A la découverte des matériaux d’impression 3D : Les plastiques
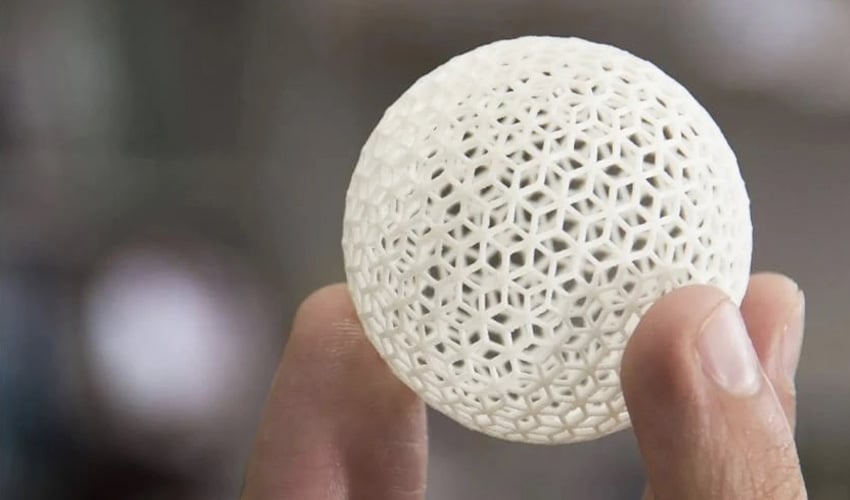
Un plastique est un matériau fabriqué à partir de composés synthétiques ou semi-synthétiques qui est malléable (capable de changer de forme). La plupart des plastiques sur le marché sont entièrement synthétiques et sont généralement dérivés de produits chimiques pétroliers. Cependant, compte tenu de la préoccupation croissante pour l’environnement, les plastiques fabriqués à partir de matériaux renouvelables tels que l’acide polylactique (PLA) sont également de plus en plus populaires. De plus, en raison de leur faible coût, de leur facilité de fabrication, de leur polyvalence et de leur résistance à l’eau, les plastiques sont utilisés dans une grande variété de produits et de secteurs, y compris l’impression 3D.
Dans le guide suivant, nous examinerons les plastiques d’impression 3D les plus courants. Comme vous le savez peut-être, le procédé d’impression 3D le plus populaire et le plus abordable, FDM, produit des pièces par extrusion de filaments plastiques. Cependant, la précision sur ces machines n’est pas la même que celle d’autres processus de fabrication additive tels que le SLS ou le SLA. Les plastiques sont souvent utilisés avec cette technologie pour créer des prototypes. Par conséquent, pour les pièces industrielles et d’utilisation finale, les fabricants peuvent décider d’opter pour les technologies SLS (utilisant des poudres plastiques) ou SLA (utilisant des résines plastiques) qui offrent plus de précision et de qualité de pièce. Deux autres technologies qui peuvent imprimer avec des plastiques sont Material Jetting et Multi Jet Fusion.
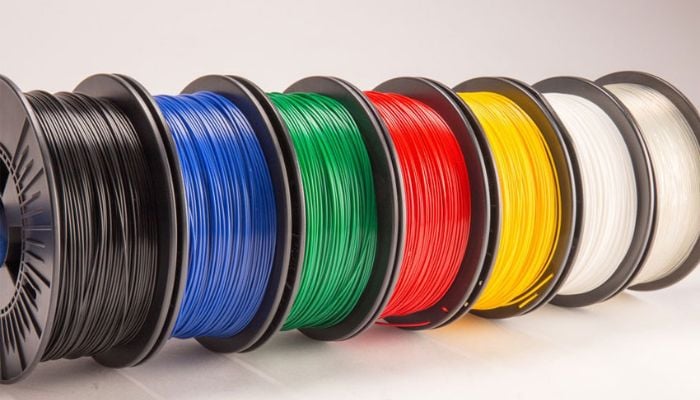
Les filaments plastiques sont disponibles en différentes couleurs (crédits photo : AGRU)
Quels plastiques peuvent être utilisés dans la fabrication additive ? Sous forme de filament ou de poudre, le plastique doit fondre pour former l’objet que vous imprimez couche par couche. Sous forme de résine, il doit se solidifier pour former l’objet. Chaque plastique nécessitera des paramètres d’impression 3D différents pendant le processus de construction et conférera aux pièces des propriétés variables. Dans le guide suivant, nous donnons un aperçu des différents matériaux plastiques utilisables en impression 3D.
ABS
L’acrylonitrile butadiène styrène, ou ABS, est le plastique le plus couramment utilisé dans l’industrie. C’est le matériau phare des briques Lego et il est également largement utilisé dans la carrosserie automobile, les appareils électroménagers et de nombreuses applications de toiture. L’ABS appartient à la famille des thermoplastiques et possède une base élastomère à base de polybutadiène, ce qui le rend plus souple et résistant aux chocs. Le plastique ABS est principalement utilisé dans la technologie des couches fusionnées (FDM) et est donc disponible pour la plupart des imprimantes 3D de bureau. L’ABS est également disponible sous forme de résine, ce qui le rend adapté aux processus SLA ou de projection de matériaux.
Le matériau a une température d’impression comprise entre 230°C et 160°C et peut tolérer des températures très basses (-20°C) et très élevées (80°C). En plus de sa haute résistance, ce matériau offre une surface polie, est réutilisable et peut être soudé par des procédés chimiques (avec de l’acétone). Cependant, il n’est pas biodégradable et rétrécit au contact de l’air, la plateforme de fabrication doit donc être chauffée pendant l’impression. De plus, il est recommandé d’utiliser une imprimante 3D avec une chambre fermée pour limiter les émissions de particules pouvant être libérées lors de l’impression.
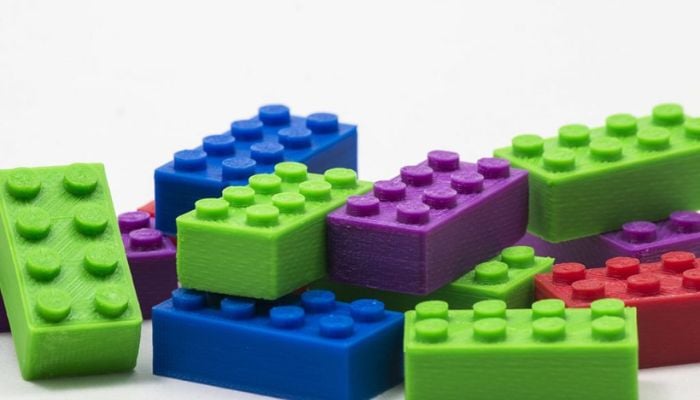
Pièces en ABS (crédits photo : Simplify3D)
PLA
L’acide polylactique ou PLA est biodégradable, contrairement à l’ABS, car il est fabriqué à partir de matières premières renouvelables (amidon de maïs). L’une des propriétés les plus importantes est le faible retrait de l’impression 3D, c’est pourquoi aucun plateau d’impression chauffé n’est nécessaire pendant l’impression. La température d’impression ne doit pas être trop élevée et doit être comprise entre 190°C et 230°C.
Le PLA est difficile à manipuler en raison de sa vitesse de refroidissement et de durcissement élevée. Il peut également être endommagé et décoloré au contact de l’eau. Cependant, ce matériau généralement translucide est utilisé par la plupart des imprimantes 3D FDM et est disponible dans une variété de couleurs.
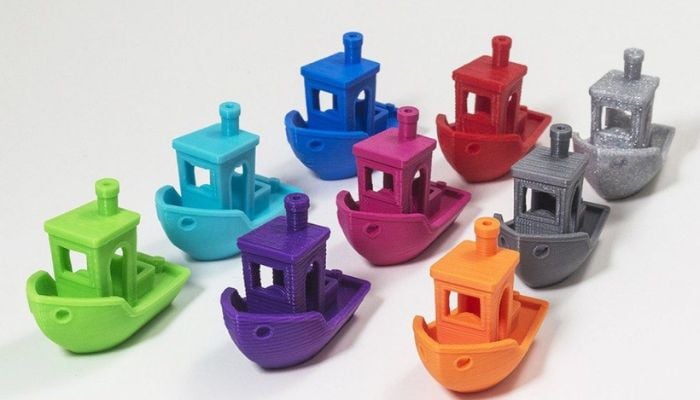
Crédits photos : Simplify3D
ASA
Techniquement connu sous le nom d’acrylonitrile styrène acrylate, ce matériau a des propriétés similaires à l’ABS, mais une meilleure résistance aux rayons UV. Néanmoins, certaines complications peuvent survenir lors de l’impression, c’est pourquoi il est recommandé d’utiliser une plaque chauffante. Les paramètres d’impression sont très similaires à ceux de l’ABS – dans le cas de l’ASA, il faut veiller à utiliser des imprimantes 3D avec des enceintes fermées ou à imprimer à l’extérieur en raison des émissions de styrène. Les pièces qui ont été imprimées avec ASA sont stables et très durables. Pour une description plus détaillée de l’ASA, veuillez consulter notre guide.
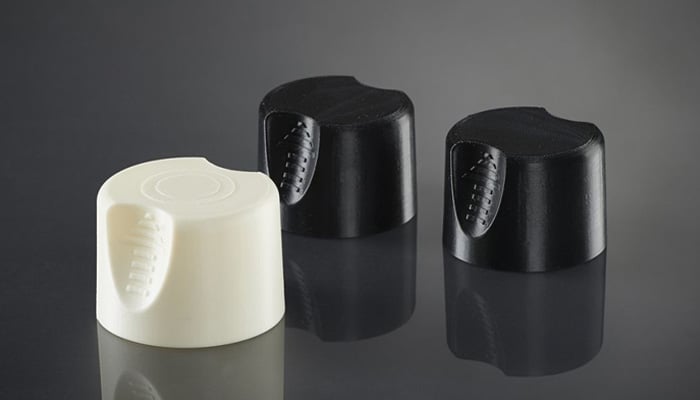
Crédits photo : Stratasys
PET
Le polyéthylène téréphtalate, plus connu sous le nom de PET, se trouve principalement dans les bouteilles en plastique jetables. C’est un filament idéal pour les objets destinés au contact alimentaire. Il est semi-rigide et a une bonne résistance. Pour obtenir les meilleurs résultats d’impression, il est nécessaire d’atteindre des températures de 75°C à 90°C. Principalement commercialisé sous forme de filament translucide, il se décline en différentes variétés telles que PETG, PETE et PETT. C’est aussi un filament qui ne dégage pas d’odeur lors de l’impression et qui est 100% recyclable.
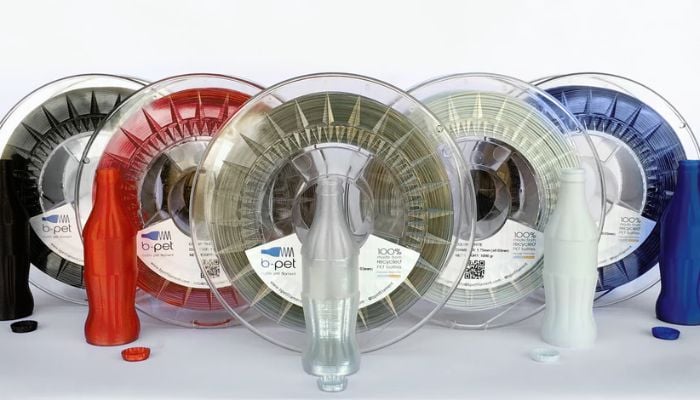
Bouteilles imprimées en 3D à partir de bouteilles PET recyclées (crédits photo : b-Pet)
PETG
Le PETG, ou polyester glycolisé, est un thermoplastique largement utilisé sur le marché de la fabrication additive qui allie à la fois la simplicité de l’impression 3D PLA et la résilience de l’ABS. C’est un plastique amorphe 100% recyclable. Il a la même composition chimique que le polyéthylène téréphtalate, plus connu sous le nom de PET, auquel du glycol a été ajouté pour réduire sa fragilité et donc sa fragilité.
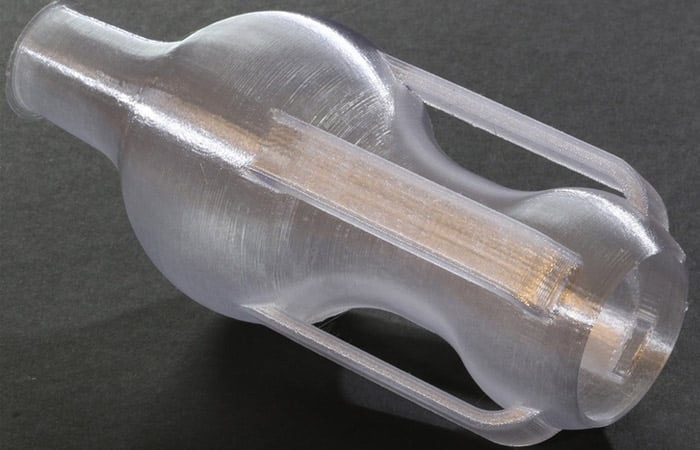
Crédits photos : Taulman3D
Polycarbonate (PC)
Le polycarbonate (PC) est un matériau très résistant développé pour des applications techniques. Ce matériau est capable de supporter des températures élevées jusqu’à 150°C sans se déformer. Le polycarbonate absorbe l’humidité de l’air, ce qui peut affecter les performances et la résistance à la compression. Par conséquent, il doit être stocké dans des boîtes hermétiques. Le PC est particulièrement apprécié dans le monde de la fabrication additive pour sa solidité et sa transparence. Il a une densité beaucoup plus faible que le verre, ce qui le rend particulièrement intéressant pour concevoir des pièces optiquement visibles, des écrans de protection ou des objets décoratifs. Pour des informations détaillées sur PC, veuillez vous référer à notre guide .
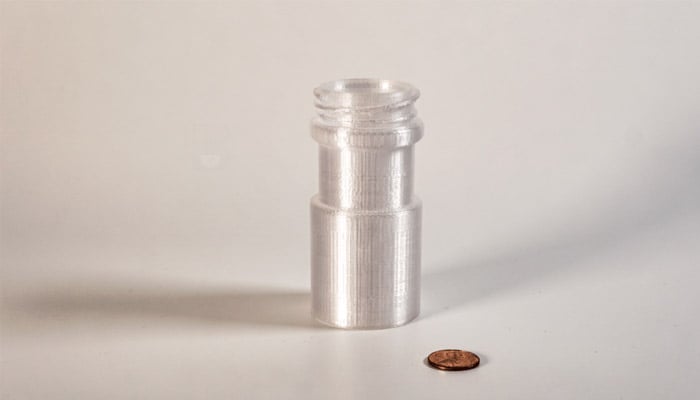
Une pièce imprimée en 3D en polycarbonate (crédits photo : IMC Grupo)
Plastiques hautes performances (PEEK, PEKK, ULTEM)
Le développement progressif des technologies d’impression 3D a conduit à des recherches approfondies sur de nouveaux matériaux d’impression et a entraîné le développement de toute une gamme de filaments hautes performances. Ceux-ci ont des propriétés mécaniques similaires aux métaux. Il existe plusieurs types de plastiques hautes performances pour l’impression 3D comme le PEEK, le PEKK ou l’ULTEM . Ceux-ci appartiennent aux familles des polyaryléthercétones (PAEK) et des polyétherimides (PEI). Entre autres choses, les plastiques nommés se caractérisent par leur très haute résistance mécanique et thermique, tout en étant nettement plus légers que les métaux. Ces propriétés les rendent très attractifs dans les secteurs aéronautique, automobile et médical.
En raison de diverses propriétés, les polymères hautes performances peuvent être imprimés avec un certain nombre d’imprimantes FDM disponibles sur le marché. Cependant, l’imprimante 3D doit avoir une plaque chauffante capable d’atteindre au moins 230°C, ainsi qu’une extrusion à 350°C et une chambre fermée. Aujourd’hui, environ 65% de ces matériaux sont fabriqués à l’aide de la technologie FDM, mais ils sont également disponibles sous forme de poudre compatible avec SLS. Apprenez-en plus dans nos guides sur le PEEK et le PEKK .
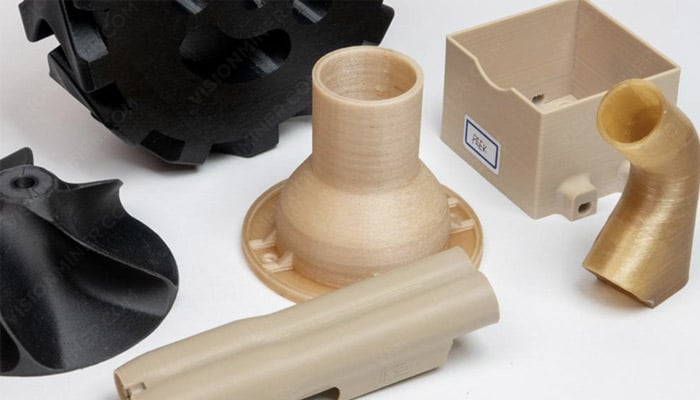
Crédits photo : VisionMiner
Polypropylène (PP)
Le polypropylène est un autre plastique largement utilisé dans le secteur automobile, l’industrie textile et dans la fabrication de centaines d’articles du quotidien. Le PP est connu pour sa résistance à l’usure, sa capacité à absorber les chocs, sa dureté et sa flexibilité relatives. Cependant, les inconvénients du matériau incluent sa faible résistance aux basses températures et sa sensibilité aux rayons UV, qui peuvent provoquer l’expansion du matériau. Pour un résumé plus détaillé du matériel, cliquez ici .
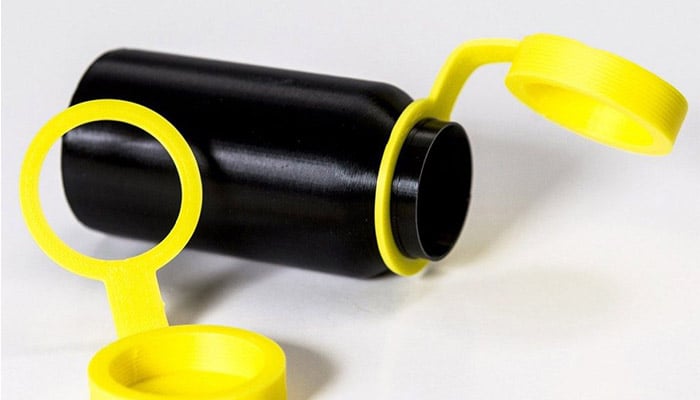
Crédits photos : Simplify3D
Matériaux composites
Les composites sont extrêmement avantageux lorsqu’il s’agit de produire des pièces légères mais solides. Les fibres ajoutent de la résistance à une pièce sans ajouter de poids supplémentaire, c’est pourquoi nous appelons les composites des matériaux renforcés de fibres. Il existe deux types de renforts : fibre courte ou fibre continue. Dans le premier cas, il s’agit de fibres coupées, constituées de segments de moins d’un millimètre de long, qui sont mélangées à des plastiques classiques pour l’impression 3D afin d’augmenter la rigidité et, dans une moindre mesure, la résistance des pièces. Les fibres coupées peuvent être mélangées avec des thermoplastiques tels que le nylon, l’ABS ou le PLA. Alternativement, les fibres peuvent être ajoutées aux thermoplastiques pour créer une pièce plus solide. La principale fibre utilisée dans l’impression 3D est la fibre de carbone, mais il existe d’autres fibres comme la fibre de verre ou le Kevlar. Avec fibre continue, les fibres sont intactes. Pour plus d’informations, voir notre guide .
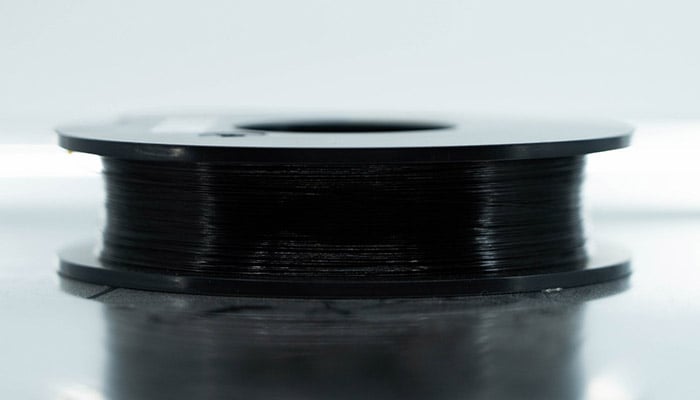
Crédits photo : Markforged
Matériaux hybrides
Il existe différents types de matériaux qui mélangent une base, comme le PLA, avec une poudre qui leur donne une couleur ou une surface différente. Ce sont essentiellement des filaments qui sont généralement composés à 70% de PLA et à 30% de matériau hybride. Sur le marché actuel, nous trouvons des filaments en bambou, liège, bois et plus encore. La présence de ces matériaux confère au filament une structure finale plus organique. De plus, il existe des machines qui utilisent la technologie FDM comme base pour extruder le métal. Par exemple, les sociétés Colorfabb ou BASF proposent du filament métallique 3D. Cela donne aux objets imprimés en 3D une couleur différente selon le métal choisi : cuivre, bronze, argent et bien d’autres couleurs.
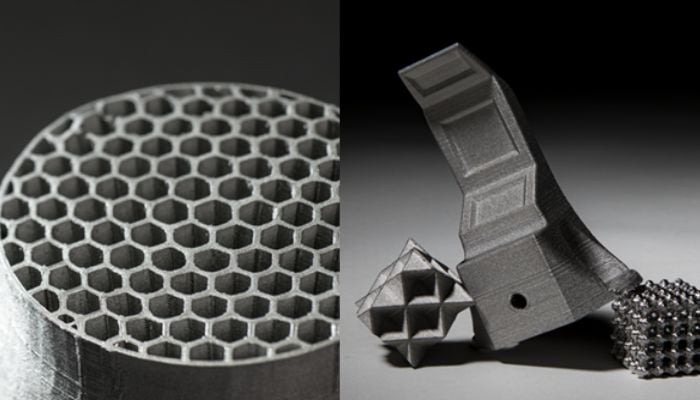
Crédits photos : BASF
Matériaux solubles
Les matériaux solubles sont des matériaux qui sont imprimés avec l’intention d’être dissous à une étape ultérieure du processus de fabrication. Les deux matériaux de filaments solubles les plus courants sont le HIPS (polystyrène à fort impact) et le PVA (acétate de polyvinyle). Le HIPS a des propriétés similaires à celles de l’ABS et peut être dissous avec du limonène, tandis que le PVA peut être dissous avec de l’eau (jusqu’à 70 °C). Il existe également des filaments BVOH qui deviennent de plus en plus populaires, en particulier dans les imprimantes à double extrudeur. En effet, le matériau est soluble dans l’eau et, selon les experts, a une solubilité encore plus élevée que le PVA.
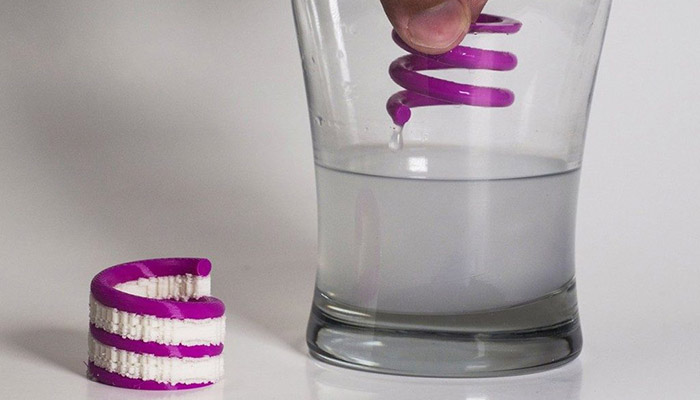
Crédits photo : Simplify3D
Matériaux flexibles
Les filaments plastiques souples sont également de plus en plus populaires sur le marché de l’impression 3D. Constitués de matériaux comme le TPE ou le TPU, ces matériaux, l’avantage de ces filaments est qu’ils sont capables de réaliser des pièces malléables. En général, ces plastiques ont les mêmes propriétés d’impression que le PLA mais avec des degrés de rigidité différents. Il est recommandé de vérifier la compatibilité du matériau avec l’extrudeur pour éviter de boucher la buse.
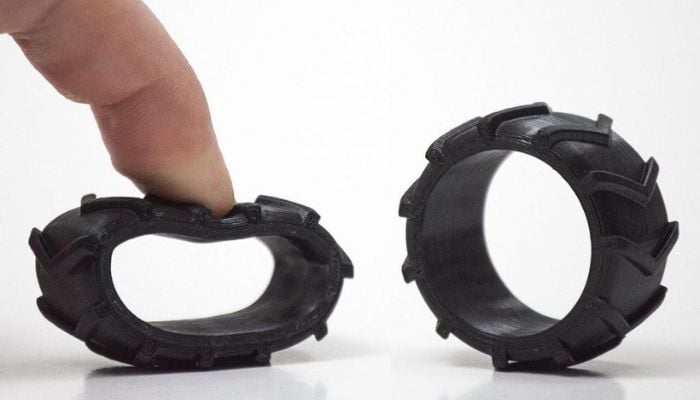
Crédits photos : Simplify3D
Polyamide (PA)
Les objets en polyamide sont généralement fabriqués à partir d’une poudre fine, blanche et granuleuse à l’aide de la technologie SLS. Cependant, certaines variantes du matériau sont également disponibles en filaments pour la modélisation par dépôt de fil fondu (FDM). Du fait de sa bonne biocompatibilité, les polyamides peuvent être utilisés pour réaliser des pièces en contact avec des aliments (sauf aliments contenant de l’alcool).
Les polyamides sont constitués de structures semi-cristallines et présentent un bon équilibre de propriétés chimiques et mécaniques, offrant une bonne stabilité, rigidité, flexibilité et résistance aux chocs. Ces avantages signifient que le matériau a de nombreuses applications intersectorielles et offre un haut niveau de détail. En raison de leur haute qualité, les polyamides sont utilisés dans la fabrication d’engrenages, de pièces pour l’aérospatiale, l’automobile, la robotique, les prothèses médicales et les moules à injection.

Crédits photos : Sculpteo
Alumide
Les objets en alumide sont produits par le procédé SLS à partir d’une combinaison de polyamides et de poudre d’aluminium. Le matériau a une surface légèrement poreuse et un aspect granuleux avec une grande résistance et une bonne résistance à la température (jusqu’à 172 °C). Cependant, lors de l’utilisation d’Alumide, certains post-traitements sont nécessaires, tels que le meulage, le revêtement ou le fraisage. L’alumide est utilisé pour des modèles complexes, des pièces de design ou pour la production en petite série de modèles fonctionnels qui nécessitent une grande rigidité et un aspect similaire à l’aluminium. Il y a peu de limites géométriques à cette technique.
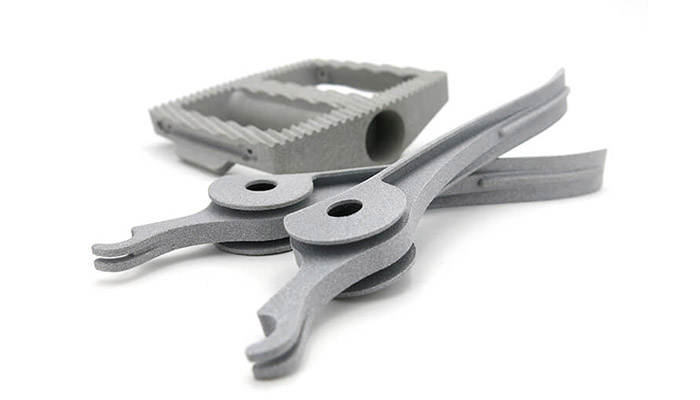
Crédits photos : Sculpteo
Quels plastiques avez-vous déjà utilisés pour l’impression 3D ? Partagez votre avis dans les commentaires de l’article. Retrouvez toutes nos vidéos sur notre chaîne YouTube ou suivez-nous sur Facebook ou Twitter !
Article très intéressant. Je vais de ce clique, voir la deuxième partie ! 🙂
Excellent article.
Merci beaucoup!
ok dacc
Merci pour cet article très instructif. Cependant vous ne faites pas mention du plastique PET, que l’on trouve également en bobine. Il serait intéressant de faire un topo sur ce type de plastique également utilisé par certaines machines 3D.
Très bon article, je confirme que l’ajout des PET serait un plus 😉
lol
Bonjour,
Pourquoi avoir différencié le nylon du polyamide? Le nylon est le nom usuel du polyamide, il n’y a donc pas d’intérêt de les différencier.
Le Nylon est UN polyamide, mais la famille est grande 😉
Bonjour,
Pensez vous qu’une imprimante 3D peut être utilisée pour des accessoires à placer sur des gâteaux type personnages de dessin animé, lettres etc… Si oui, quel matériel serait optimal.
Quelle est la finesse de détail d’une imprimante moyenne actuelle ?
peut on faire un design contenant un pas de visse fin ?
Jay, pour les pas de vis, imho il est plus intéressant de prévoir une sur-épaisseur et de tarauder ensuite, ce qui donnera une qualité bien meilleure
Bonjour, j’aimerais savoir comment calculer le coût pour imprimer un sujet que l’on a réalisé sur ordi? Donc un objet imaginé, dessiné sur un logiciel et que l’on veut matérialiser. Est-ce que ma question est claire? 😉
Salut ! Le coût de l’impression 3D se calcule facilement. Une fois que vous avez modélisé votre pièce sur votre logiciel de conception, vous pouvez obtenir sa densité et la multiplier par le coût du matériau utilisé. Bien sur cette technique ne prend pas en compte la consommation électrique du printer =)
Bonjour,
Je voudrais fabriquer des guides-langue (tiges avec embouts de différentes formes pour aider la langue à articuler certains sons) : il me faut un matériau non toxique, mais également possible à stériliser (matériel non invasif = une stérilisation simple, type tétine de biberon, suffit), il faut donc aussi un matériau qui supporte la chaleur. Que me conseilleriez-vous? On peut aussi envisager un matériau qui supporte une stérilisation chimique.
Le Frittage de poudre polyamide sert à faire des prothèses (orthèses dentaires) pour les personnes souffrant d’apnée du sommeil (prothèse que l’on met dans la bouche avant de dormir) à voir.
La température de fusion est aux alentours de 178° et le ramollissement, de 100° (je crois). A voir…
bonjour j ai un doute sur le polyamide je ne pense pas qu’il sois compatible a un usage alimentaire c est un plastique toxique que relâche des particule au lavage personnellement je n irait pas le mètre dans ma bouche ou alors des traitement son peut être possible mais c est hors de mes compétence
je pense qu’il serrait mieux d utiliser du PETG ou un dériver c est la famille des plastique de bouteille,ca résiste a des agression acide( coca par exemple même le jus d orange et est alimentaire
Bonjour, Merci pour ce super articles. Je cherche à réaliser des objets antichoc avec des caractéristique proche du caoutchouc. Il telle matière existe-t-elle pour les imprimantes 3D ?
Bonjour,
depuis 2 ans maintenant, j’utilise avec succès 2 matériaux qui ne sont pas du tout évoqués dans l’article. Le PET pour ses très bonnes propriétés mécaniques (bien meilleures que l’ABS et le PLA) et sa facilité d’impression (pas de wrapping) et le PU pour les pièces flexibles qui devrait être pouvoir se substituer au caoutchouc.
bonjour,
quelle machine utilisez vous ? vous parlez de pet , vous utilisez une extrudeuse ou vous achetez le PET directement ? d’avance merci !
Bonjour,
Merci pour votre article. Est-il possible d’obtenir les caractéristiques mécaniques des différents matériaux que vous présentez (dureté, module d’élasticité, résistance à la traction,…). D’ores et déjà merci pour votre retour.
FC
Bonjour,
Je cherche à imprimer en 3D des fleurs. Il faut qu’elles soient imprimées en blanc et que ce blanc ne jaunisse pas.
J’ai déjà fait un essai en impression frittage en nylon PA 12, mais cela a jaunit très vite même à l’abri de la lumière. Il y a le traitement chimique de surface mais cela ne fait, il semble, que ralentir le processus de jaunissement. Quelle technique et matière je peux employer pour avoir ces fleurs en un blanc durable?
Merci par avance si quelqu’un a une réponse à mes questions.