L’optimisation topologique pour l’impression 3D
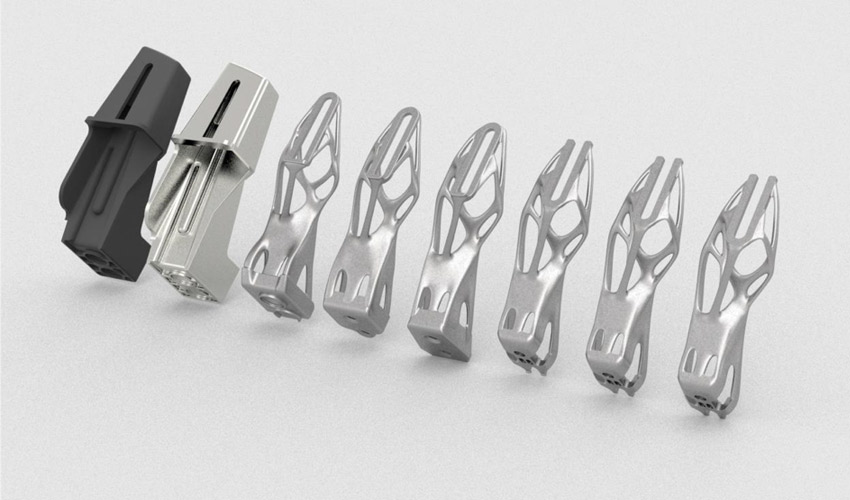
La fabrication additive, contrairement aux techniques d’usinage traditionnelles, permet de réaliser des pièces aux géométries complexes dont le poids total peut être optimisé à l’aide d’une méthode numérique appelée « optimisation topologique ». Celle-ci permet également de maximiser la résistance mécanique de la pièce créée. L’optimisation topologique est en fait un sous-domaine de la conception numérique qui permet de trouver, grâce à des formules mathématiques, la répartition de matière optimale dans un volume donné soumis à des contraintes mécaniques plus ou moins importantes.
L’optimisation topologique consiste donc à « supprimer » la matière là où les efforts ne transitent pas à l’aide d’un logiciel dédié. Parmi les plus connus, on retrouve les solutions Ansys Discovery, Tosca de Dassault Systèmes, Within Labs d’Autodesk, Inspire de SolidThinking, Netfabb ou encore Simufact Additive.
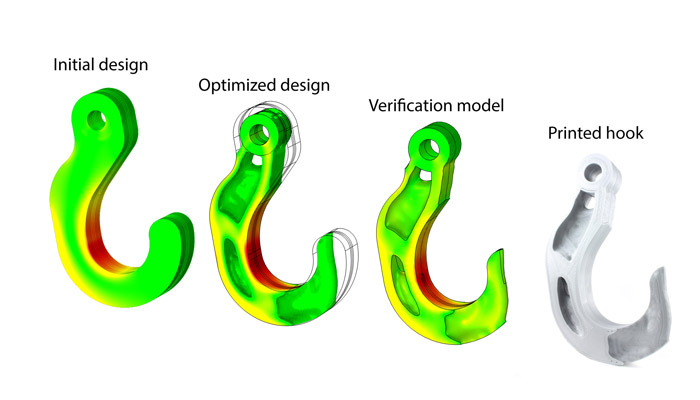
Le processus de conception via l’optimisation topologique
L’optimisation topologique, comment ca marche ?
Les procédés de conception numérique classiques consistent à appliquer des charges sur une pièce déjà fabriquée et à évaluer les endroits où elle faiblit ; les ingénieurs doivent alors repenser la conception jusqu’à ce que la pièce réponde aux contraintes mécaniques données. Avec l’optimisation topologique, la logique est différente : les charges mécaniques sont les données d’entrée qui vont permettre au logiciel de proposer une nouvelle géométrie de la pièce. Les itérations sont donc à priori moins nombreuses ce qui réduit considérablement les délais de conception et fabrication.
Concrètement, l’optimisation topologique débute par la création d’un modèle 3D grossier lors de la conception ou bien par l’utilisation d’une pièce déjà existante pour une évolution à laquelle on va appliquer différentes charges et forces supportées par la pièce (une pression sur les pattes de fixation par exemple). Le logiciel se charge alors de calculer l’ensemble des contraintes appliquées.
À ce niveau, un découpage de la pièce peut-être réalisé afin de supprimer les parties non-soumises aux efforts. Une ébauche de la future pièce optimisée est alors déjà visible. La géométrie finale, répondant aux exigences à la fois mécaniques et de design, peut être alors finalement être obtenue après lissage de la pièce. Finalement, l’optimisation topologique répond soit à un besoin de réduction de la masse ou soit à une augmentation de la résistance mécanique de la pièce.
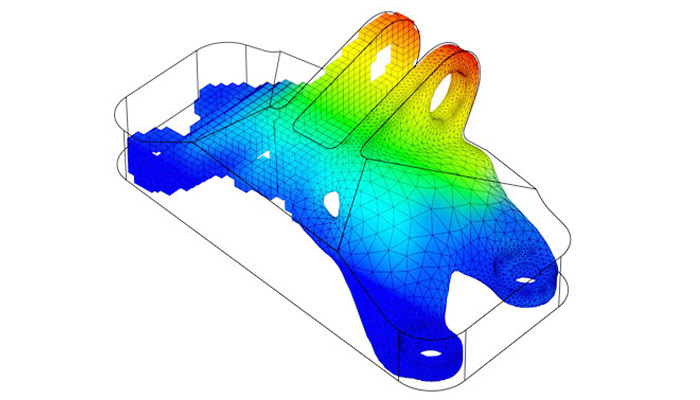
Crédits photo : Frustum/3D Systems
Les logiciels dédiés à l’optimisation de la topologie
Tous les logiciels de CAO n’offrent pas cette fonction d’optimisation topologique : même si celle-ci n’est pas forcément utilisée dans le processus de modélisation et de fabrication, il peut être préférable d’opter pour une solution qui l’inclut, pour être sûr de concevoir une pièce optimale. Certains éditeurs ont donc développé des logiciels dédiés. L’un des pionniers est sans doute Altair avec sa toute première solution OptiStruct, rejointe ensuite une autre solution, Altair Inspire. Nous pouvons également citer Ansys, Dassault Systèmes, Autodesk ou encore nTopology. Il existe de nombreux logiciels de CAO qui intègrent quant à eux des fonctionnalités pour optimiser sa pièce – on pense à Solidworks, Creo ou encore Fusion 360.
Vous l’aurez compris, choisir son logiciel d’optimisation topologique est donc une étape clé car l’outil permettra de définir les contraintes de la pièce à créer en fonction du matériau de fabrication, des propriétés géométriques et des charges mécaniques imposées. Il analysera les différents cas de charge, que la pièce soit utilisée normalement ou dans des cas extrêmes, mais aussi l’espace disponible pour la conception ainsi que les zones à ne pas modifier. Il sera donc votre meilleur allié dans cette étape de conception.
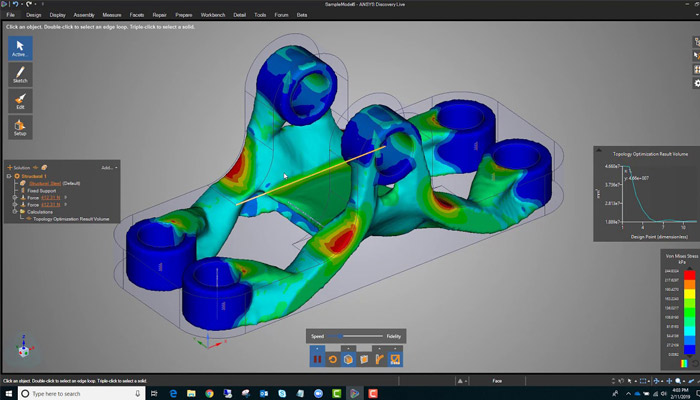
Plusieurs logiciels sont aujourd’hui disponibles
Qui utilise l’optimisation topologique et à quelles fins ?
L’automobile s’est rapidement penchée sur ce problème pour des raisons de réduction de coûts directs à travers l’économie de matières premières associée aux tailles de séries. En effet, un gain de quelques grammes par véhicule, sur une production de plusieurs millions d’unités, représente des tonnes de matière économisées. On pense directement au châssis imprimé en 3D de la Light Rider, une pièce qui ne pèse que 6 kilos grâce à une répartition de la matière optimale. Plus récemment, on peut évoquer la pièce de suspension de Fiat Chrysler Automobiles qui réunit plus de 12 composants différents en un seul. En misant sur l’optimisation topologique, les concepteurs auraient réduit de 36% son poids final.
L’aéronautique est sans aucun doute un autre secteur qui s’intéresse beaucoup à l’optimisation topologique, dans une logique de réduction de coûts indirects. Un aéronef moins lourd consomme moins de carburant ce qui sur le long terme engendre des économies non négligeables pour une compagnie aérienne. C’est ce qu’avait prouvé le designer Andreas Bastian avec ses sièges d’avion : il avait imaginé une conception 54% plus légère ce qui, mis bout à bout, représenterait une réduction de poids très élevée pour un avion. Au delà de l’aspect poids, l’optimisation topologique permet surtout au secteur aéronautique d’imaginer des formes beaucoup plus complexes puisque l’industrie se libère des contraintes imposées par un moule.
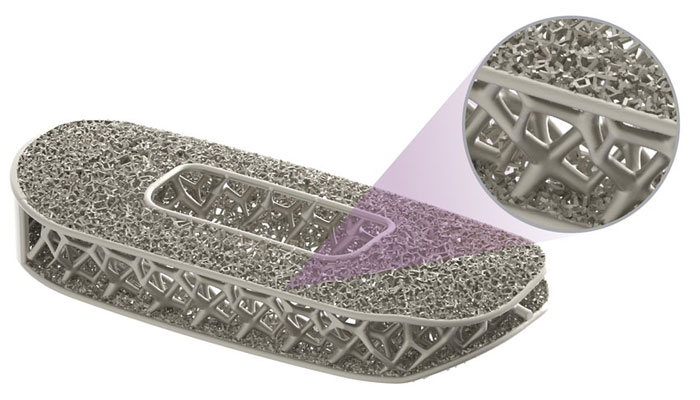
Dans le secteur médical, l’optimisation topologique permet de concevoir des implants plus résistants (crédits photo : Nuvasive)
Enfin, le médical se penche quant à lui sur cette méthode de conception notamment pour la fabrication d’implants sur-mesure : elle permet d’imiter la densité et la rigidité des os, tout en réduisant son poids total. En effet, de nombreux implants intègrent des structures lattices et restent aussi solides que ceux traditionnellement conçus, voire plus pour certains.
Et vous, utilisez-vous l’optimisation topologique ? Partagez votre avis dans les commentaires de l’article ou avec les membres du forum 3Dnatives. Retrouvez toutes nos vidéos sur notre chaîne YouTube ou suivez-nous sur Facebook ou Twitter !
Sympa l’article. Mais pourquoi dire « gain de 84% » alors que c’est une perte? la pièce est pourtant plus légère et non plus lourde !
On parle de « gain » car c’est une « perte positive » de masse et donc une économie de matière
Bonjour,
Sur quel logiciel avez-vous effectué ce test ?