Audi Sport améliore la production et les outils grâce à l’impression 3D
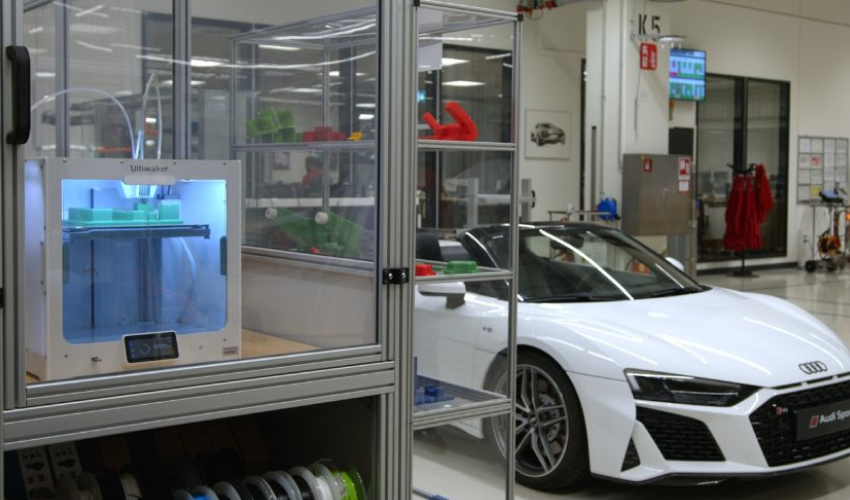
Suivant la tendance émergente de l’utilisation accrue de l’impression 3D dans le secteur automobile, l’usine Böllinger Höfe d’Audi Sport en Allemagne, renommée pour le développement de véhicules haute performance tels que l’Audi R8 et la toute électrique E-Tron GT, a récemment adopté cette technologie pour surmonter un défi de production important.
L’introduction de l’E-Tron GT nécessitait près de 200 outils, gabarits et montages spécialisés, un processus qui demandait traditionnellement beaucoup de temps et de ressources. Cependant, grâce à l’intégration de l’impression 3D et du logiciel Fixturemate de Trinckle, Audi Sport a transformé son flux de travail, réalisant une efficacité et des économies de coûts sans précédent
Au cœur du modèle de production de l’E-Tron GT se trouve un degré intense de personnalisation, chaque véhicule étant adapté aux commandes spécifiques des clients. Cela nécessite un processus de production efficace et adaptable, que l’adoption de l’impression 3D a considérablement amélioré. Le logiciel Fixturemate de Trinckle a rationalisé la conception des montages personnalisés, réduisant le temps nécessaire de plusieurs heures à seulement 10 à 20 minutes par conception. Cet outil convivial permet la création de composants précis et fonctionnels sans l’expertise approfondie typiquement requise pour les logiciels de CAO traditionnels.
Parlant des avantages du logiciel Fixturemate, Cem Guelaylar, Expert en Impression 3D chez Audi Sport, a expliqué : « Nous mettons nos pièces dans Fixturemate et sortons le montage de ce logiciel en quelques minutes. Normalement, en construction classique, nous avons besoin de deux à quatre heures, selon la taille de la pièce. Fixturemate est très facile à utiliser. Nous pouvons amener des stagiaires et leur montrer comment utiliser le logiciel, et ils peuvent directement travailler avec et produire les montages en peu de temps. »
De plus, la flexibilité de l’impression 3D a permis à l’entreprise d’expérimenter une gamme de matériaux adaptés à des applications spécifiques, du TPU95a au PLA sûr pour l’ESD. Cela a facilité la production de composants électroniques, garantissant sécurité et conformité aux normes de l’industrie.
Que pensez-vous de cette adoption accrue de l’impression 3D par Audi ? Partagez votre avis dans les commentaires de l’article. Retrouvez toutes nos vidéos sur notre chaîne YouTube ou suivez-nous sur Facebook ou LinkedIn !
*Tous les crédits photos : UltiMaker