Unilever e Serioplast utilizzano la stampa 3D per produrre flaconi di plastica
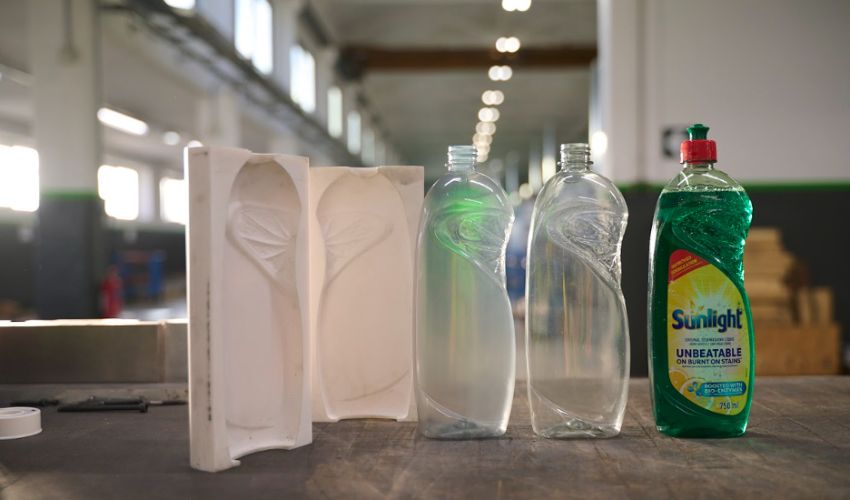
Un settore meno discusso in cui abbiamo assistito alla crescita della stampa 3D negli ultimi anni è quello del packaging. Con un mercato valutato a 1,21 miliardi di dollari nel 2023, secondo Future Market Insights, negli ultimi anni abbiamo visto sempre più grandi nomi, tra cui L’Oréal o Pepsi, utilizzare la produzione additiva. Anche la multinazionale Unilever, ha utilizzato la stampa 3D in resina di Formlabs per realizzare stampi per flaconi di plastica.
Se il nome Unilever non vi è familiare, basti pensare che si tratta di una delle più grandi aziende al mondo produttrice di beni di consumo: prodotti per l’uso quotidiano, dalla cura della persona a quella della casa, all’alimentazione e molto altro ancora. Per citare soltanto alcuni dei marchi prodotti da Unilever pensiamo a Svelto, Magnum, Dove, Knorr ecc. con prodotti disponibili in oltre 190 Paesi. Tuttavia, il settore dei beni di largo consumo è caratterizzato da un’agguerrita concorrenza e quindi Unilever è costantemente alla ricerca di modi per innovare, tra cui l’ultima mossa di utilizzare la stampa 3D per i flaconi in plastica.
Per fare questo l’azienda ha collaborato con Serioplast Global Services, una delle principali aziende partner di Unilever. Serioplast, fondata a Seriate, in provincia di Bergamo, nel 1974, e ora attiva a livello globale, è un’azienda che produce packaging rigido in plastica per i più importanti player del mercato dei beni di largo consumo.
Stefano Cademartiri, CAD & Prototyping Owner di Unilever, spiega: “Un’azienda di beni di largo consumo come Unilever deve essere sul mercato il prima possibile o prima dei suoi concorrenti. È necessario offrire ai consumatori il miglior prodotto al miglior prezzo nel più breve tempo possibile. La stampa 3D ci aiuta a velocizzare questo processo“.
La stampa 3D per produrre imballaggi di plastica
Tradizionalmente, la produzione di un semplice flacone di plastica richiede molto più tempo di quanto si possa immaginare. Progettazione al prodotto, realizzazione degli stampi e produzione, tramite combinazioni di iniezione, stiro e soffiaggio, spesso richiedono mesi. Gli stampi sono tradizionalmente realizzati in metallo mediante lavorazione meccanica CNC, che richiede attrezzature specializzate, software CAM e manodopera qualificata. La produzione di attrezzature pilota in metallo è generalmente esternalizzata e prevede tempi di realizzazione di quattro-otto settimane e costi che vanno da 2.000 a più di 20.000 €, a seconda della complessità della parte.
Integrando la stampa 3D nel processo, i tempi si riducono drasticamente, poiché uno stampo stampato in 3D può essere completato in soli due giorni, portando i test pilota a sole due settimane, il tutto con costi significativamente inferiori. Flavio Migliarelli, R&D Design Manager di Serioplast Global Services, spiega ancora: “Con lo stampo stampato in 3D, possiamo risparmiare fino al 70% di tempo e al 90% di costi rispetto allo stampo standard. In passato, [i clienti] dovevano aspettare fino a 12 settimane solo per un progetto, ora possiamo realizzarne cinque”.
In questo caso la stampa 3D viene dunque utilizzata in aggiunta a metodi tradizionali. Più precisamente, gli stampi sono prodotti con la stampante 3D Form 3L di Formlabs e la resina Rigid 10K, che consente di ottenere stampi precisi con una finitura superficiale liscia. L’uso della tecnologia SLA ha anche aiutato Unilever e Serioplast a integrare più dettagli nelle bottiglie, con loghi e altri dettagli fini.
Dopo la creazione dello stampo, le bottiglie vengono realizzate mediante iniezione (IM), stiro e soffiaggio (SBM), estrusione e soffiaggio (EBM). La tecnologia SBM, è ad esempio, comunemente utilizzata per produrre contenitori in PET trasparenti di alta qualità, come le bottiglie d’acqua.
Serioplast ha testato circa 15 diversi modelli di flaconi, lavorando su due o tre iterazioni di design per ciascuno di essi. Con un solo stampo realizzato in 3D con la Rigid 10K Resin sono state prodotte circa 200 unità senza compromettere lo stampo. La qualità generale dei flaconi ottenuta è paragonabile dal punto di vista estetico e funzionale a quella di una produzione standard, tanto da poter essere sottoposti a test di consumo. “La competenza del team unita alla tecnologia di stampa 3D Formlabs ci ha permesso di mettere a punto una soluzione per la produzione industriale su misura per soddisfare le richieste del cliente”, ha concluso Mirco Paltrinieri, Formlabs Brand Manager di SolidManufacturing.
Cosa ne pensi dell’utilizzo della stampa 3D di Unilever e Serioplast per produrre flaconi di plastica? Condividi la tua opinione sui nostri social Facebook e LinkedIn. Trovi tutti i nostri video sul nostro canale YouTube! Non dimenticare di iscriverti alla nostra Newsletter settimanale per ricevere tutte le notizie sulla stampa 3D direttamente nella casella di posta!
*Crediti per tutte le foto: Formlabs