Materiali di stampa 3D ad alte prestazioni: PEEK, ULTEM e altri polimeri
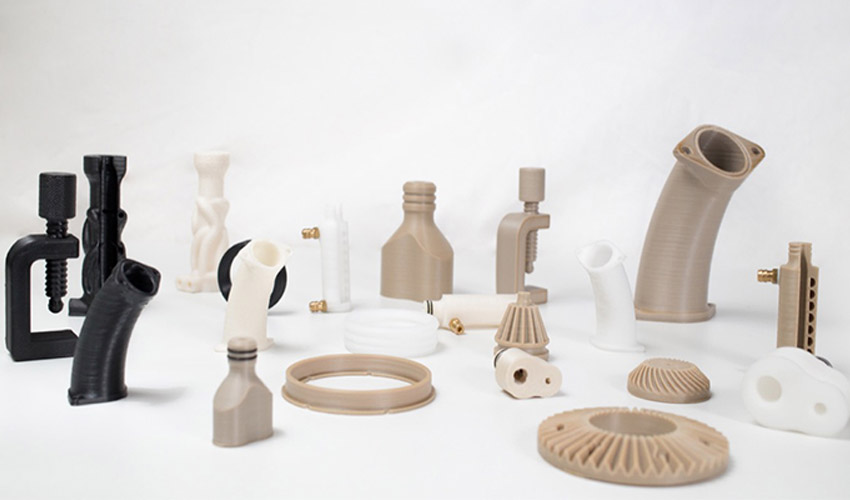
Negli ultimi anni, i materiali ad alte prestazioni sono diventati un argomento molto controverso nella comunità della stampa 3D. In un mondo in costante mutamento e adattamento a nuove tecnologie e materiali, era solo una questione di tempo prima che i polimeri termoplastici dalle prestazioni elevate si distinguessero tra gli altri materiali per stampa 3D. Il poliarileterchetone (PAEK) è una famiglia di materiali termoplastici semicristallini in grado di sopportare temperature elevate mantenendo una resistenza eccezionale. Il PAEK è principalmente utilizzato sotto forma di polietere etere chetone (PEEK) e di polietere etere chetone chetone (PEKK), due materiali dall’elevata rigidità. Tuttavia, un’alternativa molto più economica, il polieterimide (PEI), anche noto come ULTEM, ha ottenuto parecchia attenzione perché, per via della sua mancanza di chetone, costa molto meno. Trovi qui tutto quello che devi sapere sulle famiglie PAEK e PEI.
Produzione e caratteristiche dei polimeri ad alte prestazioni
La prima cosa da notare sui polimeri ad alte prestazioni è che, sebbene condividano caratteristiche comuni, non sono tutti esattamente uguali. Detto questo, in generale si può notare che i materiali termoplastici ad alte prestazioni, e il PEEK in particolare, sono resistenti quanto l’acciaio e più leggeri dell’80% rispetto al metallo, il che li rende estremamente desiderabili nel settore della produzione. Inoltre, oltre all’eccezionale resistenza meccanica e termica fino a 250 °C (482 °F) per il funzionamento continuo, i materiali PAEK sono anche resistenti alla dissoluzione negli oli e in altre sostanze, a differenza della maggior parte delle altre materie plastiche. Quando esposti al fuoco, non vengono rilasciati quasi gas o fumi nocivi.
In verità, questi materiali sono in circolazione da oltre trent’anni, soprattutto utilizzati per lo stampaggio a iniezione o per la lavorazione meccanica. In un primo momento Stratasys era l’unica azienda a produrre stampanti in grado di gestire le elevate temperature richieste per fondere i polimeri di PAEK e di PEI. Con l’apertura del mercato, però, più aziende hanno avuto l’opportunità di sperimentare questi materiali, con una conseguente commercializzazione di massa delle loro invenzioni. Con il passare del tempo e con l’indebolimento delle barriere in entrata, vediamo un sempre maggior numero di aziende che fanno il loro ingresso nel settore e iniziano a produrre stampanti in grado di gestire i termoplastici PAEK.
Il PEI è stato sviluppato per la prima volta dal dipartimento plastica di General Electric alla fine degli anni ‘80. Nel 2007, tuttavia, SABIC, una delle principali società pubbliche dell’Arabia Saudita, ha acquisito il dipartimento e quindi i diritti sul brand ULTEM. Poiché questo materiale è un’alternativa più economica al PEEK, ha generato subito un grande interesse da un punto di vista finanziario. Combinato alle sue varie e significative proprietà fisiche come la resistenza al calore elevato, ai solventi e alle fiamme, la forza dielettrica e la conduttività termica, è una fantastica soluzione per numerosi progetti di ingegnerizzazione. ULTEM è diventato il materiale di prima scelta in fatto di applicazioni ingegneristiche estremamente difficili, solitamente nel settore aerospaziale.
Stampa 3D con polimeri ad alte prestazioni
I polimeri PAEK e PEI sono stampati principalmente con FDM (modellazione a deposizione fusa) o con SLS (sinterizzazione laser selettiva). Considerando le temperature elevate cui operano questi polimeri, è comprensibile che nessuna stampante 3D ordinaria sia in grado di lavorare questi filamenti. Una stampante 3D per PAEK/PEI deve avere un ugello estrusore in grado di gestire temperature di oltre 300°C, punto di fusione di tali polimeri. Inoltre, il piatto riscaldato deve raggiungere almeno 150°C affinché l’oggetto possa essere staccato. Infine, sono richiesti importanti meccanismi di raffreddamento per garantire il corretto equilibrio termico nella camera chiusa.
Il post-processing di materiali ad elevate prestazioni è una procedura necessaria. Come nel caso di qualsiasi parte complessa stampata con FDM, è necessario un supporto. Quando si tratta di PAEK e PEI, tuttavia, per via della rigidità dell’oggetto finale, staccare il supporto può essere complicato. Di conseguenza, viene spesso utilizzata una serie di strumenti per finalizzare la post-produzione di un pezzo.
D’altro canto, però, quando si parla di SLS il pezzo è stampato praticamente alla perfezione, senza la necessità di lavorazioni meccaniche extra. Ciò nonostante, i produttori devono tenere in considerazione il fenomeno della deformazione (warping). Dopo aver completato la stampa di un oggetto e dopo che la temperatura all’interno della camera è scesa, i polimeri tendono a ritirarsi. Di conseguenza, PAEK e PEI sono molto utilizzati per la stampa di piccoli oggetti, dato che più la parte è grande e maggiore sarà l’effetto di deformazione (warping). Sebbene ciò possa essere controllato in una certa misura ottimizzando i parametri di stampa come la velocità e la temperatura.
L’uso di termoplastici ad alte prestazioni richiede è ancora in fase di perfezionamento. Si sta ancora lavorando sul processo di produzione che viene costantemente migliorato. Ad esempio, come menzionato in precedenza, una volta stampato un oggetto in PAEK è ancora necessaria un’ulteriore lavorazione spesso complessa. Tuttavia, nuove innovazioni stanno migliorando costantemente il processo. Diverse aziende stanno attualmente lavorando su una soluzione FDM in cui il supporto dell’oggetto sia stampato in un materiale diverso in modo che possa essere eliminato in maniera più semplice e rapido una volta completata la stampa. Altre aziende, inoltre, come ad esempio Kimya, hanno iniziato a concentrarsi sulle combinazioni di materiali che permettano di sfruttare il meglio di ogni materiale. In questo modo, il prodotto finale può essere ad esempio realizzato al 70% in PEEK e al 30% in fibra di carbonio.
Applicazioni
Come si può immaginare, una famiglia di materiali con un numero così elevato di caratteristiche e qualità è utilizzata in una varietà di settori. Il settore automotive ha ben presto iniziato a sfruttare le capacità uniche di PAEK e PEI per tutta una serie di applicazioni. Una delle aree in cui PAEK e PEI sono stati più sovversivi è quella della produzione di strumenti rapidi a basso costo per stampaggio a iniezione, termoformatura, dispositivi di bloccaggio e accessori. Questo permette alle aziende di produrre un volume da piccolo a medio di pezzi a basso costo senza dover investire nella produzione su larga scala. Inoltre, la produzione di pezzi customizzati è sempre più richiesta in quanto possono essere modificati per adeguarsi a certi requisiti e possono sostenere cambiamenti complessi per migliorare la loro struttura.
Come nel caso di molti altri materiali di stampa 3D, le famiglie PAEK e PEI sono ampiamente utilizzate in campo medicale. PEEK è famoso per essere utilizzato per la schermatura degli apparecchi per la risonanza magnetica (MRI). È anche considerato un materiale biologico avanzato impiegato per impianti medici e in barre di rinforzo e dispositivi di fusione spinale. Il fatto che sia in grado di resistere all’acqua bollente e al vapore surriscaldato lo rende perfetto per oggetti che devono essere sterilizzati a temperature estremamente elevate.
I termoplastici ad alte prestazioni sono anche ampiamente utilizzate nel settore aerospaziale. Resistenza chimica, elevato rapporto peso-resistenza, e basso rischio di incendio, fumo e tossicità rende tali polimeri i sostituti ideali dei metalli, spesso utilizzati per parti di velivoli e pezzi di macchinari. Isolamento termo acustico, staffe strutturali, morsetti e distanziatori, dispositivi di fissaggio, connettori e tubi sono solo alcuni esempi di elementi per cui il settore dell’ingegneria aerospaziale ha iniziato a utilizzare PAEK e PEI, spesso riducendo il peso dei pezzi del 70%. Altri settori che utilizzano i materiali ad alte prestazioni sono: marittimo, nucleare, del petrolio e del gas e molti altri.
Principali produttori e prezzo di materiali ad alte prestazioni
Molte delle grandi aziende chimiche si sono subito rese conto della rilevanza nel campo della manifattura additiva dei termoplastici ad alte prestazioni. Di conseguenza, aziende di spicco come Arkema, Lehmann & Voss e Solvay (per menzionarne alcune) sono tra le principali produttrici di materiali PAEK. Per quanto riguarda il PEI, invece, il marchio ULTEM di SABIC è l’unico per ora disponibile sul mercato.
In termini di stampanti in grado di supportare PAEK e PEI, il produttore cinese INTAMSYS, ha ricevuto moltissima attenzione in quanto offre una gamma di stampanti 3D professionali e da tavolo. Nondimeno, l’olandese Tractus3D sta diventando sempre più popolare, così come il gigante tedesco EOS, che ha messo sul mercato la stampante HTLS (High temperature laser sintering) in grado di trattare questi materiali.
Detto questo, come ci si può aspettare, questi polimeri ad alte prestazioni non sono economici. PEEK, UTLEM e PEKK sono alcuni dei materiali per la stampa 3D più costosi disponibili sul mercato. Sebbene l’ULTEM sia un’alternativa leggermente più economica, una bobina da 1 kg di filamento parte da oltre 200 dollari e spesso costa molto di più a seconda della marca e delle proprietà del materiale. Il PEEK, invece, costa spesso più di 300 dollari e fino a oltre 700 dollari per 1 kg di materiale, mentre il PEKK costa in media tra i 400 e i 500 dollari per la stessa quantità.
Non solo, ma se siete interessati al filamento, dovete anche tenere presente che la stampa non può essere effettuata da qualsiasi stampante. È necessario investire in una stampante progettata per polimeri ad alte prestazioni, come già detto. Queste stampanti sono comprensibilmente più costose di un modello FDM standard. In effetti, alcune partono da oltre 5.000 euro, ma in genere sono molto più costose. Tuttavia, nel corso degli anni abbiamo visto che con la crescita del mercato aumentano anche le scelte a disposizione dei consumatori. Forse nel prossimo futuro assisteremo a un calo dei prezzi sia delle stampanti che dei materiali, man mano che le applicazioni con polimeri ad alte prestazioni si diffonderanno nella produzione additiva.
Cosa pensi dell’uso di polimeri termoplastici ad alte prestazioni nella stampa 3D? Quali altri settori saranno coinvolti in un prossimo futuro? Condividi la tua opinione sui nostri social Facebook e LinkedIn. Trovi tutti i nostri video sul nostro canale YouTube! Non dimenticare di iscriverti alla nostra Newsletter settimanale per ricevere tutte le notizie sulla stampa 3D direttamente nella casella di posta!