Titanio vs alluminio: quale metallo scegliere per la stampa 3D?
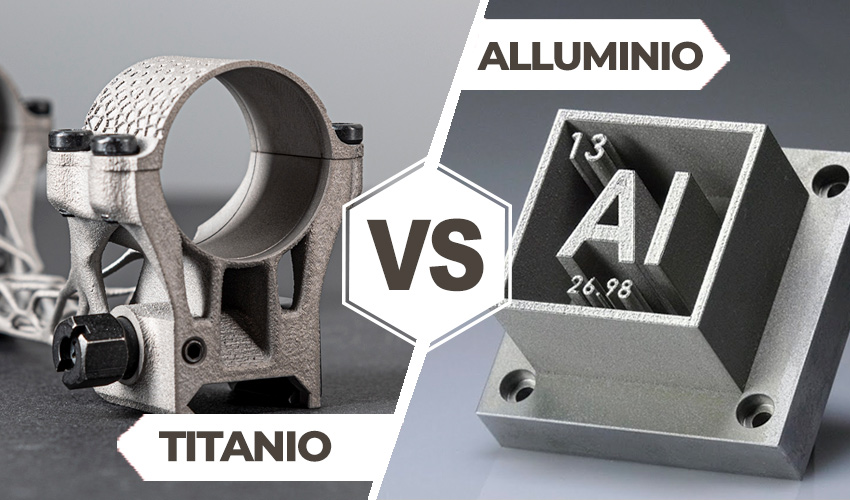
Il metallo è attualmente uno dei materiali più utilizzati nei processi di produzione additiva, insieme alla plastica. Non sorprende che le sue eccellenti proprietà lo rendano la scelta ideale per le applicazioni più esigenti in termini di prestazioni e resistenza. In questo articolo ci concentreremo su due dei principali metalli utilizzati nella stampa 3D: il titanio e l’alluminio. Questi ultimi sono utilizzati principalmente per processi come la Laser Powder Bed Fusion (L-PBF) o la Direct Energy Deposition (DED). Sono disponibili principalmente in forma di polvere per diversi settori industriali. Confronteremo le loro somiglianze e differenze, per avere una visione più approfondita delle loro proprietà e applicazioni e per comprendere i vantaggi che offrono all’interno dei processi di produzione additiva.
Produzione e caratteristiche
Titanio
Il titanio è un materiale metallico che non si trova in natura come elemento e deve essere estratto da minerali come il rutilo (TiO2) o l’ilmenite (FeTiO3). L’estrazione del titanio puro è un processo complesso che prevede diverse fasi. Il metodo più utilizzato per la produzione di titanio puro è il processo Kroll, sviluppato dal chimico americano William J. Kroll nel 1940. Questo metodo prevede la riduzione del biossido di titanio (TiO2) con cloro gassoso (Cl2) per produrre tetracloruro di titanio (TiCl4), che viene poi ridotto con magnesio (Mg) per produrre titanio metallico. Sebbene il processo Kroll sia efficace per produrre titanio puro, è un processo costoso che richiede una grande quantità di energia. Inoltre, l’elevata reattività del titanio lo rende difficile da ottenere come metallo puro, per cui un campione con una purezza del 99,9% è classificato come titanio commercialmente puro. Per questo motivo, viene normalmente utilizzato in combinazione con altri elementi per formare una lega.
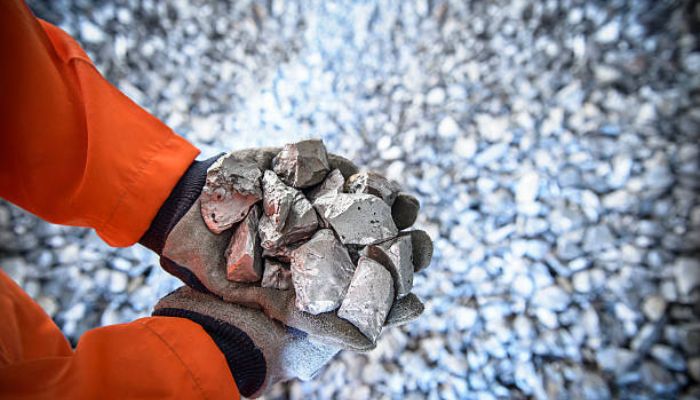
Crediti: Getty Images
Il titanio ha molte proprietà che lo rendono estremamente versatile e utile in molti settori. Di solito viene utilizzato in combinazione con altri elementi per formare una lega perché la sua elevata reattività lo rende difficile da ottenere come metallo puro, invece il titanio estratto puro viene utilizzato, ad esempio, in applicazioni mediche grazie alla sua elevata biocompatibilità. Le sue caratteristiche principali sono l’elevata resistenza meccanica, la bassa densità, l’eccellente resistenza alla corrosione e la rigidità.
Le leghe di titanio più importanti utilizzate nella stampa 3D sono le seguenti:
- Titanio 6Al-4V, grado 5: è la più importante e comune. Viene utilizzata nella stampa 3D per la sua elevata resistenza e durata. La lega è composta da titanio, alluminio e vanadio e può resistere alle alte temperature e agli ambienti corrosivi.
- Titanio 6Al-4V, grado 23: è biocompatibile e quindi comunemente utilizzato per impianti medici e protesi.
- Titanio Beta 21S: ha una forza maggiore rispetto alle leghe di titanio convenzionali ed è anche più resistente all’ossidazione e alla deformazione. È perfetto per gli impianti ortopedici e per le applicazioni nei motori aerospaziali. Il beta titanio è ampiamente utilizzato in ortodonzia.
- Cp-Ti (titanio puro), grado 1, 2: utilizzato nell’industria medica per un’ampia gamma di applicazioni grazie alla biocompatibilità del titanio con il corpo umano.
- TA15: è quasi interamente in titanio, ma con l’aggiunta di alluminio e zirconio. I componenti realizzati con questa lega sono molto forti e resistenti alle alte temperature, il che li rende ideali per la costruzione di parti robuste di aerei e motori. Sono anche piuttosto leggeri rispetto alla loro forza.
Alluminio
L’alluminio è un metallo con un ottimo compromesso tra leggerezza e resistenza. Oltre a essere resistente alla corrosione, è anche saldabile. Si trova raramente allo stato puro e più spesso in lega con altri metalli che ne migliorano le proprietà fisiche e meccaniche, come il silicio e il magnesio. Come per il titanio, due processi industriali consecutivi possono essere utilizzati per ottenere il materiale in forma pura. Nel primo processo, chiamato processo Bayer, l’ossido di alluminio si ottiene dal minerale di bauxite. Il minerale viene lavato e frantumato, sciolto in soda caustica e filtrato per ottenere idrossido di alluminio puro. Viene quindi riscaldato per ottenere polvere di ossido di alluminio. Nel secondo processo, chiamato processo Hall-Héroult, si procede alla riduzione elettrolitica dell’ossido di alluminio per ottenere alluminio puro. La maggior parte degli impianti di lavorazione viene costruita vicino alle miniere per ridurre i costi di trasporto del minerale.
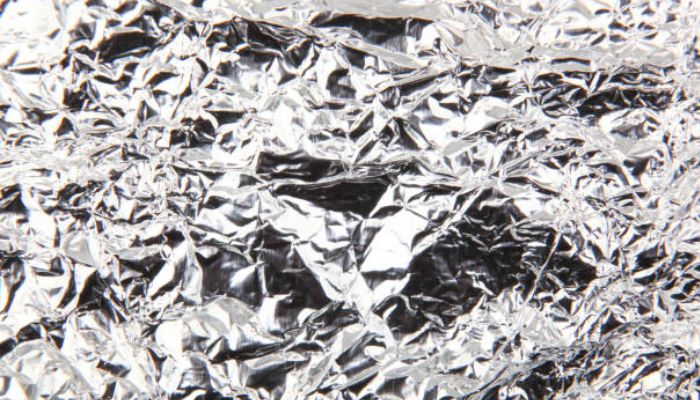
Crediti: Getty Images
Come già detto, le leghe di alluminio sono più comuni della forma pura e vengono utilizzate in molte applicazioni industriali. Inoltre, hanno un ottimo rapporto forza-peso e un’ottima resistenza alla fatica e alla corrosione. Tra le proprietà dell’alluminio ci sono anche l’elevata riciclabilità, la conducibilità termica ed elettrica e la bassa tossicità.
Le leghe più importanti utilizzate nella stampa 3D in alluminio sono:
- AISi10Mg: è la lega più comune formata da silicio e magnesio. Consente la fabbricazione di parti solide e complesse e viene utilizzata per creare vari oggetti come alloggiamenti, parti di motori e strumenti di produzione.
- Al2139: è la lega di alluminio più resistente creata dall’azienda tedesca EOS. È ideale per settori come quello automobilistico grazie alla sua leggerezza, forza e resistenza chimica ed è stata utilizzata da organizzazioni come l’aeronautica militare statunitense, Mercedes-Benz e Airbus. L’aspetto interessante di questo materiale è che è stato progettato specificamente per la produzione additiva e supera molte altre leghe presenti sul mercato.
- Serie Al 7000: una famosa serie di leghe in polvere, con elevata resistenza alla trazione e alle basse temperature.
- Al 6061 e Al 7075: recentemente i produttori di 3D stanno ottenendo ottimi risultati utilizzando queste due leghe, la 6061 ha una resistenza alla trazione e una durezza inferiori rispetto alla 7075. D’altra parte, il 7075 ha una migliore resistenza agli urti e una minore deformazione rispetto all’alluminio 6061.
- A201.1: fa parte della serie 200 di leghe rame-alluminio, note per essere molto resistenti. Tuttavia, sono difficili da fondere. Queste leghe sono consigliate per le applicazioni in cui il rapporto resistenza/peso è fondamentale, come nel settore dei trasporti e in quello aerospaziale.
Quali sono le differenze tra i due metalli?
L’alluminio e il titanio sono due metalli molto diversi tra loro, utilizzati in un’ampia gamma di applicazioni e per decidere tra i due è necessario tenere conto delle differenze nelle loro proprietà e dell’applicazione finale.
In termini di rapporto resistenza/peso, il titanio è la scelta ideale quando sono necessarie un’elevata resistenza e robustezza, motivo per cui viene utilizzato nei componenti medicali o addirittura nei componenti satellitari. D’altra parte, sebbene l’alluminio sia meno resistente del titanio, è molto più leggero e conveniente. Per quanto riguarda le proprietà termiche, l’alluminio è perfetto per le applicazioni che richiedono un’elevata conduttività termica. Il titanio, invece, è ideale per le applicazioni in ambienti ad alta temperatura, grazie al suo elevato punto di fusione, come i componenti dei motori aerospaziali. Sia l’alluminio che il titanio hanno un’eccellente resistenza alla corrosione. Tuttavia, il titanio è più biocompatibile dell’alluminio, motivo per cui è ampiamente utilizzato nel settore medico.
Forma del materiale e tecnologie 3D utilizzate
Forma
Nella maggior parte dei casi, il titanio e l’alluminio si presentano sotto forma di polvere, anche se possono essere disponibili anche sotto forma di filo, come il filamento di titanio o di alluminio di Virtual Foundry o di Nanoe con la sua offerta Zetamix.
Per stampare parti in 3D con questi metalli, è necessario ottenere la polvere, che si ottiene con due tecniche principali: atomizzazione al plasma o atomizzazione a gas. L’atomizzazione al plasma (gas ionizzato) è un processo che utilizza temperature elevate, una fonte di energia e calore, un mezzo inerte come l’argon e velocità elevate per atomizzare il metallo. Questo processo produce polveri di alta qualità resistenti all’usura. L’atomizzazione a gas, invece, utilizza aria, argon o elio come gas per frammentare un flusso di materiale fuso. È un processo molto efficiente ed è ampiamente utilizzato per produrre polveri metalliche fini e sferiche. La tecnica utilizzata per produrre la polvere metallica è importante, in quanto influenza ovviamente le proprietà finali del pezzo.
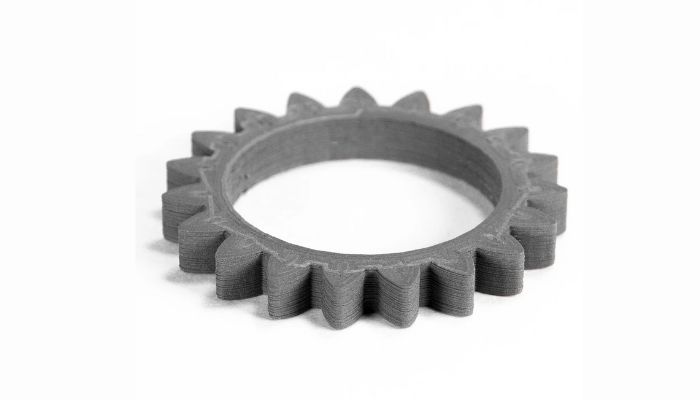
Ingranaggio realizzato con titanio 64-5 non sinterizzato. Crediti: SAPPHIRE3D
Tecnologie 3D utilizzate
Per lavorare con il titanio nella stampa 3D, è possibile utilizzare un gran numero di tecnologie metalliche, come L-PBF, DED o Binder Jetting. Per i processi relativi all’alluminio, oltre a quelli già citati, è utilizzato anche il Cold Spray.
Nei processi di manifattura additiva L-PBF, il raggio laser viene utilizzato per riscaldare il metallo in polvere, strato per strato, fino al suo punto di fusione per costruire l’oggetto. Il titanio fonde a temperature molto elevate (1600°C), quindi i comportamenti termici e meccanici del materiale dovranno essere analizzati prima della stampa 3D. La temperatura di fusione dell’alluminio è molto più bassa, circa 630°C, ma l’alluminio ha un’alta riflettività e un’alta conducibilità termica per il processo. Un’altra cosa interessante della produzione additiva con l’alluminio è che forma uno strato di ossido naturale, cosa che altri metalli fanno più tardi sui loro bordi. Questo strato sottile rallenta il processo.
Per quanto riguarda il processo DED è molto simile al precedente, ma in questo caso il materiale viene fuso nello stesso momento in cui viene depositato dall’ugello e si può trovare sotto forma di polvere o filo. Normalmente questa tecnologia consente di ottenere una maggiore velocità di produzione e un costo inferiore per unità di volume.
Nel caso del binder jetting, il materiale è in polvere e non viene fuso, ma per far aderire le particelle tra loro, un legante viene spruzzato sullo strato in punti specifici mediante una testina di stampa. Dopo la stampa è necessaria anche una fase di sinterizzazione. Usciti dalla stampante 3D, i pezzi sono molto fragili e porosi e dovranno essere trattati termicamente per ottenere le proprietà meccaniche finali.
Anche nel Cold Spray troviamo il materiale metallico in polvere, ma poiché in questo caso non è necessario fonderlo o fonderlo, quando si spruzza a freddo si può evitare la distorsione termica e non è necessaria un’atmosfera protettiva.
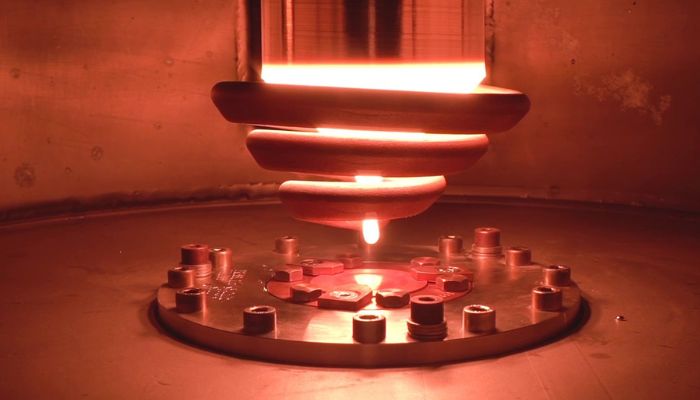
Crediti: Sandvik
Post-processing
Per ottenere un risultato ottimale, è fondamentale applicare un processo di post-processing ai pezzi. Non ci sono differenze specifiche nella post-lavorazione del titanio e dell’alluminio, quindi i passaggi seguenti si applicano a entrambi i materiali. Poiché il titanio e l’alluminio sono spesso utilizzati in applicazioni soggette a sollecitazioni meccaniche, la granigliatura e la pallinatura sono molto utili. Nel primo metodo, piccole sfere metalliche o ceramiche vengono sabbiate contro la superficie del pezzo per creare una deformazione controllata nello strato superficiale del pezzo. Ciò migliora l’adesione dei rivestimenti successivi e riduce, tra l’altro, la probabilità di crepe e fratture. La pallinatura rimuove solo lo strato superiore del materiale, il che può migliorare l’aspetto estetico del pezzo, rimuovere lo sporco e la corrosione e preparare la superficie per i rivestimenti successivi.
Un’altra opzione è quella di combinare la stampa dei metalli con i metodi di produzione tradizionali. La lavorazione CNC è un processo di post-lavorazione adatto a questo scopo, in quanto garantisce tolleranze strette e la finitura superficiale desiderata. Soprattutto con la tecnologia DED, i pezzi grezzi hanno una superficie molto ruvida perché il metallo viene fuso direttamente durante il processo di estrusione. Pertanto, la lavorazione CNC è sempre necessaria per ottenere una superficie liscia e definita.
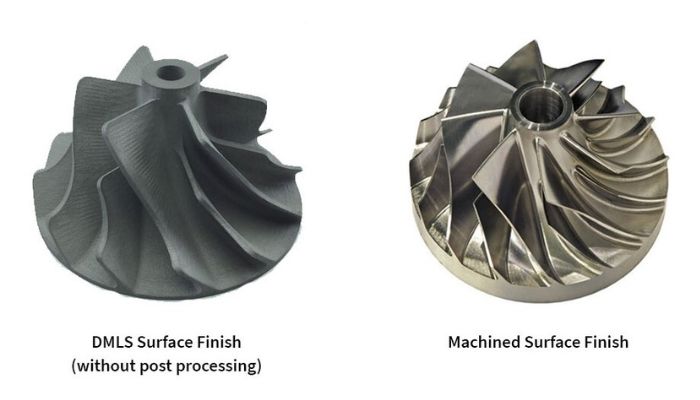
Crediti: FacFox
La ricottura è un’opzione di trattamento termico che prevede il riscaldamento della parte stampata ad alta temperatura e il suo rapido raffreddamento per modificare la microstruttura, migliorando la duttilità del materiale, cioè la sua capacità di deformarsi sotto carico prima di rompersi. In generale, con questo processo si ottengono proprietà meccaniche migliori, utilizzate soprattutto per le parti in alluminio.
La sinterizzazione è necessaria anche per l’alluminio e il titanio quando vengono utilizzati nei cosiddetti processi di stampa 3D indiretta, come la FDM o binder jetting. Dopo la fase di stampa, le parti devono essere sottoposte a un processo di debinding per separare i polimeri dal legante metallico. Le parti vengono quindi riscaldate a una certa temperatura in un forno di sinterizzazione, appena al di sotto della temperatura di fusione, che consoliderà l’oggetto finale. In questo modo si ottengono pezzi con una porosità molto bassa, poiché le cavità in cui si trovava il legante vengono chiuse durante il processo, provocando una compressione.
Applicazioni
L’industria aerospaziale ha trovato grandi vantaggi nell’uso della manifattura additiva del titanio. Il titanio è un materiale ideale per la produzione di componenti aeronautici, come i motori a reazione e le turbine a gas, in quanto può ridurre significativamente il peso di strutture altamente sollecitate. Un esempio dell’applicazione del titanio nella produzione additiva è la partnership di Boeing con Norsk Titanium per la produzione di grandi componenti strutturali per il 787 Dreamliner. La tecnologia utilizzata in questo processo è la DED. Questo processo è da 50 a 100 volte più veloce dei sistemi a polvere e utilizza dal 25 al 50% di titanio in meno rispetto alla forgiatura, con un risparmio fino a 3 milioni di dollari per aereo.
Se il titanio è attualmente più utilizzato nell’esplorazione spaziale con la stampa 3D, l’applicazione dell’alluminio nell’industria è aumentata. Ad esempio, Boeing produce parti stampate in 3D da leghe di alluminio che vengono rivestite con nanoparticelle durante la fase di raffreddamento. In questo modo è possibile saldare una lega di alluminio estremamente resistente senza incrinature a caldo. I telai fabbricati sono molto più leggeri, consentendo all’aereo di utilizzare il carburante in modo efficiente e di volare per distanze più lunghe con la stessa quantità di carburante.
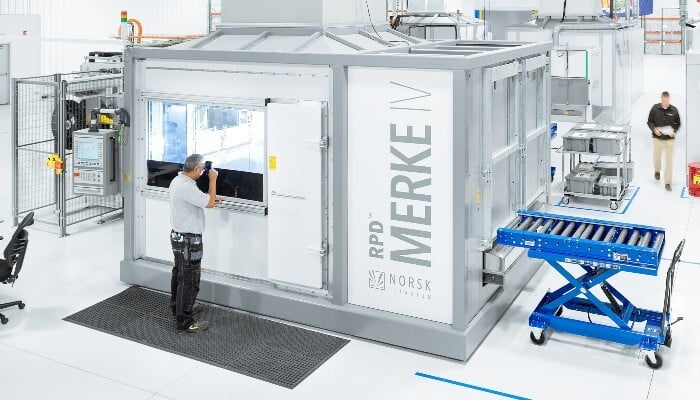
Questa macchina produce parti per il Boeing 787. Crediti: Norsk Titanium
Per quanto riguarda il settore automobilistico, sebbene il prezzo elevato del titanio possa rappresentare un ostacolo al suo impiego, potremmo assistere a un aumento del suo utilizzo in questo settore, soprattutto nel segmento del lusso. Attualmente la stampa 3D viene utilizzata per creare parti in cui il rapporto peso-prestazioni è fondamentale. Ad esempio, Bugatti ha stampato in sole 45 ore la pinza dei freni del suo sistema frenante in titanio con la tecnologia SLM, che si dice sia più leggera del 40% rispetto a una pinza dei freni in alluminio fresata in modo tradizionale. Nonostante la leggerezza, la parte in titanio garantisce anche elasticità e resistenza alle alte temperature. L’alluminio, invece, è più comune nell’industria automobilistica. Porsche ha utilizzato la stampa 3D per creare pistoni in alluminio ad alte prestazioni per il suo modello di punta 911, la GT2 RS. Grazie a questa tecnologia, il motore biturbo da 700 CV può ottenere fino a 30 CV in più di potenza e migliorare l’efficienza. Inoltre, nel 2020 Porsche ha prodotto un alloggiamento stampato in 3D interamente in alluminio per un’unità elettrica che ha superato tutti i test di qualità e di carico dell’azienda.
Il titanio è, inoltre, un materiale molto interessante nell’industria medica grazie alla sua elevata forza e resistenza alla corrosione, nonché alla sua biocompatibilità, che lo rende ideale per gli impianti ortopedici e dentali. La stampa 3D consente di creare strutture porose che imitano la struttura dell’osso, contribuendo alla rapida guarigione e alla crescita di ossa e tessuti. TrabTech, in Turchia, produce impianti trabecolari, come un’anca, utilizzando il titanio. D’altra parte, l’uso dell’alluminio è meno comune nell’industria medica rispetto al titanio, ma può essere utilizzato per applicazioni ortopediche e dentali.
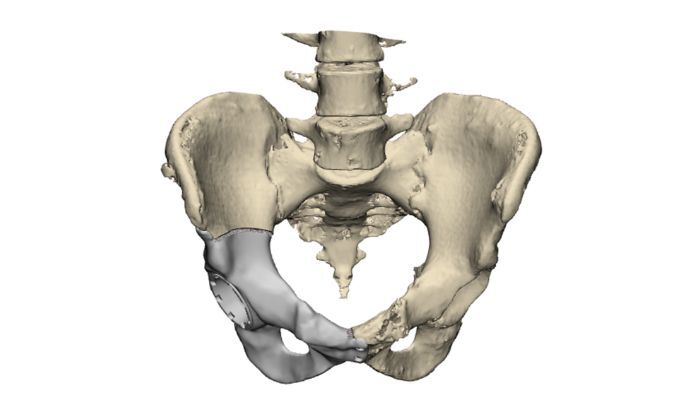
TrabTech produce impianti trabecolari in titanio. Crediti: TrabTech
Prezzo e produttori
Un limite del titanio potrebbe essere il suo prezzo elevato. Secondo il Wohlers Report 2021, la polvere di lega di titanio Ti-6AI-4V o titanio puro di grado 2 costa circa 363 dollari al chilogrammo, collocandosi in uno dei segmenti di prezzo più alti. Al contrario, l’alluminio è notevolmente più economico, con la lega di alluminio AISi7 disponibile a 94 dollari al chilogrammo di polvere e l’AISi10Mg a 98 dollari al chilogrammo.
Nel mercato dei produttori, segnaliamo Heraeus Additive Manufacturing, un’azienda tedesca specializzata nella lavorazione di metalli preziosi che produce vari tipi di titanio, come 6Al-4V, grado 5 e grado 23. GKN, invece, offre titanio puro e titanio Beta 21S. Per quanto riguarda l’alluminio, Uniformity Labs ed Equispheres sono aziende che commercializzano la lega di alluminio AISi10Mg, mentre APWorks produce polvere di lega di alluminio serie 7000.
Cosa ne pensi del nostro articolo? Faccelo sapere lasciando un commento sui nostri social Facebook e LinkedIn. Trovi tutti i nostri video sul nostro canale YouTube! Non dimenticare di iscriverti alla nostra Newsletter settimanale per ricevere tutte le notizie sulla stampa 3D direttamente nella casella di posta!