Les applications de l’impression 3D métal les plus innovantes au Formnext 2024
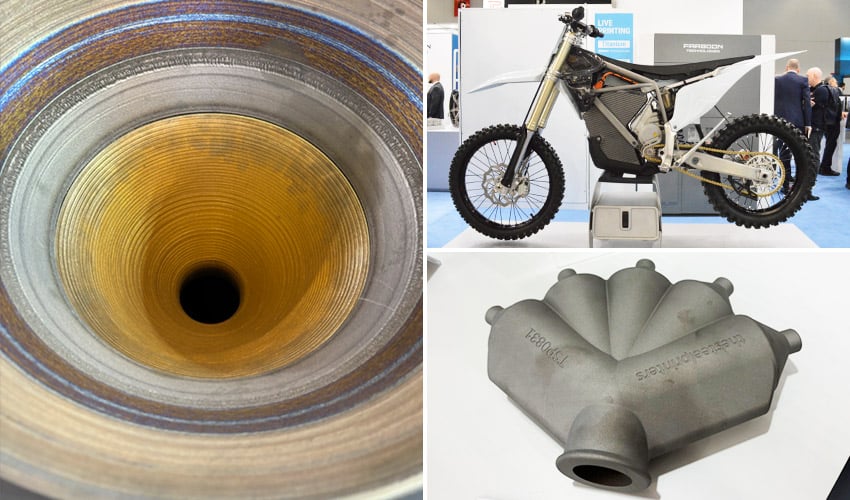
Formnext est l’endroit idéal pour découvrir des innovations, qu’il s’agisse d’impression 3D, de logiciels ou de matériaux. Cependant, il serait dommage de passer à côté des applications que les entreprises mettent en avant sur leurs stands. Actuellement sur place, nos équipes ont pu remarquer de nombreux cas d’usages, plus particulièrement dans l’impression 3D métal, que ce soit dans l’aérospatiale, l’automobile ou encore le médical. Voici un aperçu des exemples les plus marquants que nous avons découverts cette année.
La buse multi-matériaux d’InssTek
Parmi les applications qui ont retenu notre attention à Formnext, la tuyère de fusée multi-matériaux présentée sur le stand d’InssTek est particulièrement intéressante. Cette pièce de 3 tonnes (301 x 201 x 567 mm), réalisée en 600 heures, ainsi que son extension (432 x 270 x 169 mm), fabriquée en 64 heures, ont été produites grâce à la technologie d’impression 3D par dépôt d’énergie directe (DED), en collaboration avec l’Institut coréen de recherche aérospatiale (KARI). Chaque pièce a été fabriquée en utilisant le matériau optimal pour chaque composant, une caractéristique rendue possible par la technologie DMT d’InssTek. Par exemple, l’intérieur de la buse est fabriqué en Al-Bronze, avec un canal de refroidissement à intervalles de seulement 1 mm, tandis que l’extérieur est constitué d’Inconel 625. L’extension, quant à elle, est en C-103, un matériau particulièrement prisé dans l’industrie spatiale actuelle.
La pièce unifiée qui en résulte est intéressante, car la combinaison de différents métaux exploite la force de chacun d’entre eux, permettant ainsi de concevoir des structures complexes avec des fonctionnalités avancées. Ces innovations contribuent à améliorer l’efficacité et la fiabilité des composants de moteurs de fusée. Selon InssTek, cette avancée est le fruit de tests approfondis, incluant des essais de combustion réussis. Pour garantir la fiabilité des multi-matériaux, chaque composant a été fabriqué après des analyses approfondies menées grâce au MX-Lab, qui inclut des tests de résistance à la traction et de conductivité thermique. Ces avancées laissent présager des solutions sur mesure capables de répondre aux défis complexes de l’aérospatiale moderne. Le secteur spatial coréen a ainsi franchi une étape importante, ouvrant la voie à de nouvelles avancées dans l’utilisation de la fabrication additive pour la propulsion spatiale. Vous pouvez en savoir plus sur les solutions InssTek ICI ainsi que sur le stand D98 dans le hall 12.0 à Formnext.
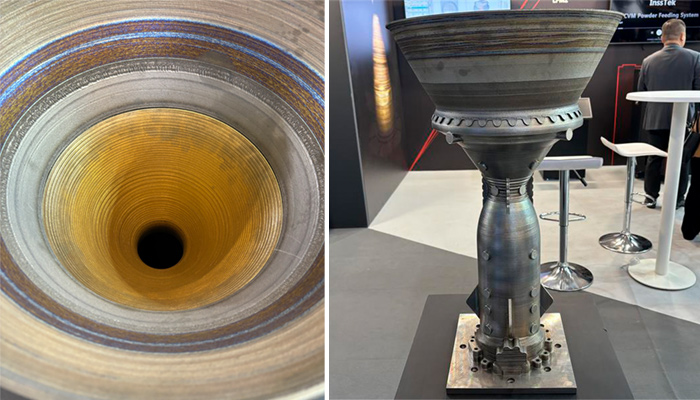
Tuyère de fusée multi-matériaux d’InssTek montrant l’intérieur (à gauche) et l’extérieur (à droite).
Fabrication d’un d’un cadre de moto électrique haut de gamme grâce à l’impression 3D métal
Une autre application que nous souhaitons mettre en avant à Formnext provient de Farsoon Europe, une entreprise asiatique spécialisée dans les solutions d’impression 3D métal polymère. En collaboration avec Stark Future, Farsoon Europe travaille au développement de solutions de fabrication performantes et évolutives pour le marché des motos électriques haut de gamme. Un exemple clair de cette collaboration est un cadre de moto complet, fabriqué en alliage de titane à l’aide de l’imprimante 3D FS721M-H-8-CAMS de Farsoon Europe. Cette solution métallique industrielle, conçue pour répondre aux demandes de production grand format, offre un volume d’impression de 720 x 420 x 650 mm.
Elle est également équipée de huit lasers à fibre de 1000 W, permettant d’optimiser la productivité tout en réduisant les coûts de production. Le système intègre également la solution CAMS de Farsoon Europe, qui utilise un système de convoyage unique et des cartouches interchangeables pour garantir une production continue et minimiser les temps d’arrêt entre les impressions. Si vous souhaitez découvrir cette pièce en métal en personne, rendez-vous sur le stand E11 dans le hall 11.0 à Formnext. Pour plus d’informations, vous pouvez consulter le site web de Farsoon Europe ICI.
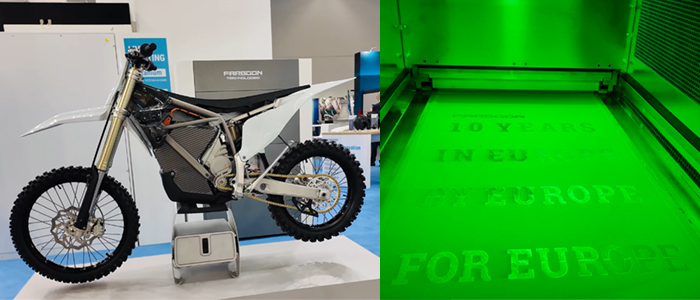
Le cadre de moto imprimé en 3D (à gauche) et la technologie Farsoon Europe (à droite).
FIDENTIS et ses prothèses multi-métaux
Les applications de la fabrication additive en dentisterie ne sont pas nouvelles, mais l’utilisation de l’impression 3D métal dans ce domaine reste un peu inhabituelle. C’est ici que FIDENTIS se distingue. Issue du Fraunhofer IGCV, cette startup a développé une solution de fusion laser sur lit de poudre multi-matériaux, particulièrement adaptée à la fabrication de prothèses dentaires. Cette technologie combine un lit de poudre et un robot capable de déposer des matériaux supplémentaires, permettant ainsi de traiter simultanément deux alliages ou plus. Pour cette application spécifique, cela inclut l’utilisation de CoCr avec de l’or fusionné sur la surface de frottement. FIDENTIS affirme que ce procédé est 20 fois plus rapide et 60 % moins coûteux que les méthodes traditionnelles. L’accueil enthousiaste réservé à cette application a valu à l’entreprise d’être finaliste du prix Rookie à Formnext 2024. Les visiteurs peuvent découvrir ces prothèses multi-matériaux sur le stand du Fraunhofer IGCV.
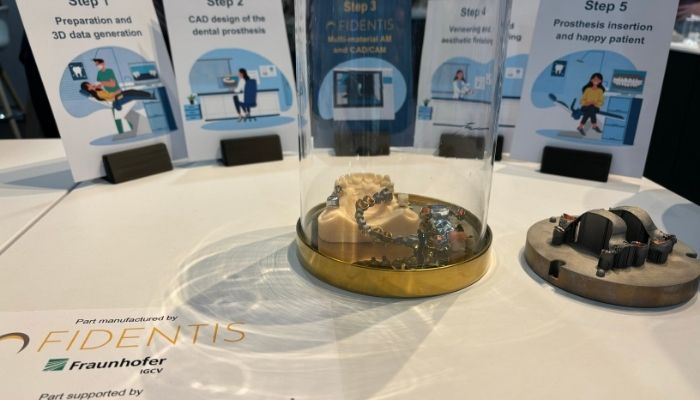
Les prothèses dentaires en métal exposées à Formnext.
Des écouteurs intra-auriculaires pour les musiciens
Les écouteurs intra-auriculaires sont essentiels pour les musiciens et chanteurs, leur permettant d’entendre leur performance sur scène. Mais saviez-vous qu’ils peuvent être fabriqués non seulement grâce à l’impression 3D, mais aussi à partir de métal ? Sur le stand de Bright Laser Technologies (BLT), les écouteurs intra-auriculaires métalliques, produits à l’aide de l’imprimante 3D BLT A160 500W, sont mis en avant. Conçus par la société EarFit, une entreprise spécialisée dans les solutions acoustiques haut de gamme pour musiciens, ces écouteurs intra-auriculaires en titane (160 mm x 160 mm x 160 mm) ont été imaginés pour offrir un son personnalisé, de haute qualité et d’une clarté cristalline. L’impression 3D a été choisie pour sa capacité à créer des solutions plus rentables, fiables et pratiques, dépassant ainsi les limites des méthodes de fabrication traditionnelles.
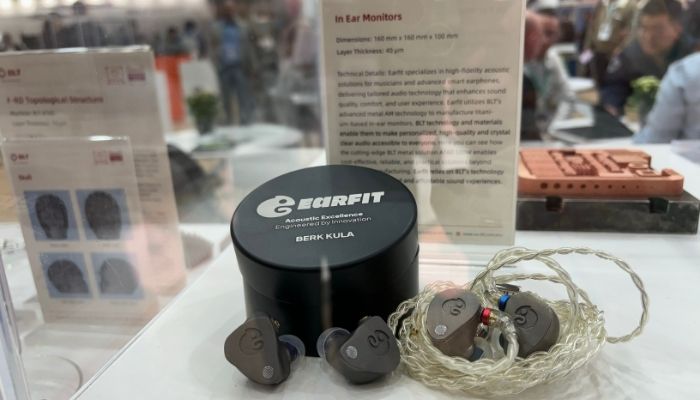
Les écouteurs intra-auriculaires en titane sur le stand de BLT.
Le vélo de Renishaw récompensé par une médaille olympique
Les Jeux Olympiques de Paris 2024 sont désormais derrière nous, mais à Formnext, vous pouvez encore découvrir une application captivante. Le fabricant britannique Renishaw met en avant un vélo de piste, développé en collaboration avec British Cycling, Lotus Engineering et Hope Technology, qui a contribué à la récolte de huit médailles aux Jeux Olympiques de cette année. Ce vélo est particulièrement intéressant car il comprend des pièces imprimées en 3D avec la RenAM 500Q de Renishaw, notamment la tige de selle et la manivelle, fabriquées en titane. Le pédalier a été conçu en Ti6Al4v, avec une structure interne en treillis, alliant solidité et légèreté pour répondre aux exigences strictes de performance du vélo. Une démonstration de la manière dont l’impression 3D peut transformer les équipements de cyclisme de haut niveau.
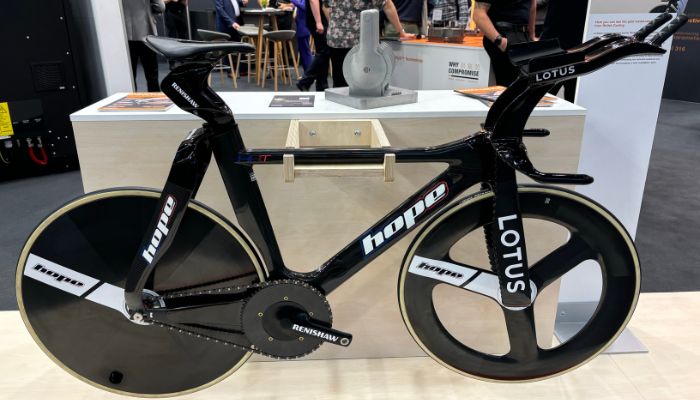
Le vélo médaillé d’or avec la manivelle en métal.
La plus grande pièce métallique imprimée en 3D de Finlande au salon Formnext 2024
Avec les pays nordiques à l’honneur au Formnext 2023, nous avons vu comment la fabrication additive se développe dans la région. Elle fait son grand retour à Formnext 2024 avec un nouveau pavillon dans le hall 11.1. C’est ici qu’on peut découvrir une application intéressante : un récipient sous pression, le plus grand de Finlande, fabriqué en métal grâce à l’impression 3D. Pesant 300 kg, ce composant a été testé selon la norme EN 13445-3 et est réalisé avec un acier inoxydable résistant aux acides à l’aide de la technologie WAAM. Avec un diamètre de 900 mm et une hauteur de 1 600 mm, il a été soumis à des tests de pression allant jusqu’à 111 bar, bien au-delà de la pression de 10 bar pour laquelle il a été initialement conçu. Ce projet est le fruit d’une collaboration entre ANDRITZ Savonlinna Works Oy et l’écosystème FAME, avec des tests non destructifs et destructifs réalisés par la LUT University.
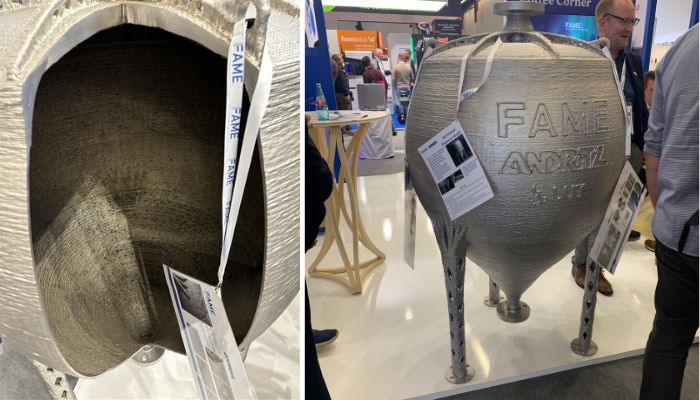
La partie montrant l’intérieur (à gauche) et l’extérieur (à droite).
EPlus3D et LEAP 71 présentent le plus grand propulseur de fusée au monde imprimé en métal
En plus de la tuyère multi-matériaux d’InssTek, nous avons été particulièrement captivés par le propulseur de fusée développé par EPlus3D et LEAP 71. Considéré par les entreprises comme le plus grand propulseur de fusée métallique imprimé en 3D au monde, ce modèle de 200 kN a été fabriqué en une seule pièce, mesurant plus de 1,3 mètre de hauteur.
Alimenté par de l’oxygène liquide cryogénique et du kérosène, ce propulseur représente une avancée par rapport au moteur-fusée Noyron TKL-5 de LEAP 71, qu’ils ont réussi à faire fonctionner en juin, tout en étant 40 fois plus puissant. Il a été réalisé en AlSi10Mg, un alliage d’aluminium haute performance, sur l’imprimante DMLS Eplus3D EP-M650-1600. Ce qui distingue particulièrement ce projet, c’est la capacité à intégrer en une seule pièce les multiples composants d’un propulseur de fusée, tels que la chambre de combustion, la tuyère, les canaux de refroidissement, les collecteurs et les éléments structurels. Cette approche pourrait réduire considérablement le temps nécessaire pour l’assurance qualité, car il ne sera plus nécessaire de tester chaque composant individuellement.
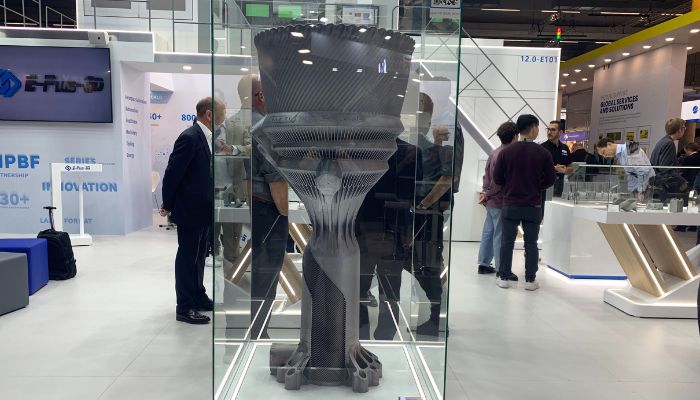
Le propulseur de fusée exposé à Formnext 2024.
Une buse à cinq sorties pour les piles de coke
L’une des dernières applications métalliques présentées à Formnext est une buse spécialement conçue pour les batteries de fours à coke. Pour mieux comprendre, une batterie de fours à coke est un ensemble de fours utilisés pour transformer le charbon en coke, un combustible riche en carbone crucial dans des secteurs tels que la fonte du minerai de fer, ainsi que dans les poêles et les forges. Cette buse à cinq sorties a été développée par ArcelorMittal en partenariat avec TheSteelPrinters. Elle regroupe cinq buses individuelles en un seul composant, ce qui permet de simplifier l’entretien et d’améliorer l’efficacité. En plus de sa conception sur mesure, cette solution a permis de réduire le délai de fabrication de quatre mois à seulement trois semaines. Le matériau utilisé, l’AdamIQ3167L, a été conçu par TheSteelPrinters, spécialisé dans l’impression 3D métallique, et optimisé pour le processus LPBF. Cette pièce pèse 8 kg et mesure 73 x 300 x 228 mm. Vous pouvez la découvrir sur le stand d’ArcelorMittal, hall 11.0.
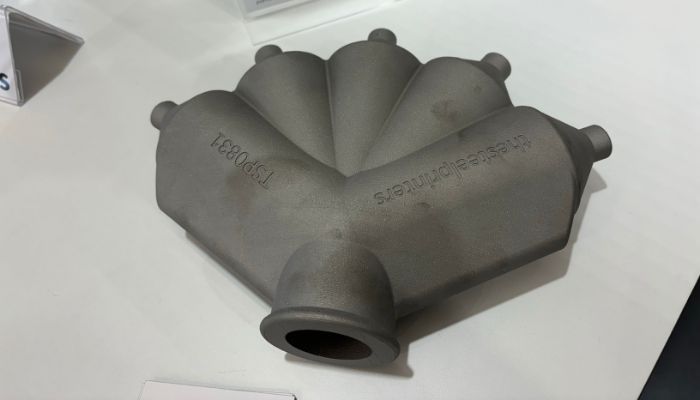
Un examen plus approfondi du composant à 5 buses.
Que pensez-vous de ces applications d’impression 3D métal présentées à Formnext 2024 ? Partagez votre avis dans les commentaires de l’article. Retrouvez toutes nos vidéos sur notre chaîne YouTube ou suivez-nous sur Facebook ou LinkedIn !
*Crédits de toutes les photos : 3Dnatives