Produzione di massa e stampa 3D: a che punto siamo?
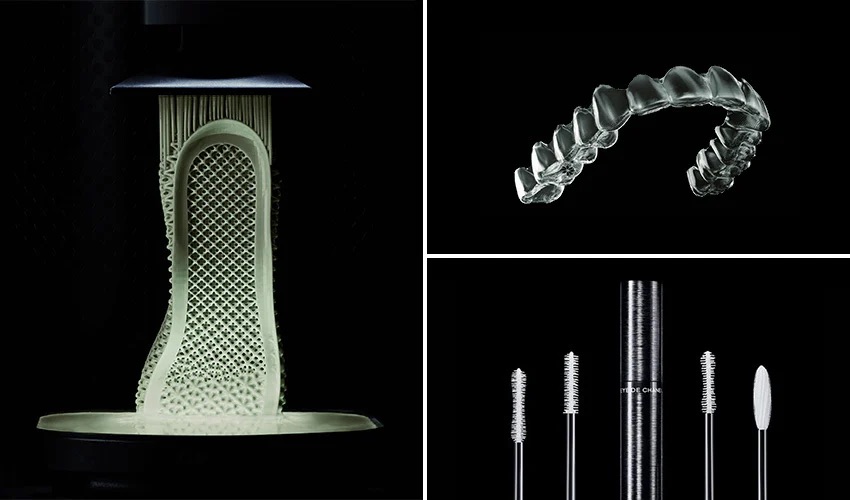
La stampa 3D da tempo non viene più utilizzata esclusivamente per lo sviluppo di prototipi, ma viene impiegata anche nella produzione di parti finali. Sebbene la sua praticabilità nella produzione di massa e in serie venga talvolta messa in discussione a causa dei costi e dei tempi di produzione, questa percezione sta ora cambiando. Sempre più aziende dimostrano che è possibile integrare la produzione massa e la stampa 3D combinando qualità, personalizzazione ed efficienza nella realizzazione di oggetti in grandi volumi. Dai componenti industriali agli articoli personalizzati, la stampa 3D si sta affermando come una vera e propria soluzione per la produzione su larga scala. Abbiamo quindi esplorato alcuni casi di studio in cui la produzione additiva è stata determinante per la creazione di migliaia di pezzi prodotti in serie, dimostrando il suo potenziale e sfidando i metodi di produzione tradizionali.
Adidas e Carbon: produzione di massa di scarpe da ginnastica
Nel 2016 Adidas ha stretto una partnership con Carbon per rivoluzionare il modo in cui possono essere realizzate le scarpe da corsa. Nel 2017 le due aziende hanno rilasciato Futurecraft 4D: la rivoluzionaria intersuola multizona prodotta in una singola sessione di stampa e dotata di un’innovativa struttura reticolare. Insieme, hanno lanciato la produzione di 100.000 paia di scarpe Futurecraft 4D con suola centrale stampata in 3D. Futurecraft 4D è stata sguita da AlphaEDGE nel 2018 alla quale sono stati aggiunti, rispetto al modello precedente, spessore ai montanti direttamente sotto il tallone, il punto in cui il corridore mette più pressione durante la corsa. Nel 2021 è stata lanciata la l’Adidas 4DFWD, la terza generazione delle intersuole 4D, che sfrutta la proprietà fisica dell’anisotropia per rendere la scarpa comoda e funzionale per la corsa. Sempre frutto della collaborazione tra Adidas e Carbon, la nuova intersuola è realizzata con il processo Carbon DLS™ e sfrutta l’elastomero EPU 44, una versione aggiornata del precedente EPU 41 utilizzato per la Futurecraft 4D. Questo materiale di nuova generazione è altamente resiliente, resistente agli strappi e più sostenibile, grazie a una formulazione a base biologica al 40%. Adidas 4DFWD è la più recente evoluzione del marchio che unisce innovazione tecnologica, design avanzato e sostenibilità su scala industriale.
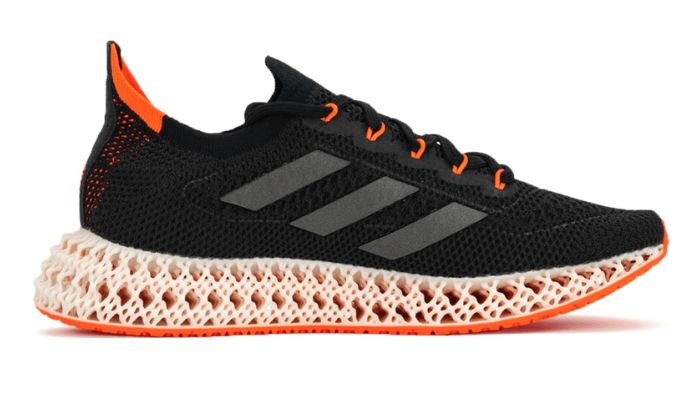
(Crediti fotografici: Carbon)
Align Technology: la stampa 3D per la produzione di massa di dispositivi dentali
Quando si parla di produzione di massa nella stampa 3D, Align Technology rappresenta un caso emblematico. L’azienda americana, nota per aver dato vita a Invisalign, è specializzata in soluzioni ortodontiche personalizzate realizzate tramite stampa 3D. Da sempre promotrice dell’innovazione nel settore, ha investito sia nella stampa che nella scansione 3D: basti pensare all’acquisizione del produttore di scanner intraorali iTero nel 2011, seguita da quella del produttore di stampanti 3D a polimeri Cubicure nel 2024. Inoltre, vanta una collaborazione di lunga data con 3D Systems. La stampa 3D viene impiegata da Align Technology per una vasta gamma di prodotti, dagli stampi per i famosi allineatori fino all’espansore palatale, il primo dispositivo ortodontico stampato direttamente in 3D dall’azienda. Con una produzione che può arrivare fino a un milione di allineatori al giorno, insieme alla produzione di centinaia di migliaia di stampi creati quotidianamente, è evidente l’enorme portata di questa tecnologia. Un esempio perfetto di come la stampa 3D possa coniugare personalizzazione su larga scala e produzione industriale.
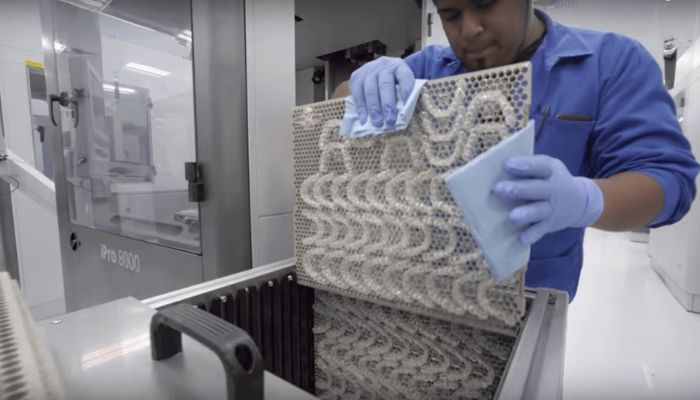
(Crediti fotografici: Align Technology)
Chanel: stampa 3D degli scovolini per mascara high-tech
Ti ricordi forse del mascara Volume Révolution di Chanel: lanciato nel 2018, si è distinto dagli altri suoi concorrenti per essere dotato di uno scovolino stampato in 3D. All’epoca se n’era parlato molto perché si trattava di una vera produzione su larga scala. Infatti, Erpro 3D Factory, la startup responsabile della stampa degli scovolini, affermava di poter produrre 250.000 pezzi a settimana grazie a una quindicina di macchine. Da quel progetto, le due aziende hanno lanciato E.Y.E, un servizio su misura di mascara stampati in 3D. Concretamente, grazie a un’app su tablet, puoi scegliere il tuo scovolino tra 10 modelli diversi, in base alle tue esigenze e ai tuoi desideri in fatto di trucco. Lo scovolino viene poi stampato in 3D in PA 11. Non si sa con precisione quanti scovolini siano stati stampati finora, ma una cosa è certa: questo esempio dimostra chiaramente tutti i vantaggi della produzione additiva e il fatto che è possibile unire personalizzazione a produzione di massa!
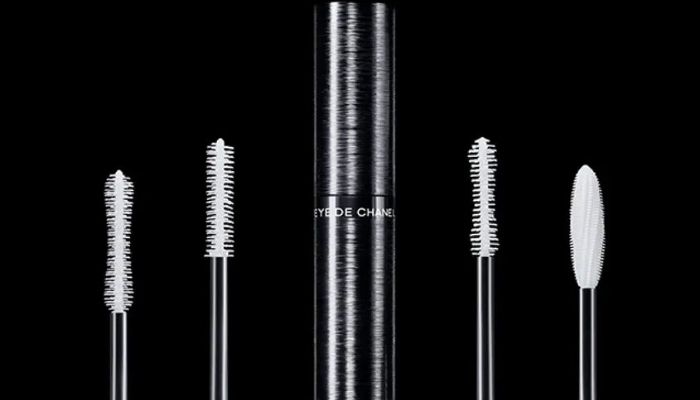
(Crediti fotografici: ERPRO / Chanel)
GE Additive: componenti per turbine stampati in 3D
GE Aviation ha raggiunto diverse pietre miliari nella produzione in serie con additive manufacturing. Lo stabilimento GE Aviation di Asheville, in Carolina del Nord, ha prodotto negli anni più di 100.000 componenti per turbine realizzati in materiali compositi a matrice ceramica (Ceramic Matrix Composite – CMC), mentre lo stabilimento di Auburn, Alabama, ha prodotto più di 100.000 componenti per ugelli prodotti con produzione additiva.
Il CMC è un materiale avanzato contenente fibre di carburo di silicio che pesa un terzo delle leghe metalliche tradizionali e resiste a temperature doppie, contribuendo a migliorare l’efficienza termica del motore, riducendo così il consumo di carburante e le emissioni di carbonio. Lo stabilimento di Asheville è il primo sito di produzione in serie con produzione additiva del settore aeronautico per componenti di motori a reazione realizzati con CMC, avviato nel 2014. Il sito di Auburn ha iniziato a produrre ugelli per carburante nel 2015 ed è stato il primo sito di produzione in serie del settore per la produzione di componenti di motori aeronautici mediante produzione additiva.
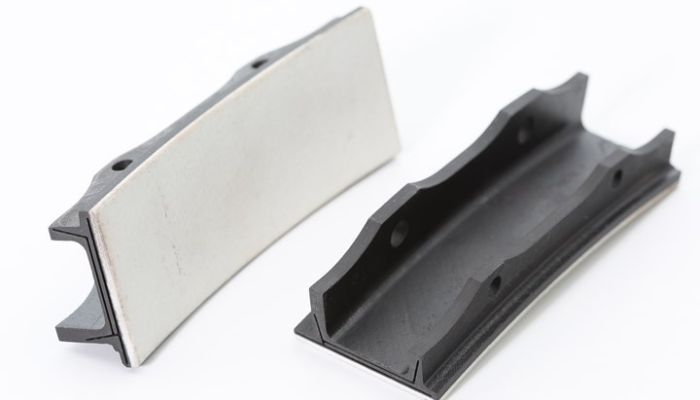
Componenti per turbine stampati in 3D in CMC (Crediti fotografici: GE Aviation)
Photocentric: i badge per Badgemaster stampati in 3D
Un altro esempio dell’uso della stampa 3D per la produzione di massa è la collaborazione tra l’azienda britannica Badgemaster e il produttore di stampanti 3D Photocentric. Di fronte all’urgente necessità di produrre badge personalizzati in tempi brevi, Badgemaster si è rivolta alla tecnologia di stampa 3D a resina di Photocentric, utilizzando le sue macchine LC Magna. Questo metodo ha permesso di produrre 30.000 parti finali in modo rapido e di qualità, senza la necessità di stampi o attrezzature tradizionali. La scelta di questa tecnologia è stata in parte dovuta alle sfide logistiche derivanti dalla pandemia, che hanno limitato la produzione convenzionale. Questa collaborazione evidenzia il potenziale della manifattura additiva nel rispondere alle richieste industriali, offrendo soluzioni rapide, flessibili ed efficienti, anche in scenari di forte domanda.
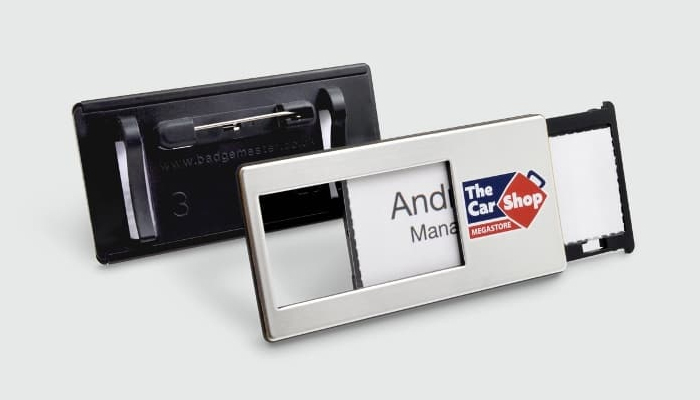
(Crediti fotografici: Badgemaster)
Cobra: mazze da golf create con la stampa 3D in metallo
L’azienda ha presentato il primo putter prodotto in serie con la tecnologia HP Metal Jet, inaugurando una nuova era nelle attrezzature da golf. L’obiettivo è quello di combinare innovazione e produzione in serie, mantenendo i costi contenuti. Da diversi anni Cobra Golf esplora le possibilità offerte dalla produzione additiva per progettare delle mazze da golf sempre più performanti. Grazie alla tecnologia HP Metal Jet, i suoi ingegneri godono di una libertà di progettazione senza precedenti, che consente loro di immaginare strutture impossibili da produrre con metodi tradizionali. Un tempo limitata ai prototipi, la stampa 3D in metallo sta ora raggiungendo qualità e velocità sufficienti per la produzione su larga scala. In collaborazione con HP, Cobra ha potuto accelerare lo sviluppo delle sue mazze e renderle accessibili al grande pubblico.
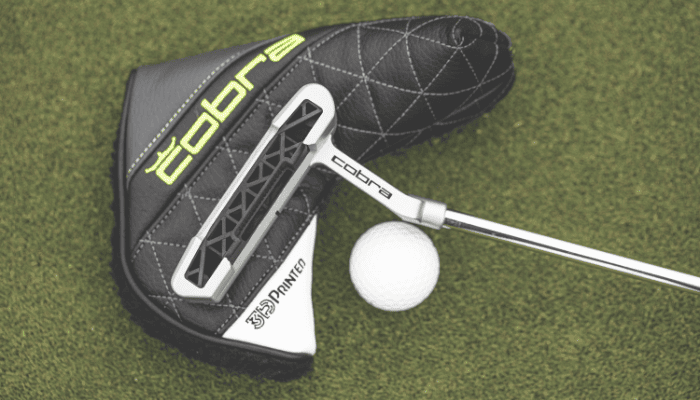
(Crediti fotografici: HP)
Stryker: le protesi per il ginocchio in titanio stampate in 3D
Un’altra iniziativa che unisce la produzione additiva a quella di massa arriva dal settore medicale. Dal 2013, l’azienda irlandese Stryker ha migliorato la sua produzione realizzando circa 2 milioni di protesi servendosi delle tecnologie di stampa 3D. Per farlo, ha sviluppato un materiale proprietario chiamato Tritanium, una lega di titanio progettata appositamente per la stampa, con cui ha prodotto sia una portesi per il ginocchio senza cemento, chiamata Triathlon Tritanium, che tre diverse protesi spinali Tritanium. Ma come funziona il sistema Triathlon Tritanium? Questa protesi combina un design avanzato con una tecnologia di fissaggio biologico altamente porosa, progettata con strumenti SOMA e realizzata grazie alla tecnologia additiva proprietaria di Stryker. Tramite l’analisi del ciclo di vita della protesi al ginocchio, l’azienda ha evidenziato numerosi vantaggi derivanti dall’utilizzo della manifattura additiva, sia in termini economici che di risparmio di risorse materiali e ambientali. Ma non finisce qui. Stryker è entrata a far parte dell’Additive Green Manufacturing Trade Association, con il fine di promuovere l’impiego della stampa 3D nell’industria per adottare delle scelte produttive sempre più sostenibili.
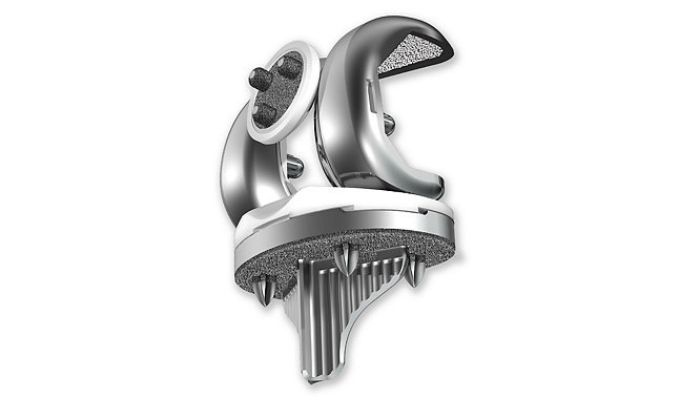
Nell’immagine può essere osservato il modello Triathlon Tritanium, la protesi per il ginocchio non cementata. (Crediti fotografici: Stryker)
Bosch Advanced Ceramics: strumenti laparoscopici stampati in 3D
Non è un segreto che la ceramica sia diventata un attore importante nel settore della produzione additiva. Bosch Advanced Ceramics ha saputo sfruttare al meglio la combinazione tra ceramica tecnica e stampa 3D per incrementare la produzione di componenti medicali ad alta precisione. Tra questi, spiccano le guaine isolanti, elementi fondamentali negli strumenti laparoscopici impiegati nella chirurgia mini-invasiva. Dopo una fase di campionamento riuscita con successo, l’azienda è riuscita a produrre 1.400 pezzi in un singolo lotto, una capacità produttiva che potrebbe coprire una domanda annuale fino a 20.000 unità. La realizzazione di questi manicotti isolanti ha rappresentato una sfida ingegneristica notevole, viste le dimensioni estremamente ridotte: un diametro esterno di appena 1,3 mm e pareti sottili solo 90 micron. Per raggiungere questo livello di dettaglio e precisione, Bosch Advanced Ceramics ha fatto ricorso alla tecnologia LCM (Lithography-based Ceramic Manufacturing) di Lithoz, un processo basato sulla fotopolimerizzazione strato per strato che consente di ottenere geometrie complesse con un controllo di qualità elevatissimo.
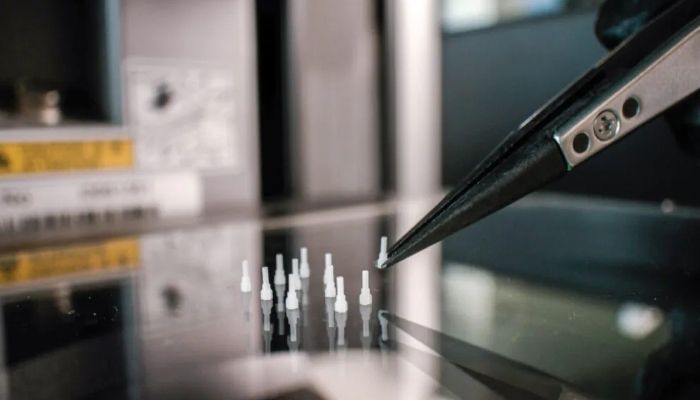
Componenti in ceramica stampati in 3D pronti per essere utilizzati negli strumenti laparoscopici (Crediti Fotografici: Lithoz)
Cosa ne pensi della stampa 3D nella produzione di massa? Se ti interessa l’argomento, non perderti la nostra pagina esclusiva dedicata alla stampa 3D nel settore automotive e trasporti. Lascia un commento sui nostri canali Facebook, LinkedIn e YouTube. Segui tutte le novità dal mondo della stampa 3D nella nostra Newsletter settimanale!