BASF Forward AM et ses solutions de fabrication additive pour l’automobile
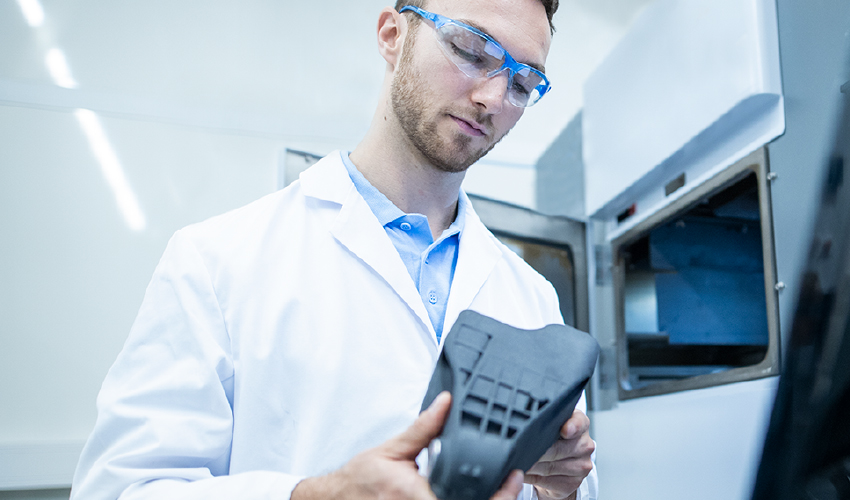
L’industrie automobile est sans aucun doute l’un des secteurs qui a le plus adopté les technologies de fabrication additive, pour le développement de prototypes dans un premier temps, et pour la création de pièces d’utilisation finale plus récemment. Selon l’étude publiée par SmarTech Publishing, ce marché devrait atteindre 5,3 milliards de dollars en termes de recettes en 2023, et 12,4 milliards de dollars en 2028.
Au cours des dix prochaines années, ce segment devrait représenter le plus grand marché de l’industrie mondiale de l’impression 3D, avec la réalisation de ce qu’on appelle l’Additive Automotive. L’un des acteurs qui favorise cette croissance est Forward AM, le spécialiste de la fabrication additive faisant partie de la société allemande BASF. Experte en matériaux, Forward AM s’est également développée sur l’accompagnement des entreprises du secteur automobile qui souhaitent innover via l’impression 3D.
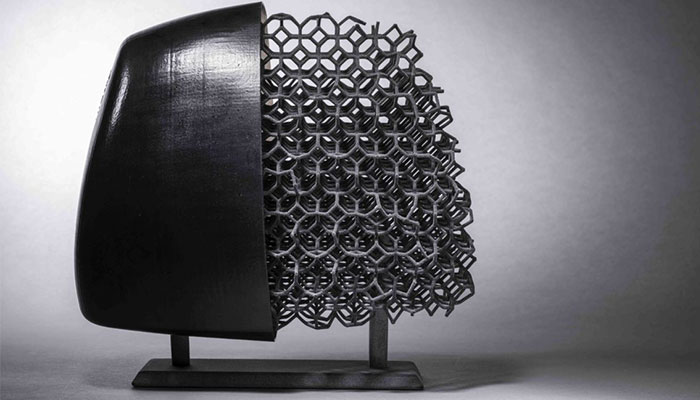
L’évolution des matériaux a encouragé le secteur automobile à adopter la fabrication additive (crédits photo : BASF Forward AM)
Forward AM a été créé dans le but de développer des matériaux de haute performance pour l’impression 3D. Lancée en 2017, cette division possède déjà l’une des plus grandes gammes de matériaux du secteur. Grâce à ses connaissances en matière de matériaux et d’adoption industrielle, elle a également développé des solutions de post-traitement, de conseil et de suivi pour les entreprises de tout secteur industriel souhaitant faire évoluer leurs applications de fabrication additive. La marque Sculpteo de BASF, basée à Paris et San Francisco, fournit également des services d’impression 3D professionnelle en ligne pour la production à la demande de prototypes, de produits uniques et de petites séries.
La fabrication additive dans l’industrie automobile
De nombreux constructeurs automobiles ont déjà commencé à utiliser les technologies de fabrication additive, que ce soit Audi, BMW ou même Ferrari pour ses voitures de Formule 1. Les applications de la fabrication additive dans le secteur automobile sont nombreuses, mais nous pouvons les diviser en trois groupes principaux :
- Le prototypage : c’est encore l’application la plus répandue aujourd’hui, qui permet de développer et de tester rapidement différentes pièces.
- Les pièces d’utilisation finale : elles sont apparues il y a quelques années grâce au développement des matériaux et des machines. Selon le dernier rapport The State of 3D Printing de Sculpteo, 50% des entreprises qui ont utilisé l’impression 3D l’année dernière l’ont fait pour produire des pièces d’utilisation finale.
- Les gabarits et fixations : parfois appelés pièces d’outillage, ils accélèrent la production. Les gabarits sont des outils qui guident l’outil de coupe ou d’usinage dans une chaîne de production et les fixations sont des outils qui maintiennent la pièce avec le banc de la machine précisément à l’endroit souhaité.
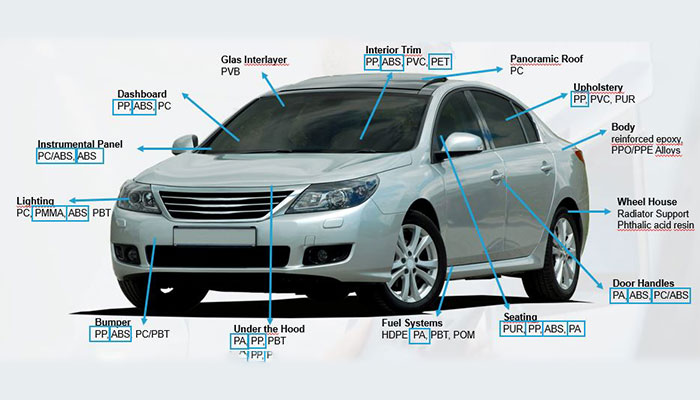
La fabrication additive peut être utilisées pour toutes les pièces d’un véhicule (crédits photo : BASF Forward AM)
L’adoption des technologies d’impression 3D permet d’augmenter la productivité et de réduire les coûts, mais a également ouvert la porte à la personnalisation de masse, permettant aux OEM (Original Equipment Manufacturers) de proposer des pièces uniques, tout en étant en mesure de répondre aux besoins de l’utilisateur final avec des pièces personnalisées pour leurs voitures.
Forward AM et son engagement envers l’industrie automobile
Nous savons donc que Forward AM est un expert en matériaux au sein de l’industrie ; n’oublions pas qu’il a également acquis une expérience égale dans l’industrie automobile grâce à sa collaboration avec différents constructeurs et équipementiers qui collaborent avec ces constructeurs. Pour ces derniers, la société allemande propose des services de simulation, de post-traitement et d’impression 3D. Ils permettent d’adopter la fabrication additive de manière structurée, garantissant une mise en œuvre réussie. D’ailleurs, BASF Forward AM a participé à de nombreux projets dans le secteur automobile ; deux d’entre eux en particulier ont retenu notre attention.
Forward AM et Daimler : développement rapide de supports moteur
La relation entre Daimler et Forward AM remonte à plusieurs années, lorsque la multinationale allemande cherchait à accélérer le processus de développement des supports moteur – des pièces clés du moteur qui offrent stabilité et alignement. Pour permettre le passage du moulage par injection à l’impression 3D, la division allemande a commencé par tester les matériaux. Elle visait également à réduire les coûts en fonction de la durée des cycles de développement. Elle a donc procédé à différents tests, sur la base du matériau le plus performant pour cette pièce : Ultrasint® PA6 MF, un polyamide à stabilité mécanique et thermique, qui peut être utilisé avec les technologies de fusion sur lit de poudre. Avec l’adoption de l’Ultrasint® PA6 MF, des prototypes ont été développés en peu de temps. Cette réduction a été considérable si on la compare aux semaines nécessaires pour réaliser ces mêmes pièces par moulage par injection.
Forward AM et OECHSLER : optimiser le design des selles de moto
OECHSLER, un spécialiste de la transformation des polymères, et Forward AM ont uni leurs forces pour développer des selles de moto de dernière génération. L’objectif principal était de développer un prototype pour améliorer la conception même de la pièce en question. Grâce aux avantages de l’impression 3D, la selle a été développée en un seul composant avec une structure en treillis, réduisant ainsi le temps de fabrication et d’assemblage. Ils ont utilisé l’Ultrasint® TPU01 de Forward AM, idéal pour la production de pièces nécessitant une absorption élevée des chocs à long terme, un retour d’énergie et une grande flexibilité. Ses caractéristiques rendent ce matériau parfait pour le développement en série avec la technologie HP Multi Jet Fusion. Le processus d’assemblage était en effet beaucoup plus simple et plus court, aucun processus de collage n’était nécessaire et le revêtement supérieur n’avait pas besoin d’être fixé avec des agrafes métalliques. De plus, le poids de la selle a été réduit de 25 %, avec moins de matériau utilisé.
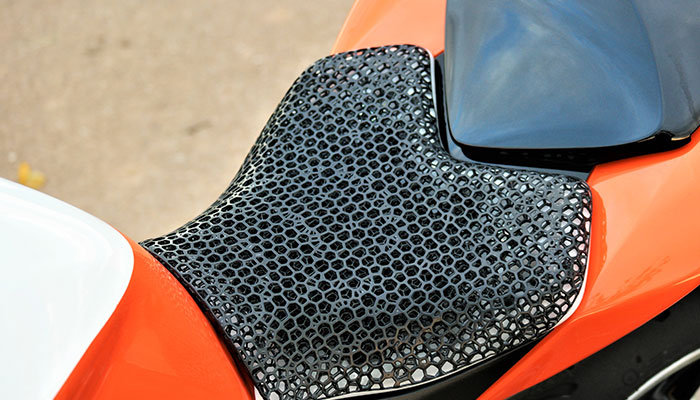
Des selles optimisées grâce à la fabrication additive et à ses matériaux (crédits photo : BASF Forward AM)
Forward AM a participé à différents projets automobiles pour permettre à un nombre croissant d’entreprises de tirer parti des avantages de l’impression 3D en implémentant cette technologie avec succès. Vous pouvez trouver plus d’informations dans un webinaire approfondi sur leurs solutions pour l’automobile ou les contacter ICI.