I materiali ceramici di Lithoz stanno rivoluzionando l’industria aerospaziale?
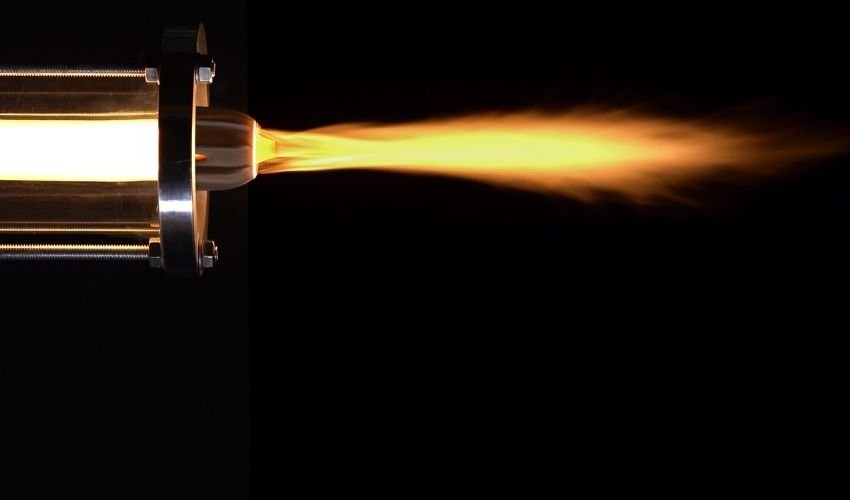
Si prevede che il mercato della stampa 3D in ceramica raggiungerà i 4,8 miliardi di dollari entro il 2030. Uno dei settori che sta adottando maggiormente la stampa 3D della ceramica è l’industria aerospaziale. In questo settore troviamo l’azienda austriaca Lithoz, che si dedica, tra le altre cose, alla produzione additiva della ceramica applicata al settore aerospaziale. Lithoz è riuscita a sviluppare la tecnologia Lithography-based Ceramic Manufacturing (LCM), un processo basato sulla produzione di ceramica mediante stereolitografia che permette di creare parti particolarmente adatte per applicazioni aerospaziali. Quali possibilità dunque offrono la stampa 3D della ceramica e i materiali sviluppati per essa, e quali sono i loro campi di applicazione? Come contribuiscono a migliorare gli esigenti standard del settore?
Componenti in ceramica stampati in 3D
Più veloce, più semplice e più economico. È questo il triplice principio perseguito da molte aziende e organizzazioni del settore aerospaziale. In quasi nessun altro campo le aspettative e i requisiti per i componenti stampati in 3D sono così alti. Probabilmente le maggiori sfide da superare sono i carichi estremi, così come il riscaldamento e il surriscaldamento. Spesso le pale delle turbine si muovono a una velocità così elevata che il calore generato è maggiore di quello utilizzato nella fabbricazione del metallo. Ciò spinge al limite i processi produttivi convenzionali. I componenti, però, non devono solo resistere al surriscaldamento, ma anche al freddo estremo. Visto che la temperatura esterna nello spazio può scendere a oltre -200 °C, il che fa sorgere un’ulteriore esigenza. Il settore aerospaziale necessita quindi di un’alternativa al processo di produzione dei componenti.
Queste condizioni estreme non possono influenzare le prestazioni dei componenti, poiché stabilità e porosità costanti sono essenziali per i viaggi nello spazio. La dimensione dei catalizzatori, per esempio, riveste un ruolo molto importante. Se i componenti sono troppo grandi possono infatti subire perdite di calore e se sono troppo piccoli possono impedire la massima decomposizione del propellente. Il risultato in entrambi i casi sono prestazioni inferiori e costi più alti. Ma come può la stampa 3D in ceramica risolvere queste criticità? Le ceramiche sono particolarmente note per le proprietà termiche, le prestazioni meccaniche e anche per il loro utilizzo nella produzione di pregiati componenti di alta qualità. La produzione additiva consente di progettare forme complesse riducendo i costi e i tempi di consegna, il che non è possibile con altri metodi convenzionali.
Si può quindi dedurre che la stampa 3D in ceramica sia una soluzione ideale per un settore esigente come quello aerospaziale. Lithoz si è rapidamente posizionata in questo segmento sviluppando un nitruro di silicio (Si3N4) contraddistinto da eccellenti proprietà. Tra queste proprietà troviamo una grandissima resistenza alle alte temperature, la capacità di resistere agli sbalzi termici e un’impressionante durezza. Per dimostrare tali proprietà e testare il materiale in condizioni estreme, l’azienda austriaca ha eseguito un test di resistenza termica con un ugello in Si3N4.
Il team di Lithoz ha voluto provare la resistenza agli shock termici del suo materiale utilizzando l’ugello in nitruro di silicio stampato in 3D. È stato riscaldato a 900 °C e subito dopo raffreddato con acqua a temperatura ambiente. Nonostante tali sbalzi termici improvvisi, l’ugello stampato in 3D ha superato il test senza subire alcun tipo di danno. Secondo Lithoz il materiale può resistere anche a una temperatura maggiore a 900 °C, il che lo rende ideale per il settore aerospaziale.
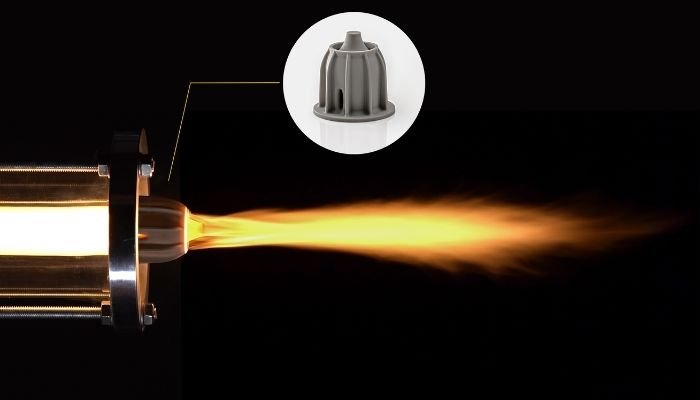
L’ugello prodotto da Lithoz è in grado di resistere alle temperature più elevate.
Cosa significa questo per l’industria aerospaziale? Grazie al nitruro di silicio, i componenti stampati in 3D sono in grado di resistere perfettamente a importanti sbalzi termici. Possiedono inoltre un’enorme resistenza e durezza, nonché il vantaggio di rendere possibile la produzione di componenti ceramici complessi. Per il settore aerospaziale ciò vuol dire la possibilità di realizzare microturbine, propulsori e utensili da taglio in modo rapido e preciso. Per di più, questi componenti possono essere usati a temperature che vanno fino ai 1.200 °C, il che richiederebbe tempo e denaro se fossero realizzati tramite un processo produttivo tradizionale. Il Si3N4 viene poi anche utilizzato in altri settori. Il settore medico, per esempio, sfrutta questo materiale per la sua chimica superficiale antibatterica e antivirale, nonché per la sua eccellente biocompatibilità. Nello specifico, il nitruro di silicio è adatto ai settori dell’odontoiatria, dell’ortopedia e degli impianti cranio maxillo facciali. Può essere usato anche nella lotta al coronavirus, poiché le sue proprietà superficiali lo rendono resistente a virus e batteri.
Stampa 3D sulla luna: realtà o fantascienza?
Può sembrare la sceneggiatura di un film di fantascienza, ma Lithoz ricorre già alla polvere lunare nella stampa 3D della ceramica. La tecnologia LCM consente di usare la regolite lunare per produrre componenti aerospaziali dalle dimensioni molto precise. Nelle future missioni spaziali i ricambi e gli strumenti necessari potrebbero essere prodotti direttamente in loco e su richiesta. Questo materiale è considerato una risorsa atossica per l’uomo e disponibile in grandi quantità. La stretta collaborazione tra Lithoz e l’Agenzia Spaziale Europea (ESA) riguardo a questo progetto consente continue ricerche oltre a un maggiore sviluppo della polvere lunare nel campo della stampa 3D. Nel corso del progetto RHEFORM di Horizon 2020 dell’UE, è stata studiata una soluzione per sostituire l’idrazina. Tale sostanza, considerata cancerogena, ha svolto un ruolo importante nei viaggi spaziali sin dagli anni ‘60. Utilizzando la stampante 3D CeraFab 7500, una soluzione DLP (Digital Light Processing) sviluppata da Lithoz, nonché il legante fotopolimerizzante anch’esso sviluppato da Lithoz, i ricercatori sono stati in grado di compiere significativi progressi in termini di applicazioni ottimizzate per il settore aerospaziale. Attualmente sono in corso diversi progetti, in cui Lithoz è attivamente coinvolta, volti a esplorare ulteriori possibilità di utilizzo che può offrire la polvere lunare.
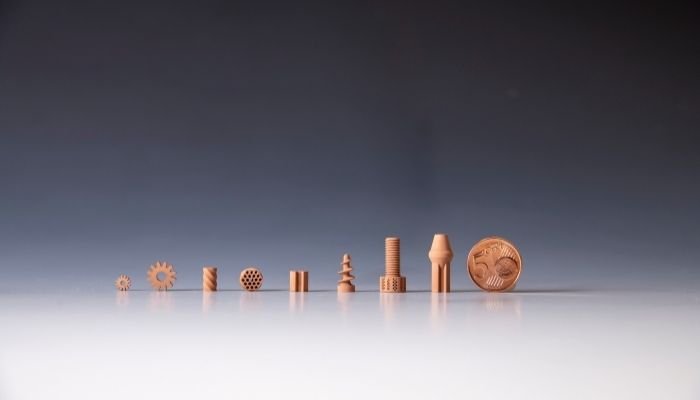
Sfruttando la polvere, i componenti stampati in 3D lunare possono assumere dimensioni e forme diverse (Crediti foto: Lithoz)
Produzione di turbine per aerei più leggere
Le turbine sono l’elemento più rilevante nel decollo aereo. Uno dei componenti più importanti all’interno della turbina sono le pale, che vengono tradizionalmente prodotte mediante cera persa. Tuttavia, ciò pone un problema serio. Con anime convenzionali create mediante stampaggio a iniezione, la capacità d’incorporare elementi di raffreddamento multipale stretti e complessi è limitata. A lungo termine le conseguenze possono essere non solo costose, ma possono anche comportare rischi relativi alla sicurezza. Come si possono quindi produrre turbine in modo più efficiente e innovativo senza aumentare i costi? La soluzione risiede nel LithaCore 450, un materiale a base di silice ideale per produrre anime da fonderia utilizzando la tecnologia LCM. Grazie alla bassa espansione termica e all’elevata porosità, questo materiale è ideale per la produzione additiva di anime ceramiche destinate ad applicazioni aerospaziali.
Questo metodo produttivo LCM non evita solo costi elevati e ulteriori sforzi necessari, consente anche una produzione più rapida. In questo modo sia i prototipi che la produzione in serie possono essere realizzati in tempi brevi, di conseguenza anche il time to market è più breve. Ciò permette inoltre di ottenere anime da fonderia sottili almeno 200 µm e grandi fino a 30 cm, e ciò vale anche per forme complesse con determinate caratteristiche come i bordi d’uscita. Grazie al sistema CeraFab sviluppato da Lithoz, l’azienda è stata persino in grado di produrre diverse anime da fonderia aventi una dimensione di 500 mm. Tale prodigio tecnico, che è una prima assoluta, dimostra quali siano le possibili soluzioni future a disposizione del settore aerospaziale, dai prototipi alle grandi anime per turbine industriali firmate Lithoz.
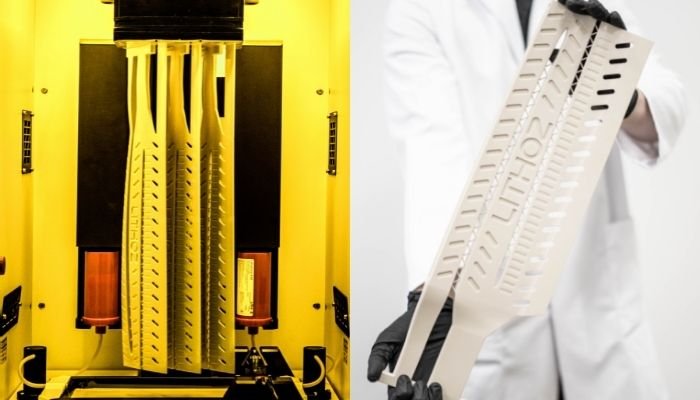
Nuclei in ceramica stampati tramite CeraFab S230 con LithaCore 450 per turbine a gas industriali (Crediti foto: Lithoz)
I nuovi materiali sviluppati da Lithoz
Lithoz ha aggiunto altri due materiali alla sua gamma di soluzioni ceramiche. Il primo è il carburo di silicio infiltrato (SiSiC), un materiale ceramico leggero, ma duro, che offre una perfetta conduttività termica e un’espansione termica minima. Pertanto, le ceramiche SiSiC vengono spesso utilizzate come scambiatori di calore, ugelli o terminali per diversi tipi di bruciatori. Il secondo materiale è il nitruro di alluminio (AIN), che viene utilizzato con la tecnologia DLP. Il nitruro di alluminio possiede un’elevata conduttività termica come il SiSiC. La resistenza alla flessione dell’AIN, che è stata possibile misurare nei campioni di ricerca, variava invece tra i 320 e i 498 MPa. Nel loro insieme, queste proprietà consentono di produrre componenti molto complessi e privi di spaccature, creando così nuove possibilità applicative nel campo della gestione termica.
Questa vasta e diversificata gamma di materiali e tipologie di sviluppo illustra chiaramente i progressi che sono stati ottenuti nel settore aerospaziale grazie alla stampa 3D della ceramica, e quali nuove possibilità permettano le soluzioni Lithoz. Oltre a produrre componenti con strutture complesse, l’azienda consente anche una grande libertà e precisione di progettazione grazie ai suoi nuovi materiali. A prescindere dal poter ottenere componenti che hanno dimensioni diverse, le soluzioni Lithoz garantiscono una qualità del materiale di primissimo ordine, una precisione di esposizione costante e una grande precisione dei pixel. Ciò si ottiene utilizzando un sistema CeraFab in modo uniforme su tutta la piattaforma di costruzione, il che agevola la fabbricazione di componenti per la produzione in serie ed elimina le relative criticità produttive.
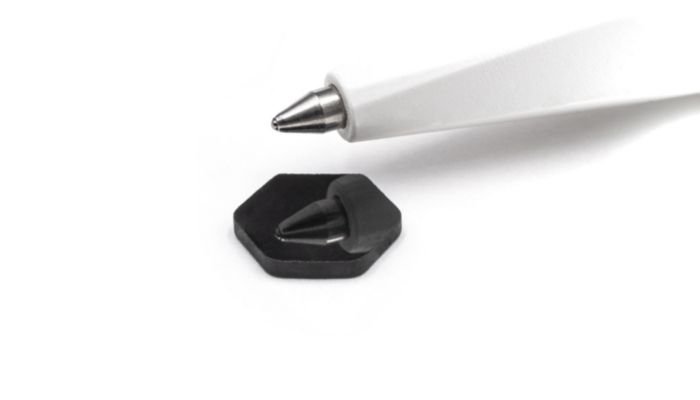
Il carburo di silicio consente di produrre forme e dimensioni inimmaginabili (Crediti foto: Lithoz)
I progetti di Lithoz per il settore aerospaziale
Lithoz è attualmente coinvolta in alcuni progetti che hanno intensificato notevolmente questo aspetto produttivo. Insieme ai ricercatori dell’Università di Poitiers (Francia), al FOTEC Forschungs- und Technologietransfer GmbH (Austria) e all’Università di Scienze Applicate Wiener Neustadt GmbH (Austria), Lithoz ha messo a confronto catalizzatori ceramici monolitici stampati in 3D e catalizzatori convenzionali, nonché diversi washcoat. Per quanto riguarda la decomposizione del perossido di idrogeno altamente concentrato, è stato riscontrato che il fattore di porosità segna un’importante differenza nella messa a confronto diretto. In generale la porosità misurata della struttura stampata è di gran lunga maggiore rispetto a quella della struttura estrusa. Una delle conseguenze di ciò è che il comportamento della temperatura transitoria migliora anche con una maggiore porosità. Questi risultati possono rappresentare un passo decisivo per aumentare il ricorso alla stampa 3D della ceramica nel settore aerospaziale. Trovi maggiori informazioni sui progetti Lithoz qui.
Cosa ne pensi dei materiali Lithoz e del ruolo che rivestono nel settore aerospaziale? Condividi con noi la tua opinione nei commenti qui sotto o sui nostri canali social Facebook, Twitter, Linkedin e YouTube! Non dimenticare di iscriverti alla nostra Newsletter settimanale per ricevere tutte le notizie sulla stampa 3D direttamente nella tua casella di posta!