Quali sono i diversi metodi di finitura delle superfici nella stampa 3D?
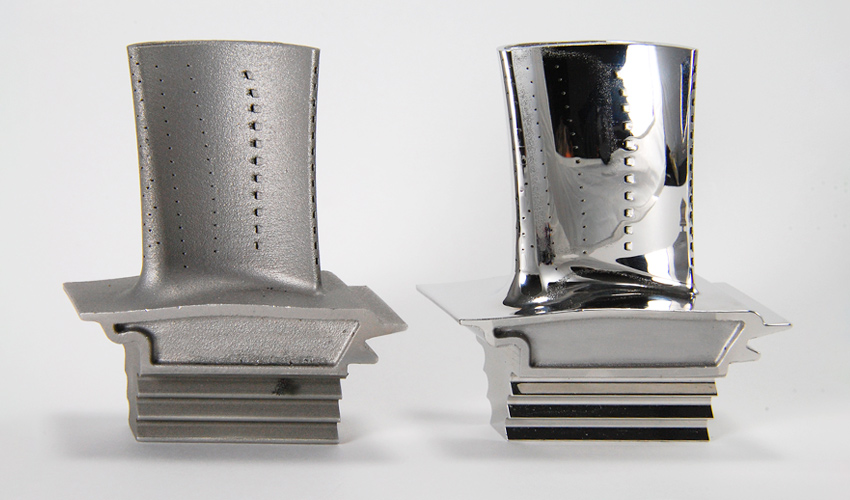
Negli ultimi anni la produzione additiva ha conosciuto un’enorme crescita, trasformandosi da una tecnologia di nicchia a un metodo sempre più industriale che consente di realizzare qualsiasi cosa, dalla prototipazione alla produzione di parti per uso finale. Tuttavia, nonostante i vantaggi della stampa 3D, soprattutto in termini di libertà di progettazione e produzione personalizzata, la tecnologia da sola non è in grado di creare pezzi finiti di qualità professionale. Spesso sono necessari vari processi di post-processing per ottenere modelli finali di alta qualità. Ciò comporta una serie di fasi diverse.
Ad esempio, in precedenza abbiamo spiegato perchè il post-processing è importante nella produzione additiva e abbiamo trattato approfonditamente sull’importanza della pulizia delle parti stampate in 3D. In aggiunta a ciò che è già noto, sottolineamo come sia essenziale anche trattare la rugosità di tali parti, a seconda del materiale e della tecnologia utilizzati. Pertanto, oggi vogliamo approfondire questo aspetto creando una guida completa sulla finitura delle superfici nella stampa 3D. Questo tipo di trattamento è spesso necessario per modificare l’aspetto del pezzo grezzo, levigare le superfici, regolare le dimensioni e la forma o migliorare la durata.
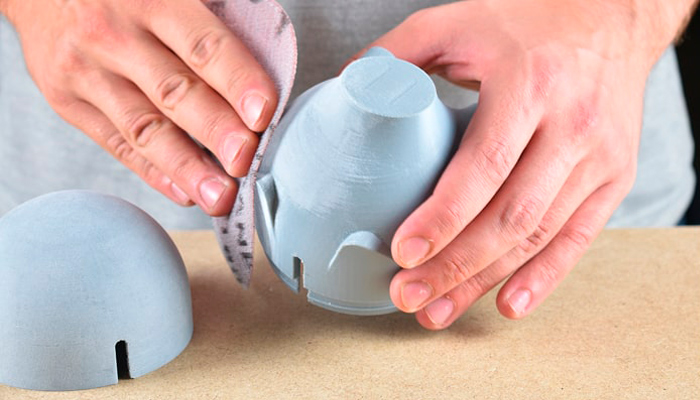
La levigatura, uno dei metodi più diffusi per la finitura della superficie delle parti stampate in 3D, può essere eseguita manualmente, sebbene siano disponibili in commercio anche strumenti meccanici.
Levigatura della superficie
Nelle parti stampate in 3D, soprattutto quelle create con metodi di estrusione, sono spesso visibili nella superficie delle linee di strato e, a volte, altre possibili imperfezioni. Per rimuovere questi difetti, uno dei metodi più utilizzati è la levigatura. Questo sistema prevede l’uso di un materiale ruvido come la carta vetrata di diverse grane per limare la superficie e fornire una finitura uniforme priva di imperfezioni. Questa tecnica è molto utile se sulla superficie deve essere applicato un qualsiasi tipo di rivestimento successivo. Infatti, questa deve essere liscia per permettere un’applicazione ottimale.
La levigatura viene generalmente eseguita iniziando con una carta vetrata a grana grossa e passando a una carta vetrata a grana più fine per ottenere una superficie sempre più liscia. Tuttavia, è importante fare attenzione quando si carteggia per non danneggiare la geometria del modello. Inoltre, uno svantaggio di questo metodo è che può essere difficile raggiungere alcuni punti dei pezzi, in particolare piccoli fori e sottosquadri. La levigatura può essere eseguita manualmente, anche se può richiedere molto tempo. Per questo motivo, sul mercato sono disponibili anche strumenti e macchinari per la levigatura automatica.
Pallinatura e la granigliatura
La pallinatura e la granigliatura, in inglese definite come Shot Peening e Bead Blasting, sono altre tecniche comuni utilizzate per la finitura delle superfici nella stampa 3D. Sono generalmente utilizzate su un’ampia varietà di parti metalliche, tra cui leghe di alluminio, acciaio, titanio, rame e altri metalli. Questi processi consentono di migliorare la resistenza e la durata dei pezzi, ma presentano alcune differenze fondamentali.
La pallinatura prevede l’uso di piccole sfere di metallo o ceramica che vengono sparate da aria compressa ad alta velocità contro la superficie del pezzo. Questo impatto genera una deformazione plastica controllata nello strato superficiale del pezzo, che a sua volta aumenta la resistenza alla fatica e riduce la formazione di crepe e rotture. La pallinatura può anche migliorare la resistenza alla corrosione e l’adesione dei rivestimenti successivi.
La granigliatura, invece, prevede l’uso di piccole sfere di vetro, metallo, plastica o altro materiale abrasivo per pulire, lucidare o texturizzare la superficie del pezzo. A differenza della pallinatura, che causa la deformazione della forma esterna del pezzo, la granigliatura rimuove solo lo strato superiore del materiale. Viene utilizzata per migliorare l’aspetto estetico del pezzo, rimuovere lo sporco e la corrosione e preparare la superficie a ricevere i successivi rivestimenti.
La differenza principale tra pallinatura e granigliatura è molto semplice. Il primo metodo genera una deformazione plastica sulla superficie del pezzo, migliorandone la resistenza finale e la durata. Il secondo metodo si limita a levigare lo strato superiore del materiale, migliorando l’aspetto estetico e preparando la superficie per i rivestimenti successivi. Queste tecniche di post-processing sono particolarmente utili per i pezzi che saranno sottoposti a sollecitazioni o sforzi meccanici, come ingranaggi, molle, componenti di turbine e parti strutturali di aerei e veicoli.
Metodi di lucidatura nella stampa 3D: vibrofinitura e burattatura
A differenza dei metodi menzionati in precedenza, in cui le parti vengono trattate una per una, i sistemi di lucidatura vengono utilizzati per trattare più oggetti stampati in 3D contemporaneamente. In questo gruppo possiamo individuare due tecniche che, sebbene possano sembrare simili, presentano alcune differenze sostanziali. Si tratta della vibrofinitura e della burattatura, nota anche come tumbling o rumbling. Entrambe le tecnologie consistono nel collocare le parti stampate in 3D in un tamburo o in un tumbler accanto a un materiale abrasivo che, combinato con il movimento di vibrazione, genera l’attrito necessario affinché le parti ottengano una finitura ottimale. Tuttavia, la scelta tra un metodo e l’altro dipende dai requisiti specifici del pezzo e dal risultato desiderato.
Sebbene entrambi i metodi permettano di ottenere finiture di qualità, la vibrofinitura è generalmente più adatta per ottenere una superficie liscia e omogenea, creando una distribuzione più uniforme del materiale sui pezzi. Pertanto, la vibrazione è ideale per i pezzi di grandi dimensioni o con bordi arrotondati che non presentano un elevato livello di dettaglio. La burattatura, invece, si basa su un sistema di cilindri centrifughi che applicano un movimento più fluido, il che la rende migliore per i pezzi più piccoli, delicati e finemente dettagliati. La velocità è un altro aspetto che differenzia i due metodi. Mentre la vibrofinitura è una tecnica più veloce, la burattatura richiede solitamente più tempo per ottenere superfici di alta qualità. A seconda della finitura desiderata e dei materiali utilizzati, la burattatura può richiedere da poche ore a diversi giorni. La vibrofinitura, invece, permette di ottenere gli stessi risultati in minor tempo, spesso in poche ore.
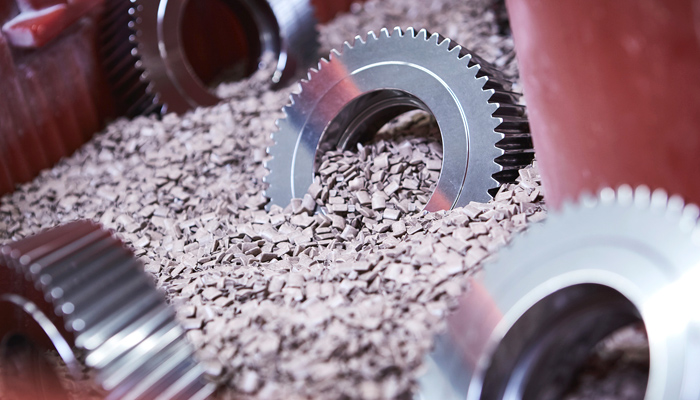
Questa tecnica di post-processing può essere utilizzata sia su parti in metallo che in plastica.
In sintesi, la vibrofinitura e la burattatura sono metodi efficaci per la post-produzione di pezzi in metallo e plastica, ma si differenziano per il movimento, la velocità, la finitura superficiale e l’idoneità alle diverse geometrie dei pezzi. Inoltre, è necessario prestare attenzione quando si mescolano diversi tipi di mezzi abrasivi, poiché alcune combinazioni causano uno squilibrio e possono arrecare danni ai pezzi o compromettere l’uniformità della finitura.
Vapor smoothing
Il Vapor smoothing è un altro metodo per ottenere una superficie liscia di una parte stampata in 3D, con la principale differenza che la finitura sarà lucida anziché opaca. A tale scopo, si utilizza un solvente gassoso per fondere la superficie del componente fino a renderla uniforme. Una volta esposti al solvente nella camera di vapore, i pezzi vengono introdotti direttamente in una camera di raffreddamento per fermare la liquefazione. La liquefazione è il processo in cui una sostanza allo stato solido o gassoso passa direttamente allo stato liquido, a causa di un cambiamento radicale delle sue condizioni fisiche. Il raffreddamento assicura che venga fusa solo la superficie e che venga mantenuta la forma desiderata dell’oggetto.
Questo processo di Vapor smoothing serve anche a riempire i pori all’esterno dell’oggetto e a sigillare la superficie, rendendo i pezzi utili per contenere liquidi o gas. Sebbene questa tecnologia sia compatibile con un’ampia gamma di materiali termoplastici, va notato che non può essere utilizzata con alcuni materiali in quanto potrebbe causare una reazione chimica dannosa. Tra le plastiche incompatibili vi sono il policarbonato (a seconda della soluzione di post-processing), il polifenilsolfone (PPSF), l’ULTEM 1010 e l’ULTEM 9085.
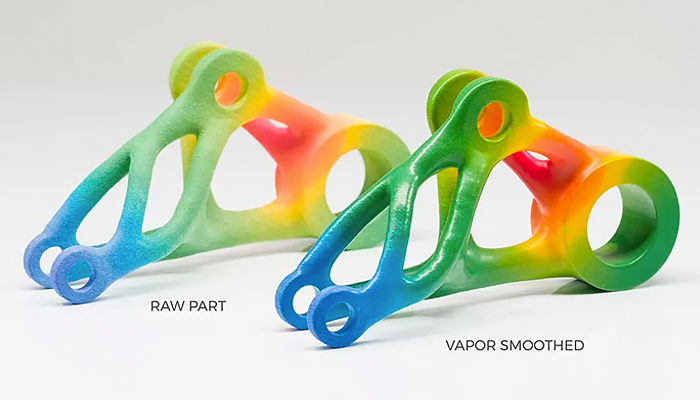
Confronto tra il pezzo grezzo e il pezzo trattato con il Vapor smoothing (Crediti fotografici: AMT)
Un’alternativa al Vapor smoothing è l’immersione in solvente. Come suggerisce il nome, si tratta di immergere le parti stampate in 3D in un solvente anziché esporle alla sostanza chimica vaporizzata. Sebbene i risultati siano abbastanza simili a quelli del Vapor smoothing, è più difficile mantenere la precisione dimensionale perché il solvente agisce in modo più rapido e aggressivo. Questo metodo è spesso utile se le parti sono più grandi delle dimensioni della camera di vapore.
Resine epossidiche per la finitura delle superfici: rivestimento e infiltrazione
Le resine epossidiche sono una classe di polimeri reattivi che contengono gruppi epossidici (eteri ciclici a tre membri contenenti due atomi di carbonio e un atomo di ossigeno). Quando si trattano le parti stampate in 3D, queste resine consentono di ottenere una finitura superficiale sigillata, rendendo la parte ermetica e aumentandone la resistenza alle alte temperature e ad alcune sostanze chimiche. Questo metodo è ideale per le parti che devono affrontare condizioni operative difficili. Quando si applica questo tipo di resina, si può scegliere tra due metodi: il rivestimento e l’infiltrazione.
Il rivestimento epossidico viene solitamente applicato a mano. Ciò consente di ridurre i costi evitando l’acquisto di attrezzature costose, ma allo stesso tempo aumenta il tempo e la quantità di manodopera necessaria per l’applicazione. Inoltre, questa tecnica è più adatta a piccole produzioni, a componenti di dimensioni ridotte o ad articoli che devono sigillare solo una parte della loro superficie. Tuttavia, ci sono aree che non possono essere raggiunte con questa tecnica, come i canali interni e i sottosquadri. Inoltre, potrebbe non essere la scelta ideale per i pezzi che richiedono dimensioni precise, poiché il rivestimento epossidico aumenta leggermente lo spessore del pezzo.
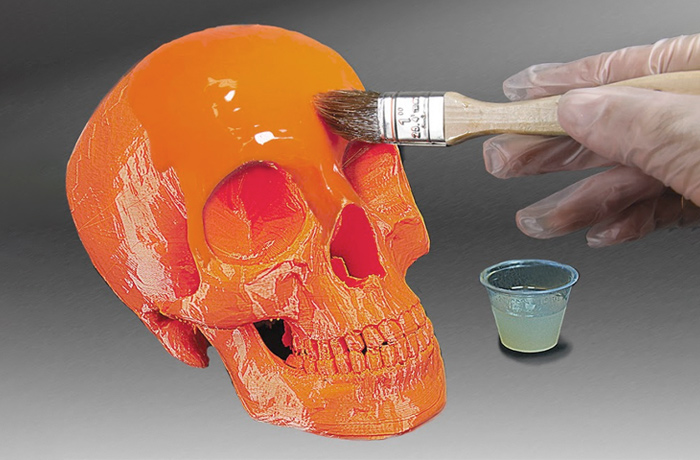
Un esempio di rivestimento manuale di resina epossidica.
D’altro canto, il sistema di infiltrazione epossidica contrasta molte delle limitazioni riscontrate quando lo si applica a mano. Nel metodo di infiltrazione, la parte viene immersa nella resina epossidica e viene utilizzata una camera a vuoto per introdurre la resina nell’oggetto, riempiendo così i pori. Questo processo richiede circa tre ore per essere completato ed è meno laborioso, il che significa che è più pratico e veloce quando applicato a componenti di grandi dimensioni. Tuttavia, lo svantaggio principale rispetto al rivestimento manuale è il suo costo più elevato. Richiede una camera a vuoto, un forno per preriscaldare e polimerizzare la resina, il tutto in aggiunta al costo della resina epossidica stessa.
Il ruolo della lavorazione CNC nel post-processing
Come sappiamo, le tecnologie additive e sottrattive possono essere utilizzate in modo complementare per combinare i vantaggi di entrambi i metodi. Tra i sistemi di produzione sottrattiva più noti troviamo la lavorazione CNC che, sebbene non sia propriamente un metodo di post-processing, può essere utilizzata come risorsa per una finitura superficiale di qualità nella stampa 3D. Questo uso è particolarmente efficiente se associato a tecnologie come la Direct Energy Deposition (DED).
Le parti prodotte con la DED hanno una superficie molto ruvida, poiché il metallo viene fuso direttamente durante il processo di estrusione. Pertanto, è sempre necessaria una fase di lavorazione CNC per ottenere una superficie liscia e definita. Per questo motivo, sul mercato sono disponibili numerose soluzioni di produzione ibride che integrano entrambi i processi per accelerare le fasi di produzione.
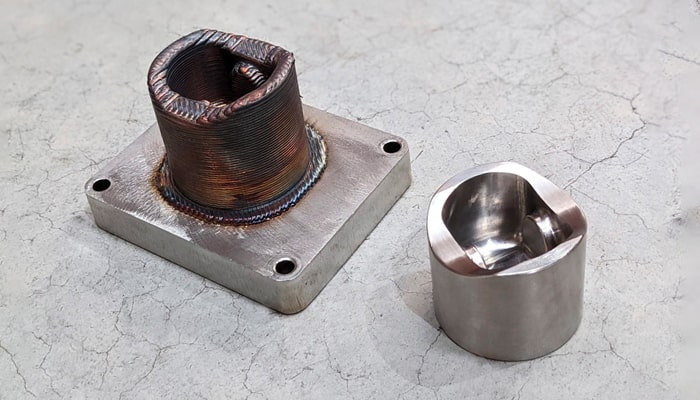
A destra, il pezzo dopo la lavorazione CNC (crediti foto: Meltio)
Cosa pensi dei diversi metodi di finitura superficiale nella stampa 3D? Faccelo sapere lasciando un commento qui sotto o sui nostri canali social Facebook, Linkedin e YouTube! Non dimenticare di iscriverti alla nostra newsletter settimanale per ricevere tutte le notizie sulla stampa 3D direttamente nella casella di posta!
*Crediti per la foto di copertina: EOS