Sostituire i metalli con i polimeri ad alte prestazioni nelle applicazioni industriali
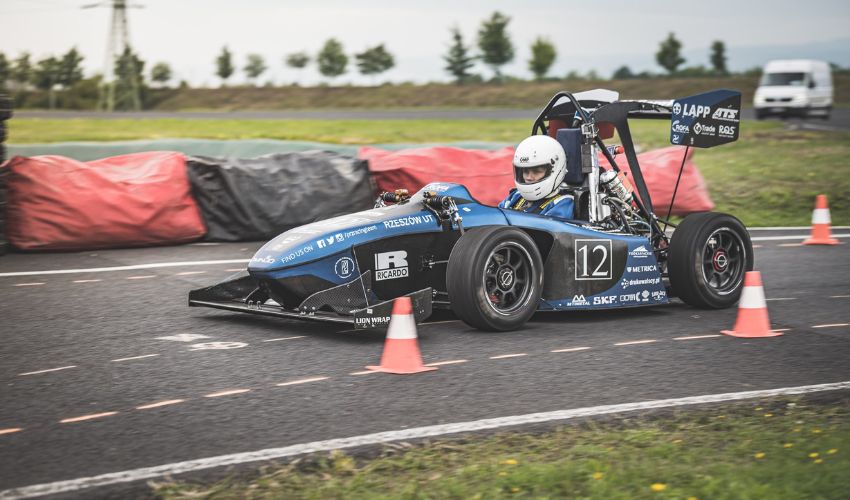
Nella produzione tradizionale, il metallo è apprezzato per la sua forza, la resistenza alla corrosione e la durata, tra le altre proprietà. Anche se questo non cambierà mai, l’aumento dell’uso della produzione additiva con polimeri ad alte prestazioni ha portato a uno sviluppo sorprendente: la capacità di sostituire parti in metallo con questi polimeri tecnici. Questo può avvenire anche in settori critici per la sicurezza come quello aerospaziale, automobilistico e ferroviario.
Ma quali sono i vantaggi della sostituzione di parti metalliche con parti in polimeri ad alte prestazioni? E soprattutto, quali sono gli strumenti necessari per garantire che ciò avvenga in modo sicuro? Omni3D, nota per le sue stampanti 3D di livello industriale, si è affermata come uno dei leader in questo campo e sta lavorando attivamente per dimostrare come sia possibile sostituire i metalli con polimeri ad alte prestazioni in diversi settori. Abbiamo approfondito la questione.
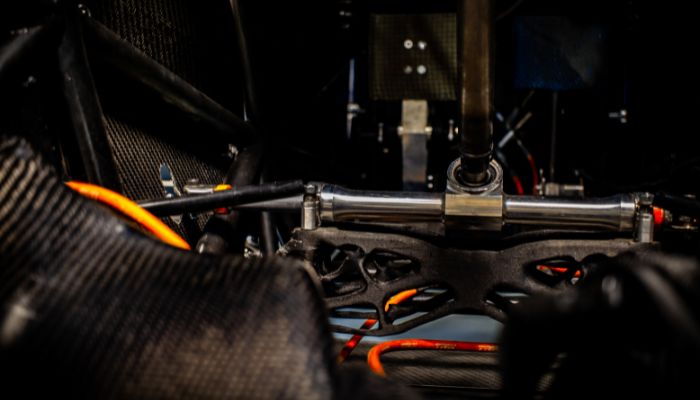
Un supporto per ingranaggi in polimero realizzato con la stampa 3D di grande formato di Omni3D
Quali sono i vantaggi dell’uso dei polimeri ad alte prestazioni rispetto ai metalli?
In primo luogo, è importante notare che cosa sono esattamente i polimeri ad alte prestazioni. Questi materiali termoplastici si distinguono per le loro incredibili proprietà, come la resistenza alla corrosione, il rapporto superiore forza-peso, la durata, la stabilità termica, la resistenza allo scorrimento e la resistenza chimica, tra le altre, a seconda del materiale. Per la produzione additiva, alcuni dei più utilizzati sono PEEK, PEKK e ULTEM, che offrono diversi vantaggi.
Uno dei più significativi è la capacità di ridurre il peso. Nonostante i numerosi vantaggi dei metalli, non si può negare che siano pesanti. I polimeri ad alte prestazioni sono più leggeri e le loro proprietà consentono di offrire prestazioni paragonabili a quelle dei metalli. L’alleggerimento è fondamentale per settori come quello aerospaziale, automobilistico e ferroviario. Infatti, la riduzione del peso si traduce direttamente in una maggiore efficienza del carburante, in una maggiore capacità di carico utile e in una riduzione dell’impatto ambientale.
Non solo, ma combinando i polimeri ad alte prestazioni con la produzione additiva, i vantaggi diventano ancora maggiori. Ciò è dovuto al fatto che la produzione additiva permette di creare parti geometricamente molto più complesse rispetto alla produzione tradizionale, aiutando a liberarsi dai vincoli tradizionali. In particolare, questo può essere utilizzato per ottimizzare i progetti e creare pezzi ancora più leggeri.
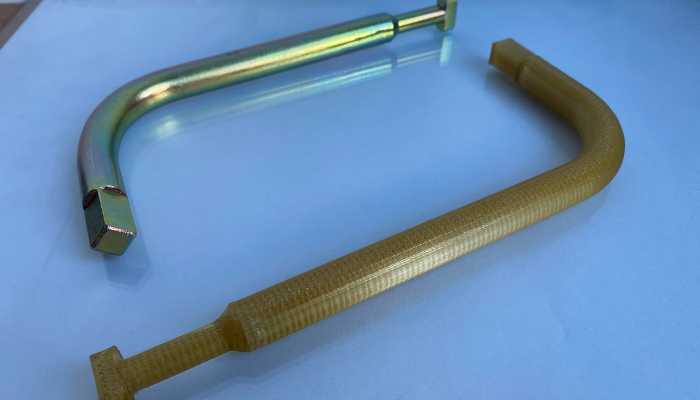
Una chiave metallica per chiusino (in alto) che Omni3D ha sostituito con una versione in polimero ad alte prestazioni (in basso)
L’additive manufacturing è anche noto per essere una svolta quando si tratta di migliorare le catene di fornitura, grazie alla capacità di produrre pezzi su richiesta. È anche una valida alternativa quando si tratta di componenti rotti o obsoleti, soprattutto quelli in metallo. Utilizzando polimeri ad alte prestazioni e la produzione additiva, la produzione sarà significativamente più rapida, riducendo così i tempi di inattività.
Attrezzature necessarie per i polimeri ad alte prestazioni
Tuttavia, c’è un motivo per cui i polimeri ad alte prestazioni non possono essere utilizzati per ogni singolo pezzo realizzato con la stampa 3D. E questo perché non basta una qualsiasi soluzione di produzione additiva. Sono necessarie attrezzature di livello industriale per consentire agli utenti di sfruttare davvero i vantaggi di questi materiali termoplastici e gestire le richieste di produzione su larga scala.
Una delle esigenze più importanti, ovviamente, è la compatibilità dei materiali. Se una macchina non dispone di una camera riscaldata o di un estrusore in grado di raggiungere determinate temperature, sarà impossibile stampare con polimeri ad alte prestazioni. Il controllo preciso della temperatura e il riscaldamento uniforme sono particolarmente importanti per le prestazioni.
Altre qualità ideali sono un volume di stampa maggiore per la produzione di pezzi più grandi e complessi, sistemi di controllo avanzati e meccanismi di precisione e, naturalmente, la capacità di funzionare ininterrottamente con tempi di inattività minimi. I sistemi a materiale aperto sono preferibili anche per consentire agli utenti di sperimentare un’ampia gamma di filamenti e materiali, fondamentali per ottimizzare le proprietà dei pezzi ed esplorare nuove applicazioni.
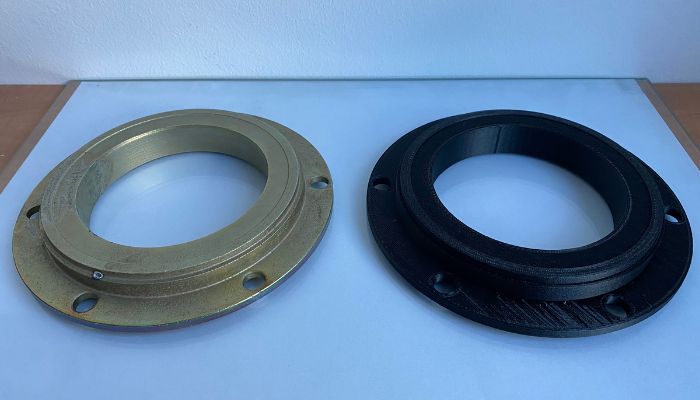
Un cuscinetto per ruota in metallo (a destra) e la versione in polimero ad alte prestazioni realizzata da Omni3D per i veicoli NATO
Omni3D, leader nella stampa 3D industriale, è un buon esempio a questo proposito. Le stampanti di grande formato dell’azienda sono dotate di camere riscaldate, progettate per una regolazione precisa della temperatura, per un riscaldamento uniforme e per evitare punti freddi. Ciò contribuisce a garantire una cristallizzazione ottimale del materiale e a ridurre al minimo la deformazione e altri difetti dei pezzi.
Grazie a queste proprietà, queste macchine sono in grado di gestire gli esigenti requisiti termici di materiali come PEEK, PEKK e ULTEM. Inoltre, viene garantito anche il mantenimento di impostazioni di temperatura accurate anche per lavori di stampa prolungati. Anche se ci sono ancora problemi da superare, queste caratteristiche sono ideali per la stampa con polimeri ad alte prestazioni.
Prendendo un esempio da Omni3D nel settore della difesa, la stampa 3D di grande formato con polimeri ad alte prestazioni ha aiutato la NATO con la manutenzione di una flotta di veicoli BMP-1. Questi carri armati sono risorse fondamentali per le forze militari della NATO, ma possono rappresentare una sfida logistica significativa in quanto l’approvvigionamento di parti di ricambio per loro è un processo sia lungo che costoso. Soprattutto i lunghi tempi di consegna possono mettere a rischio la prontezza operativa.
Omni3D è stata in grado di dimostrare che la NATO poteva produrre parti funzionali ad alta resistenza per i carri armati direttamente in loco. Combinando questo con una libreria digitale di componenti del BMP-1, le forze militari della NATO sono state in grado di evitare i ritardi della catena di approvvigionamento e di garantire il funzionamento continuo del veicolo con tempi di inattività minimi. Nel complesso, grazie alla produzione additiva, la NATO ha registrato un miglioramento significativo nella manutenzione della flotta.
Un altro esempio di sostituzione di parti metalliche con polimeri ad alte prestazioni grazie alle soluzioni Omni3D proviene da Luk-Plast. In questo caso, l’azienda aveva un problema: i rotori in ottone delle pompe a vuoto si stavano logorando a causa dell’esposizione a condizioni difficili, come sostanze chimiche aggressive, acqua e gas. Questo, unito al funzionamento ad alta velocità e al servizio continuo che aggiungeva stress meccanico, comportava frequenti sostituzioni e un aumento dei tempi di inattività, dunque inefficienze nei sistemi ferroviari.
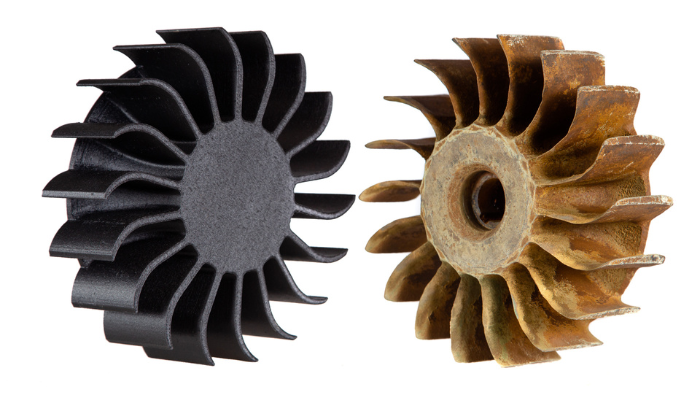
I rotori della pompa per vuoto in ottone (a destra) e in polimero ad alte prestazioni (a sinistra)
Anche in questo caso, Omni3D è riuscita a risolvere il problema con parti in polimero. In particolare, la stampante 3D Omni Pro e il CF PA-12 sono stati utilizzati per creare parti durevoli in grado di resistere a queste condizioni estreme. L’azienda ha osservato che il controllo preciso della temperatura nella camera riscaldata ha permesso al componente stampato in 3D di mantenere la sua forza e stabilità, anche di fronte a sostanze chimiche aggressive e ad elevate sollecitazioni meccaniche. Alla fine, il rotore stampato in 3D ha migliorato notevolmente la durata di vita, riducendo gli intervalli di manutenzione e minimizzando i tempi di fermo.
Analogamente, nel settore automobilistico, Omni3D è stata in grado di sostituire un collettore di aspirazione in metallo, un supporto per ingranaggi e una copertura del giunto per il PRz Racing Team utilizzando la stampa 3D, il CF PA-12 e il TPU-93A. Le parti polimeriche ottenute erano leggere, durevoli e resistenti al calore. Il ricorso alla produzione additiva ha consentito una flessibilità di progettazione e una produzione rapida ed economica, oltre a parti più leggere: il peso del collettore di aspirazione è stato ridotto di 1,5 kg rispetto all’equivalente in alluminio.
Questi sono soltanto alcuni esempi che dimostrano cosa si può ottenere quando si utilizzano polimeri tecnici ad alte prestazioni per sostituire il metallo, soprattutto quando si ricorre alla produzione additiva.
Come favorire i progressi futuri?
C’è un altro fattore però di importanza critica quando si lavora con i polimeri ad alte prestazioni: l’elemento umano. Allo stato attuale, gli ingegneri e i tecnici non sono sempre dotati delle conoscenze necessarie per utilizzare l’AM per le applicazioni industriali, soprattutto quando si tratta di sostituire parti metalliche con parti in polimeri ad alte prestazioni. Anche in questo caso, i leader del settore come Omni3D hanno un ruolo importante da svolgere.
Gli ingegneri che lavorano con i polimeri ad alte prestazioni devono essere competenti in un’ampia gamma di aree. Tra queste, la capacità di valutare i progetti di parti per la stampabilità, saper utilizzare la scansione 3D e il reverse engineering, essere in grado di creare progetti CAD ottimizzati per la produzione, selezionare i materiali più appropriati in base ai requisiti della parte e al processo AM utilizzato, essere in grado di ottimizzare i parametri di stampa e comprendere le tecniche di post-processing necessarie. Tutti questi aspetti sono importanti per poter utilizzare veramente le tecnologie e sfruttarne i vantaggi.
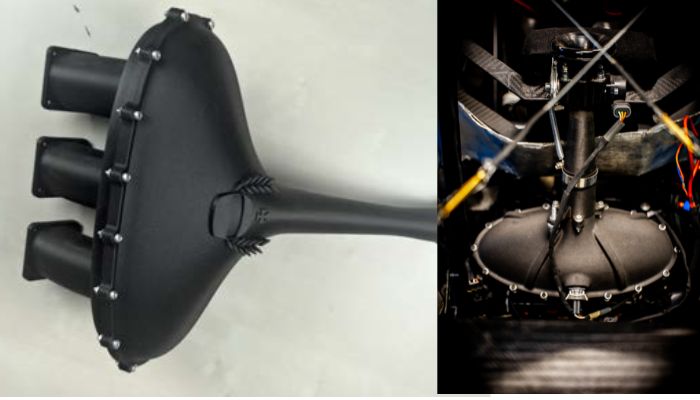
Un collettore di aspirazione realizzato per PRz Racing con le soluzioni Omni3D e il CF PA-12
Ma come è possibile? Un modo è garantire che i sistemi siano aperti. Omni3D, ad esempio, ha sempre sottolineato l’importanza di mantenerli aperti per favorire lo sviluppo futuro delle apparecchiature utilizzate per la sostituzione di parti metalliche con sostituti stampati in 3D. Le piattaforme e i software open-source contribuiranno ad aumentarne l’adozione, in quanto i team tecnici possono utilizzare e testare le tecnologie AM al proprio ritmo.
Un ulteriore aspetto è quello di dare maggiore priorità alla formazione e all’assistenza. Entrambe le cose su cui Omni3D si è impegnata negli ultimi anni. Attraverso workshop pratici, risorse online per l’apprendimento autonomo, assistenza tecnica in caso di problemi e persino programmi di formazione personalizzabili, Omni3D spera di consentire alle aziende di sfruttare il potenziale dell’AM nell’industria.
Questa attenzione alla formazione e all’assistenza è uno dei fattori più importanti che contribuirà a favorire il passaggio dai metalli ai polimeri ad alte prestazioni, anche per le parti critiche per la sicurezza. I materiali stessi e le attrezzature appropriate renderanno possibile massimizzare l’uso della produzione additiva e promuovere l’innovazione. Per saperne di più su come Omni3D fa tutto questo, puoi consultare il white paper gratuito, scaricabile QUI.
Cosa ne pensi della sostituzione dei metalli con polimeri ad alte prestazioni? Condividi la tua opinione sui nostri social Facebook e LinkedIn. Trovi tutti i nostri video sul nostro canale YouTube! Non dimenticare di iscriverti alla nostra Newsletter settimanale per ricevere tutte le notizie sulla stampa 3D direttamente nella casella di posta!