APG produce ganasce per mandrini da tornio con la tecnologia MoldJet di Tritone
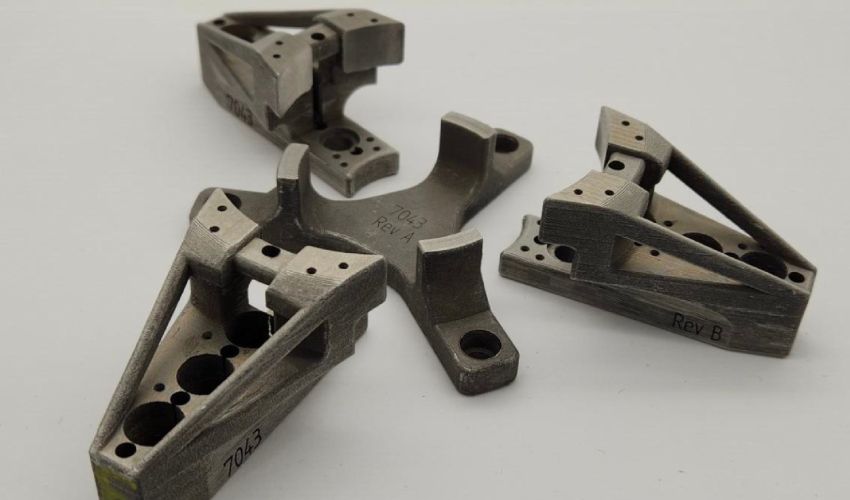
Uno dei vantaggi della produzione additiva più noti e apprezzati dalle diverse industrie è la libertà di design. Pur dovendo seguire regole e determinate limitazioni in funzione del pezzo da produrre, il Design for Additive Manufacturing (DfAM) permette di ottenere geometrie e performance spesso non ottenibili con altri metodi. Tecniche come il design generativo o l’ottimizzazione topologica sono sempre più utilizzate in combinazione alla stampa 3D per reimmaginare il design di pezzi in maniera non convenzionale e renderli più performanti, leggeri e ottimizzati.
L’azienda statunitense Alpha Precision Group (APG), leader nella fornitura di componenti di precisione, valvole speciali e componenti metallici, ha deciso di utilizzare la stampa 3D proprio a questo fine, per trovare una soluzione ad un problema non risolvibile con altre tecniche e processi. Riprogettando e stampando in 3D delle ganasce di mandrini per tornio, prima realizzate con lavorazione CNC, l’azienda è stata in grado di migliorare il suo processo produttivo. In che modo? Vediamolo di seguito nel dettaglio.
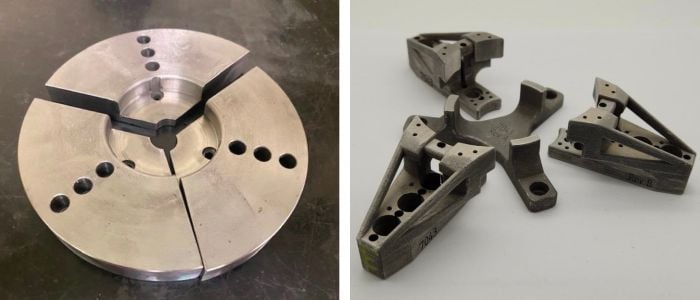
A sinistra, il design originale del mandrino prodotto con CNC. A destra, il nuovo design leggero delle ganasce prodotte con la tecnologia additiva MoldJet di Tritone.
Il Design for Additive Manufacturing per ottenere ganasce per mandrino più leggere
Nella sua attività di oltre 50 anni, APG ha raggruppato sotto il suo marchio aziende pioniere nelle tecnologie di miglioramento dei materiali e dei processi. L’azienda lavora oggi con diverse tecniche, tra cui lo stampaggio a iniezione di metalli (MIM) e la produzione additiva.
Uno degli ultimi esempi di utilizzo della produzione additiva in metallo da parte di APG, per produrre parti finali, è stata la stampa 3D di nuove ganasce per mandrini da tornio. Il ricorso alla produzione additiva è stato dettato da una problematica specifica presso uno degli impianti dell’azienda per la produzione di polveri metalliche. Il problema risiedeva nel peso eccessivo delle ganasce dei mandrini, che metteva a rischio il rispetto delle tolleranze critiche durante la lavorazione dei pezzi.
Le ganasce convenzionali in acciaio dolce, utilizzate per tenere gli ingranaggi durante la lavorazione, erano troppo pesanti e generavano una forza centrifuga eccessiva quando il tornio girava ad alto numero di giri. Per trattenere il pezzo era quindi necessaria un’elevata forza di serraggio, che a sua volta comportava una distorsione nel pezzo.
Dopo aver provato a ridurre il peso delle ganasce con la lavorazione CNC, senza ottenere risultati soddisfacenti, il progetto è passato al team Additive dell’azienda che ha esplorato nuove soluzioni per migliorare il meccanismo. Il team Additive di APG ha immaginato una riprogettazione delle ganasce, sfruttando appieno i vantaggi dalla stampa 3D, tra cui la maggiore libertà di design offerta dal DfAM (Design for Additive Manufacturing).
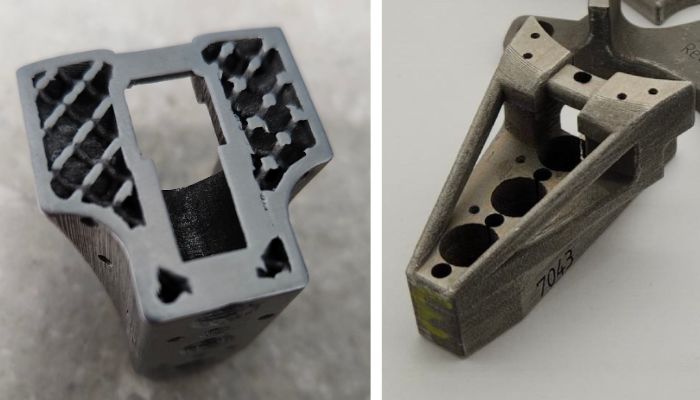
A sinistra, la sezione trasversale della nuova ganascia del mandrino con design interno a reticolo. A destra, il dettaglio del nuovo design esterno della ganascia.
Per ridurre al minimo il peso di ogni componente del sistema, APG ha dovuto riprogettare l’esterno e l’interno dei componenti, optando per strutture interne reticolari. In quanto alla tecnologia utilizzata per ottenere queste complesse strutture, la scelta è ricaduta sul processo di produzione additiva in metallo MoldJet di Tritone.
La tecnologia additiva MoldJet di Tritone
La tecnologia MoldJet è un innovativo processo additivo per metallo e ceramica che, come materiale, non utilizza polveri ma una pasta e che consente la produzione di parti su scala e con velocità notevole. A svilupparlo è stato il produttore israeliano Tritone, che ha progettato MoldJet per produrre parti di geometria complessa, con alta densità e in medi volumi. Per realizzare le ganasce è stato utilizzato il sistema Dominant di Tritone.
Il processo funziona in più step e con più vassoi di stampa, che operano in parallelo e in modo indipendente. Il primo step è la stampa di stampi polimerici, il secondo è la deposizione della pasta metallica negli stampi, il terzo è la fase termica di solidificazione del materiale tramite aria calda, e infine c’è il controllo qualità degli strati in tempo reale con correzione automatica, tramite telecamere dotate di IA.
Uno dei vantaggi di questa tecnologia è la flessibilità offerta, che consente, ad esempio, di cambiare facilmente cartucce di materiale, di produrre in un solo processo pezzi con uno spessore di strato diverso o geometrie diverse. Inoltre, il post-processing è molto semplice dato che gli stampi polimerici si dissolvono completamente, e la parte è subito pronta per la sinterizzazione.
Nel caso di APG, questi aspetti sono stati fondamentali per raggiungere l’obiettivo di riduzione di peso delle ganasce tramite una geometria reticolare proprietaria per tutti i componenti. Questa è stata realizzabile con la tecnologia MoldJet proprio perché, durante la stampa, tutto lo spazio vuoto del reticolo è stato occupato dal materiale di stampo solubile. Questo materiale è stato poi eliminato con il post-processing hands-free di Tritone, consentendo di ottenere una struttura molto più leggera di quella che si sarebbe potuta produrre con tecnologie concorrenti.
Ottimizzazione dei componenti e del processo produttivo grazie alla stampa 3D
I risultati del progetto sono andati anche oltre le aspettative di APG. Il peso delle ganasce è stato ridotto dell’84% (da 2,13 KG a 0,336 kg) e la forza di serraggio è stata ridotta del 67% rispetto al progetto originale (da 30 a 10 psi). Ciò ha permesso di raggiungere gli obiettivi prefissati e ottenere tolleranze più strette, meno scarti, riduzione dell’usura dei torni con un carico più leggero e in generale costo inferiore rispetto ad altre alternative di riduzione del peso esaminate.
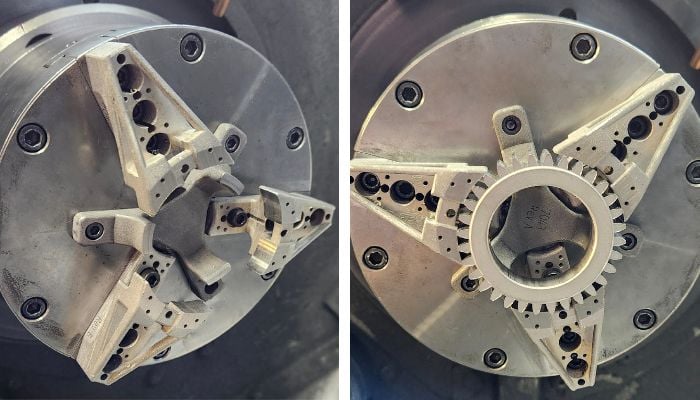
Il nuovo set di ganasce installato sul tornio, con l’ingranaggio in posizione.
Joe Taylor, ingegnere di produzione di APG ha commentato: “Siamo entusiasti dei risultati ottenuti. Non vediamo l’ora di espandere questo successo all’interno dei nostri stabilimenti e di offrire questi dispositivi “chiavi in mano” ai clienti”.
In definitiva, la tecnologia MoldJet di Tritone non ha solo consentito la risoluzione della problematica relativa alla forza di serraggio, ma ha offerto anche il potenziale per migliorare la ripetibilità complessiva e i tassi di rendimento nei processi di produzione, portando maggiore efficienza operativa, precisione e affidabilità nelle operazioni di lavorazione. Per saperne di più sulla tecnologia MoldJet e sui suoi vantaggi: QUI.
Come immagini di utilizzare queste potenzialità nella tua attività? Condividi la tua opinione sui nostri social Facebook e LinkedIn. Trovi tutti i nostri video sul nostro canale YouTube! Non dimenticare di iscriverti alla nostra Newsletter settimanale per ricevere tutte le notizie sulla stampa 3D direttamente nella casella di posta!
Crediti per tutte le foto: Tritone Technologies, Alpha Precision Group