Sinterizzazione laser selettiva (SLS): tutto quello che c’è da sapere
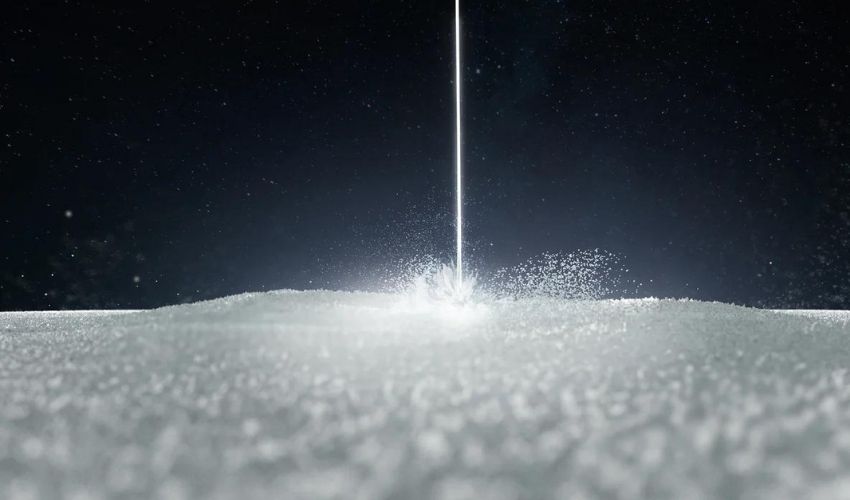
La sinterizzazione laser selettiva (SLS) è una tecnologia di stampa 3D basata sulla sinterizzazione di uno strato di polvere per creare oggetti tridimensionali. È uno dei metodi di produzione additiva industriale più diffusi. In questo articolo analizzeremo in dettaglio il funzionamento di questo processo.
Storia e sviluppo della tecnologia SLS
La storia della tecnologia SLS risale agli anni ’80, quando Carl Deckard e Joseph Beaman iniziarono a lavorarci all’Università del Texas ad Austin, negli Stati Uniti. La nascita di questa tecnologia è strettamente legata alla DTM Corporation, che ha ottenuto il brevetto nel 2001, prima di essere acquisita da 3D Systems. Anche altre aziende, come Farsoon Technologies, fondata nel 2009 in Cina, hanno contribuito allo sviluppo di questo metodo di stampa 3D. È interessante sapere che un altro processo simile alla SLS è stato inventato e brevettato nel 1979 da R.F Housholder, ma non è mai stato messo in commercio.
Come funziona la sinterizzazione laser selettiva (SLS)?
La tecnologia SLS si basa sul principio della fusione a letto di polvere. Le fasi e i componenti principali del processo di stampa sono i seguenti:
- Stoccaggio del materiale in polvere: Il materiale utilizzato nella stampa SLS è una polvere fine di polimero termoplastico. Questa polvere viene stoccata in un contenitore apposito;
- Preriscaldamento: la polvere viene preriscaldata all’interno della stampante a una temperatura leggermente inferiore a quella di sinterizzazione. Questa temperatura è inferiore anche a quella di fusione del materiale;
- Distribuzione del materiale con il rullo: per ogni strato della stampa, un sottile strato di polvere viene distribuito sul piatto di stampa tramite un rullo;
- Sinterizzazione laser: un laser CO2 scansiona accuratamente la superficie della polvere. Il raggio laser riscalda la polvere in maniera selettiva e precisa, fornendo l’energia necessaria per sinterizzare il materiale. Le particelle di polimero, sotto l’effetto del calore, si saldano tra loro formando l’oggetto solido.
I principali vantaggi della tencologia SLS
La sinterizzazione laser selettiva offre una serie di vantaggi, tra cui :
- Libertà di progettazione: uno dei vantaggi più utili che offre la tecnologia SLS è la libertà di progettazione. La tecnologia consente di creare parti con forme e geometrie complesse, impossibili da ottenere con altri metodi di stampa 3D. La regione di questa libertà sta nel fatto che non sono necessari supporti per la stampa. A differenza di altri processi, come la modellazione a deposizione fusa (FDM), la tecnologia SLS non utilizza supporti temporanei per sorreggere le parti sporgenti dell’oggetto durante la stampa. Le parti SLS sono infatti ricoperte e circondate da polvere non fusa che funge da supporto naturale. Questo permette di poter creare senza problemi modelli complessi con sporgenze, angoli vivi e dettagli interni;
- Riciclaggio dei materiali: il riciclaggio della polvere non fusa è un importante aspetto economico ed ecologico della SLS. Dopo ogni ciclo di stampa, la polvere non utilizzata viene recuperata e rimescolata con polvere vergine;
- Precisione: questo livello di precisione è particolarmente vantaggioso in applicazioni che richiedono la produzione di pezzi di alta qualità, con finiture impeccabili. I componenti realizzati tramite SLS presentano una superficie liscia e uniforme, con pochissimi o con nessun segno visibile dei singoli strati, garantendo un aspetto finale di grande precisione e qualità estetica.
Materiali per la sinterizzazione laser selettiva
La sinterizzazione laser selettiva offre un’ampia varietà di materiali compatibili. Sebbene la tecnologia SLS sia principalmente associata ai polimeri plastici, è estremamente versatile. Il nylon, meglio conosciuto come poliammide, è il materiale più comunemente utilizzato. La tecnica è compatibile anche con TPU, polipropilene, allumide, carbonmide, PEBA, PA11 e potenzialmente anche PEEK. Inoltre, è possibile incorporare additivi come carbonio, vetro o alluminio, migliorando così le proprietà meccaniche dei pezzi.
Post-processing
Dopo la stampa i pezzi vengono rivestiti di polvere creando un blocco chiamato “cake” (torta). Per consentire la depolverizzazione e il post-processing, il serbatoio della polvere deve essere raffreddato, il che può richiedere diverse ore. I pezzi vengono poi depolverizzati utilizzando aria compressa o sabbiatura, un metodo che prevede la proiezione di un getto di materiale abrasivo, come particelle di sabbia, ad alta pressione sui pezzi. Le particelle abrasive rimuovono efficacemente la polvere non fusa, lasciando i pezzi con una finitura pulita. Questo metodo garantisce che i dettagli fini e le geometrie complesse non siano ostruiti dai residui di polvere. Una volta pulito, il pezzo può essere utilizzato così com’è, oppure dipinto o verniciato. La verniciatura può migliorare ulteriormente l’aspetto e la durata dei pezzi creati con la tecnologia SLS. Si tratta dell’applicazione di uno strato di rivestimento protettivo sulla superficie dei pezzi per migliorarne l’aspetto e la sensazione al tatto, proteggerli dall’usura e garantirne l’impermeabilità.
Mercato della stampa 3D SLS
La tecnologia SLS trova applicazione in diversi campi, dal design industriale al settore automobilistico, aerospaziale e ingegneristico. Storicamente, i principali attori del mercato sono stati 3D Systems e EOS GmbH, specializzati in sistemi SLS professionali. Tuttavia, con la scadenza del brevetto di questa tecnologia nel 2014, sono emersi nuovi attori, come Formlabs con Fuse 1 e Sinterit con Lisa. Questa aumentata accessibilità della tecnologia sta aprendo nuove prospettive per la stampa 3D SLS, avvicinandola a un pubblico sempre più ampio.
Utilizzi la tecnologia di sinterizzazione laser selettiva? Faccelo sapere condividendo la tua opinione nei commenti qui sotto o con la comunità di 3Dnatives sui nostri social Facebook e Linkedin . Trovi tutti i nostri video sul nostro canale YouTube!
*Crediti per la foto di copertina: EOS