Honda sfrutta e perfeziona la tecnologia Laser Powder Bed Fusion per i veicoli
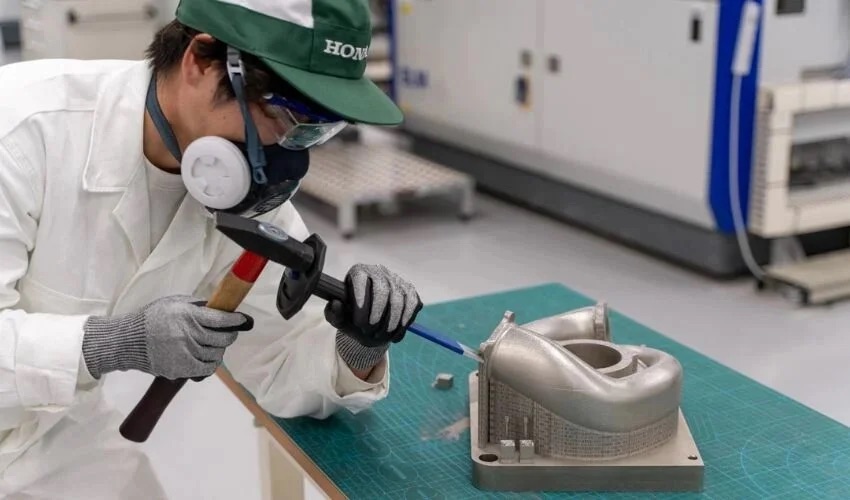
La casa automobilistica giapponese Honda ha recentemente rivelato in che modo si serve della stampa 3D per aumentare l’efficenza e le prestazioni dei propri veicoli. La tecnologia scelta? La Laser Powder Bed Fusion (LPBF). Questa tecnologia di stampa 3D dei metalli consente di creare geometrie complesse impossibili da ottenere con la fusione o le tecniche di forgiatura tradizionali, rendendola così adatta alla produzione rapida di pezzi unici o di piccole quantità di vari prodotti. Tuttavia, il processo non è privo di complicazioni. Per questo motivo, i centri di ricerca e sviluppo di Honda hanno adottato una tecnologia che simula e prevede la deformazione del materiale, per risolvere le problematiche che possono emergere dall’uso della LPBF.
Uno degli aspetti principali ottimizzati all’interno degli stabilimenti Honda è quello relativo al flusso di gas usato nella tecnologia LPBF. Durante il funzionamento, un gas inerte viene fatto circolare nella camera per creare un ambiente privo di ossigeno. Lo scopo di questo gas è eliminare i fumi e gli schizzi generati dalla fusione del metallo e impedire all’ossigeno di entrare nella camera perchè causerebbe vuoti e difetti alle parti stampate.
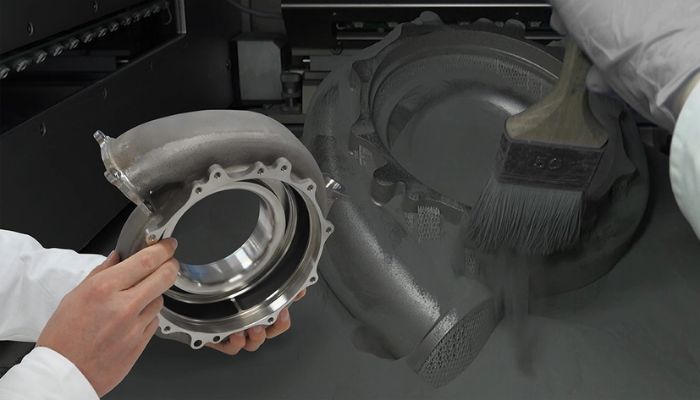
Un componente prodotto da Honda con la tecnologia LPBF.
L’azienda spiega che quanto più grande è l’area di stampa, tanto questa risulti essere più sensibile alle influenze esterne. Nelle zone in cui il flusso del gas inerte è più lento, infatti, fumi e schizzi di metallo non vengono eliminati correttamente, causando problemi di modellazione. Per risolvere questa criticità, il team utilizza una telecamera ad alta velocità per monitorare l’eliminazione degli schizzi strato per strato. Confrontando questi dati con la distribuzione della velocità del flusso d’aria, misurata tramite un sensore anemometrico, riescono a individuare la fonte del problema. Questi dati permettono di ottimizzare la velocità del flusso e definire condizioni precise per l’intera area di stampa.
Honda sta utilizzando questo metodo, che alterna test, errori e raccolta dati per migliorare altri aspetti della tecnologia LPBF. Fotografando ogni strato per verificare lo stato di fusione, nonché la temperatura e la potenza del laser, il team può comprendere meglio il materiale, il laser e il flusso di gas.
Una volta creato un pezzo, il team Honda ne testerà anche la resistenza alla trazione. L’obiettivo è formare parti in cui ogni strato non contenga spazi vuoti. Se il laser non è abbastanza potente, le sfere (ossia le parti in cui la polvere di metallo si fonde e si solidifica) saranno troppo piccole, creando uno strato con spessore insufficiente e vuoti nella parte stampata. Monitorando attentamente questi processi, possono ottimizzarli e garantire pezzi di alta qualità.
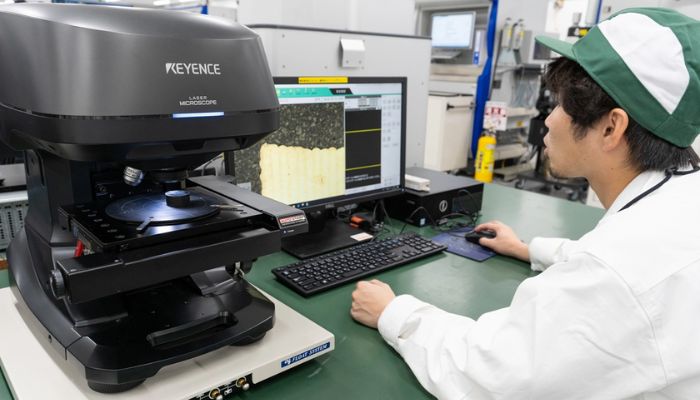
Fase di test di una parte stampata.
Cosa stampa Honda in 3D?
Honda ha una lunga storia di utilizzo e supporto della produzione additiva. Nel 2016, l’azienda ha stampato in 3D i componenti del suo veicolo Micro Commuter e nel 2020 ha aggiornato le proprie auto con alberi motore in metallo leggero stampati in 3D. Nel 2023, Honda ha anche fatto notizia investendo in Seurat Technologies, un’azienda di produzione additiva che si concentra sulla creazione di parti metalliche. L’azienda utilizza la stampa 3D per produrre parti destinate alla Formula 1 e manubri per sedie a rotelle.
Componenti per la Formula 1
Per la Formula 1, ottimizzare il peso e la resistenza delle parti è essenziale. Ecco perché, dal 2020, Honda utilizza la produzione additiva per produrre rapidamente parti uniche con forme complesse e pareti sottili. Ad esempio, Honda ha utilizzato la stampa 3D dei metalli per realizzare i pistoni, che in precedenza venivano realizzati in alluminio forgiato. Ora si utilizza il ferro che, pur avendo una densità e un peso superiori all’alluminio, può essere lavorato con la stampa 3D per ottenere componenti abbastanza leggeri e resistenti da sopportare la pressione della combustione.
Il turbocompressore è un’altra parte che Honda realizza grazie alla tecnologia LPBF per i veicoli di F1. In precedenza, queste parti venivano realizzate mediante la tecnologia di fusione di precisione. Oggi sono realizzati in Inconel, una lega a base di nichel altamente resistente al calore. L’alloggaimento delle turbine e i pistoni stampati in 3D hanno superato i rigorosi standard dimensionali, riducendo al contempo i tempi di produzione e i costi.
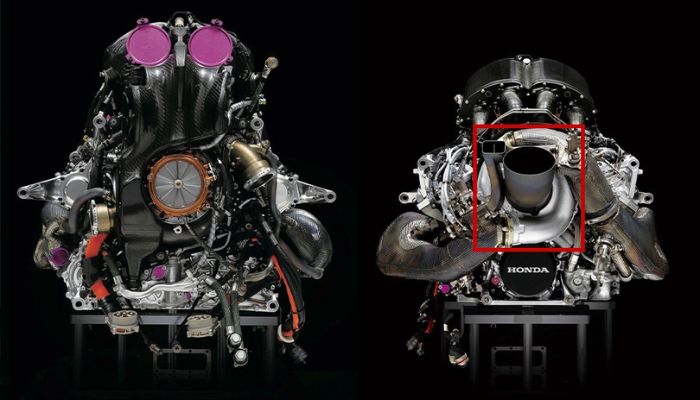
Area stampata in 3D del turbocompressore.
Manubri per sedie a rotelle da corsa
Honda produce anche sedie a rotelle da corsa e utilizza la stampa 3D per creare i suoi manubri in alluminio. La particolarità è che possono essere personalizzati per adattarsi all’atleta. Tradizionalmente, questi manubri venivano saldati insieme alla struttura, rendendo difficile la personalizzazione del veicolo. Grazie alla produzione additiva, è stato possibile non solo creare dei manubri specifici per gli atleti, ma anche di ottimizzarne il peso con delle maniglie che incorporano una struttura reticolare. Invece di adattare l’uomo all’oggetto, l’oggetto si adatta all’uomo, migliorando le prestazioni di un pezzo.
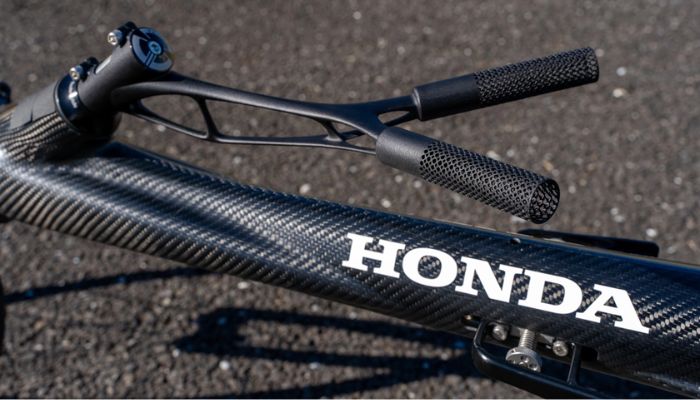
Manubri per media a rotelle da corsa
Honda ha utilizzato l’ottimizzazione topologica per creare i manubri, avendo cura di immaginare le strutture più efficienti possibili, senza l’aggiunta di componenti superflui. I manubri e le parti dell’auto di F1 sono solo due esempi di come il marchio sta sfruttando la tecnologia 3D, ma sicuramente ci saranno molti altri casi d’uso in futuro. Per saperne di più su come Honda si serve della stampa 3D, clicca qui.
Cosa ne pensi dell’uso che Honda fa della stampa 3D? Faccelo sapere lasciando un commento qui sotto o sui nostri canali social Facebook, Linkedin e YouTube! Non dimenticare di iscriverti alla nostra newsletter settimanale per ricevere tutte le notizie sulla stampa 3D direttamente nella casella di posta!
*Crediti per tutte le foto: Honda