Stampa 3D multimateriale in metallo per parti di automobili leggere e resistenti
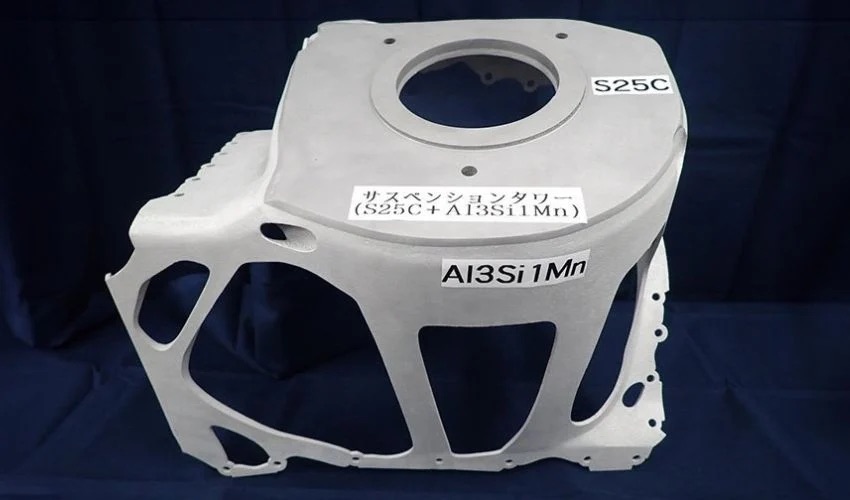
Una delle principali tendenze nella produzione di automobili è senza dubbio quella di rendere le parti che compongono il veicolo più leggere possibile per ottenere una migliore efficienza dei consumi, autonomia delle batterie, velocità ecc. Ma le sfide rimangono, in particolare quando si tratta di combinare diversi materiali per sfruttarne le proprietà, ad esempio l’acciaio che garantisce resistenza e l’alluminio noto per la sua leggerezza. Una soluzione potrebbe arrivare ora dai ricercatori dell’Institute for Materials Research and New Industry Creation Hatchery Center dell’Università di Tohoku, che hanno fatto un passo avanti studiando la stampa 3D multimateriale in metallo per creare parti di automobili leggere e resistenti.
La produzione additiva è sempre più presente nel settore automobilistico. In un comunicato stampa dell’Università di Tohoku, la precisione della stampa 3D è stata messa in evidenza come un modo per produrre forme uniche e altamente personalizzabili. Tuttavia, i materiali utilizzati presentano spesso degli svantaggi, ed è qui che entra in gioco la stampa 3D multimateriale.
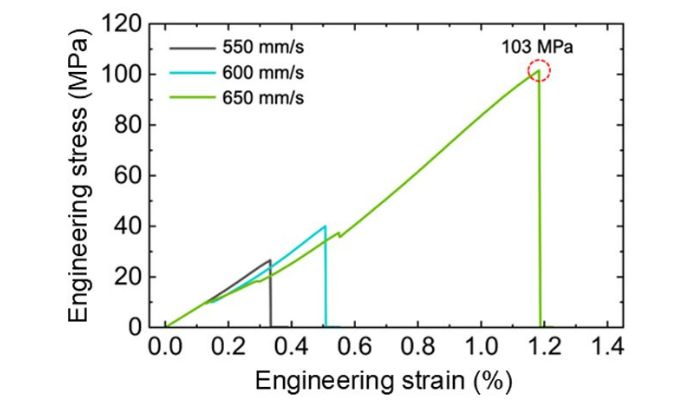
Resistenza lega acciaio-alluminio con LPBF (crediti fotografici: Kenta Yamanaka et al.)
“I multimateriali sono un tema caldo nel campo della produzione additiva grazie alla loro flessibilità di processo”, spiega il Professore Associato Kenta Yamanaka, ”Tuttavia, una sfida importante nell’implementazione pratica è che per alcune combinazioni di metalli, come l’acciaio e l’alluminio, si possono formare composti intermetallici fragili con interfacce dissimili. Quindi, anche se il materiale è più leggero, finisce per essere più fragile”.
Studiando il LPBF, uno dei processi di produzione additiva in metallo più utilizzati nel settore automobilistico, il team di ricerca ha cercato di produrre una lega di acciaio e alluminio che fosse leggera ma resistente. I ricercatori hanno scoperto che l’aumento della velocità del laser sopprime in modo significativo la formazione di composti intermetallici fragili (citando gli esempi di Al5Fe2 e Al13Fe4).
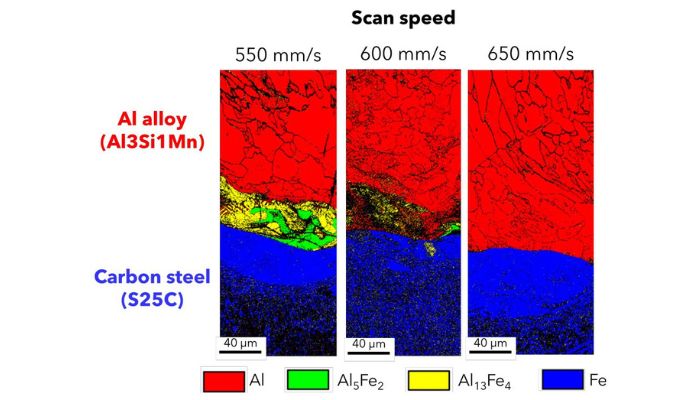
Crediti fotografici: Kenta Yamanaka et al.
I ricercatori ritengono che ciò sia dovuto a un fenomeno chiamato solidificazione di non-equilibrio, che riduce al minimo la separazione degli atomi di metallo, che può portare a punti deboli nel materiale. Di conseguenza, sono stati in grado di dimostrare la presenza di forti interfacce. Il professore Seungkyun Yim, uno dei membri del team, ha aggiunto: “In altre parole, non si possono semplicemente mettere insieme due metalli e aspettarsi che aderiscano senza un controllo preciso”.
Il risultato? Un prototipo di successo di quello che, a detta del gruppo, è il primo componente multimateriale automobilistico in scala reale (una torre di sospensione) con geometria personalizzata. Il gruppo prevede di applicare i risultati ad altre combinazioni di metalli per consentire un numero ancora maggiore di applicazioni. È possibile accedere allo studio completo QUI.
Cosa ne pensi di questa notizia? Se ti interessa l’argomento, non perderti la nostra pagina esclusiva dedicata alla stampa 3D nel settore automotive. Lascia un commento sui nostri canali Facebook, LinkedIn e YouTube. Segui tutte le novità dal mondo della stampa 3D nella nostra Newsletter settimanale!
*Crediti copertina: Kenta Yamanaka et al.