets de fabrication additive grâce à son expertise dans plusieurs procédés, dont le liage de poudre métallique. Enfin, notre dernier expert est Vincent Poirier, fondateur et président de Novadditive, le premier centre de production sur-mesure de céramiques en impression 3D multi-procédés.
- Andreas Müller
- Lefteris Havouzis
- Vincent Poirier
Comment fonctionne le liage de poudre ?
Comme tout procédé de fabrication additive, le liage de poudre vient réaliser une pièce en superposant des couches de matériau. Cette matière se présente sous la forme d’un lit de poudre dont les grains sont idéalement sphériques, avec un diamètre micrométrique. Pour que les particules de poudre se collent les unes aux autres, un liant est projeté sur le plateau aux endroits souhaités grâce à une tête d’impression. Le processus se répète couche par couche jusqu’à obtenir l’objet final. Andreas Müller de chez ExOne ajoute : « Semblable à l’impression sur des feuilles de papier, le processus est répété couche par couche, à l’aide d’une carte provenant d’un fichier de conception numérique, jusqu’à ce que l’objet soit complet. Après l’impression, on obtient un batch rempli de pièces qu’il faut retirer du plateau. Selon le matériau et le liant utilisés, des étapes supplémentaires de recuit et de post-traitement peuvent être nécessaires. »
Vous l’aurez compris, deux matières sont nécessaires au bon fonctionnement du procédé : le matériau d’impression 3D et le liant. Et ce qui est particulièrement intéressant avec le liage de poudre, c’est justement la diversité matériaux du marché.
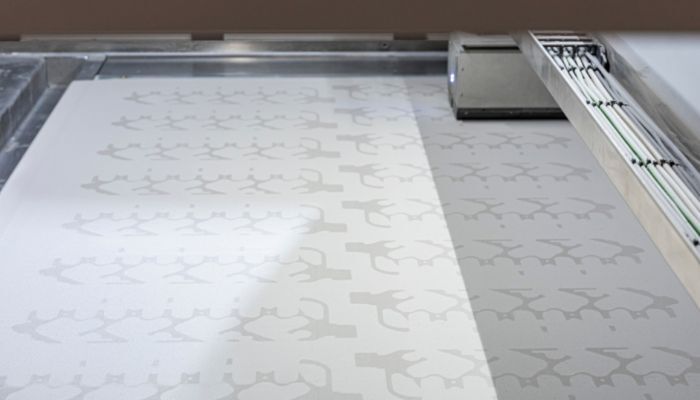
Pendant l’impression, le liant est placé de manière sélective sur le matériau – du sable dans cet exemple (crédits photo : ExOne)
La flexibilité matériaux du procédé Binder Jetting
Le liage de poudre est compatible avec des poudres métalliques, céramiques, du sable et des composites. C’est donc une technologie qui va répondre à plusieurs types d’applications – par exemple, le Sand Binder Jetting est très prisé pour la conception de noyaux de fonderie ou de moules, évitant d’avoir recours à de l’outillage et offrant une plus grande liberté de design. Andreas Müller explique : « L’impression 3D de sable ExOne utilise du sable de qualité fonderie et un liant pour créer des moules et des noyaux de fonderie. Le sable est également imprimé dans d’autres conceptions complexes et infiltré avec de la résine pour former des pièces d’utilisation finale durables. La combinaison du support d’impression et du liant est personnalisée pour chaque application. Nos imprimantes 3D traitent une variété de matériaux de sablage, notamment les sables de silice et de céramique. Différents liants, tels que les liants furaniques, phénoliques et inorganiques, sont disponibles pour couler une variété d’alliages allant de l’aluminium et du magnésium au fer et à l’acier. »
Si on se penche maintenant sur les métaux, la même diversité de matériaux existe. Lefteris Havouzis précise : « En général, tous les alliages peuvent être efficacement frittés (principalement les alliages à base de fer comme l’acier inoxydable, les aciers à outils, les superalliages à base de nickel, les alliages de chrome-cobalt, ainsi que les alliages difficiles à souder comme les alliages réfractaires). Le point le plus important est que le liage de poudre peut travailler avec des alliages difficiles à souder, là où les procédés utilisant un laser échouent. »
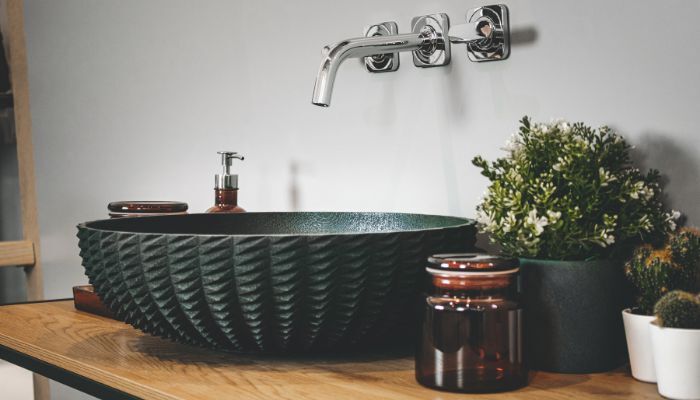
Bien qu’elle soit souvent utilisée pour des processus indirects, le liage de poudre sable peut également permettre de créer des pièces durables à usage final (crédits photo : ExOne)
Rappelons qu’en termes de process, une étape de frittage après l’impression sera nécessaire : à la sortie de l’imprimante 3D, la pièce est très fragile et poreuse et devra être traitée thermiquement pour obtenir ses propriétés mécaniques finales. A l’inverse des autres procédés métalliques utilisant de la poudre, le liage de poudre métallique n’a pas besoin de générer des supports d’impression puisque la poudre environnante soutient la pièce.
Enfin, côté céramiques, le liage de poudre est également une des technologies utilisées par les industriels. Vincent Poirier explique : « Théoriquement, toutes les céramiques sont compatibles avec le binder jetting pour peu qu’on ait mis au point un liant adapté et qu’on réussisse à réaliser des poudres à grains sphérique ou qui puissent s’étaler correctement. En pratique, les céramiques développées pour ce procédé doivent avoir un intérêt par rapport aux technologies de fabrication additive concurrentes. » L’application est donc clé quand on opte pour le liage de poudre céramique : il faut avoir un projet très spécifique en tête, autrement, le choix de ce procédé ne se justifie pas. Sachez que l’alumine, la zircone, le carbure de bore ou encore du carbure de silicium infiltré sont des céramiques utilisées en binder jetting.
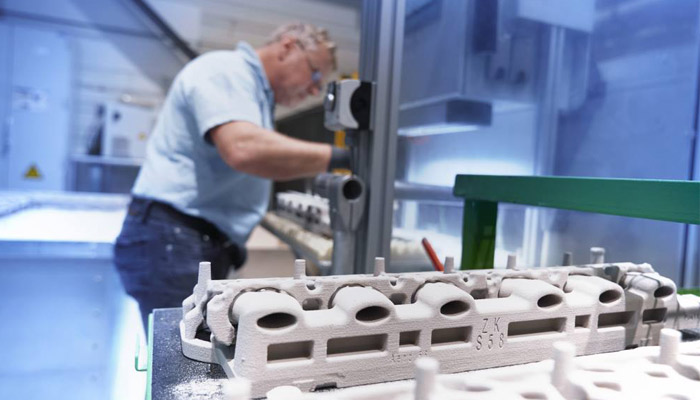
Le liage de poudre sable est très utilisé pour créer moules et noyaux (crédits photo : BMW Group)
Avantages et limites du binder jetting
Vous l’aurez compris, l’un des avantages principaux du liage de poudre est sa compatibilité matériaux. Attention, tout est relatif : la gamme de métaux par exemple est plus limitée que celle utilisée avec des procédés laser. Mais il est intéressant de pouvoir jouer sur la combinaison poudre/liant en fonction de l’application souhaitée.
C’est une technologie qui permet de réaliser de grandes pièces – selon les capacités des machines bien entendu. En effet, le binder jetting vient réaliser son étape de collage des poudres à une température ambiante ce qui éliminent les risques de distorsions thermiques – on n’a pas de phénomène de warping par exemple. L’utilisateur va donc pouvoir imaginer des pièces plus grandes et plus complexes. Lefteris Havouzis de Lino3D ajoute : « Si l’on compare avec d’autres technologies de l’industrie métallurgique, il faut mentionner en général une plus grande liberté de conception, une réduction des délais de fabrication et de mise sur le marché en raison de l’absence d’outils et une plus grande complexité du mélange de production que nous pouvons réaliser. Dans la même impression, on peut imprimer des dizaines de lots différents sans aucun changement. »
Au delà du volume des pièces, on peut aussi évoquer les relatives rapidité et simplicité du procédé. Andreas Müller affirme : « Le liage de poudre est réputé parmi les méthodes de fabrication additive, notamment pour son rendement volumétrique élevé. Parmi les technologies de fabrication additive, c’est aussi celle qui ressemble le plus à l’impression traditionnelle par son approche simple et sa rapidité. Le liant fonctionne comme l’encre lorsqu’il se déplace sur les couches de poudre, ce qui, comme l’impression sur papier, forme le produit final. En revanche, de nombreuses autres formes d’impression 3D fabriquent des pièces à l’aide d’un point unique – souvent un laser ou une buse – qui extrude, fait fondre ou soude le matériau. Ces procédés nécessitent beaucoup plus de matériau et de temps pour dessiner chaque pièce avec un seul point, couche par couche. » Les machines de liage de poudre peuvent déposer de nombreuses gouttelettes de liant en un passage, réduisant le temps de fabrication et augmentant la productivité. Attention toutefois à ne pas se méprendre : les étapes de post-traitement peuvent rallonger le processus.
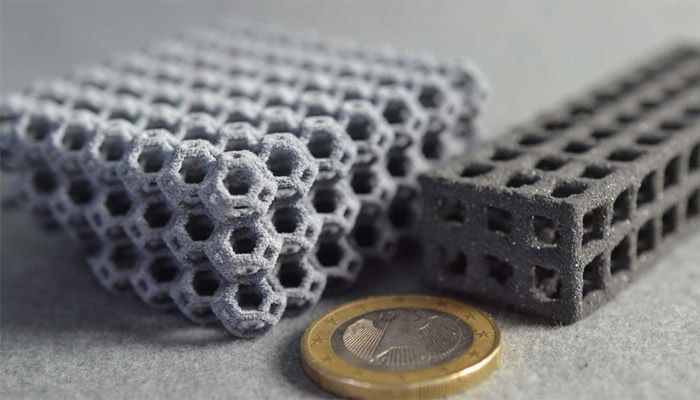
L’utilisation de la céramique nécessite des étapes de post-traitement (crédits photo : WZR)
Le post-traitement fait partie d’une des limites finalement du liage de poudre, particulièrement quand on utilise de la poudre métallique et céramique. Il faut passer par des étapes de déliantage et de frittage qui vont ajouter du temps mais aussi affecter la pièce finale. Lefteris de Lino3D déclare : « Lorsque l’on s’intéresse de plus près à la technologie, il est important de mentionner que la phase critique du Binder Jetting est la phase de frittage où il faut prendre en compte plusieurs phénomènes. Travailler avec un partenaire capable de gérer l’ensemble du flux de valeur peut alors être très intéressant. »
On aura donc tendance à obtenir une pièce plus poreuse, avec des propriétés mécaniques plus faibles. Vincent Poirier conclut : « Plus la poudre aura une capacité à bien se tasser, moins la préforme puis la pièce céramique sera poreuse. Il est donc essentiel de bien choisir sa poudre et opter pour des poudres sphériques. »
Les derniers conseils de nos experts
Lefteris Havouzis affirme : Le mot clé le plus important est l’INTEGRATION : le Binder Jetting, comme toute autre technologie de fabrication, n’est pas une solution isolée, mais pour exploiter son potentiel, il doit être intégré dans l’écosystème de l’entreprise, de la conception au post-traitement.
Andreas Müller ajoute : L’impression 3D de sable est une technologie de production flexible. Elle convient comme méthode de fabrication rapide pour la production d’outils de sablage et peut également être utilisée pour produire des produits finis uniques. L’important est de trouver la bonne combinaison de technologie et de matériau pour répondre à ces besoins. Chez ExOne, nous offrons une assistance complète en matière d’impression 3D de sable, avec un centre de service pour nos clients européens ici même en Allemagne, où nous guidons les clients à travers les différentes options et évaluons la meilleure solution pour résoudre leurs défis de production.
Vincent Poirier conclut : Pour la céramique, il faut avoir une application bien spécifique demandant sans équivoque cette technologie-là. Car à l’instar des autres technologies de fabrication additive céramique, on ne peut pas couvrir tous les cas de figure. De plus, il faut bien intégrer que le savoir-faire n’est pas que dans l’impression. Le savoir-faire céramique est aussi important pour maitriser par exemple cycles de cuisson et conséquences du retrait de frittage sur les produits finis.
Et vous utilisez-vous le Binder Jetting ? N’hésitez pas à partager votre avis dans les commentaires de l’article. Retrouvez toutes nos vidéos sur notre chaîne YouTube ou suivez-nous sur Facebook ou Twitter !
*Crédits photo de couverture : Tecnalia