Ricottura VS pressatura isostatica a caldo: quale trattamento termico scegliere?
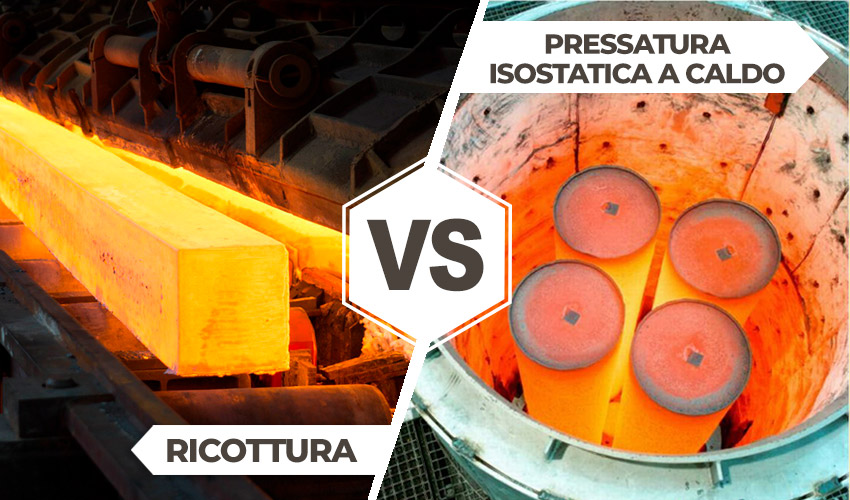
Con la continua industrializzazione della produzione additiva, la post-produzione sta diventando sempre più cruciale. Attraverso questa fase critica, gli utenti possono migliorare le parti, rendendole più resistenti e più dense o persino conferendo loro proprietà specifiche, assicurando che possano essere utilizzate per importanti applicazioni finali. Tra i diversi tipi di post-processing, uno dei più importanti per la stampa 3D a letto di polvere, soprattutto per i metalli, è il trattamento termico.
Ma quale trattamento termico scegliere? Per rispondere a queste domande, abbiamo voluto analizzare due processi di trattamento termico comunemente utilizzati: la pressatura isostatica a caldo (Hot Isostatic Pressing – HIP) e la ricottura.
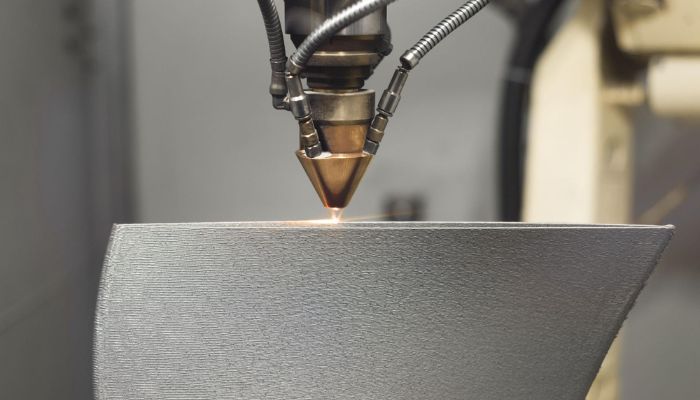
Una parte in metallo realizzata con la produzione additiva (Crediti immagine: Industrial Metal Service)
Entrambi sono compatibili con i processi metallici, tra cui LPBF, EBM, Binder Jetting, DED e persino il Nanoparticle Jetting. Possono essere utilizzati anche con ceramiche e polimeri, anche se in misura diversa. Hanno molti vantaggi, come il rafforzamento dei materiali e il miglioramento delle loro proprietà. Di base, queste due tecniche ottimizzano i componenti, ma i loro processi e i risultati specifici sono diversi. Vediamoli nel dettaglio.
Come funzionano HIP e ricottura
Per comprendere le differenze e le analogie tra HIP e ricottura, analizzeremo ciascuna procedura. In primo luogo, la ricottura è un trattamento termico che prevede il riscaldamento di metalli, vetro, ceramica o polimeri e il lento raffreddamento del materiale per eliminare le tensioni interne. Questo processo altera le proprietà fisiche e talvolta chimiche di un materiale, aumentandone la duttilità e riducendone la durezza per facilitarne la lavorazione.
La pressatura isostatica a caldo, invece, consiste nell’esporre un pezzo a una combinazione di alte temperature e pressioni di gas per eliminare la porosità nei materiali metallurgici. Può anche aumentare la densità di molte ceramiche, trasformandole in componenti completamente densi.
Ricordiamo che la parola “isostatica” si riferisce al gas che viene applicato in modo isostatico, ovvero esercita una pressione uguale in tutte le direzioni su un materiale. In questo modo si ottiene una forza uniforme intorno all’oggetto. Analogamente alla ricottura, la pressatura isostatica a caldo migliora le proprietà meccaniche e la lavorabilità di un materiale. Il processo può anche unire materiali diversi per creare pezzi unici.
Il processo di ricottura
La ricottura avviene in un forno di ricottura. Questi variano a seconda delle esigenze dei materiali e del costo, ma in generale possono essere riscaldati tra 300°C e 1000°C (per i modelli di fascia più alta). La temperatura all’interno del forno deve essere accuratamente controllata, motivo per cui questi forni di ricottura sono generalmente consigliati, anche se in teoria si può utilizzare qualsiasi forno che raggiunga la giusta temperatura.
La ricottura consiste in tre fasi, tutte determinate da parametri di temperatura che dipendono dal tipo di materiale utilizzato. Per effettuare la ricottura è fondamentale quindi conoscere il materiale e i suoi requisiti.
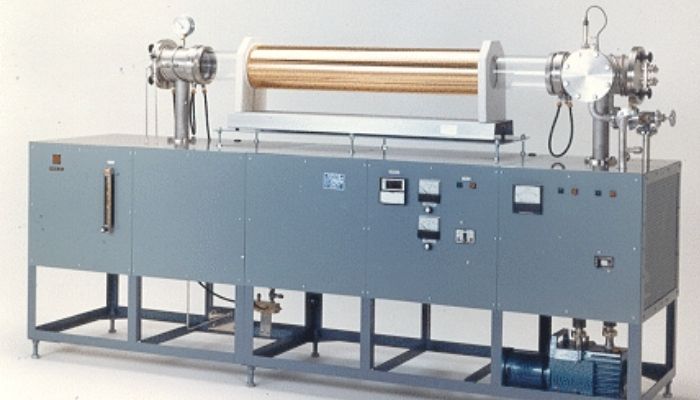
Un forno di ricottura (crediti fotografici: Thermcraft)
1. Fase di riscaldamento
Nella prima fase della ricottura, la temperatura del materiale viene portata al di sopra della temperatura di cristallizzazione, in modo che gli atomi abbiano l’energia per muoversi. Il movimento degli atomi aiuta a ridistribuire ed eliminare le dislocazioni (irregolarità all’interno di una struttura cristallina), in particolare nei metalli. Ciò rende il metallo più deformabile e quindi più duttile. Lo stesso effetto può verificarsi con la ceramica, ma in misura minore. Nel complesso, questa fase allevia le tensioni interne del materiale.
2. Fase di mantenimento
Man mano che il materiale continua a riscaldarsi, raggiunge la fase di ricristallizzazione, a una temperatura sufficientemente alta per la ricristallizzazione ma ancora inferiore al punto di fusione. Qui si formano e crescono nuovi grani privi di deformazioni, che sostituiscono lo spazio lasciato dalle dislocazioni precedenti.
3. Fase di raffreddamento graduale
Una volta completata la ricristallizzazione, l’oggetto può iniziare a raffreddarsi. Durante il raffreddamento, si sviluppano e crescono nuovi grani nel materiale. Tuttavia, la crescita dei grani non è casuale. È controllata a seconda della velocità di raffreddamento e dell’atmosfera in cui si raffredda.
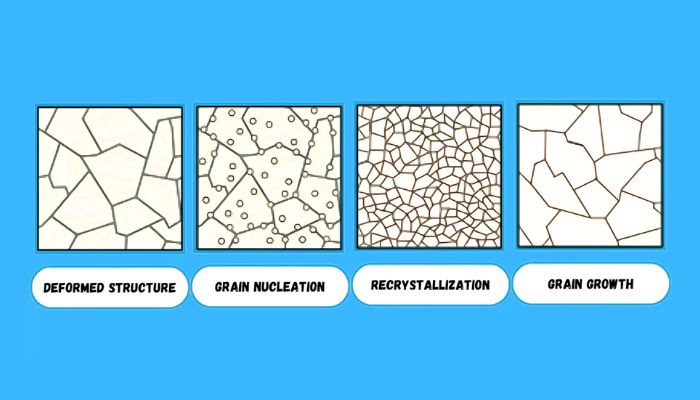
Una rappresentazione grafica di ciò che accade alle molecole durante la ricottura (crediti fotografici: MechDaily)
A seconda del materiale, la ricottura può durare anche solo quattro ore o un giorno intero. Si noti inoltre che esistono diversi tipi di ricottura. Anche se non si tratta di un elenco completo di tutti i processi di ricottura, alcuni dei più utilizzati includono la ricottura completa o totale, la ricottura isotermica, la ricottura sferoidizzante, la ricottura per diffusione e la ricottura di distensione.
I pezzi di produzione additiva, o almeno quelli realizzati con materiali adatti, possono beneficiare di tutti questi processi. Nella scelta tra i diversi tipi di processi di ricottura, i fattori determinanti sono il materiale e l’applicazione.
Il processo di pressatura isostatica a caldo (HIP)
Il processo HIP consiste nel caricare i pezzi in un recipiente di contenimento ad alta pressione e nell’esporli a una temperatura elevata e a un’alta pressione isostatica del gas. Le temperature possono raggiungere i 2.000°C e la pressione i 310 MPa – circa la stessa pressione della Fossa delle Marianne a 11.000 m di profondità nell’Oceano Pacifico. In questo modo il materiale si contrae, mantenendo la sua forma iniziale fino a quando i pori all’interno scompaiono, densificando il pezzo. Il processo è ampiamente utilizzato per alleviare le tensioni in componenti sinterizzati, fusi e prodotti additivi.
L’argon è il gas di pressurizzazione più utilizzato per il processo. In particolare, l’argon è un gas inerte, quindi non fa reagire chimicamente il materiale. Anche il tipo di metallo utilizzato può ridurre al minimo gli effetti di una reazione chimica. Alcuni sistemi utilizzano anche il pompaggio del gas associato per raggiungere il livello di pressione necessario. Questi gas vengono applicati uniformemente all’oggetto e mantenuti per un tempo specifico.
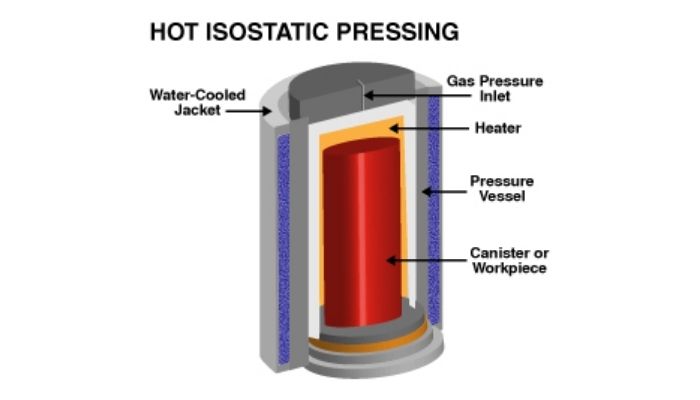
Crediti fotografici: Metal Powder Industries Federation
I livelli di temperatura e pressione del gas, così come la durata del ciclo, sono tutti determinati dal tipo di materiale utilizzato e dalle proprietà desiderate del prodotto finale. I cicli possono durare da otto a dodici ore o giorni. Il processo conferisce ai pezzi una microstruttura uniforme, migliorandone le proprietà.
In termini di processi di stampa 3D, Hiperbaric, leader nella pressatura isostatica a caldo, osserva che l’HIP può essere facilmente combinato con la LPBF e l’EBM per ottenere parti di qualità superiore. Sono compatibili anche il binder jetting, il DED, l’estrusione di materiale metallico e il getto di materiale metallico (come nel caso del nanoparticle jetting).
Compatibilità dei materiali per HIP e ricottura
Lo abbiamo accennato brevemente sopra, ma HIP e ricottura hanno alcune sovrapposizioni per quanto riguarda i materiali. In particolare, entrambi i processi possono essere utilizzati con diversi metalli. Inoltre, non sembrano esserci restrizioni sui metalli che possono essere utilizzati per entrambi i processi.
Prendiamo ad esempio la ricottura. Questo metodo di post-lavorazione è compatibile sia con i materiali amorfi che con quelli cristallini. Pertanto, può essere utilizzato, tra gli altri, per metalli refrattari, leghe e acciaio. L’acciaio inossidabile è uno dei materiali più comunemente utilizzati per le parti ricotte, ma vengono citati anche bronzo, alluminio, rame e ottone.
Con la pressatura isostatica a caldo, tutti i metalli sembrano essere compatibili. Ciò significa che funziona anche con la maggior parte dei processi di stampa 3D in metallo e i relativi materiali compatibili. Può essere utilizzato anche con materiali difficili da lavorare, come le superleghe di nichel e le leghe di titanio.
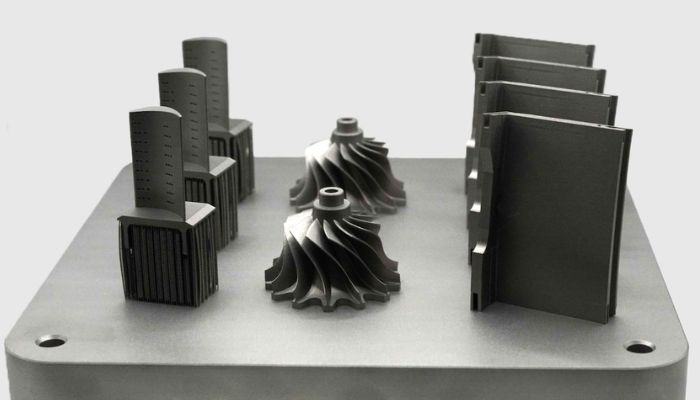
Esempio di superlega di nichel stampata in 3D (crediti fotografici: Alloyed Aubert & Duval)
Tuttavia, i metalli non sono gli unici materiali compatibili. Anche le parti in ceramica possono essere post-processate con HIP o ricottura. Anche in questo caso, sembra che, se si rispettano le proprietà del materiale ceramico, tutte le ceramiche siano compatibili con entrambi i processi.
La ricottura, invece, è compatibile con la maggior parte dei polimeri. Poiché la ricottura non comporta pressione, ma è legata a variazioni di temperatura, molti polimeri utilizzati per l’Additive Manufacturing possono essere ricotti. In effetti, la ricottura è stata spesso citata come un modo per migliorare la resistenza delle parti in ABS. Altri materiali standard, come il PLA e il PETG, vengono sempre più spesso ricotti anche dai produttori.
La pressatura isostatica a caldo di polimeri è meno diffusa, soprattutto nella produzione additiva. Tuttavia, alcuni ricercatori hanno scoperto che se la temperatura viene abbassata, in un processo noto come Warm Isostatic Pressing (WIP), materiali come il nylon o l’HPP possono essere post-processati con questo metodo. Tuttavia, si tratterebbe in genere di un’eccezione, soprattutto se si considera il costo dell’HIP rispetto alla ricottura. Questo metodo è più adatto alle applicazioni e ai materiali industriali.
Vantaggi e svantaggi dei processi
Sebbene la ricottura e la pressatura isostatica a caldo comportino processi diversi, i vantaggi sono simili. Entrambi migliorano la duttilità e rimuovono le imperfezioni del materiale, che siano pori (HIP) o dislocazioni all’interno della struttura cristallina (ricottura). La ricottura e la pressatura isostatica a caldo rimuovono essenzialmente i difetti e le tensioni interne e migliorano l’omogeneità microstrutturale e le proprietà del materiale.
La ricottura, poiché provoca la migrazione delle molecole all’interno della microstruttura, elimina le tensioni che possono essere state introdotte durante la formazione del materiale. Il processo previene anche le cricche e migliora la lavorabilità. Inoltre, con la rettifica delle dislocazioni nel reticolo cristallino del metallo, la conducibilità elettrica del metallo viene migliorata, così come le proprietà magnetiche. La ricottura può consentire di manipolare con precisione un materiale per ottenere le caratteristiche desiderate, riscaldando e raffreddando selettivamente e ottenendo così il tipo di grani desiderato, influenzando le proprietà fisiche del materiale.
La pressatura isostatica a caldo è ottima per aumentare la densità di un materiale perché il processo forma legami metallurgici tra materiali diversi attraverso l’incollaggio per diffusione. Questi miglioramenti sono fondamentali per le applicazioni che richiedono elevata resistenza e affidabilità. Il metodo può anche riparare i difetti di un materiale. Ad esempio, un pezzo di metallo con un foro interno può essere sottoposto a HIP, in modo da riempire il foro con materiale compresso. In generale, sia l’HIP che la ricottura possono contribuire a ridurre al minimo gli sprechi di materiale perché possono migliorare il materiale esistente, garantendone una maggiore durata e riducendo la necessità di acquistare altro materiale.
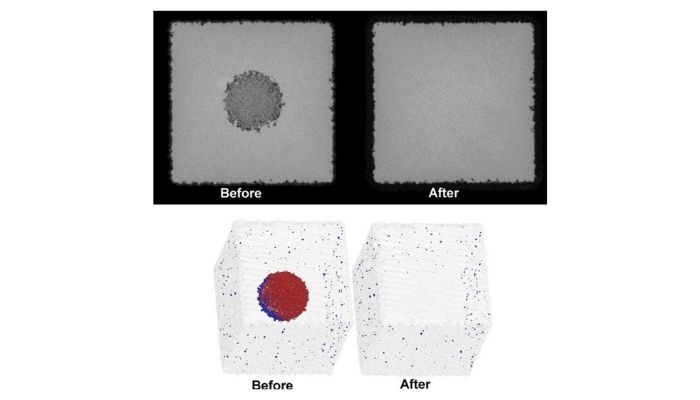
Una rappresentazione prima e dopo di un materiale sottoposto a HIP (crediti fotografici: Hot isostatic pressing in metal additive manufacturing X-ray tomography reveals details of pore closure, Science Direct, A. du Plessis a b, E. Macdonald)
Uno svantaggio di HIP e ricottura è il tempo necessario per completare il processo. Entrambi i metodi possono richiedere più di 24 ore, e l’HIP in particolare può richiedere diversi giorni. Naturalmente, entrambe le tecnologie comportano anche una spesa da considerare. Richiedono costi iniziali per le attrezzature e gli operatori qualificati, e poi richiedono elevate quantità di energia per il calore. La ricottura può anche comportare un raffreddamento forzato, il che significa ancora più energia. Per entrambi i metodi, i tempi e i costi dipendono in larga misura dal materiale utilizzato e dalle dimensioni della produzione.
Infine, entrambi i processi possono influire sulle dimensioni finali del pezzo, il che non è necessariamente uno svantaggio, ma è da tenere in considerazione. La ricottura può causare un cambiamento nelle dimensioni perché la microstruttura del materiale viene modificata, e questo può accadere anche con l’HIP perché il materiale viene compresso. Il grado di variazione dipende da fattori quali il materiale utilizzato e i parametri del processo.
Quindi, quando non utilizzare la ricottura o la pressatura isostatica a caldo? Se i vostri pezzi non richiedono proprietà meccaniche migliorate, potrebbe non valere la pena di pagare per questi processi. In particolare, l’HIP potrebbe non essere adatto se avete un pezzo con cavità interne o canali intricati che potrebbero collassare a causa della pressione. L’HIP è ideale quando si desidera che un pezzo sia denso, quindi se si dispone di un pezzo di produzione additiva già completamente denso (come un pezzo di alta qualità ottenuto con fusione a letto di polvere laser), non sarebbe necessario.
Applicazioni di pressatura isostatica a caldo (HIP) e ricottura
In termini di applicazioni, la più importante per entrambi è il post-processing generale come metodo per migliorare le proprietà dei materiali nei pezzi. Ciò significa che tecnicamente sia la ricottura che la pressatura isostatica a caldo potrebbero essere utilizzate in qualsiasi settore in cui le proprietà dei materiali sono importanti. Anche se è necessario menzionare che, mentre l’HIP è relativamente inaccessibile se non a livello industriale, la ricottura può essere eseguita molto più facilmente, aprendola a un pubblico più ampio.
Esistono tuttavia anche settori specifici in cui questi metodi di post-processing sono comunemente utilizzati. L’HIP, ad esempio, è stato utilizzato per la prima volta in ambito commerciale nell’industria aerospaziale. In particolare, per produrre le pale delle turbine dei motori a reazione. Naturalmente, all’epoca non si trattava di parti realizzate con la produzione additiva.
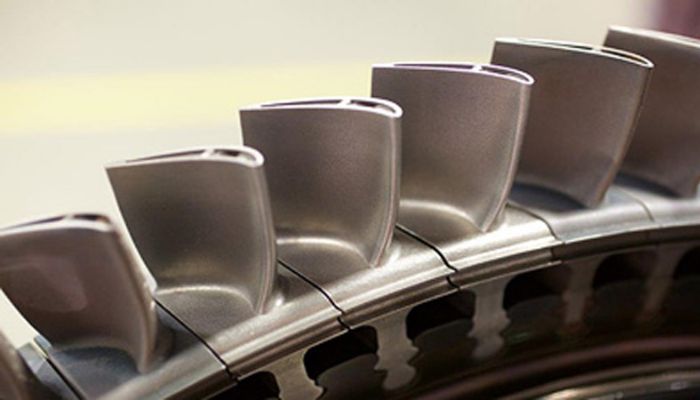
Pale di turbina stampate in 3D (crediti fotografici: Siemens)
Se vogliamo esaminare nello specifico l’uso dell’HIP in combinazione con la stampa 3D, sono molti i settori in cui si riscontrano vantaggi. Ad esempio, nel settore medico, i processi HIP e LPBF possono essere utilizzati per creare protesi di anca e di ginocchio utilizzando leghe di titanio. Nel settore aerospaziale, le superleghe di nichel sono utilizzate con LBPF per le pale delle turbine e CoCR per gli iniettori di carburante. L’HIP è presente anche nel settore automobilistico, in quanto consente una maggiore affidabilità delle parti stampate in 3D. In sostanza il processo è utile ovunque siano necessarie migliori proprietà di fatica grazie all’eliminazione delle concentrazioni di stress.
La ricottura può essere utilizzata in settori simili, poiché migliora la duttilità, elimina le tensioni e riduce la durezza dei materiali. Anche la fragilità dei metalli può essere ridotta, migliorando le proprietà magnetiche. Pertanto, le applicazioni in cui queste caratteristiche sono apprezzate sono le più adatte.
I settori chiave per la ricottura sono quello medico, aerospaziale, automobilistico e dei semiconduttori. Nel settore aerospaziale, viene comunemente utilizzata per i componenti degli aerei e può essere impiegata in modo analogo per i pannelli della carrozzeria nel settore automobilistico. In medicina, invece, può essere utilizzata per dispositivi medici come gli impianti ortopedici, in quanto può essere utile per formare leghe e metalli biocompatibili con le caratteristiche di resistenza e durata richieste. Infine, poiché la ricottura può migliorare la conducibilità elettrica, può essere utile nell’industria elettronica per la produzione di semiconduttori o celle solari.
Produttori e prezzi
Per la ricottura, come accennato, non è per forza necessario un forno di ricottura. A volte, i forni standard come quelli da laboratorio sono adatti, soprattutto per progetti su piccola scala o fai da te, dove non è necessaria un’estrema precisione, soprattutto con i polimeri. Tuttavia, nei casi in cui è necessaria un’elevata precisione, potrebbe essere necessario un forno di ricottura dedicato. Tra i produttori di forni di ricottura troviamo Precons, Gasbarre Products, Inc e CM Furnaces, Inc.
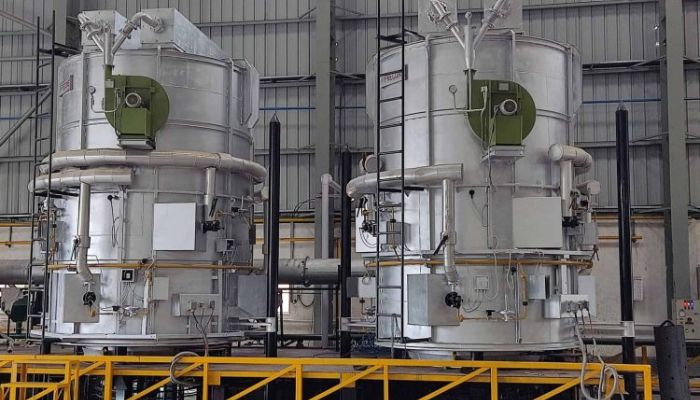
Forni di ricottura a campana (crediti fotografici: Precons)
A differenza della ricottura, l’HIP richiede macchine specializzate. Si può ricorrere a un servizio di HIP o prendere in considerazione l’acquisto di una macchina. Tra i produttori più noti ricordiamo Bodycote, Kobe Steel, Aalberts, Quintus ed ESPI.
Il costo dipende da vari fattori, come il materiale utilizzato, la scala della produzione, i requisiti dell’applicazione e la scelta di esternalizzare il servizio o di completare il trattamento internamente. Per la ricottura, i forni da laboratorio possono partire da circa 500 euro, mentre quelli industriali possono costare da 3.000 a oltre 100.000 euro. Le macchine per la pressatura isostatica a caldo seguono fasce di prezzo simili: le piccole macchine HIP sono disponibili a partire da circa 7.000 euro, mentre quelle grandi possono costare centinaia di migliaia di euro o più.
Utilizzi i processi di ricottura e pressatura isostatica a caldo? Lascia un commento sui nostri canali social Facebook, Twitter, Linkedin e YouTube! Non dimenticare di iscriverti alla nostra Newsletter settimanale per ricevere tutte le notizie sulla stampa 3D direttamente nella tua casella di posta!
*Crediti immagine di copertina: Ricottura (crediti: Aria); HIP (crediti: ThermalProcessing.Com)