Comment les céramiques de Lithoz transforment-elles l’aérospatiale ?
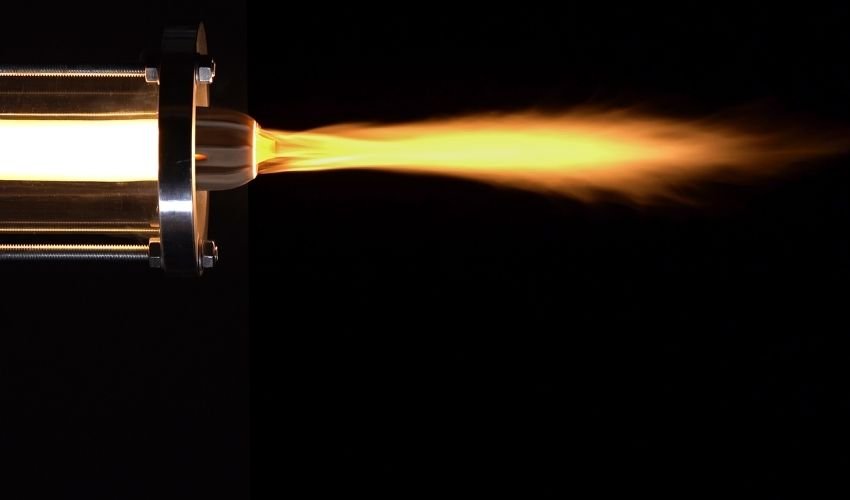
Certains statisticiens évaluent le marché de la fabrication additive céramique à 4,8 milliards de dollars dans le monde en 2030. L’industrie aérospatiale est sans doute l’un des secteurs qui génère le plus de revenus. L’un des acteurs les plus notables de ce marché est la société Lithoz, basée à Vienne, qui s’est concentrée en autres sur l’impression 3D céramique pour le secteur aérospatial. Lithoz a réussi à développer un système de fabrication basé sur la fabrication de céramique par lithographie (LCM). Mais quelles sont les possibilités et les domaines d’application spécifiques de l’impression 3D céramique et des matériaux développés pour elle dans ce cas ? Et comment répondent-ils aux exigences de l’aérospatiale aujourd’hui ?
Des vaisseaux spatiaux décollent avec des pièces en céramique imprimées en 3D
Plus rapide, plus facile et plus rentable, tel est l’objectif suivi par de nombreuses entreprises de l’aérospatiale. Les attentes et exigences sont très élevées en matière de fabrication, et cela s’applique aussi à l’impression 3D. Les plus grands défis pour les composants du marché sont non seulement les charges extrêmes, mais aussi le réchauffement et la surchauffe. Si on prend le cas des aubes de turbine par exemple, elles se déplacent à une vitesse telle que la chaleur qu’elles génèrent est supérieure à celle du métal utilisé pour les fabriquer. Les différents composants doivent non seulement être capables de résister sans problème à une chaleur excessive, mais aussi à un froid glacial. Si l’on considère que la température extérieure dans l’espace peut rapidement descendre à plus de – 200 °C, on comprend vite que le secteur aérospatial a besoin d’une alternative d’avenir pour le processus de fabrication.
Ces différentes conditions extrêmes ne doivent avoir aucune influence sur les performances des pièces, car la stabilité et la porosité continues sont essentielles dans les voyages spatiaux. La taille des catalyseurs, par exemple, joue également un rôle majeur en aval : si les pièces sont fabriquées trop grandes, cela peut entraîner une perte de chaleur inutile ; si les pièces sont trop petites, cela peut empêcher une décomposition maximale du propergol. Dans les deux cas, il en résulte une réduction des performances et une augmentation des coûts. Mais comment l’impression 3D céramique peut-elle surmonter ces obstacles ?
Les céramiques sont connues pour leurs propriétés telles que la résistance à la chaleur, leurs performances mécaniques, mais aussi pour leur utilisation dans la production de composants fins de la plus haute qualité. La fabrication additive permet donc de concevoir des formes complexes tout en réduisant les coûts et les délais – ce que ne permet pas la fabrication conventionnelle. On peut rapidement en déduire que l’impression 3D céramique est une solution idéale pour une industrie aussi exigeante que l’aérospatiale. Lithoz s’est rapidement positionné sur ce marché en développant un nitrure de silicium (Si3N4) qui se distingue par ses propriétés optimales, telles qu’une grande solidité même à haute température, une excellente résistance aux changements de température inattendus, et aussi une dureté élevée. Pour prouver ces propriétés et tester le matériau dans des conditions extrêmes, l’entreprise autrichienne a effectué un test de contrainte avec une buse en Si3N4 et les résultats sont excellents.
L’équipe de Lithoz a voulu tester la résistance aux chocs thermiques de son matériau à l’aide d’une buse en nitrure de silicium imprimée en 3D. Ils l’ont donc chauffé à 900 °C, puis l’ont immédiatement refroidie à température ambiante en la plongeant dans l’eau. Malgré la charge thermique élevée, la buse imprimée en 3D a résisté au test sans aucun dommage. Selon Lithoz, le matériau résiste même à une température supérieure à 900 °C.
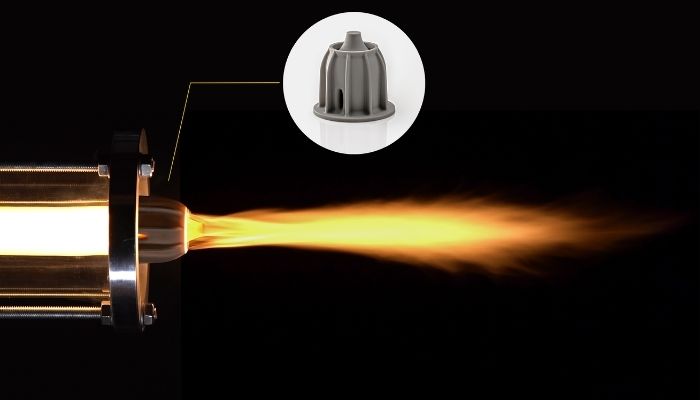
La buse fabriquée par Lithoz résiste aux températures les plus élevées (crédits photo : Lithoz GmbH)
Qu’est-ce que cela signifie concrètement pour l’aérospatiale ? Grâce à la fabrication additive et à l’utilisation de nitrure de silicium, les pièces imprimées en 3D présentent une résistance élevée aux chocs thermiques, ainsi qu’une solidité et une ténacité énormes, et l’avantage de pouvoir fabriquer des formes complexes. Par exemple, dans le domaine de l’aérospatiale, des microturbines, des roues et des outils de coupe peuvent être conçus rapidement et avec précision et utilisés à des températures allant jusqu’à 1200 °C, ce qui prendrait beaucoup de temps et coûterait cher dans un processus de production traditionnel. Le Si3N4 est également largement utilisé dans d’autres industries : le secteur médical profite particulièrement de ce matériau grâce à sa chimie de surface antibactérienne et antivirale, ainsi qu’à son excellente biocompatibilité. Concrètement, le nitrure de silicium convient surtout aux domaines de la médecine dentaire, de l’orthopédie et des implants cranio-maxillo-faciaux. Le nitrure de silicium peut également être utilisé de manière optimale dans la lutte contre le coronavirus, car sa nature de surface le rend résistant aux virus et aux bactéries.
L’impression 3D sur la lune : réalité ou fiction ?
Cela peut sembler sortir tout droit d’un scénario de film de science-fiction, mais l’utilisation de poussière lunaire, également appelée régolithe, est déjà utilisée par Lithoz en impression 3D céramique. Grâce à la technologie LCM, il est possible de fabriquer des pièces à partir de régolithe dans des dimensions très précises. Pour les futures missions dans l’espace, cela signifie que les pièces de rechange et les outils nécessaires pourront être produits sur place et à la demande. Ce matériau est considéré comme une ressource suffisamment disponible et non toxique pour l’homme. L’étroite collaboration avec l’Agence spatiale européenne (ESA) permet une recherche et un développement continus de cette poussière lunaire en vue. Dans le cadre du projet européen Horizon 2020 RHEFORM, des recherches ont déjà été menées sur une solution pour remplacer l’hydrazine. Cette substance, considérée comme cancérigène, joue un rôle important dans le domaine spatial depuis les années 1960. Grâce à l’utilisation de l’imprimante 3D CeraFab 7500, un système de fabrication additive basé sur la technologie DLP (Digital Light Processing) développé par Lithoz et de son propre liant photodurcissable, les chercheurs ont pu réaliser des progrès significatifs en matière d’applications dans le domaine spatial. Afin d’explorer les autres possibilités du matériau Moondust, plusieurs projets sont en cours.
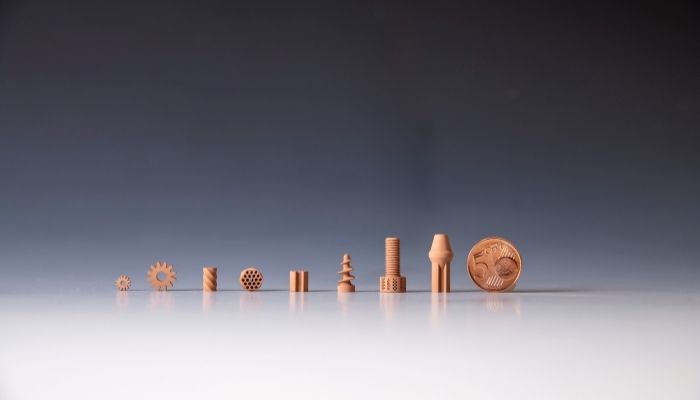
Les pièces imprimées en 3D à partir de régolithe peuvent prendre différentes tailles et formes (crédits photo : Lithoz GmbH)
Produire plus facilement des turbines d’avion grâce à Lithoz
Pour permettre aux avions de décoller, les turbines sont essentielles à chaque vol. L’une des pièces les plus importantes de la turbine sont les aubes de turbine, qui sont traditionnellement fabriquées par moulage à la cire perdue. Mais cela pose souvent un problème majeur : avec les noyaux moulés par injection, l’intégration d’éléments de refroidissement complexes et étroits à plusieurs pales est limitée. Les conséquences peuvent être non seulement coûteuses à long terme, mais aussi comporter des risques pour la sécurité. Comment fabriquer aujourd’hui des turbines de manière plus efficace et innovante sans que les coûts n’augmentent ? La solution est offerte par le LithaCore 450, un matériau à base de silice qui convient parfaitement à la fabrication de noyaux grâce à une faible dilatation thermique et à une porosité très élevée. En passant par la fabrication additive, plus besoin d’outillage ou de moules, offrant un procédé de production plus rapide. Les noyaux de coulée peuvent avoir une finesse d’au moins 200 µm et une taille allant jusqu’à 30 cm, même pour des formes complexes avec des caractéristiques telles que les bords arrière. Grâce à son système CeraFab, Lithoz a même réussi à produire plusieurs noyaux de fonderie d’une taille de 500 mm, ce qui n’avait jamais été fait auparavant, et montre ainsi des solutions d’avenir pour la fabrication de prototypes jusqu’aux grands noyaux pour les turbines industrielles.
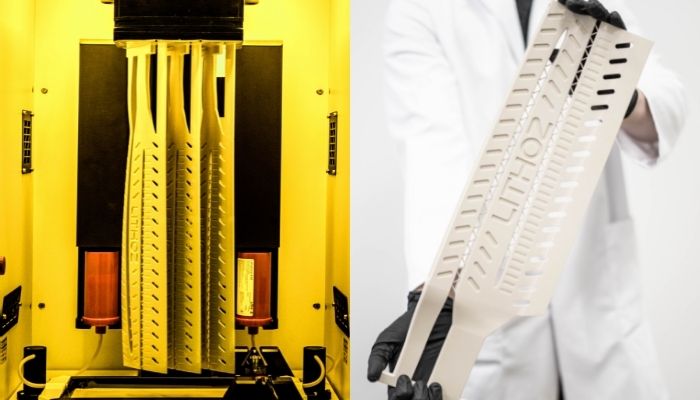
Noyaux en céramique imprimés sur la CeraFab S230 avec le LithaCore 450 pour des turbines à gaz industrielles (crédits photo : Lithoz GmbH)
Les derniers matériaux développés par Lithoz
Alors que les matériaux précédents ont déjà été éprouvés par des années d’utilisation, Lithoz élargit son choix de matériaux céramiques avec deux autres. D’une part, le carbure de silicium infiltré (SiSiC), un matériau céramique à la fois léger et dur qui offre une très bonne conductivité thermique et une dilatation thermique minimale. Les céramiques SiSiC sont donc souvent utilisées pour concevoir des échangeurs de chaleur, buses ou embouts pour différents types de brûleurs. D’autre part, le nitrure d’aluminium (AIN) qui présente une conductivité thermique élevée. Sa résistance à la flexion a pu être mesurée pendant les essais de recherche, variait entre 320 et 498 MPa. L’ensemble de ces propriétés contribue à rendre possible la fabrication de pièces très complexes et sans fissures, ce qui ouvre de nouvelles possibilités d’application dans le domaine de la gestion thermique.
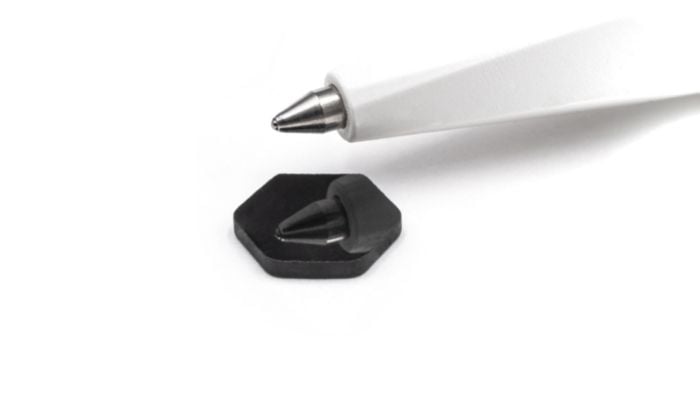
Le carbure de silicium permet d’imaginer toutes sortes de forme et de taille (crédits photo : Lithoz GmbH)
Cette gamme de matériaux illustre bien les progrès réalisés par en impression 3D céramique dans le domaine de l’aérospatiale et les nouvelles possibilités qu’elle ouvre. Outre la fabrication de pièces aux structures complexes, Lithoz permet, avec ses matériaux, une grande liberté de conception, associée à une grande précision. Que la pièce imprimée en 3D soit de quelques millimètres ou d’un demi-mètre, la qualité supérieure des matériaux et la précision constante de l’exposition au pixel près, obtenue de manière uniforme sur tout le plateau d’impression, font que la fabrication de pièces en série n’est enfin plus un problème.
Quels sont les projets actuels de Lithoz dans le domaine de l’aérospatiale ?
En collaboration avec des chercheurs de l’université de Poitiers, de FOTEC Forschungs- und Technologietransfer GmbH (Autriche) et de la Fachhochschule Wiener Neustadt GmbH (Autriche), Lithoz a comparé des catalyseurs céramiques monolithiques imprimés avec des catalyseurs fabriqués de manière traditionnelle ainsi qu’avec différentes couches de washcoat. En ce qui concerne la décomposition du peroxyde d’hydrogène à haute concentration, il a été constaté que le facteur de la porosité joue un rôle crucial. En général, la porosité mesurée de la structure imprimée est plus grande que celle de la structure extrudée, améliorant le comportement thermique instationnaire. Ces résultats peuvent en convaincre plus d’uns à utiliser la fabrication additive céramique dans le secteur aérospatial ! Si vous souhaitez obtenir plus d’informations à ce sujet, n’hésitez pas à vous inscrire à la newsletter de Lithoz ICI.
Que pensez-vous des solutions de Lithoz pour le secteur aérospatial ? N’hésitez pas à nous dire ce que vous pensez dans les commentaires de l’article. Retrouvez toutes nos vidéos sur notre chaîne YouTube ou suivez-nous sur Facebook ou Twitter !
*Crédits photo de couverture : Lithoz GmbH