Il Machine Learning per la tecnologia LPBF in uno studio dell’APL
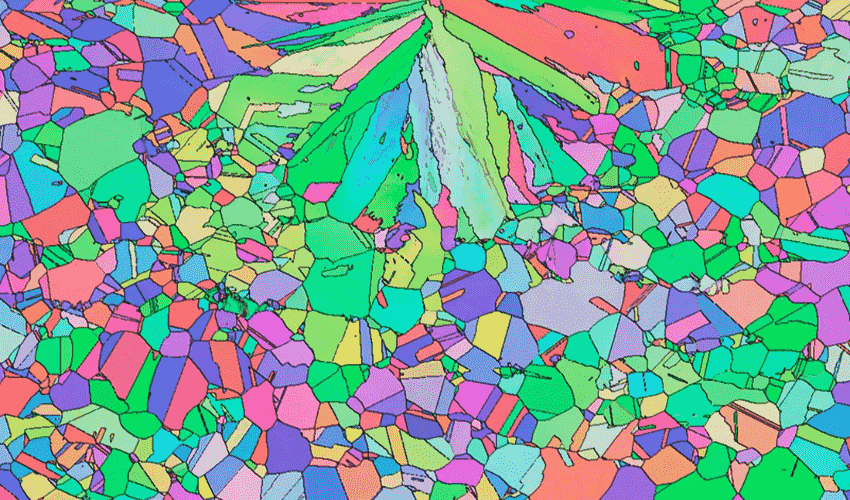
I ricercatori del The Johns Hopkins University Applied Physics Laboratory (APL) hanno sviluppato un nuovo approccio che integra la stampa 3D al Machine Learning. Si tratta di un modello che permette di creare delle simulazioni utili per verificare la produzione di materiali creati tramite Laser Powder Bed Fusion (LPBF). Il Machine Learning (ML), in italiano conosciuto anche come apprendimento automatico, fa parte di una branca dell’intelligenza artificiale e può essere applicato in vari settori, dal medicale all’aerospaziale.
La tecnica ideata dall’APL permette di prevedere quale sarà la microstruttura che si andrà a formare sul piano di stampa grazie alle misurazioni effettuate sul singolo strato di polvere. Per farlo, i ricercatori si sono serviti infatti della modellazione e della simulazione computazionale. Queste previsioni dell’oggetto che si andrà a creare permettono di intervenire tempestivamente in caso di errori. Questo permetterebbe così non solo di risparmiare tempo, materiali e costi, ma anche di aumentare esponenzialmente la produzione dei materiali fabbricati tramite la tecnologia LPBF.
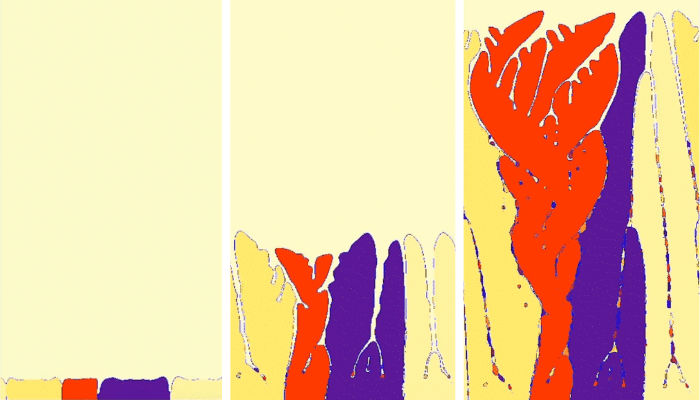
In questa immagine è illustrato il processo di previsione della microstruttura, che viene ottenuto attraverso l’analisi dell’impatto del tasso di raffreddamento e del gradiente di temperatura sull’orientamento e sulle dimensioni dei grani.
Questo studio fa parte di un più ampio insieme di lavori condotti al The Johns Hopkins University Applied Physics Laboratory incentrati sull’uso dell’intelligenza artificiale per accelerare la scoperta di nuovi materiali destinati ad ambienti estremi. Morgan Trexler, il referente per il programma Science of Extreme and Multifunctional Materials dell’APL nell’Area di Missione Ricerca e Sviluppo Esplorativo, ha dichiarato che: “Questo nuovo approccio sarà di grande impatto per aiutare a progettare e comprendere la formazione dei materiali durante i processi di fabbricazione additiva, e questo si inserisce nella nostra strategia generale incentrata sull’accelerazione dello sviluppo dei materiali per la sicurezza nazionale”.
Perchè usare il Machine Learning per la tencologia LPBF
Nella LPBF gli strati di polvere metallica vengono fusi tramite un laser ad alta potenza per creare, strato dopo strato, degli oggetti tridimensionali. Questa tecnologia è utile per produrre parti metalliche resistenti che supportano geometrie complesse. Tuttavia, essendo le polveri differenti l’una dalle altre e avendo quindi caratteristiche proprie, le condizioni di lavorazione possono subire molte variazioni, a partire delle impostazioni del laser per arrivare alle interazioni tra le varie particelle di polvere. Di conseguenza, le proprietà degli oggetti che vengono stampati possono variare notevolmente.
Per realizzare questa applicazione, il team di ricercatori guidato da Li Ma, ingegnere senior presso l’APL, ha utilizzato un modello di fluidodinamica computazionale (CFD) per misurare con precisione le variazioni di temperatura e i tassi di raffreddamento durante il processo di stampa, in relazione all’orientamento e alla dimensione dei grani. La fluidodinamica computazionale (CFD) è una disciplina che impiega simulazioni al computer per prevedere il comportamento dei flussi di materiale, basandosi sulle leggi di conservazione di massa, quantità di moto ed energia. Questo approccio innovativo consente non solo di prevedere la microstruttura del componente prima della stampa, ma anche di stimare le proprietà meccaniche del materiale e le prestazioni fisiche del pezzo finito.
Ali Ramazani ha sviluppato il primo modello di formazione microstrutturale a campo di fase, integrando i risultati ottenuti dal modello CFD. Questo approccio ha migliorato la precisione e la validità delle simulazioni. Tuttavia, il suo contributo, seppur significativo, non è stato sufficiente a risolvere tutte le problematiche relative alla rilevazione dei dati. La produzione di un singolo componente con la tecnologia LPBF implica infatti milioni di interazioni tra polvere e laser, richiedendo un’enorme quantità di tempo di calcolo e rendendo così la simulazione di ogni piccola sezione estremamente complessa.
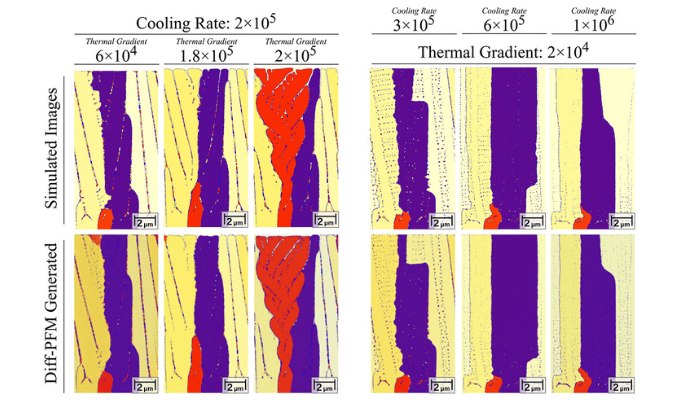
In questa immagine sono stati messi a confronto i risultati del modello di campo probabilistico di diffusione dell’APL con i risultati delle simulazioni. Il modello di APL rileva accuratamente la formazione della microstruttura e la crescita dei grani osservata nei risultati simulati.
Così, la svolta è arrivata da Hudson Liu, uno stagista dell’APL Student Program to Inspire, Relate, and Enrich (ASPIRE), nonché studente delle scuole superiori della Gilman School di Baltimora. Ha infatti teorizzato un modello di apprendimento automatico che avrebbe ridotto notevolmente la necessità di eseguire costose simulazioni. In sintesi, Hudson Liu ha integrato diversi modelli di machine learning preesistenti per sviluppare quello che il team definisce “diffusion probabilistic field model”, ovvero un “modello di campo probabilistico di diffusione”. Questo modello genera immagini basate sulla velocità di raffreddamento e sul gradiente termico della stampa LPBF, quantificando le variazioni di temperatura in base a parametri come la distanza tra il punto di impatto del laser e il metallo solido circostante.
Hudson Liu ha dichiarato: “Il vantaggio principale dell’utilizzo di questo modello è la sua velocità. Il nostro modello può prevedere in pochi secondi o minuti ciò che richiederebbe ore in una simulazione”, aggiungendo: “questo permette ai ricercatori di esplorare rapidamente un’ampia gamma di parametri e a costi molto più bassi”. Il modello è stato convalidato attraverso le analisi del materiale LPBF tramite microscopio. L’addestramento del programma di Machine Learning ha richesto più di 400 simulazioni effettuate presso l’APL.
Prospettive future
Il team di ricerca sta già lavorando per addestrare dei nuovi modelli utilizzando dati video, che consentiranno di prevedere le microstrutture sia in 3D che in 2D. Con il tempo, sarà quindi possibile effettuare delle previsioni delle microstrutture di componenti più grandi e di analizzare i risultati di un maggior numero di passaggi laser.
Ma non è tutto. Il progetto, nato grazie ad un finanziamento interno all’università, è stato oggetto di interesse da parte dello Space Technology Research Institute (STRI) della NASA, che lo vorrebbe implementare per i propri servizi. Li Ma ha dichiarato: “La NASA desidera modelli validati che possano aiutarli a prevedere cosa accadrà durante la produzione e come si comporterà il pezzo finale, senza dover ricorrere a costosi esperimenti. Questo approccio è particolarmente utile se pensiamo alla produzione additiva sulla Luna o nello spazio, dove sperimentare diventa così costoso da essere praticamente impossibile.” Non desterà dunque stupore se in un futuro prossimo sentiremo parlare delle applicazioni dell’APL implementate non solo nei viaggi spaziali della NASA, ma anche in altri settori.
Cosa ne pensi dell’uso del Machine Learning con la stampa 3D? Per scoprire altre notizie di questo tipo, consulta la nostra pagina delle notizie. Lascia un commento sui nostri canali Facebook, LinkedIn e YouTube. Segui tutte le novità dal mondo della stampa 3D nella nostra Newsletter settimanale!
Descrizione dell’immagine di copertina: nell’immagine è raffigurata la microstruttura della superlega a base di nichel rinforzata per precipitazione utilizzata per convalidare il modello di APL e la sua previsione del tasso di raffreddamento.
*Crediti fotografici: ASM International, 2024.