PEEK vs PEKK: quale materiale sceglierere?
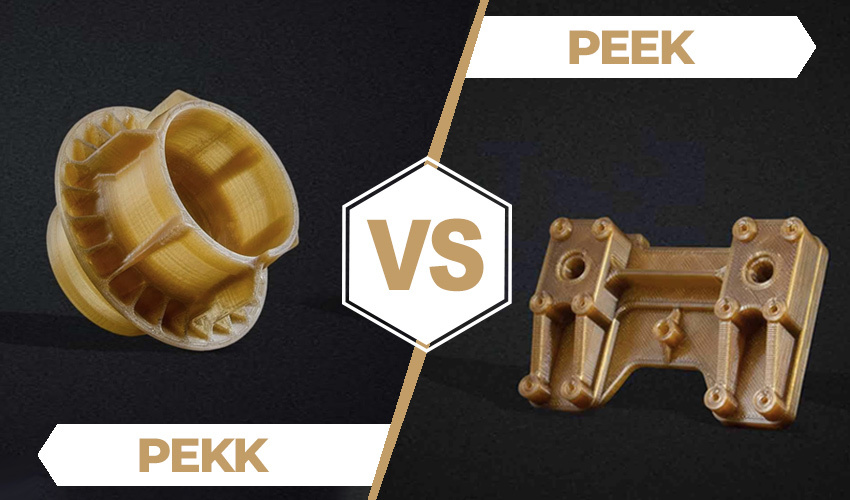
I materiali utilizzati nella produzione additiva sono una componente chiave del processo, in quanto conferiscono al pezzo finale le proprie proprietà chimiche e caratteristiche meccaniche. Oggi il mercato offre un’ampia scelta di materiali, dai polimeri ai metalli, alle ceramiche e agli inchiostri organici. Se consideriamo le materie plastiche, esse sono molto numerose e possono essere più o meno complesse da stampare. Che si tratti di filamenti, resine o polveri, ognuno ha le sue specificità. Oggi ci concentreremo sulla categoria dei polimeri ad alte prestazioni e più precisamente sulla famiglia dei poliarileterchetoni (PAEK). Due materiali di questo gruppo sono sempre più utilizzati dall’industria: PEEK e PEKK.
Generalmente utilizzati nella cosiddetta industria manifatturiera tradizionale (che include tecniche come lo stampaggio a iniezione, la lavorazione meccanica e tanti altri), il PEEK e il PEKK presentano entrambi caratteristiche termiche interessanti e sono noti per la loro resistenza. Spesso paragonati ai metalli, da qualche anno sono compatibili con alcuni processi di produzione additiva, tra cui la modellazione a deposizione fusa (FDM) e la sinterizzazione laser selettiva (SLS). Ma quali sono le differenze tra questi due materiali termoplastici ad alte prestazioni? Quale scegliere? In questo articolo ti esporremo tutto quello che c’è da sapere!
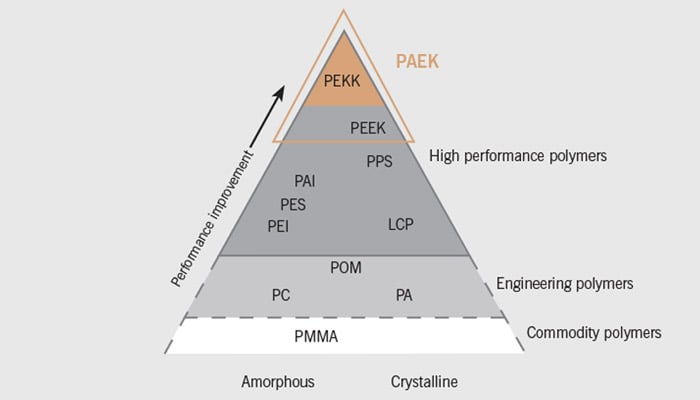
Il PEEK e il PEKK sono considerati polimeri ad alte prestazioni.
Composizione e caratteristiche
Quando si confrontano due polimeri ad alte prestazioni è importante partire dalla loro composizione e dalle loro proprietà. Questo per capire come si comporteranno durante il processo di produzione, che può essere un fattore determinante nella scelta. Questi due materiali appartengono alla famiglia PAEK, un gruppo di termoplastici semicristallini e amorfi ad alte prestazioni. In questa famiglia, il polimero più comunemente utilizzato è il PEEK, formato da una struttura molecolare di 1 chetone e 2 eteri. Invece il PEKK ha una struttura molecolare inversa: ha 2 chetoni e 1 etere. I legami chetonici sono più flessibili, il che aumenta la flessibilità del polimero in questione. Ciò significa che la temperatura di transizione vetrosa, ossia la temperatura per la quale il polimero inizia ad ammorbidirsi, e la temperatura di fusione sono più elevate nel PEKK.
Le caratteristiche principali di entrambi i materiali includono non solo un’elevata resistenza meccanica, termica e alla fatica, ma anche una bassa infiammabilità. Nel caso del PEKK, questo termoplastico è più resistente ai fluidi chimici, ha una buona stabilità dielettrica e non emette fumi tossici. Il PEEK, invece, ha eccellenti proprietà meccaniche e un buon rapporto resistenza/peso, che lo rendono un buon sostituto di alcuni metalli. Entrambi i polimeri possono essere sterilizzati, il che ne facilita l’uso nelle applicazioni sanitarie.
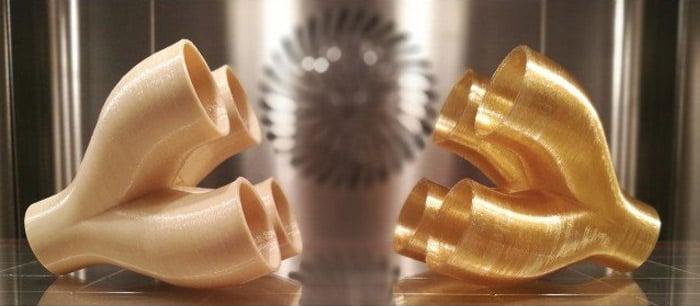
Parti stampate con PEKK (crediti fotografici: miniFactory)
Il PEEK e il PEKK hanno quindi proprietà comuni, data la loro appartenenza alla stessa famiglia di polimeri. Tuttavia, alcune caratteristiche differiscono a causa della loro composizione. La principale distinzione tra questi due materiali è il loro grado di cristallinità e la velocità di cristallizzazione. Questo concetto si riferisce al numero totale di regioni cristalline presenti in un polimero ed è rappresentato in percentuale. In questo caso, stiamo confrontando due elementi semicristallini, ma il loro grado di cristallinità dipende e varia a seconda di come vengono lavorati. In generale, quando si parla di processo di stampa 3D, il PEEK può raggiungere un alto livello di cristallizzazione, mentre il PEKK ha una struttura cristallina molto più debole. La cristallinità influisce sulle proprietà del pezzo finale, mentre la velocità di cristallizzazione e le proprietà reologiche hanno un impatto sulla facilità di stampa.
Facilità di stampa
In questa sezione ci concentreremo principalmente sulla tecnologia di modellazione a deposizione fusa (FDM). Quando si trattano polimeri ad alte prestazioni, è fondamentale conoscere approfonditamente il materiale per evitarne lo spreco, data la sua elevata costosità, e per prevenire errori durante il processo di stampa.. È necessario, prima di tutto, disporre di una stampante 3D che soddisfi determinati requisiti di temperatura. Quando si utilizza il PEEK per la stampa 3D occorre servirsi di una macchina con un estrusore che possa raggiungere i 400°C, una camera riscaldata a 120°C e un piano di lavoro che possa raggiungere i 230°C, in modo che gli strati possano aderire ad esso e il modello possa essere rimosso senza problemi, evitando così la deformazione. Nel caso del PEKK amorfo i requisiti saranno molto simili, ma non così rigidi. La temperatura di estrusione è tipicamente compresa tra i 340 e 360°C. Inoltre, è necessario disporre di una piastra di accumulo e di una camera riscaldate.
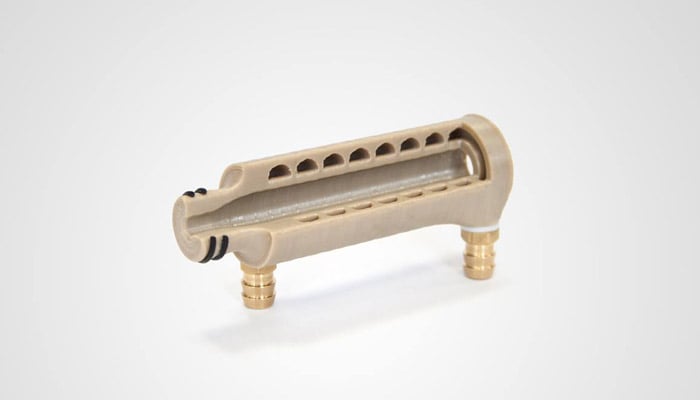
Un sistema di raffreddamento stampato in 3D con PEEK (crediti fotografici: Apium)
In termini tecnici, quando il filamento estruso si solidifica si verifica un parziale allineamento delle catene molecolari del polimero. Sulla base dei nuclei di cristallizzazione le catene molecolari si ripiegano e formano regioni ordinate. Pertanto, minore è la percentuale di nuclei di cristallizzazione nel polimero, più veloce sarà il processo di raffreddamento permettendo agli strati una migliore adesione reciproca. In questo modo si evita la deformazione. In altre parole, se il processo di raffreddamento e solidificazione è troppo veloce, le catene molecolari non si deformeranno correttamente, il che influirà direttamente sull’adesione del pezzo al letto di stampa e sulle sue proprietà meccaniche finali.
Come già detto, il PEKK ha un grado di cristallizzazione inferiore rispetto al PEEK. Ciò significa che sarà meno influenzato dal processo di raffreddamento una volta che il pezzo è stato stampato in 3D. Pertanto, in termini di facilità di stampa 3D, il PEEK sarà più complesso e tecnico da utilizzare, in quanto richiede conoscenze specifiche che consentano all’utente di controllare il processo di estrusione e le fasi di raffreddamento. D’altra parte, nella tecnologia di sinterizzazione laser selettiva (SLS), il comportamento del polimero varia in base alle dimensioni delle parti da realizzare. In particolare, le deformazioni risultano minori o assenti per i modelli di piccole dimensioni, mentre per pezzi più grandi, diventa più complesso controllare i parametri di stampa.
Post-processing di PEEK e PEKK
Le operazioni di post-processing del PEEK e del PEKK non sono semplici. Nella tecnologia FDM l’impiego di substrati per la realizzazione delle parti più complesse è ormai quasi indispensabile. Tuttavia, esistono pochissimi substrati compatibili con queste due termoplastiche, poiché la maggior parte delle soluzioni disponibili non è resistente al calore e, di conseguenza, non può essere utilizzata.
Tuttavia, alcuni operatori hanno sviluppato supporti di stampa 3D specifici per questi materiali ad alte prestazioni: Ad esempio, 3DGence e AquaSys. Si noti, tuttavia, che sono ancora più costosi dei materiali convenzionali.
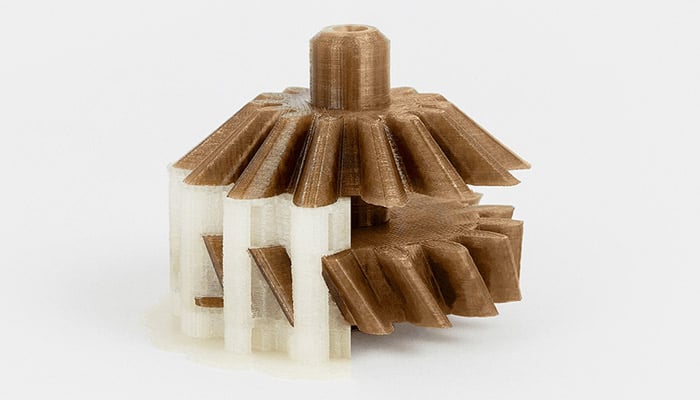
Il supporto di stampa 3DGence è compatibile con materiali ad alte prestazioni (crediti fotografici: 3DGence)
Se si utilizza il processo di sinterizzazione non è necessario avvalersi di supporti di stampa, ma si dovrà comunque valutare il costo del materiale per chilo di polvere. Torneremo su questo concetto in seguito.
Concentrandosi sui metodi di post-processing, è importante sapere che le parti stampate in 3D con PEEK o PEKK possono essere sottoposte a ricottura per migliorare la fusione degli strati e conferire al pezzo finale proprietà meccaniche superiori. Alcune stampanti 3D, come la miniFactory Ultra, integrano direttamente questa fase di ricottura nel processo di stampa.
Inoltre, i pezzi realizzati con PEEK possono essere lavorati tramite tecniche come la foratura o la fresatura. Se necessario, è anche possibile procedere con la metallizzazione delle parti per migliorarne ulteriormente le caratteristiche.
Applicazioni
Per quanto riguarda l’utilizzo di PEEK e PEKK, i settori che adottano maggiormente questi materiali ad alte prestazioni sono l’aerospaziale, l’automobilistico e l’aeronautico, grazie alla loro resistenza meccanica e alle alte pressioni, insieme alla leggerezza e la rigidità del materiale. Essendo biocompatibili, sono spesso utilizzati nel settore medico. Il PEEK ha proprietà che facilitano l’osteointegrazione, cioè la connessione diretta, strutturale e funzionale tra un osso e la superficie di un impianto sotto carico funzionale. D’altra parte, il PEKK ha una migliore resistenza ai fluidi chimici, motivo per cui viene adoperato maggiormente nell’industria petrolifera e del gas. Può anche essere utilizzato per l’industria ferroviaria.
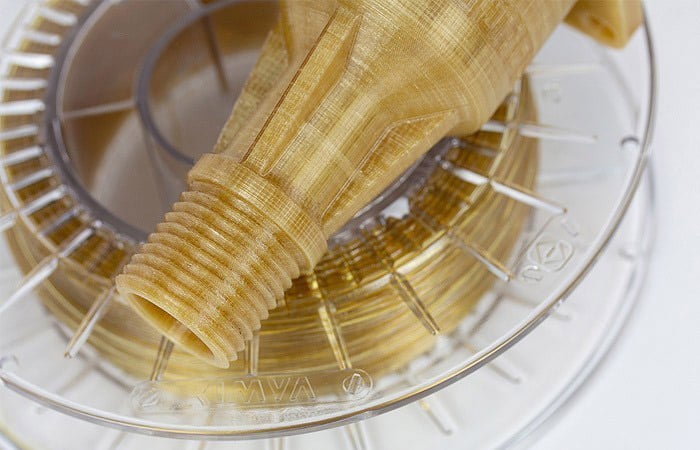
Il PEKK è maggiormente utilizzato nel settore Oil&Gas (crediti fotografici: Kimya)
Il costo di PEEK e PEKK
Il PEEK e il PEKK sono più costosi della maggior parte dei polimeri presenti sul mercato a causa delle loro proprietà e caratteristiche. In media, una bobina da 500 grammi di PEEK costerà tra i 300 e i 350 euro, mentre la stessa quantità di PEKK costerà tra i 350 e i 400 euro. Il prezzo sarà ancora più alto se si decide di acquistare un polimero ad alte prestazioni rinforzato con fibra di carbonio.
Il prezzo della polvere di PEKK si aggira intorno ai 500 euro al chilo. Pertanto, una stampa 3D SLS può diventare rapidamente costosa, considerando che una macchina EOS P800, a seconda delle dimensioni dei pezzi da stampare, può richiedere circa 100 kg di polvere. Anche se circa il 50% della polvere inutilizzata può essere riciclata, i lavori di stampa SLS con materiali ad alte prestazioni sono piuttosto costosi rispetto al nylon. È quindi necessario assicurarsi che il file 3D abbia i parametri di stampa corretti per evitare di sprecare materiale e soldi.
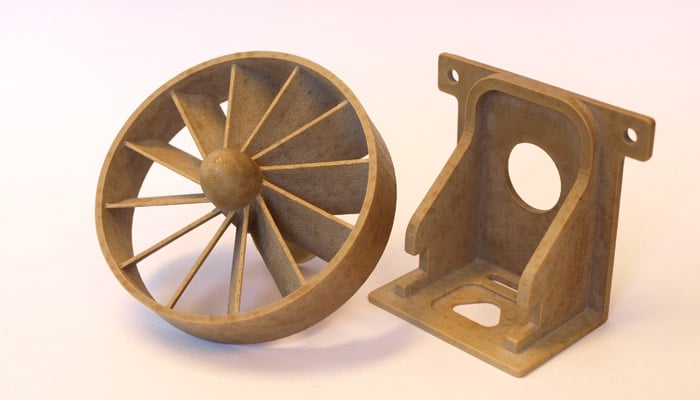
Parti stampate in 3D con PEKK attraverso un processo di sinterizzazione a polvere (crediti fotografici: Arkema)
Produttori
Come accennato in precedenza, il PEEK e il PEKK sono principalmente disponibili sotto forma di filamenti, ma esistono anche polveri specifiche per la sinterizzazione, sebbene questa opzione sia disponibile solo per il PEKK. Per quanto riguarda il PEEK, i principali produttori di questo materiale sono chimici come Victrex, Evonik o Solvay. La maggior parte di loro ha sviluppato una propria gamma di filamenti; Victrex, ad esempio, offre il suo Low Melt PAEK (LMPAEK) e collabora con produttori di macchine ad alte prestazioni come Intamsys e 3DGence; Evonik ha sviluppato la sua gamma VESTAKEEP® per la stampa 3D di impianti.
Oltre ai chimici, ci sono diversi produttori di materiali per la stampa 3D che offrono i loro PEEK: 3DXTECH, 3D4Makers, W2 Polymer e OPM. Anche i produttori di macchine si stanno occupando piano piano della produzione, come Zortrax con il suo Z-PEEK.
Per quanto riguarda il PEKK, l’azienda chimica francese Arkema rimane il maggior produttore, sia in polvere che in granuli. La sua gamma di PEKK Kepstan® soddisfa le esigenze di molti produttori. Anche Lehvoss offre il suo LUVOCOM 3F PEKK 50082 NT in forma granulare. Infine, Oxford Performance Materials offre una polvere di PEKK, in particolare per il settore medicale. Per quanto riguarda i produttori di filamenti PEKK, alcuni dei più importanti sono il marchio francese Kimya, l’azienda olandese 3D4Makers, l’americana 3DXTECH o Nanovia.
Cosa ne pensi del PEEK e del PEKK? Faccelo sapere lasciando un commento qui sotto o sui nostri canali social Facebook, LinkedIn e YouTube! Non dimenticare di iscriverti alla nostra newsletter settimanale per ricevere tutte le notizie sulla stampa 3D direttamente nella casella di posta!