Arris Composites et l’utilisation de la fabrication additive composite pour la production de masse
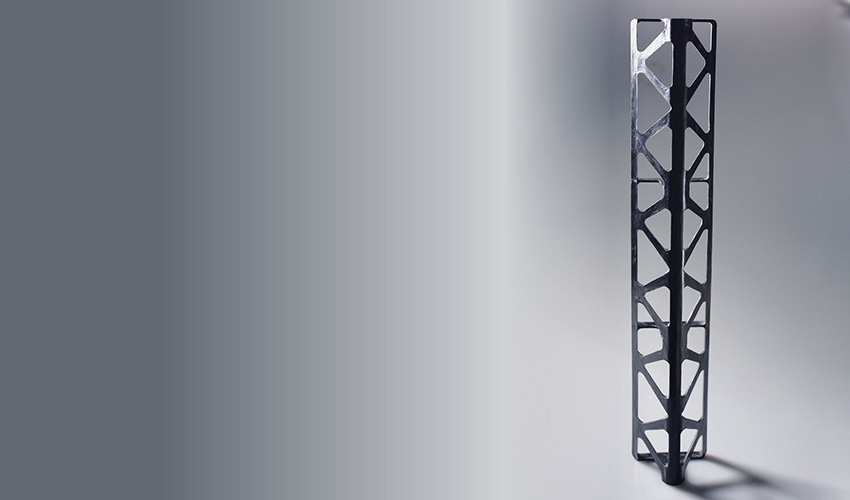
Arris Composites, l’un des pionniers des matériaux composites de nouvelle génération, a annoncé fin mai qu’il avait obtenu un financement de 48,5 millions de dollars dans le cadre de la série B pour étendre ses capacités de fabrication de composites exclusifs et ouvrir de nouvelles installations aux États-Unis et à Taïwan. Fondée en 2017, la startup travaille depuis quelques années déjà au développement de sa technologie Additive Molding. Selon l’entreprise, celle-ci permet la production en masse de pièces composites à haute résistance et à faible poids grâce à la fabrication additive. En appliquant cette technique à la méthode de fabrication conventionnelle des composites, elle est capable de produire des pièces en fibre de carbone à la même vitesse que les produits moulés en plastique. Pour en savoir plus sur la vision de l’entreprise et les applications qu’elle permet, nous avons parlé à son PDG et fondateur, Ethan Escowitz !
3DN : Pouvez-vous vous présenter ainsi que votre lien avec l’impression 3D ?
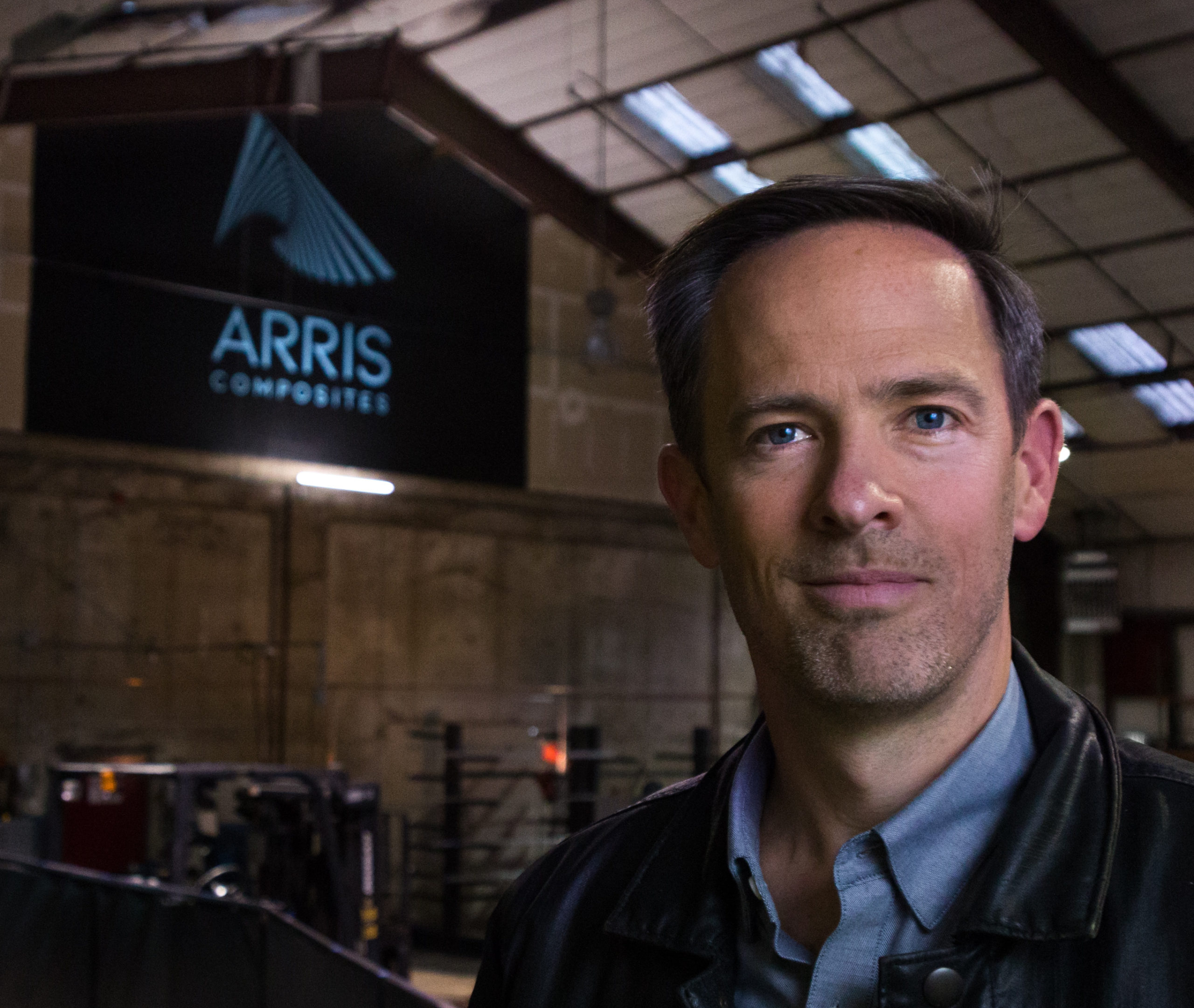
Ethan Escowitz
Je m’appelle Ethan Escowitz et je suis le PDG et fondateur d’Arris Composites. J’ai passé plus de dix ans à travailler dans l’impression 3D et la fabrication additive et, avant cela, je travaillais avec des technologies de fabrication traditionnelles. J’ai fondé Arris en 2017 avec la vision de débloquer la production de masse de composites haute performance en utilisant des techniques de fabrication additive.
La mission d’Arris Composites est de faire progresser l’humanité en créant les produits les plus performants imaginables. Nous travaillons en partenariat avec les entreprises les plus innovantes du monde pour imaginer, concevoir et façonner le futur.
3DN : Pouvez-vous nous en dire plus sur les avantages des composites en fabrication additive ? Peuvent-ils concurrencer les métaux ?
Avant tout, permettez-moi d’énoncer ce qui est évident mais applicable : il existe différents outils pour différents emplois. Pour les applications appropriées, en particulier le prototypage, nous avons, à Arris, utilisé la fabrication additive plastique, composite et métal pour obtenir des pièces fabriquées plus rapidement que nous ne pourrions le faire sur nos machines CNC. Cela dit, il y a de nombreuses applications où nous remplacerons les solutions métalliques conventionnelles et l’impression 3D. Un exemple en est les supports métalliques optimisés topologiquement et imprimés en 3D. Le logiciel d’optimisation topologique a créé ces conceptions idéales, cependant, il n’y a pas eu de technologie de fabrication composite continue qui puisse produire ces structures, donc, en conséquence, le métal imprimé 3D à faible résistance spécifique a été suffisant. La technologie Additive Molding™ permet de fabriquer ces structures à topologie optimisée avec le matériau idéal (composites à fibres continues alignées sur les axes x, y et z) et donc de mieux répondre aux besoins de ces clients du secteur aérospatial. Dans ces applications, nous répondons généralement aux exigences fonctionnelles des clients avec un gain de poids de 50 à 70 %.
De plus, la nature évolutive (en termes de volume) de notre processus de fabrication nous permet d’introduire ces conceptions structurelles innovantes sur de nouveaux marchés, comme l’automobile, où le coût élevé de l’impression 3D métal a empêché la commercialisation de ces formes structurelles optimisées. De plus, la nature évolutive (en termes de taille) de notre processus de fabrication nous permet de produire de grandes structures qui incarnent ces idéaux de conception dans une forme unique qui, autrement, nécessiterait un assemblage. Bien qu’il s’agisse d’une application où nous chevauchons la fabrication additive métal, nous avons de nombreuses autres applications, comme la production d’appareils électroniques grand public et d’équipements de loisirs, où nous excellons mais où l’impression 3D métal n’est pas pertinente.
3DN : Arris Composites a récemment levé 48.5 millions de dollars, qu’est-ce que cela signifie pour l’entreprise ?
Bien que nous ayons travaillé avec de jeunes utilisateurs au cours des trois dernières années, nous devons augmenter notre capacité de production pour 1) mettre en ligne les commandes de production en volume plus élevé de nos clients « jeunes utilisateurs » qui ont qualifié notre technologie de fabrication et 2) répondre à la forte augmentation des clients « majoritaires précoces » qui travaillent à la qualification aujourd’hui. Par conséquent, l’augmentation de la capacité de production et des ressources d’ingénierie et de collaboration avec les clients sont deux domaines d’expansion majeurs chez Arris Composites.
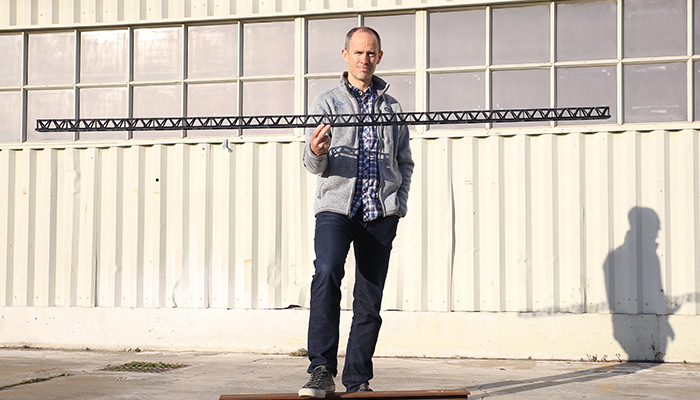
Ethan Escowitz tenant une pièce en fibre de carbone continue de 2,4 mètres (crédits photo : Arris Composites)
3DN: À quoi ressemble la fabrication additive pour la production de masse ? Quels sont les principaux avantages et limites ?
La production de masse utilisant Additive Molding™ ressemble à bien des égards à d’autres systèmes de fabrication avancés car nous tirons parti des technologies existantes comme la robotique, l’automatisation industrielle et les contrôles industriels. L’utilisation des meilleures technologies de fabrication disponibles sur le marché pour faire fonctionner notre matériel de traitement unique offre la fiabilité, la répétabilité et l’évolutivité requises dans les environnements de production.
Bien que nous ayons remporté d’importantes victoires en matière de pièces de rechange, certains des avantages les plus importants pour nos clients demeurent dans les performances des produits et l’efficacité de la fabrication qui découlent de la consolidation d’un assemblage complexe de plusieurs pièces et parfois de plusieurs matériaux en une seule pièce dans le cadre de volumes de production. Notre procédé permet de créer des géométries complexes, composées des matériaux les plus résistants et les plus légers pour la structure adjacente aux matériaux fonctionnels (métaux, plastiques, céramiques, etc.) afin d’optimiser les diverses exigences de performance d’un produit. Généralement, ce type d’architecture est soit impossible, soit d’un coût prohibitif.
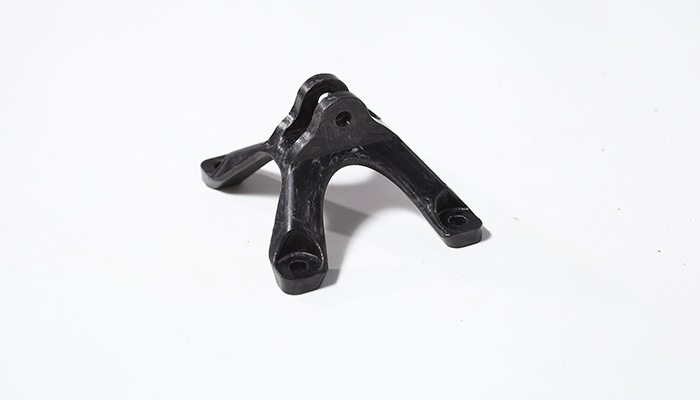
Un support de fixation pour l’aérospatiale (crédits photo : Arris Composites)
Notre plus grande limite est la même que celle de nos collègues du marché de la fabrication additive. Il faut du temps pour former les ingénieurs et les concepteurs à un nouveau processus de fabrication, pour identifier les meilleurs produits et applications sur lesquels collaborer, puis pour qualifier et mettre ces nouveaux produits sur le marché. Cela dit, nous travaillons déjà avec les leaders de l’électronique grand public, des articles de sport, de l’automobile et de l’aérospatiale. Je pense que les efforts collectifs de l’industrie de la fabrication additive, en particulier au cours de la dernière décennie, ont aidé ces leaders de tous les secteurs à accélérer le processus d’évaluation et d’adoption de nouvelles méthodes de fabrication. En ce qui concerne les limites techniques, notre processus implique des coûts fixes qui n’ont généralement pas de sens pour moins de 100 pièces au total (c’est pour cela que nous avons des imprimantes 3D et des machines CNC).
3DN : Un dernier mot pour nos lecteurs ?
Beaucoup de mots ont été consacrés à l’impact que l’impression 3D aura sur la fabrication et beaucoup d’entre eux indiquent qu’elle remplacera la fabrication conventionnelle. Bien que cela puisse être exact pour certains produits, comme les tuyères de moteurs à réaction, je voudrais partager mon expérience en matière de développement d’applications dans un certain nombre de technologies 3D. La fabrication additive améliore bien plus qu’elle ne remplace les technologies de fabrication conventionnelles qui produisent la grande majorité des produits dans le monde. Les applications telles que les gabarits et les dispositifs de fixation, les moules, les composants d’automatisation personnalisés et, bien sûr, le prototypage, réduisent toutes les coûts de mise en place et d’exploitation de la fabrication et accélèrent le délai de mise sur le marché. Notre technologie Additive Molding est essentiellement un exemple hautement intégré de ce point. En appliquant une technique de moulage additif à une méthode de fabrication conventionnelle, nous avons pu bénéficier des avantages des deux.
Enfin, examinons le marché dans les années à venir. Nous sommes à un moment important de la fabrication où les progrès dans un certain nombre de domaines ont convergé, créant une prolifération de nouvelles architectures de produits. En ce moment, avec les nouvelles technologies de fabrication, nous ne travaillons plus contre l’inertie des fournisseurs en place et des technologies de fabrication précédemment spécifiées. Dans ces moments-là, la logique règne et les meilleures solutions en termes de coût/performance prévalent. C’est là que nous pouvons accélérer les progrès le long de la courbe d’adoption. Vous pouvez trouver plus d’informations ICI.
Que pensez-vous de la technologie de l’entreprise Arris Composites ? Partagez votre avis dans les commentaires de l’article ou avec les membres du forum 3Dnatives. Retrouvez toutes nos vidéos sur notre chaîne YouTube ou suivez-nous sur Facebook ou Twitter !