Il primo edificio antisismico stampato in 3D: il progetto avanguardistico di Enel Green Power e l’Univeristà Federico II di Napoli
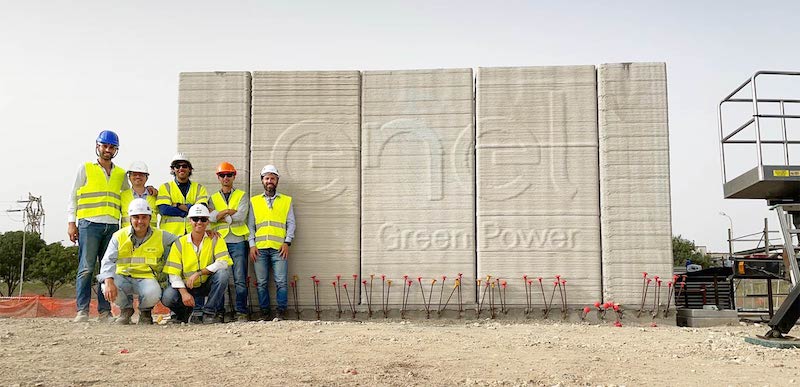
Una delle sfide maggiori che l’edilizia italiana è costretta ad affrontare ogni giorno è senza dubbio quella dell’impatto dei terremoti sul territorio nazionale. Negli ultimi trent’anni, la Rete Sismica Nazionale ha registrato oltre 190.000 eventi sismici di varia magnitudo, un dato che mette in luce la vulnerabilità del nostro paesaggio. A fronte di queste problematiche, Enel Green Energy e l’Università Federico II di Napoli, insieme alla collaborazione dello spin-off Etesias, hanno costruito il primo edificio antisismico permanente realizzato in stampa 3D. Si tratta di un evento rivoluzionario che potrebbe cambiare radicalmente le sorti non solo dell’edilizia antisismica, ma dell’intero settore edile.
La collaborazione tra il team di ingegneria di Enel Green Power e l’Università Federico II di Napoli è incominciata circa due anni fa, con l’obiettivo di sviluppare una nuova teoria innovativa per il calcolo strutturale degli elementi destinati alla stampa 3D. Questa teoria è stata inizialmente testata in laboratorio, approfondita attraverso simulazioni numeriche e infine collaudata in cantiere. Il risultato è stato poi presentato al Genio Civile e condiviso con il Consiglio Superiore dei Lavori Pubblici: l’approvazione del progetto è stata concessa l’11 gennaio 2024.
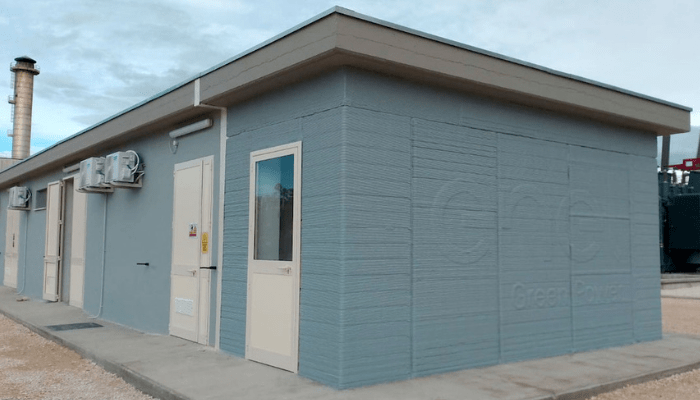
Foto dell’edificio realizzato tramite l’impiego dell’additive manufacturing. Crediti per la foto: Enel Green Power.
ll primo edificio in calcestruzzo con autorizzazione sismica
Il progetto nato dalla collaborazione delle due realtà, aziendale e universitaria, prevedeva la realizzazione di una piccola struttura in calcestruzzo delle dimensioni di circa 15 metri quadrati, sostenuto da due elementi di fondazione che supportano le attrezzature elettriche. L’edificio è stato progettato per far parte di una sottostazione dell’impianto BESS, acronimo di Battery Energy Storage System, ossia il sistema di accumulo delle energia prodotta dalla centrale elettrica Enel di Montalto di Castro, in provincia di Viterbo. Grazie all’impiego dell’additive manufacturing, la struttura portante è stata stampata quasi interamente all’interno della centrale elettrica, mentre le fondazioni sono state create presso l’Area industriale di Volla, nel napoletano, durante il febbraio del 2024.
La struttura non vanta soltanto il primato di essere il primo edificio antisismico in Italia realizzato con l’additive manufacturing. È infatti la prima struttura in calcestruzzo creata tramite l’uso della stampa 3D a ricevere l’autorizzazione sismica dal Genio Civile, un riconoscimento finora riservato esclusivamente a costruzioni progettate con il metodo tradizionale della produzione sottrattiva. La struttura di stoccaggio ha aperto la strada a una nuova metodologia costruttiva, che può essere applicata anche a futuri progetti del settore energetico e industriale.
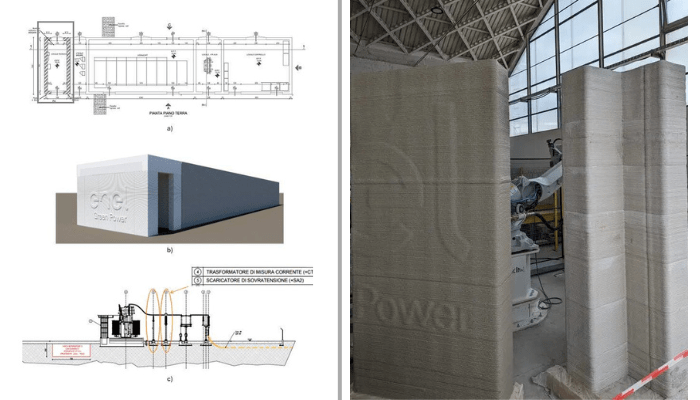
Sulla sinistra è possible osservare la disposizione in pianta dell’edificio di controllo, il render dell’edificio che sarà realizzato tramite l’impiego dell’additive manufacturing, le fondazioni destinate a contenere i BESS. Sulla destra è presente una foto delle pareti che andranno a comporre la struttura. Crediti per le foto: Ingenio#calcestruzzo.
Tuttavia, il cammino verso la realizzazione del progetto non è stato privo di ostacoli. Infatti, Costantino Menna, professore associato di Tecnica delle Costruzioni dell’Università di Napoli Federico II, ritiene che le difficoltà principali legate all’impresa si siano manifestate “in particolar modo per quello che riguarda il controllo del processo di stampa e la determinazione delle proprietà fisiche e meccaniche dei materiali utilizzati. Una delle principali difficoltà è stata la capacità di produrre, in modo consistente e in continuo, elementi alti fino a tre metri, come nel caso delle pareti dell’edificio. Questo ha richiesto un controllo preciso del processo di stampa per garantire stabilità allo stato fresco e, allo stesso tempo, integrità strutturale allo stato indurito”.
Il lavoro in cantiere
Per edificare la struttura atta a contenere i BESS si è impiegato un braccio robotico che ha depositato circa 2,5 chilometri di cemento, strato dopo strato, ottenendo un blocco di parete di circa 3 metri di altezza e 1,5 metri di larghezza. Una quantità simile di materiale è stata utilizzata per ciascun plinto a forma di tronco, con una base di 1,40 per 1,40 metri e un’altezza di circa un metro. Ogni blocco di cemento è stato lasciato asciugare nella stazione di Volla, successivamente i pezzi pronti per l’assemblaggio sono stati trasportati alla centrale di Montalto. Il tetto è stato invece realizzato in cantiere.
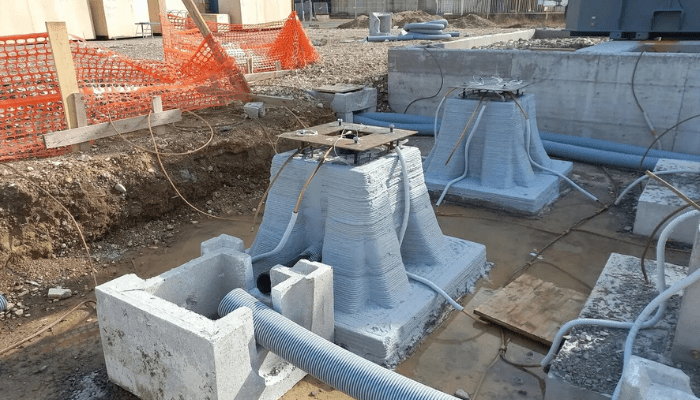
I piloni destinati a sostenere la struttura. Crediti per la foto: Enel Green Power.
Tra i numerosi vantaggi dell’uso della stampa 3D nel settore edilizio, uno dei più rilevanti riguarda la sicurezza del personale. In merito si esprime l’ingegnere Martina Palomba, membro del team di ricerca impegnato nello studio della stampa 3D per Heidelberg Materials: “grazie all’alto grado di digitalizzazione, [la stampa 3D] consente di aumentare la sicurezza in cantiere e di costruire strutture con forme complesse e dettagli personalizzati che sarebbero difficili o impossibili da realizzare con metodi tradizionali”.
L’innovativo calcestruzzo sostenibile i.tech 3D N
Per il progetto finanziato da Enel Green Power è stato utilizzato il calcestruzzo i.tech 3D N brevettato da Heidelberg Materials, ex Ital Cementi, depositato grazie all’uso di un braccio robotico mobile. Il composto è stato progettato specificamente per soddisfare i requisiti di stampa necessari appunto per l’additive manufacturing. La malta, infatti, è composta da sabbie e additivi selezionati che migliorano l’edificabilità del materiale durante il processo di stampa, garantendo che gli elementi estrusi dal braccio meccanico mantengano la forma originale prevista nel modello virtuale. Inoltre, il calcestruzzo di Heidelberg Materials è interamente riciclabile e composto solo da elementi minerali, con un legante che presenta un’impronta di carbonio ridotta di circa il 55% rispetto al cemento tradizionale. Il cemento i.tech 3D N offre quindi un’eccellente lavorabilità e sviluppa una resistenza ottimale rendendolo particolarmente indicato per riprodurre elementi rettilinei, curvi, strutturali e non strutturali. Gli elementi stampati possono essere sia in forma di prefabbricati (off-site) che gettati in opera (on-site). Sebbene attualmente questo calcestruzzo sia più costoso rispetto a quello tradizionale, questa tecnologia permette di accelerare il processo di costruzione consentendo di ridurre i tempi di almeno il 50%. Inoltre, la stampa 3D elimina la necessità di impiegare le casseforme, ossia le strutture temporanee tradizionalmente utilizzate per contenere il calcestruzzo fino alla sua solidificazione.
La stampa 3D nelle costruzioni: vantaggi e prospettive future
L’uso della stampa 3D nel settore edile offre numerosi vantaggi. Innanzitutto, la stampa 3D del calcestruzzo consente di ideare forme complesse che sarebbero difficili, se non impossibili, da realizzare con i metodi tradizionali. Permette inoltre di servirsi di meno materiale, riducendo così l’impatto ambientale e migliorando la sostenibilità. Si stima che l’impiego del calcestruzzo nelle costruzioni sia responsabile di una percentuale compresa tra il 4 e l’8% delle emissioni totali di CO2 prodotte dall’uomo. Inoltre, permette di ottenere risultati quasi irraggiungibili con le metodologie tradizionali. La struttura antisismica, frutto della collaborazione tra Enel Green Power e l’Università Federico II di Napoli, ha infatti ricevuto una sovvenzione dal Centro di Competenza ARTES4.0. Questa sovvenzione, finanziata attraverso i fondi del PNRR, è riservata ai servizi qualificati per promuovere l’innovazione nelle imprese.
In soli due anni il progetto è riuscito non solo a prendere forma a livello teorico, ma anche a concretizzarsi, spianando così la strada a nuovi progetti. A riprova di questo successo è stato avviato un nuovo programma denominato OM3GA, ecOManufactured 3D Printing Foundations, in collaborazione con WASP, una delle principali aziende nel settore della produzione di macchine per la stampa 3D. Il progetto vede anche la collaborazione di Materias, azienda specializzata in materiali e tecnologie avanzate, e del Sustainability Management Lab della Scuola Superiore Sant’Anna di Pisa. L’obiettivo, simile a quello del progetto di Montalto, è la realizzazione di fondazioni per apparecchiature di sottostazione, stampate in 3D grazie a una fabbrica temporanea mobile.
Questi risultati dimostrano chiaramente che la tecnologia dell’additive manufacturing ha il potenziale per rivoluzionare il modo in cui concepiamo e costruiamo le infrastrutture del futuro. L’innovazione della stampa 3D non solo affronta con successo le sfide reali, ma offre anche soluzioni per un futuro più sostenibile a livello ambientale, con un significativo risparmio economico e un miglioramento della sicurezza per i lavoratori nel settore edile.
Anche tu come noi pensi che la stampa 3D possa rivoluzionare il settore dell’edilizia? Faccelo sapere lasciando un commento sui nostri canali social Facebook, Linkedin e YouTube! Non dimenticare di iscriverti alla nostra Newsletter per ricevere tutte le notizie dall’evento direttamente nella tua casella di posta!
*Crediti per la foto di copertina: Enel Green Power