Le più recenti applicazioni della stampa 3D nel settore aeronautico
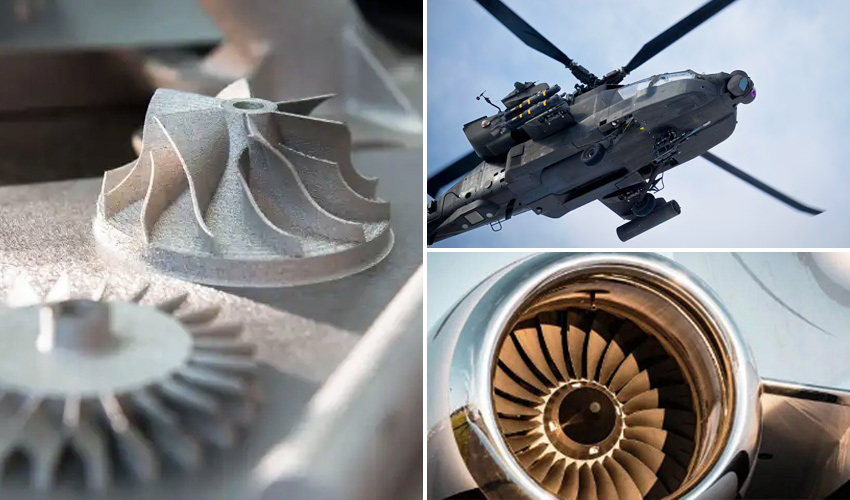
L’Additive Manufacturing (AM) è una tecnologia straordinaria per la produzione di parti leggere, resistenti e geometricamente complesse ed è quindi particolarmente preziosa nel settore aeronautico, dove l’ottimizzazione della resistenza e del peso sono fondamentali. L’aeronautica è la scienza e la pratica della progettazione, della costruzione e del volo di tutti gli aeromobili, tranne quelli che vanno nello spazio. Questo settore è stato uno dei primi ad adottare l’AM, utilizzandola inizialmente per la prototipazione rapida. Oggi, tuttavia, le sue applicazioni si sono estese fino a includere parti per uso finale in aeroplani, elicotteri, droni e altro ancora. Per mostrare la versatilità e l’impatto della stampa 3D in questo campo, abbiamo compilato un elenco di alcune delle più recenti e notevoli applicazioni dell’AM nell’aeronautica.
Norsk Titanium fornisce parti per il Boeing 787 e lancia una nuova partnership con i fornitori
Norsk Titanium US Inc, leader nella produzione additiva di titanio nel settore aerospaziale, ha già fornito parti per il Boeing 787 Dreamliner nel 2021. Norsk è nota soprattutto per la sua tecnologia brevettata Rapid Plasma Deposition®, che migliora la resistenza e la durata del pezzo finale e funziona in modo simile alla Directed Energy Deposition (DED). Al contrario, però, Norsk utilizza un fascio di elettroni che consente di riscaldare la polvere in più punti contemporaneamente. Tra le parti prodotte ci sono componenti in titanio stampati in 3D che sono stati certificati dalla FAA (Federal Aviation Administration). Ora l’azienda ha stipulato un accordo per la fornitura di parti in serie direttamente a The Boeing Company, segnando l’inizio di un rapporto di fornitura diretta. Norsk Titanium prevede di fornire centinaia di parti strutturali entro il 2025. “La nostra tecnologia RPD® e le specifiche consolidate dei materiali consentono a Norsk Titanium di rispondere rapidamente alle esigenze dei nostri clienti”, spiega Nick Mayer, vicepresidente commerciale.
ITP Aero ottiene la certificazione EASA per i componenti stampati in 3D
Con sede a Bizkaia, ITP Aero è riuscita a ottenere le certificazioni dell’Agenzia europea per la sicurezza aerea (EASA) e dell’Agenzia statale per la sicurezza aerea (AESA) per i componenti strutturali stampati in 3D. L’azienda diventa così la prima nel settore dei motori aeronautici a ricevere queste approvazioni per i componenti realizzati utilizzando la sinterizzazione laser selettiva (SLS), applicata alle pale posteriori del motore TP400. Questo processo di produzione additiva industriale consente di creare componenti complessi utilizzando meno materiale ed energia, contribuendo alla sostenibilità del settore. Inoltre, ITP Aero ha sviluppato i propri standard e specifiche di produzione additiva per componenti di motori aeronautici ad alta temperatura. L’azienda dispone di una cella di produzione dedicata e sta costruendo il centro di ricerca “ADMIRE” per continuare a promuovere tecnologie di produzione digitali e sostenibili.
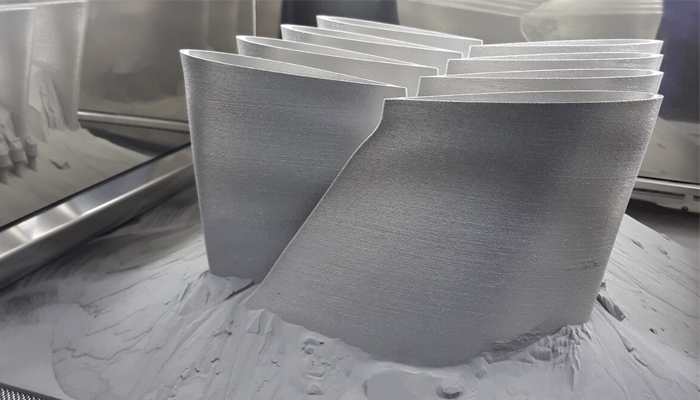
(Crediti fotografici: ITP Aero)
Safran ha investito 80 milioni di euro per il suo campus dedicato alla stampa 3D
Safran è un gruppo internazionale di alta tecnologia che opera nei settori aerospaziale, spaziale e della difesa. Ha investito la somma di 80 milioni di euro per aprire un Campus dedicato all’Additive Manufacturing a Le Haillan, vicino a Bordeaux. L’obiettivo è stato quello di creare un grande centro di eccellenza per la produzione additiva. Il campus, che ospita circa 200 addetti specializzati nel settore della stampa 3D, raggiunge le dimensioni di 12.500 metri. Al suo interno sono presenti almeno otto stampanti 3D con tecnologie a fusione a letto di polvere, attrezzature per la finitura, due forni per il trattamento termico, un microscopio elettrico a scansione, un laboratorio metallurgico e uno per le polveri. Safran si pone l’obiettivo di integrare la produzione additiva all’interno delle componenti dei suoi motori dall’1% al 25%. L’azienda ha prodotto finora più di 1.000 parti stampate in 3D e ha previsto di produrre, grazie a questa tecnologia, più di 4.000 componenti nel 2022 e oltre 8.000 nel 2023. Questo investimento di Safran rappresenta un ulteriore passo verso il rafforzamento della collaborazione tra aziende, istituti di ricerca e difesa europei, avvicinandoli ai massicci investimenti degli Stati Uniti che, ad oggi, continuano a dominare in questo settore.
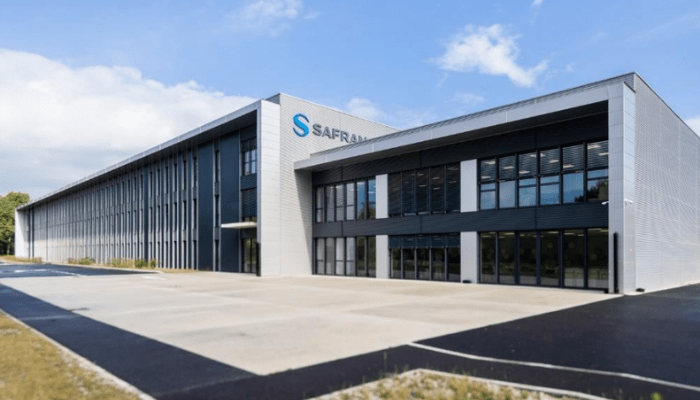
(Crediti fotografici: Safran)
Materialise sviluppa soluzioni di cabine stampate in 3D con i suoi partner
Materialise ha ampliato il suo ruolo nel settore della manutenzione, riparazione e revisione (MRO) aerospaziale e ora sta collaborando con Proponent, il più grande distributore aerospaziale del mondo, e Stirling Dynamics, un’organizzazione di progettazione leader certificata EASA 21.J, per sviluppare soluzioni di cabine stampate in 3D. Materialise ha già collaborato con Airbus ed EOS per produrre con successo parti stampate in 3D per l’aereo A350, tra cui circa 100 parti ignifughe. L’obiettivo della nuova partnership è ora quello di fornire parti di ricambio certificate stampate in 3D per l’industria aeronautica. Stirling Dynamics si concentrerà sul miglioramento dei progetti per le parti interne della cabina, mentre Materialise utilizzerà le sue capacità di produzione certificate. “Con la nostra esperienza congiunta, stiamo abbassando le barriere per l’adozione dell’AM nel settore dell’aviazione e forniamo soluzioni certificate per l’aftermarket”, spiega Jurgen Laudus, vicepresidente di Materialise Manufacturing. La collaborazione ha già dato vita a diverse soluzioni per la riparazione delle cabine degli aerei finalizzate a risolvere problemi specifici. Proponent, in particolare, ha svolto un ruolo chiave lavorando con gli OEM per offrire queste soluzioni in tutto il mondo.
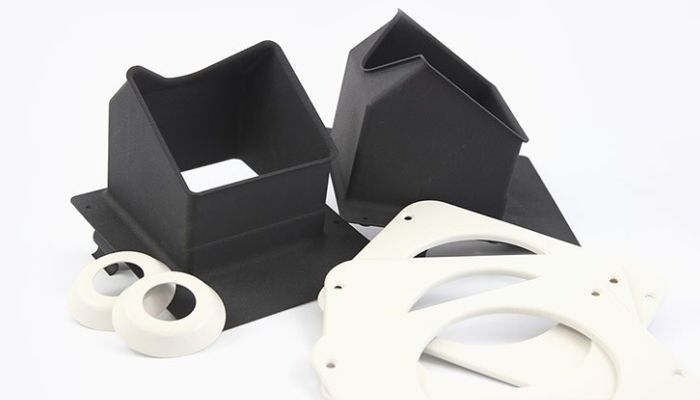
Pezzi di ricambio idonei al volo realizzati con il materiale ritardante di fiamma PA 2241 FR, offerto da Materialise in qualità certificata da Airbus. (Crediti footgrafici: Materialise)
Lufthansa usa la stampa 3D per creare le parti delle cabine dei propri aerei
Lufthansa Technik, uno dei principali fornitori di servizi di manutenzione, riparazione, revisione e modifica di aeromobili civili, ha dichiarato di servirsi della produzione additiva di polimeri sia per riprogettare parti specifiche di cabina, che per riprodurre parti convenzionali dell’aeromobile. Lufthansa, infatti, usa la stampa 3D per personalizzare le cabine VIP dei passeggeri. La produzione additiva viene usata però anche per rendere più robusti o leggeri i componenti convenzionali per le cabine degli aerei di linea. Per i loro velivoli hanno infatti già migliorato la funzione delle griglie di ventilazione, clip e coperture. Lufthansa prevede di servirsi sempre di più della produzione additiva, soprattutto per quello che riguarda l’uso del design bionico. Si tratta infatti dell’applicazione dei metodi biologici al design per le tecnologie 3D. Secondo l’azienda, gli aggiustamenti al design della cabina e la riduzione del peso realizzati con l’AM possono contribuire in modo significativo agli sforzi dell’industria aeronautica per una maggiore sostenibilità e una riduzione dell’impronta di carbonio.
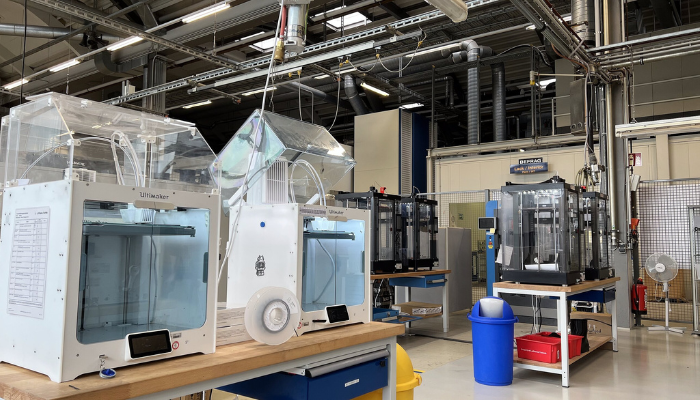
(Crediti fotografici: Lufthansa Group)
Il centro di stampa 3D di Airbus Helicopters
Airbus non è estranea alla stampa 3D: da anni l’azienda integra parti stampate in 3D nei suoi aerei. Spesso ha esternalizzato i servizi di produzione additiva, ma alla fine del 2023 Airbus Helicopters ha aperto un proprio centro di stampa 3D presso la sede di Donauwörth, in Germania, ampliando le proprie capacità interne relive all’AM. Il centro dispone di tre macchine per le parti in titanio, quattro per la plastica e una per l’alluminio. Airbus Helicopters utilizza la tecnologia per creare parti di produzione in serie, oltre a parti per prototipi come CityAirbus NextGen eVTOL e l’elicottero sperimentale ad alta velocità Racer. Stefan Thomé, direttore generale di Airbus Helicopters per la Germania, ha spiegato i vantaggi dell’utilizzo dell’AM. “Tra gli altri vantaggi, la stampa 3D può ridurre il peso dei componenti dell’aeromobile, con conseguente riduzione del consumo di carburante”, ha dichiarato Thomé. “Questo potenziale può portare benefici finanziari e contribuire a ridurre le emissioni di CO2 durante le operazioni”.
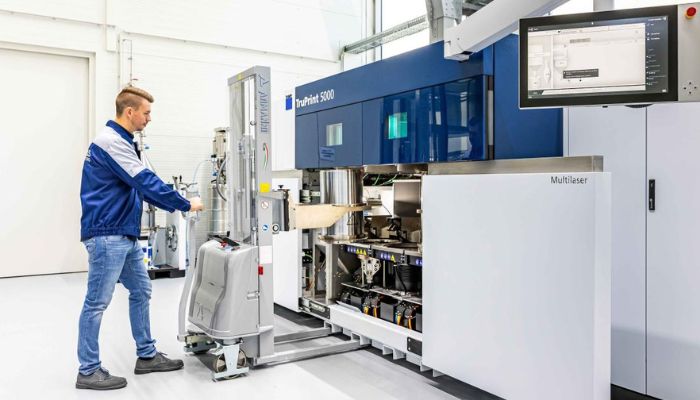
(Crediti fotografici: Airbus)
Rotori stampati in 3D per gli elicotteri Boeing Apache
L’azienda Boeing ha iniziato a testare un sistema completo di rotore principale stampato in 3D per l’elicottero d’attacco AH-64 Apache. Questo progetto mira a ridurre i tempi di attesa e a migliorare le catene di fornitura per i pezzi che vengono solitamente prodotti con i metodi di produzione tradizionali. Alla conferenza annuale dell’Associazione dell’esercito statunitense, Boeing e ASTRO America hanno presentato il loro primo componente stampato in 3D. Si tratta di un collegamento del rotore principale prodotto su una stampante 3D in metallo di grande formato. ASTRO, finanziata dal governo, ha lavorato a un contratto da 95 milioni di dollari per sviluppare capacità di produzione additiva per componenti di grandi dimensioni, come gli scafi dei carri armati. Un componente del rotore principale stampato in 3D viene prodotto in 8 ore, mentre per crearlo tramite i metodi di produzione tradizionali è necessario attendere fino ad un anno. Boeing intende effettuare degli stress test su larga scala su questi velivoli, il che potrebbe accelerare la riparazione degli aeromobili e ottimizzare la produzione dei componenti.
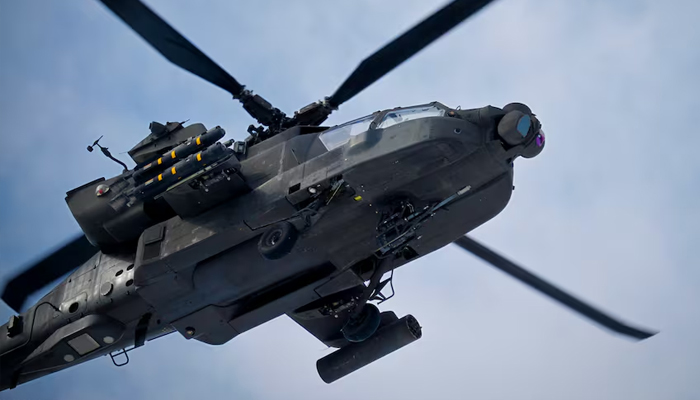
(Crediti fotografici: Boeing)
Finnair utilizza parti stampate in 3D negli aerei A320
Hai presente quei pannelli video posizionati sui sedili sopraelevati di alcuni aerei? Diverse compagnie aeree, tra cui la finlandese Finnair, li stanno progressivamente rimuovendo. La compagnia li ha recentemente sostituiti con pannelli di copertura stampati in 3D (ossia dei pannelli utilizzati per coprire gli “spazi vuoti” inutilizzati) nelle cabine dei suoi Airbus A320, per offrire un’alternativa leggera ai pesanti lettori video. L’azienda di produzione additiva AM Craft ha creato oltre 300 pannelli di copertura per rinnovare 17 aerei A320 di Finnair. Secondo Finnair, la stampa 3D dei pannelli ha contribuito a minimizzare le scorte in eccesso e a ridurre i costi associati alla catena di fornitura tradizionale. In aggiunta, Aviation Week ha riferito che i pannelli sono stati progettati per funzionare con le guide di montaggio già esistenti per una facile installazione. Inoltre, qualsiasi compagnia aerea che dispone di aerei A320 potrebbe beneficiare di questo progetto di stampa 3D perché i pannelli di copertura sono disponibili nel catalogo digitale di AM Craft.
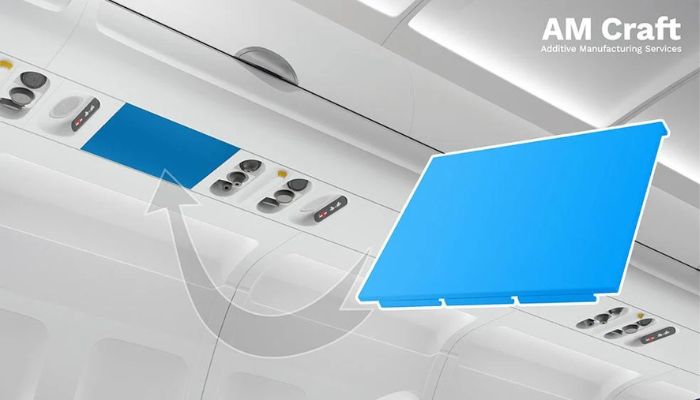
(Crediti fotografici: AM Craft)
Liebherr-Aerospace Lindenberg GmbH produce un albero flessibile stampato in 3D
Liebherr-Aerospace Lindenberg GmbH, un’azienda che realizza sistemi integrati per l’industria aeronautica, ha sviluppato un albero flessibile per applicazioni aerospaziali utilizzando la produzione additiva (ALM). Tradizionalmente, questo componente è composto da sette parti che devono essere assemblate tramite processi complessi. Grazie all’uso della stampa 3D, il processo di produzione è stato semplificato, riducendo così la necessità di manutenzione e rendendo la produzione meno complessa. L’albero flessibile, stampato in 3D con polvere di titanio, è stato approvato da Airbus e dall’EASA per la produzione in serie. Questo componente verrà integrato nel differenziale del sistema di flap dell’Airbus A350, dove trasmetterà movimenti rotatori a un sensore di posizione e compenserà eventuali errori di angolazione e allineamento tra il cambio e il sensore. L’approvazione dell’albero flessibile stampato in 3D dimostra che la produzione additiva è una tecnologia affidabile per migliorare la sostenibilità nel settore aerospaziale. “Questo componente dimostra come diverse funzionalità possano essere integrate in modo efficiente in una singola parte, aprendo la strada a future applicazioni più complesse dell’additive manufacturing“, spiega Svenja Pestotnik, responsabile della produzione additiva presso Liebherr-Aerospace Lindenberg GmbH.
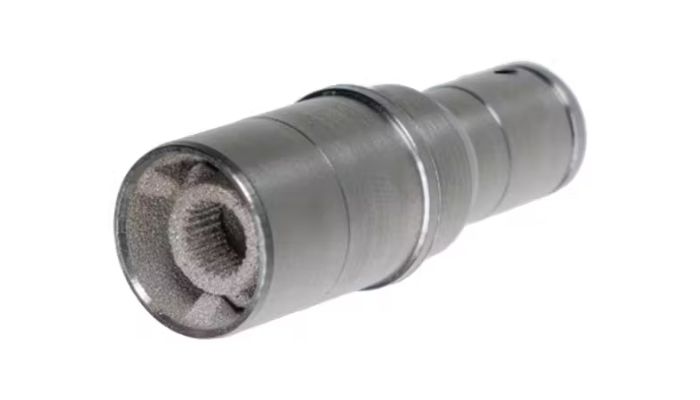
L’albero flessibile di Liebherr-Aerospace presenta una struttura complessa ed è prodotto utilizzando la tecnologia di stampa 3D in polvere di titanio. (Crediti fotografici: Liebherr-Aerospace Lindenberg GmbH)
LEAP e la produzione additiva
Quando si parla di aeronautica e stampa 3D è impossibile non menzionare il motore LEAP. Progettato da CFM International, una joint venture tra GE Aerospace e Safran Aircraft Engines, questo sistema di propulsione per aerei commerciali (come l’Airbus A320neo e il Boeing 737 MAX) è stato lanciato nel 2016 con l’obiettivo di migliorare l’efficienza energetica, ridurre le emissioni di CO2 e diminuire il rumore. A quasi dieci anni dal suo debutto, LEAP sembra aver mantenuto le promesse, almeno secondo CFM. Ma ciò che cattura davvero il nostro interesse è il contributo della stampa 3D nella sua progettazione. Diverse componenti del motore, tra cui le carenature della turbina, le punte degli ugelli e gli iniettori di carburante, sono state realizzate grazie alla produzione additiva, utilizzando un processo di fusione laser a letto di polvere.
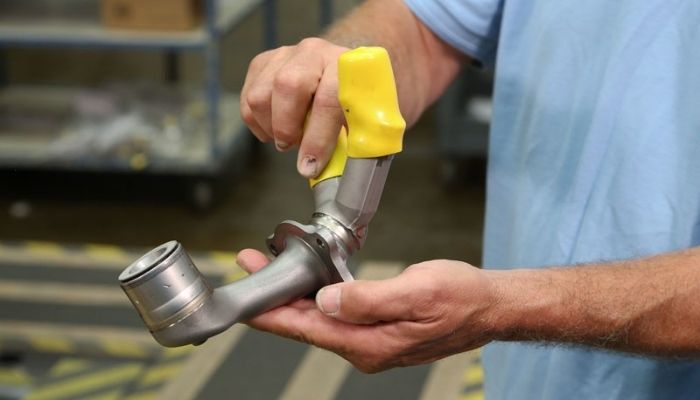
(Crediti fotografici: GE)
I Marines rendono più efficiente la manutenzione degli alesatori degli F-35B Lightning II
L’obiettivo del Marine Aviation Logistics Squadron 13 è quello di fornire supporto logistico al Marine Aircraft Group, come la fornitura di personale e parti di ricambio. Tuttavia, nel luglio 2024, il MALS-13 ha dovuto affrontare una carenza critica di alesatori per gli sqadroni del F-35B Lightning II. Si tratta di strumenti di taglio di precisione essenziali per la manutenzione dell’aviazione. Gli alesatori tradizionali erano infatti costosi e il MALS-13 ne disponeva in quantità insufficienti a causa dei lunghi tempi di approvvigionamento. Grazie alla produzione additiva hanno creato una soluzione on-demand, sviluppando degli alesatori ad alte prestazioni. In questo modo hanno ridotto non solo i costi di manutenzione dell’oltre il 50%, ma anche i tempi di approvvigionamento. I pezzi, infatti, sono passati dall’essere disponibili in tre mesi all’essere prodotti in giornata. Per ricreare gli alesatori mancanti sono state acquistate due stampanti 3D industriali Markforged X7 che hanno permesso al MALS-13 di produrre i componenti di livello aerospaziale “in casa”, eliminando la dipendenza da fornitori esterni.
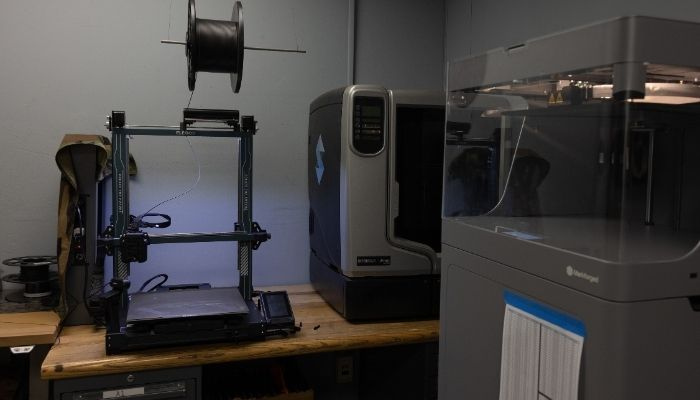
(Credits fotografici: Lance Cpl. Elizabeth Gallagher)
Il drone Titan Falcon
Parlando di aeronautica, è impossibile non menzionare i velivoli senza pilota, più noti come droni. Indipendentemente dall’impiego, che sia per esplorazione, in ambito militare o per la ricerca scientifica, questi dispositivi sono sempre più diffusi e spesso integrano componenti realizzate con la stampa 3D. Un esempio significativo è il Titan Falcon, sviluppato da Titan Dynamics. Questo drone vanta una batteria con 6 ore di autonomia e un raggio d’azione di 400 chilometri, permettendogli di coprire vaste aree. Equipaggiato con una telecamera, si è rivelato una soluzione efficace per il monitoraggio dei campi di battaglia, essendo stato impiegato anche durante il conflitto tra Ucraina e Russia. Per quanto riguarda la produzione additiva, Titan Dynamics mantiene riservati i dettagli su materiali e tecnologie utilizzate. Ciò che è certo, però, è che l’impiego della stampa 3D ha permesso all’azienda di ridurre i tempi di consegna e semplificare le iterazioni progettuali.
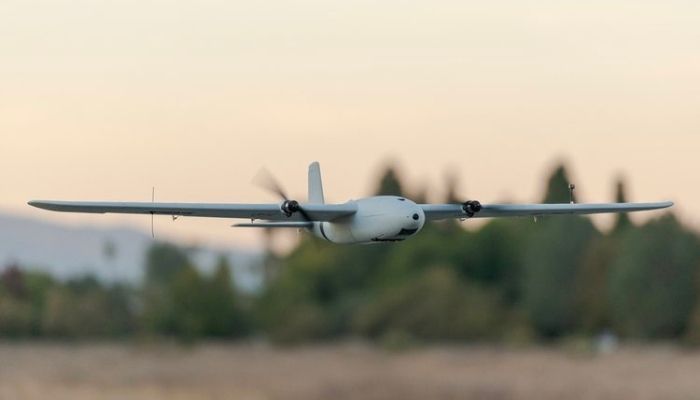
(Crediti fotografici: Titan Dynamics)
Conflux produce scambiatori di calore utilizzando la stampa 3D in metallo
La missione di Conflux è quella di contribuire all’aviazione moderna utilizzando la stampa 3D. Ciò comporta il compito di garantire maggiori prestazioni e affidabilità. Conflux produce scambiatori di calore per aeromobili utilizzando la stampa 3D in metallo per realizzare geometrie più complesse e ottimizzare così le prestazioni degli scambiatori di calore. Ciò contribuisce alle prestazioni complessive dell’aereo. Da un lato, il peso complessivo può essere ridotto grazie a componenti leggeri, dall’altro, una gestione efficiente del calore ha un impatto diretto sulle prestazioni e sull’autonomia di un aereo.
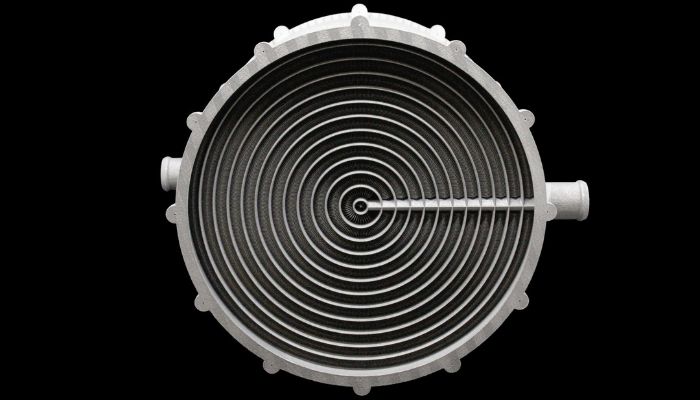
(Crediti fotografici: Conflux)
Cabina di pilotaggio di un elicottero stampata in 3D per un simulatore di volo completo
Nel 2024, Murtfeldt Additive Solutions ha stampato una cabina di pilotaggio modulare per elicottero per conto di Reiser Simulation and Training GmbH. A questo scopo, Murtfeldt ha utilizzato diversi sistemi della stampante 3D di grande formato Queen 1 di Q.BIG 3D. Utilizzando il processo Variable Fused Granulate Fabrication (VFGF), i singoli componenti potrebbero essere stampati in 3D e poi assemblati rapidamente. Il tempo di stampa più lungo per un singolo componente è stato di 100 ore, mentre il tempo di produzione totale è stato di poco più di un mese. Con dimensioni di 2.260 x 1.780 x 17,05 mm, l’abitacolo pesa “solo” 200 kg. In questo progetto, la stampa 3D con pellet di plastica si è rivelata preziosa per raggiungere obiettivi di costruzione leggera e produrre in modo più economico. Poiché la produzione tradizionale richiede molti utensili per dare vita a un progetto di questo tipo, i costi potrebbero essere ridotti grazie alla stampa 3D. Inoltre, i prezzi dei pellet per la stampa di grande formato sono molto più convenienti di quelli del filamento.
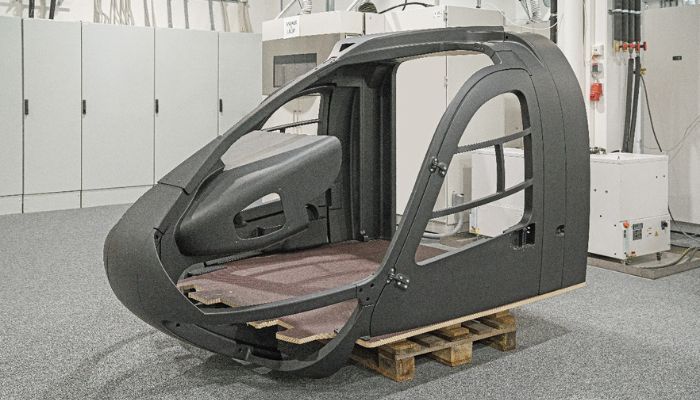
(Crediti fotografici: Q.BIG 3D)
La partnership tra BEAMIT e Leonardo Aircraft per la produzione in serie con la produzione additiva
Il gruppo italiano Leonardo è uno dei principali a livello internazionale nella realizzazione di capacità tecnologiche in ambito Aerospazio, Difesa & Sicurezza. L’azienda è partner tecnologico di Governi, Amministrazioni della Difesa, Istituzioni e imprese. Da tempo è noto l’utilizzo dell’additive manufacturing nelle attività di Leonardo. Negli ultimi anni, in particolare, per quanto riguarda la divisione Aircraft, Leonardo ha rinnovato una partnership con il service BEAMIT per per la produzione in serie di diversi componenti con tecnologia Additive Manufacturing in metallo, che sarà attiva almeno fino al 2028. Ad oggi Leonardo Aircraft ha ora più di 100 parti qualificate con BEAMIT che sono attualmente installate su velivoli chiave come M345, M346 e C27J.
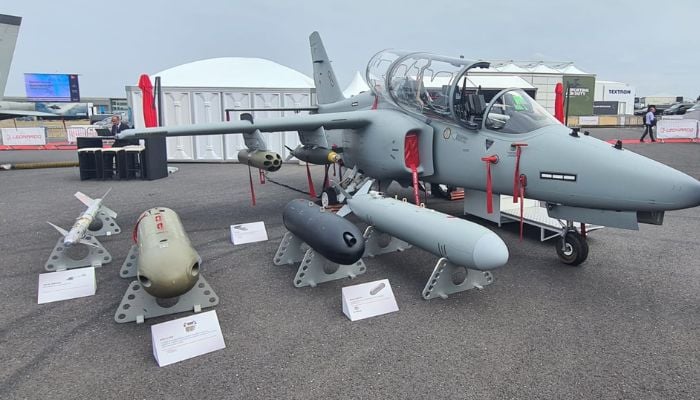
Il Leonardo M-345. (Crediti fotografici: Italia Vola)
Il progetto MIMOSA per ottimizzare i velivoli con la stampa 3D
Il progetto europeo MIMOSA, che vede la partecipazioni di vari partner istituzionali e aziendali europei, è stato lanciato nel 2022 e ha l’obiettivo di trasformare la costruzione dei velivoli grazie all’uso congiunto di materiali compositi e metalli stampati in 3D. Il progetto mira a supportare le prossime generazioni di velivoli, che dovranno necessariamente seguire criteri di produzione a ridotto impatto ambientale e minore necessità di materie prime. Lo studio si basa sulla realizzazione di strutture multimateriale composte da leghe metalliche e materiali compositi senza elementi intermedi, mediante l’integrazione di manifattura additiva metallica, trattamenti superficiali al plasma e fibre di carbonio. A fine servizio, le strutture realizzate con la tecnologia MIMOSA potranno essere rigenerate grazie a un processo di “atomizzazione”, riducendo gli scarti e diventando materia prima “secondaria” per gli stessi processi di additive manufacturing.
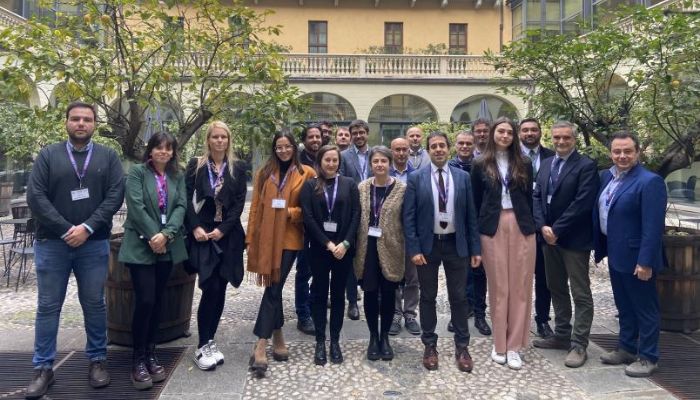
Il team del progetto MIMOSA (Crediti fotografici: Politecnico di Torino)
Cosa ne pensi del futuro della stampa 3D nel settore areonautico? Se ti interessa l’argomento, non perderti la nostra pagina esclusiva dedicata a stampa 3D nel settore aerospaziale e della difesa. Lascia un commento sui nostri canali Facebook, LinkedIn e YouTube. Segui tutte le novità dal mondo della stampa 3D nella nostra Newsletter settimanale!