HAVA3D accompagne l’armée de Terre dans le déploiement de la plus grande ferme d’imprimantes 3D d’Europe
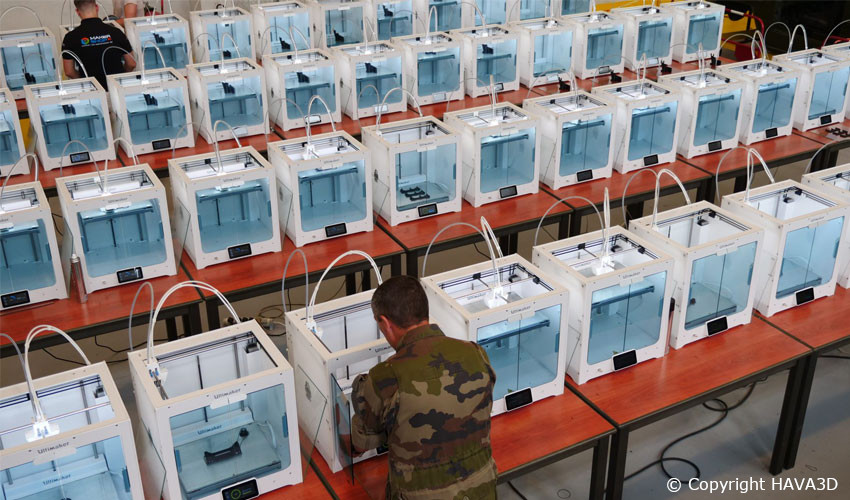
Aux Ecoles Militaires de Bourges, 60 imprimantes 3D FDM ont trouvé un nouveau foyer depuis avril dernier, installées par les équipes du groupe français HAVA3D dans le cadre d’un plan d’investissement visant à offrir davantage d’autonomie à l’armée de Terre française. Ces imprimantes constituent la plus grande ferme d’imprimantes 3D militaire en Europe et permettent aujourd’hui à l’armée française d’être plus flexible dans la production de pièces détachées et de petites séries. Bagues, capuchons, commodos, ce sont plus de 70 000 pièces qui ont été imprimées en 3D dans cette ferme baptisée I3D.
Grâce à un accompagnement de la part des équipes techniques de HAVA3D auprès des opérateurs machines, les Ecoles Militaires de Bourges tirent désormais pleinement profit des imprimantes 3D : celles-ci raccourcissent les délais de fabrication, évitent des immobilisations de véhicules trop longues sur le terrain et forment leurs élèves et stagiaires sur des outils pédagogiques plus concrets.
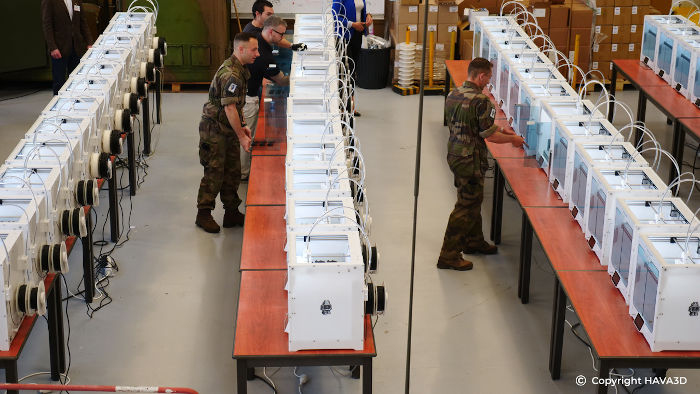
La ferme d’imprimantes 3D au sein des Ecoles Militaires de Bourges
Depuis quelques années maintenant, l’armée française s’intéresse de près aux capacités de la fabrication additive : dans le cadre de l’opération Barkhane par exemple, elle avait investi dans plusieurs machines dont une reposant sur un procédé de frittage sélectif laser afin de concevoir différentes pièces directement sur le terrain. Un investissement qui s’était avéré particulièrement utile pendant la crise du COVID-19 où la majorité des secteurs ont été touchés par la rupture des chaînes d’approvisionnement. A Bourges, le constat est le même : installées mi-avril en 5 jours seulement, les 60 machines ont aidé à faire face à la crise sanitaire. Les imprimantes 3D ont servi dans un premier temps à fabriquer des équipements de protection individuelle, puis à concevoir tout type de pièces, du sous-ensemble complet au composant élémentaire. L’armée pouvait imaginer et fabriquer tout ce dont elle avait besoin sans dépendre d’une chaîne d’approvisionnement lourde et affaiblie par la COVID-19.
La plus grande ferme d’imprimantes 3D militaire d’Europe
Plusieurs facteurs ont motivé les Ecoles Militaires de Bourges (EMB) à investir dans la fabrication additive. Tout d’abord, c’est un procédé qui permet de modéliser et de réaliser très rapidement une pièce, sans passer par des processus industriels lourds, chers et souvent inadaptés à de la petite série. Les technologies 3D répondent à un besoin de production à la demande, locale et flexible. L’armée de Terre peut ainsi imaginer des pièces détachées qui ne sont plus fabriquées par le fournisseur d’origine ou tout simplement améliorer les fonctionnalités de certains composants. Le Général de brigade Baldi, commandant des EMB, explique : « Entre une commande, l’ordre reçu, la modélisation de la pièce ou la récupération du fichier numérique, et le lancement de l’opération, il faut compter quelques heures. Nous sommes capables de travailler en série grâce à notre ferme d’imprimantes 3D et d’avoir une meilleure capacité de réaction, que ce soit dans le temps ou dans la production. »
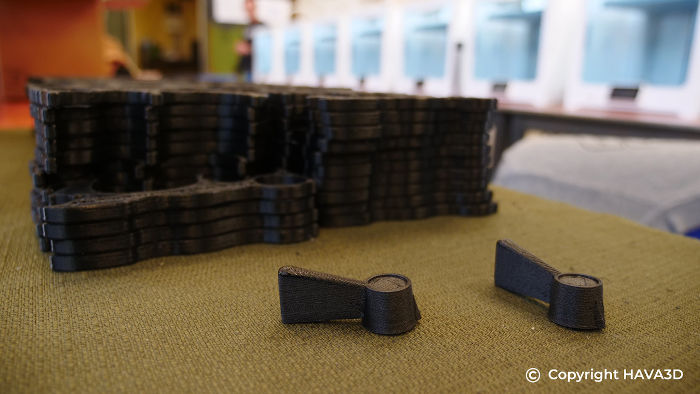
L’Armée de Terre imprime différentes pièces comme des commutateurs
Depuis la mise en marche des machines, les opérateurs ont imprimé plus de 70 000 pièces. Parmi celles réalisées, on trouve ainsi un bocal de lave-glace pour un véhicule de l’avant blindé (VAB), une pièce qui n’est plus approvisionnée par le fabricant d’origine. On peut aussi parler des pieds de support de caméra thermique imprimés en 3D en 4 heures : l’objectif était de trouver une solution pour fixer tout type de caméra sur un trépied rapidement et d’améliorer les fonctionnalités du capteur. L’armée a ainsi conçu une plate-forme adaptateur avec un polyamide BASF Ultrafuse PAHT CF15, un plastique connu pour ses propriétés de haute résistance thermique et de rigidité mais offrant toutefois une facilité d’impression et de stabilité dimensionnelle.
Les équipes ont également imprimé des commutateurs de véhicules légers, les pièces originales étant trop usées. C’est un PETG en fibre de carbone qui a été privilégié ; la pièce, imprimée en 2 heures, offre des fonctionnalités identiques et résiste parfaitement à une utilisation régulière. On peut aussi citer des étuis de protection pour les bouteilles médicales imprimés en 5 heures avec un TPU semi-rigide. L’objectif est finalement d’être autonome dans la production et ne plus dépendre de fournisseurs externes, mais aussi de proposer des idées innovantes qui n’auraient pas pu être matérialisées aussi facilement via des méthodes de production classiques. Cela réduit les temps d’immobilisation et les risques de panne.
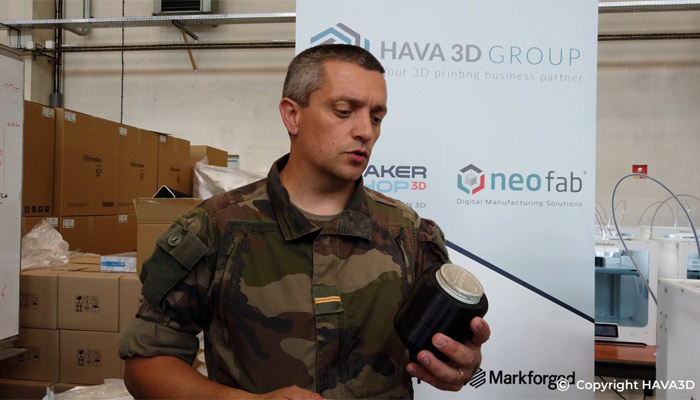
Un bocal de lave-glace imprimé en 3D
Au-delà de la production de pièces pour les activités de terrain, la ferme d’imprimantes 3D a également une vocation pédagogique. L’étape de formation est aujourd’hui assez complexe, les élèves passant soit par la lecture de schémas compliqués, ou alors par la manipulation de vrais ensembles qui sont lourds et difficiles à manipuler mais aussi à sourcer. Grâce à sa ferme d’imprimantes 3D, l’armée peut réaliser des modèles réduits de ces ensembles ce qui facilite la visualisation, la manipulation et la compréhension. Un mécanicien pourra ainsi se former sur une boîte de vitesse, un moteur ou un pont différentiel imprimé en 3D plus aisément.
Un accompagnement nécessaire pour une réelle autonomie
Si l’armée a pu imprimer autant de pièces en seulement quelques mois, c’est aussi grâce à l’accompagnement du groupe HAVA3D et plus particulièrement à travers l’une de ses divisions, Makershop. Le Général de brigade Baldi affirme : « Notre succès vient surtout du dialogue permanent entre les opérateurs, le chef de production et son correspondant industriel chez HAVA3D. Ils nous ont accompagnés dans la mise en œuvre des imprimantes en nous apportant une autonomie progressive, mais aussi pendant toute la phase de production. Si nous avons un quelconque problème avec une machine, ils peuvent le résoudre très rapidement. »
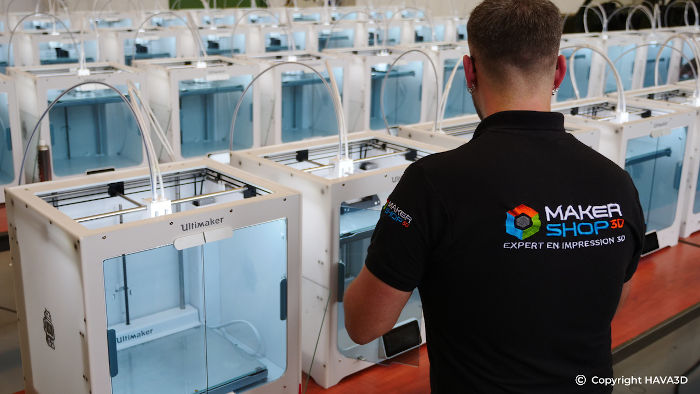
Makershop a accompagné l’Armée de Terre dans l’installation des 60 Ultimaker S5
Le groupe français a d’ailleurs conseillé les EBM dans le choix des imprimantes 3D. C’est le modèle Ultimaker S5 qui a été choisi, une machine qui peut être rapidement installée et prête à l’emploi et qui est compatible avec un large choix de matériaux, du thermoplastique standard comme l’ABS à plus technique comme le PETG. Stanislas Clicquot, PDG de HAVA3D, ajoute : « Nous avons proposé un modèle d’imprimante professionnelle : l’Ultimaker© S5. Puissante, fiable, polyvalente et intuitive, elle permet de répondre très rapidement et efficacement à une gestion de crise avec une production centralisée. Cette solution peut aussi être facilement déployée au sein des différents régiments et permettre un mode de production distribué pour plus de réactivité et d’agilité au sein de l’armée. »
L’objectif de l’armée de Terre est d’investir dans 130 imprimantes 3D d’ici 2021, objectif qu’elle devrait atteindre sans trop de difficultés et qui permettrait d’élargir toujours plus le champ d’applications de l’impression 3D. Vous pouvez retrouver davantage d’informations sur cette ferme d’imprimantes 3D en vidéo ci-dessous :
Que pensez-vous de l’utilisation de la fabrication additive par l’Armée de Terre ? Partagez votre avis dans les commentaires de l’article ou avec les membres du forum 3Dnatives. Retrouvez toutes nos vidéos sur notre chaîne YouTube ou suivez-nous sur Facebook ou Twitter !
Dommage, qu’ils n’aient pas pris le temps de travailler avec des imprimantes 3d à résine étant bien plus rapide pour le niveau de détails obtenus. Je pense que le frein principal c’est l’odeur toxique de la résine mais avec un masque ffp2, il n’y a pas de problèmes.
Xau
Le detail n’etais pas la premiere contrainte mais surtout la solidité sur le terrain et la facilité d’utilisation
Effectivement, il existe aujourd’hui des imprimantes 3D résine qui travaillent à 10cm de l’heure avec des résines aux propriétés intéressantes dont la qualité est proche d’une pièce injectée et le tout pour un coût d’équipement abordable.
les imprimante 3D résine, ca sera peut-être dans un second temps. mais déja ils avaient une imprimante de frittage laser métal. ca permet de faire des choses quand meme. du cote mili, la priorité est la resistance. pas de remplacer toutes les pieces de tous les materiels par des fac similés imprimés..peut etre un jour, mais déja, c’est un beau progrés, dommage que le gouvernement n’ait pas laissé faire les militaires en janvier et fevrier., eux, ils auraient mis en place une usine de masques rapidement. on a quand meme polytechnique ,le génie et dautres. les resources en cerveaux francais ne manquent pas.c’est la volonté en haut qui est absente. à tout vouloir controler et centraliser entre les mains d’un seul homme limité, on finit par ne faire que du vent,pour faire tourner les girouettes. n’est pas napoléon qui veut..
Comment est gérée la propriété intellectuelle?
Quid de la responsabilité des industriels ?
L’armée a-t-elle fait une expérimentation sur ces questions là ?
Elles restent à mon sens les principaux pour le passage à une production distribuée.
Logique différente.l’armee fabrique et utilise en interne. Pas de revente. Et je penses, sur des choses basiques. Ces ‘problèmes’ ne sont que des faux fuyants pour ne pas faire. Lorsque cela se présentera ou même avant, ces problèmes seront tranchés. Il est certain qu’a partir du moment où des pièces d’armement ou autres conçus par des industriels seront fabriqués sur place, les industriels en question trouveront leur intérêt à négocier une rétrocession sur l’usage de leur propriété industrielle. Sur le terrain, c’est l’opérationnel qui compte.
C’est bien mais pourquoi ne pas investir dans une imprimante française , pour permettre d’être autonome en cas de crises mondial on ne retiens pas les leçon qui sont pourtant toujours en cours.
Et pou pour la relance de économie française
Mais pourquoi achete de l’ultimaker! Pourquoi pas du Volumic 3D!!!
Très efficace probablement. Bravo.
Les modèles 3D des pièces non obsolètes sont t’ils fournis/ouverts pas les grands donneurs d’ordres…?
Enfin, il eu été bienvenu de passer aussi un accord avec un concepteur et fabricant français d’imprimante 3D (comme par exemple, les excellents Volumic3D, ou Gorgé), et pas uniquement le distributeur makershop d’un produit étranger (aussi bon soit il et aussi bonne les ultimaker soient elles).
Bonjour
J’ai juste une question : depuis quand le PETG est plus « technique que l’ABS ?!