Ford e Red Bull Powertrains usano la stampa 3D per ottimizzare i veicoli per la F1
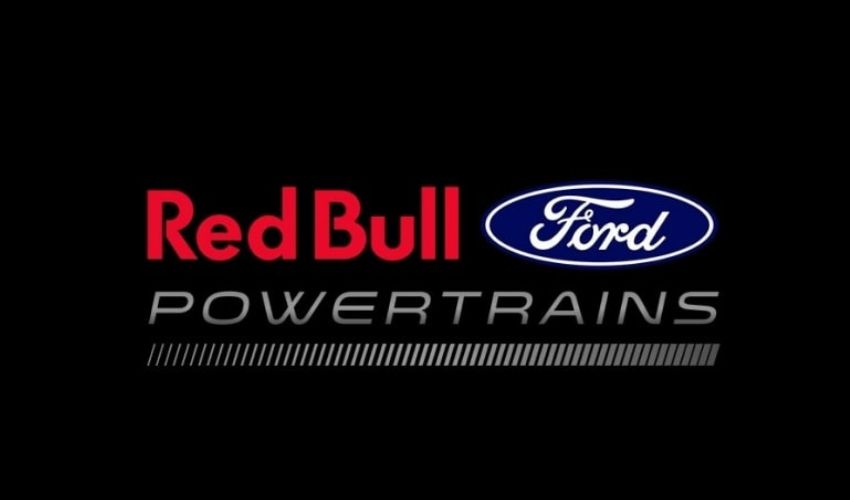
Nel 2023 Ford Motor Company ha dichiarato di aver stretto una partnership con Red Bull Powertrains per tornare a gareggiare nelle piste di Formula 1. Era da più di vent’anni, infatti, che il marchio automobilistico non sfrecciava tra gli autodromi. In cosa consiste però questa collaborazione? L’unione tra Ford Red Bull Powertrains è finalizzata a sviluppare il power unit ibrido di nuova generazione per i team della Oracle Red Bull Racing e della Scuderia AlphaTauri. In questo modo, le auto della scuderia di Red Bull Racing saranno conformi agli standard imposti dalla FIA, ossia la Federazione Internazionale dell’Automobile, per la Formula 1, che entreranno in vigore dal 2026. Questi prevedono, tra le altre cose, che le auto siano più aerodinamiche e che si servano carburanti carbon neutral. Per permettere ai veicoli di raggiungere questi standard, Ford Motor Company ha scelto di utilizzare anche le tecnologie di produzione additiva.
Infatti, da due anni, Ford si sta servendo delle tecnologie di stampa 3D per potenziare le auto da corsa e adattarle ai nuovi standard imposti dalla FIA. Finora ha già prodotto oltre 1000 componenti stampate in 3D per Red Bull Powertrains. Attualmente, Red Bull Powertrains, azienda che produce i propulsori proprietari dell’azienda Red Bull, collabora con Honda, ma dal 2026 sino al 2030 Ford diventerà il nuovo partner ufficiale. Le due aziende stanno già lavorando in sinergia per potenziare le auto da corsa destinate alle gare di Formula 1. L’obiettivo, che rappresenta una vera e propria sfida, è quello di ricreare da zero il power unit dei veicoli della scuderia Red Bull Racing, sfruttando al massimo il poco tempo a disposizione.
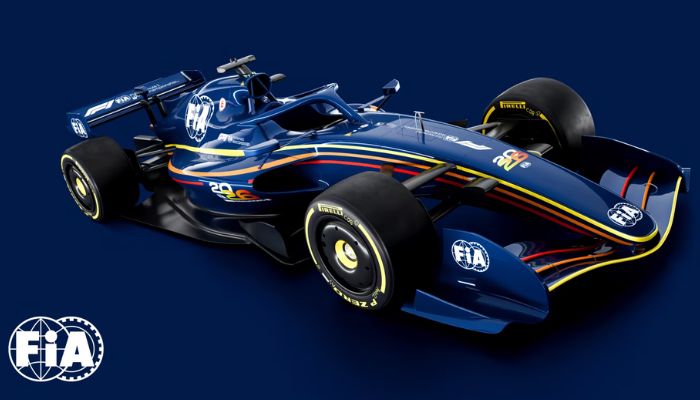
Nel 2024, FIA ha presentato sia il nuovo Regolamento Tecnico 2026 che le prime immagini di come dovrebbe essere la nuova generazione di vetture per la F1. (Crediti fotografici: FIA)
I nuovi standard della FIA per la Formula 1
Per rendere le gare più sostenibili e al passo con le esigenze della modernità, sono stati stabiliti degli standard molto alti che ogni casa automobilistica in gara deve raggiungere entro il 2026. Le vetture dovranno essere, complessivamente e rispetto alle misure attuali, più leggere di 30 kg, più corte di 20 cm e più strette di 10 cm. Inoltre, per favorire i sorpassi, ogni macchina deve essere dotata di un doppio sistema di aerodinamica attiva, sia posteriore che anteriore, che andrà a sostituire l’attuale sistema di riduzione della resistenza aerodinamica, il Drs. I carburanti utilizzati devono essere inoltre sostenibili e il propulsore della macchina, ossia il power unit, deve essere per metà ibrido e per metà endotermico. Riassumendo, la F1 vuole regalare ai milioni di spettatori non solo gare più emozionanti (l’aumentata richiesta di aerodinamicità serve a favorire i sorpassi anche sulle piste cittadine come quelle di Monaco e Baku), ma anche più green. Per rispettare dunque le esigenti richieste imposte dalla FIA per la F1, Ford e Red Bull Powertrains stanno collaborando e adottando tecnologie avanzate come la produzione additiva, il cloud computing di Oracle e la suite di software industriali Siemens Xcelerator per ottimizzare i processi.
Scansione a raggi X e TC per l’ispezione di componenti ad alte prestazioni
Per potenziare le auto da corsa di Red Bull Racing, Ford ha infatti già prodotto più di 1000 componenti stampati in 3D finalizzati a rendere il power unit delle auto da corsa più efficiente e perfettamente in linea con le nuove regolamentazioni. Ford ha prodotto dei componenti ad alte prestazioni, servendosi sia di materiali come il metallo che i polimeri, che devono resistere ad ambienti particolarmente estremi, in questo caso a velocità che raggiungono oltre i 300 km/h orari e, di conseguenza, a calori intensi. Queste parti necessitano quindi di essere collaudate per valutarne la resistenza meccanica, la durezza e la conformità geometrica. Ford ha prodotto per Redbull Powertrains componenti come le piastre fredde delle batterie e delle piastre di raffreddamento per altri sistemi, che sono state sottoposte a scansioni a raggi X e Tomografia Computerizzata (TC).
Si tratta di strumenti molto utili per effettuare valutazioni analitiche dei componenti nelle loro strutture più interne, grazie alla creazione di modelli digitali delle parti ottenute a seguito dei dati raccolti dalle scansioni. La TC permette infatti di rilevare sia la presenza di vuoti all’interno della parte stampata, sia eventuali zone soggette a delaminazione, fenomeno per cui gli strati creati con la stampa si separano l’uno dall’altro. I dati reperiti tramite queste scansioni permettono quindi di trattare in maniera più efficiente gli eventuali problemi che possono insorgere durante le varie prove meccaniche a cui vengono sottoposte le parti e, di conseguenza, ottimizzare e velocizzare la produzione. L’Additive Manufacturing, unita quindi alle procedure avanzate per l’ispezione 3D, permette che si producano delle parti altamente performanti e sicure. Tuttavia, Ford non si serve solo delle scansioni per effettuare delle ispezioni sulle componenti stampate in 3D: tutte le parti prodotte vengono sottoposte a dei test ulteriori all’interno del laboratorio metrologico dell’azienda.
Ford e l’uso della stampa 3D oltre la Formula 1
Ford non si serve della stampa 3D unicamente per creare le componenti dei veicoli da corsa che gareggeranno in Formula 1, ma è da anni che utilizza questa tecnologia per adempiere a vari scopi. Nel 2023, in Germania, l’azienda ha inaugurato il Cologne Electrification Center, un centro specializzato nell’uso della stampa 3D per supportare la produzione della prima serie di veicoli 100% elettrici realizzati in Europa. Al Cologne Electrification Center vengono utilizzate dodici stampanti 3D ad alta tecnologia per produrre un’ampia varietà di componenti in polimero e metallo. Queste parti possono partire da pochi centimetri di lunghezza e avere un peso di soli 30 grammi, a raggiungere i 2,4 metri di lunghezza e un peso di 15 chilogrammi.
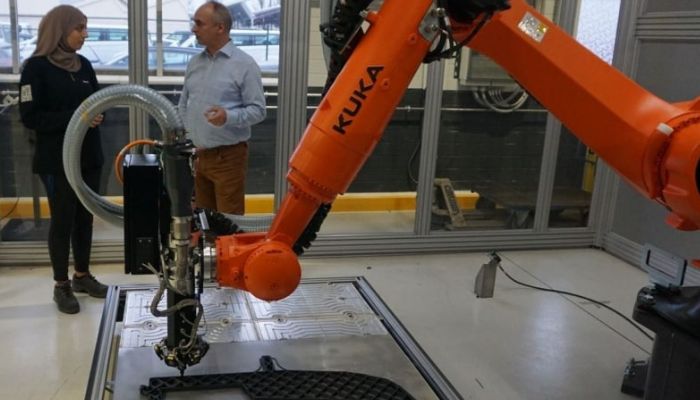
Foto scattata al Cologne Electrification Center, nello stabilimento di Ford in Germania. (Crediti fotografici: Ford Media Center)
Ma Ford non è sicuramente nuova nel campo della sperimentazione tecnologica. La sede tedesca dell’azienda si serve della stampa 3D circa dagli anni Novanta, dove gli ingegneri del centro di sviluppo di Merkenich hanno iniziato a stampare in 3D componenti per veicoli di prova e prototipi. Ma non solo: nel 2019 nel Ford Research and Innovation Center nel Michigan è stata prodotta la più grande parte metallica mai realizzata con la stampa 3D. Il team ha riprodotto un collettore di aspirazione in alluminio per il motore di una Ford F-150. Invece, nello stabilimento Ford di Valencia, in Spagna, è stato creato un catalogo di 5.000 parti stampabili in 3D, destinate a offrire soluzioni innovative per le varie fasi del processo produttivo dello stabilimento. Solo nel 2021, sono state create un totale di 20.000 parti stampate. Infine, Ford si serve della stampa 3D per automatizzare i processi di produzione.
Non resta dunque che attendere il 2026 per vedere sfrecciare sui circuiti di Formula 1 le vetture nate dalla collaborazione tra Red Bull Powertrains e Ford. Con il passare dei mesi è probabile che Ford progetti, introduca e implementi altre componenti stampate in 3D per migliorare la performance in gara delle auto destinate alle corse automobilistiche del prossimo anno. Ciò che è certo è che, nel frattempo, Ford continuerà a investire nella produzione additiva non solo per sviluppare componenti ad alte prestazioni, ma anche per rendere il settore automotive in generale sempre più efficiente, grazie alla sua esperienza di quasi un secolo e alla capacità di sfruttare le tecnologie più avanzate.
Cosa ne pensi della collaborazione tra Ford e Red Bull Powertrains? Se ti interessa l’argomento, non perderti la nostra pagina esclusiva dedicata alla stampa 3D nel settore automotive. Lascia un commento sui nostri canali Facebook, LinkedIn e YouTube. Segui tutte le novità dal mondo della stampa 3D nella nostra Newsletter settimanale!
*Crediti per la foto di copertina: Ford Media Center