La stampa 3D di compositi per nuove applicazioni aerospaziali e robotiche in Cina
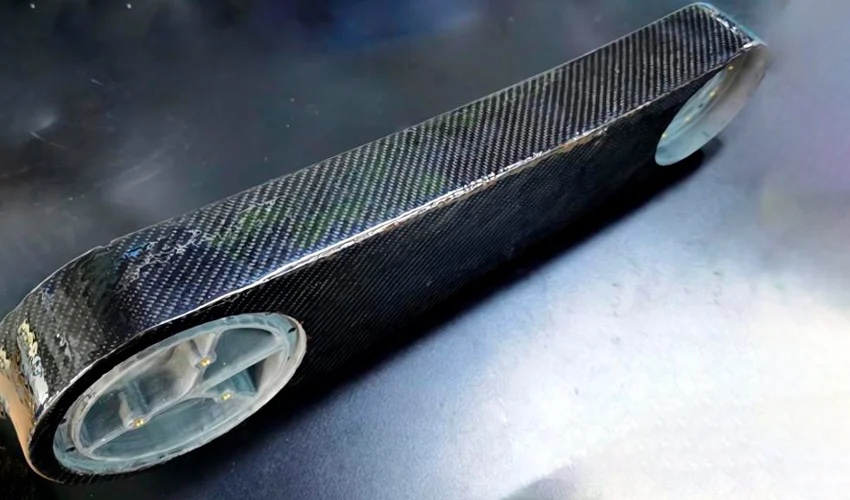
Sebbene negli ultimi anni ci si sia concentrati sulla stampa 3D con polimeri e metalli, c’è una famiglia di materiali che ha mostrato un’immensa crescita nella sfera della produzione additiva: i compositi. Resistenti come il metallo e leggeri come molti polimeri, i compositi per la stampa 3D FFF spesso includono una matrice polimerica e un riempimento come la fibra di vetro o la fibra di carbonio. Sono diventati così diffusi che si prevede che il mercato globale della stampa 3D in composito raggiungerà 490,47 milioni di dollari entro il 2030, dopo aver già raggiunto un valore di 198,31 milioni di dollari nel 2023. L’importanza dei compositi per la stampa 3D è stata riconosciuta anche dall’Institute of Industrial New Materials di Dezhou, in Cina.
Fondato nel gennaio 2021, l’istituto si dedica alla ricerca, allo sviluppo e alla commercializzazione di materiali compositi per applicazioni in settori come quello marittimo, delle comunicazioni 5G, dei processi produttivi avanzati e delle apparecchiature di fascia alta. Un “istituto di ricerca e sviluppo di nuovo stile” in Cina, che ha visto il vantaggio di rivolgersi alla stampa 3D. In collaborazione con INTAMSYS, l’istituto sta portando avanti due iniziative per applicare la stampa 3D allo sviluppo di parti di prodotti in composito.
Sostituzione del tradizionale stampaggio
Non è certo una novità che la stampa 3D sia stata proposta come sostituzione o addirittura integrazione di molti processi produttivi tradizionali. Il motivo è che con la stampa 3D è più facile realizzare geometrie complesse. Inoltre, la progettazione può essere ulteriormente ottimizzata per ridurre i costi e i tempi di consegna.
In un caso, l’istituto è stato incaricato di sviluppare collettori di aspirazione per uno specifico motore aeronautico. I collettori di aspirazione sono componenti critici all’interno dei sistemi motore e hanno un impatto diretto sulle prestazioni complessive del motore, in quanto forniscono aria fresca ai cilindri per garantire la corretta miscela di aria e carburante bruciata in un motore. Tuttavia, lo sviluppo può essere difficile a causa del loro design complesso e delle difficoltà legate alla realizzazione di stampi, ai costi elevati e al processo di saldatura a vibrazione che richiede molto tempo. È qui che entra in gioco la stampa 3D.
L’istituto ha deciso di realizzare questi collettori di aspirazione utilizzando la stampa 3D FFF. In particolare, hanno scelto la stampante 3D 610HT e il PEEK-CF di INTAMSYS. Questi materiali sono stati scelti per le prestazioni del materiale, le capacità dell’apparecchiatura e l’assistenza.
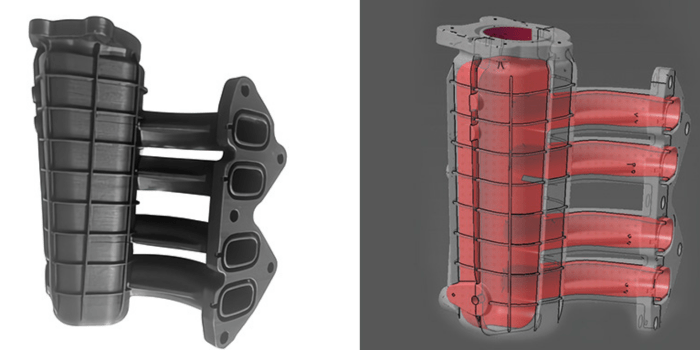
Il collettore finito (a sinistra) e il disegno del pezzo compreso l’interno (a destra)
Vi abbiamo già parlato della FUNMAT PRO 610HT. Questa stampante 3D a doppio ugello e di grande formato è stata progettata per stampare materiali termoplastici ad alta temperatura come PEEK, ULTEM e PPSU e può gestire un’ampia gamma di materiali, compresi i polimeri personalizzati. Questo è possibile grazie a ugelli che possono raggiungere i 500°C e a una camera che può essere riscaldata a 300°C. Ciò consente di stampare materiali ad alte prestazioni senza distorsioni.
Inoltre, gli esperti dell’istituto e di INTAMSYS hanno utilizzato il DfAM per ottimizzare la progettazione e i processi di stampa per realizzare il pezzo di 218,4 × 216,4 × 95,4 mm. Il risultato è stato una riduzione di peso del 30%, con uno spessore della parete più sottile di soli 1,7 mm. È stato inoltre possibile controllare le dimensioni del pezzo per ottenere un accoppiamento preciso e i test hanno dimostrato una resistenza meccanica di 100mPA, superando di oltre il 30% i tradizionali prodotti in PA66-GF stampati a iniezione, il tutto resistendo a temperature di 114°C a lungo termine.
Considerando che le parti realizzate con i tradizionali processi di stampaggio a iniezione (compresi gli utensili) sarebbero costate circa 27.803 dollari con un tempo di consegna di 45 giorni, il valore della stampa 3D è apparso subito evidente. L’istituto è stato in grado di produrre i collettori di aspirazione come un unico pezzo integrato, riducendo così i costi a 1/10 rispetto a quelli realizzati con metodi tradizionali e accorciando i tempi di produzione a soli 4-7 giorni.
Produzione ibrida con la stampa 3D di materiali compositi
Naturalmente, la stampa 3D in composito non è utile solo per sostituire i metodi tradizionali. Può anche essere integrata nei processi esistenti. Questo è stato fatto dall’istituto in collaborazione con un’università cinese per sviluppare un braccio manipolatore robotico in materiale composito.
Per realizzare il braccio manipolatore, ad esempio, sono stati utilizzati la FUNMAT PRO 610HT e il PEEK-CF per la struttura di supporto interna. Il componente risultante non solo era di grandi dimensioni, ma presentava superfici curve, un elevato rapporto rigidità-peso e un’eccezionale resistenza specifica. Questo dimostra la capacità della stampa 3D di compositi di creare parti complesse e ad alte prestazioni.
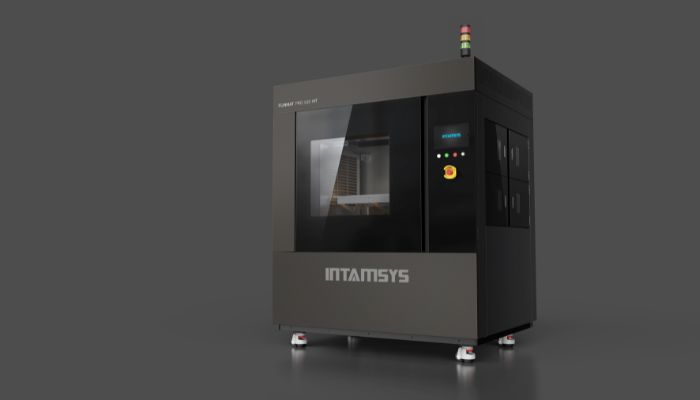
La FUNMAT PRO 610HT è stata utilizzata sia per i collettori di aspirazione che per il componente del braccio robotico.
L’università ha poi utilizzato un metodo di stratificazione pre-impregnato per avvolgere la fibra di carbonio intorno alla struttura stampata in 3D. In questo modo è stato possibile creare rapidamente e a costi contenuti un braccio manipolatore in composito leggero e robusto. La parte migliore? È stato possibile evitare i costosi stampi, pur ottenendo una resistenza strutturale paragonabile a quella delle leghe di alluminio. Inoltre, la stampa 3D in composito può essere combinata con altre tecniche tradizionali, come l’avvolgimento di filamenti, la stratificazione automatizzata e i processi di stampaggio a compressione.
In ogni caso, è chiaro che l’Institute of Industrial New Materials ha dimostrato i vantaggi di sostituire e integrare i processi tradizionali con la stampa 3D di compositi. In particolare, migliorando l’efficienza e riducendo i costi nella produzione di parti in composito.
E tu cosa ne pensi della decisione dell’Institute of Industrial New Materials di passare alla stampa 3D in composito? Condividi la tua opinione sui nostri social Facebook e LinkedIn. Trovi tutti i nostri video sul nostro canale YouTube! Non dimenticare di iscriverti alla nostra Newsletter settimanale per ricevere tutte le notizie sulla stampa 3D direttamente nella casella di posta!
*Copertina: Il componente del braccio robotico, stampato con la stampa 3D di compositi (crediti fotografici: INTAMSYS)