Fibra corta o continua: quale tipo di rinforzo scegliere per le parti stampate in 3D?
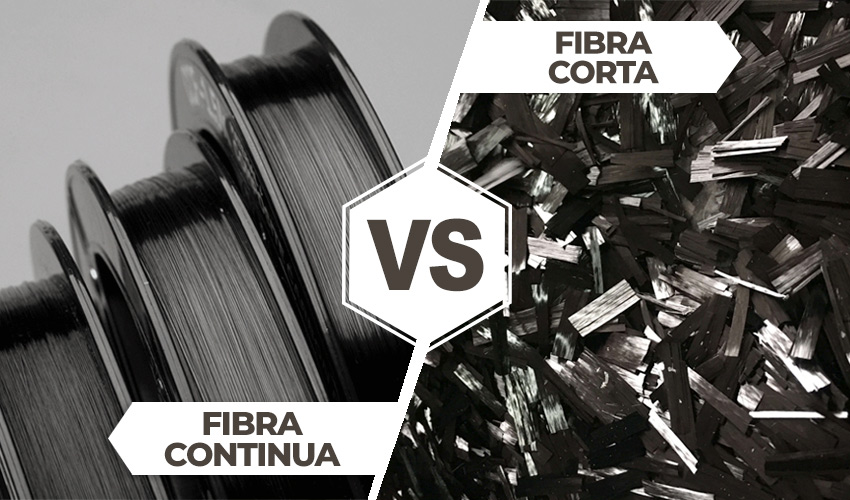
Quando si vogliono conferire proprietà specifiche e superiori alle parti stampate in 3D, spesso si ricorre alla stampa 3D di compositi. Questi possono essere persino più resistenti di alcuni metalli e offrono alte prestazioni. I materiali compositi sono formati da almeno due materiali che vengono combinati per ottenere proprietà nuove o migliorate rispetto a quelle dei materiali di partenza. Come possiamo immaginare, esistono numerosi materiali compositi, noi qui ci concentreremo in particolare sui materiali compositi formati da una matrice polimerica e da un rinforzo di fibre. Nell’industria della stampa 3D la fibra di carbonio, la fibra di vetro e il kevlar sono tre dei materiali in fibra più comuni utilizzati per i compositi.
In questo articolo analizzeremo la stampa 3D di compositi rinforzati con fibre corte e continue. Queste due tecniche danno risultati diversi e vedono l’utilizzo di tecnologie diverse, quella a cui daremo rilievo è la tecnologia più diffusa, ovvero quella a estrusione di materiale. Ma quali sono dunque le similitudini e le differenze tra queste due tecniche e come scegliere il tipo di rinforzo più adatto ad un’applicazione specifica? Vediamolo qui di seguito.
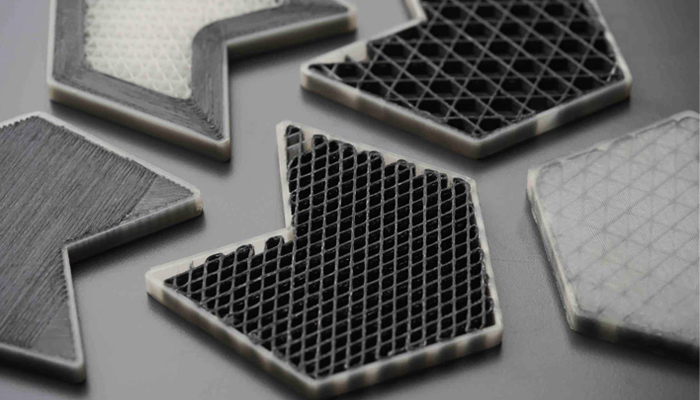
Crediti: Anisoprint
Caratteristiche dei materiali compositi a fibra corta e continua
Per fibre corte intendiamo pezzi più piccoli di materiale fibroso, la cui lunghezza può variare da centimetri a millimetri o anche meno. Si tratta di un processo simile a quello utilizzato per rinforzare il calcestruzzo con pezzi di armatura. Le fibre si disperdono nella matrice plastica e agiscono come rinforzo in tutto il materiale. Le fibre continue, invece, sono lunghi fili che si estendono per tutta la lunghezza della parte composita. Queste fibre vengono integrate in una matrice plastica attraverso il processo di stampa 3D, creando un materiale composito che combina le proprietà di entrambi. Prima di passare al processo di produzione additiva in sé e ai punti da tenere in considerazione per la creazione di queste parti, è importante conoscere le caratteristiche di entrambi i rinforzi.
In entrambi i casi troviamo la stessa composizione: un rinforzo (fibra) e una matrice (polimero). Il primo fornisce le proprietà meccaniche, mentre il secondo funge da contenitore e, con l’aiuto di una resina, assicura che i due elementi siano tenuti insieme, cioè che la fibra aderisca al materiale durante la produzione. Una volta scelti i composti della matrice (tra i polimeri più frequenti troviamo PLA, ABS, polipropilene, HIPS, PETG, ecc.) e le fibre di rinforzo (vetro, carbonio o aramide), si passa ad unirli in un unico materiale.
Le fibre corte possono essere ottenute mediante un processo di estrusione: la miscela di fibra e matrice viene fusa ed estrusa per formare un singolo filamento. Durante questo processo, la temperatura e la velocità possono essere controllate per garantire una buona distribuzione delle fibre. Le fibre continue, invece, quando formano filamenti, possono essere coestruse con una resina speciale attraverso un processo in cui la miscela viene mescolata, polimerizzata e solidificata con la resina. In alcuni casi, esistono sistemi di produzione che stampano direttamente la matrice e il rinforzo allo stesso tempo durante la deposizione di strati successivi, ma di questo parleremo più avanti. In entrambi i casi, le fibre corte e continue devono essere pulite e prive di contaminanti per garantire una buona adesione alla matrice polimerica.
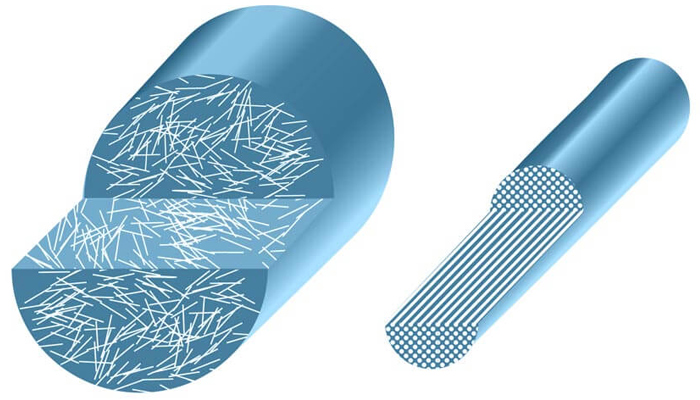
Differenza della disposizione delle fibre corte e continue nella matrice (Crediti: Coperion)
Se ci concentriamo sulle caratteristiche dei materiali rinforzati stessi, vediamo che esse differiscono notevolmente a seconda del polimero utilizzato come matrice e della scelta del tipo di fibra. Ovviamente, se il materiale plastico di base è un tecnopolimero, il composito avrà proprietà più avanzate rispetto a quelle dei materiali plastici a matrice standard. Ad esempio, se un composito ha come polimero di matrice il polipropilene, avrà una buona resistenza all’usura di base, capacità di assorbimento degli impatti e maggiore tenacità e flessibilità. Se invece si utilizza il PLA, il composito sarà più facile da stampare, ma avrà una maggiore tendenza alla rottura a causa della bassa resistenza del materiale.
Come menzionato, esistono tre tipi principali di fibre, sia corte che continue: carbonio, vetro e aramide (Kevlar). Le fibre di carbonio sono le più utilizzate nell’industria manifatturiera, grazie all’elevata resistenza e rigidità che offrono ai pezzi finali. I rinforzi in fibra di vetro sono generalmente più accessibili e offrono anch’essi una buona resistenza, anche se non quanto il carbonio. Infine, le fibre di kevlar sono spesso utilizzate nei giubbotti antiproiettile per la loro elevata resistenza agli urti e agli impatti. In ogni caso, lo scopo dell’utilizzo di fibre di rinforzo corte e continue è quello di ottenere pezzi resistenti e leggeri.
Processi di stampa 3D
La maggior parte delle stampanti 3D in grado di elaborare materiali compositi si basa sul processo di estrusione di polimeri. Per quanto riguarda la stampa 3D FFF di fibra corta, il processo è quello classico. Le fibre corte tagliate in piccoli pezzi vengono mescolate al materiale plastico per formare una bobina di filamento che può essere utilizzata con stampanti 3D FFF. In questo caso, le fibre sono semplicemente sospese nel termoplastico, che viene riscaldato ed estruso per formare la parte strato per strato proprio come qualsiasi altra parte realizzata con questa tecnologia. Sarà però necessario un ugello temprato per resistere ai fili di fibra abrasivi.
La stampa 3D di compositi a fibra continua è invece più complessa, nel processo di estrusione di materiale è spesso necessario un secondo ugello per depositare separatamente la matrice e il filo di fibra continuo. In alternativa, la testina a ugello singolo deve avere una costruzione specifica per miscelare la fibra con la matrice. Il processo consiste nel disporre delle fibre continue e con una direzione specifica all’interno della matrice. Quest’ultima funge da involucro che contiene le fibre di rinforzo. Per garantire l’adesione delle fibre con la matrice, si utilizza solitamente una matrice o un riempimento a base di resina termoindurente. Questa viene quindi polimerizzata tramite raggi UV o sorgente termica per fondere insieme gli strati e i materiali. La descrizione del processo è volutamente generica, poiché esistono numerose tecnologie proprietarie per la stampa 3D di compositi in fibra continua che differiscono, seppur minimamente, le une dalle altre.
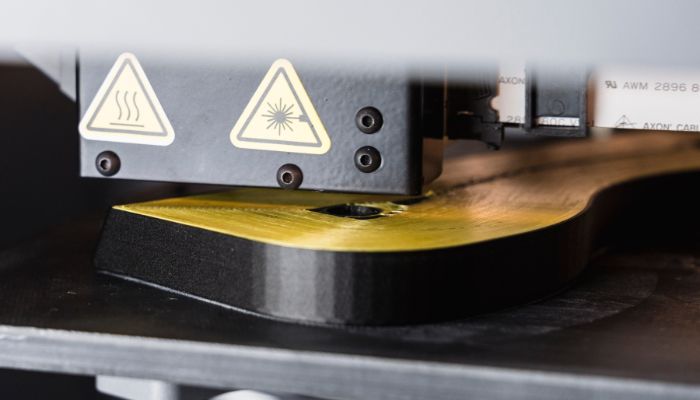
Stampa 3D di una matrice polimerica e rinforzo con fibra di kevlar. (Crediti: Markforged)
Un aspetto importante quando si stampa con fibre, in modo particolare quelle continue, è l’uso di software di analisi ad elementi finiti (FEA), ovvero un metodo computerizzato che consente di prevedere in che modo un prodotto reagirà a forze e stimoli esterni. Questo permette di analizzare le caratteristiche dei materiali e definire con precisione il modello secondo cui disporre le fibre continue nella matrice. D’altro canto, ciò significa anche andare incontro ad alcune limitazioni di design per privilegiare il corretto posizionamento delle fibre e quindi le performance del pezzo. Le proprietà specifiche del materiale saranno così definite secondo un processo controllato. Non è esattamente lo stesso invece per i compositi rinforzati con fibre corte, poiché in questi non è possibile controllare la quantità e la posizione delle fibre depositate, rappresentando esse un tutt’uno con la matrice.
Vantaggi e limiti
Come sappiamo, alcuni dei principali vantaggi della stampa 3D con i compositi includono una maggiore flessibilità e velocità di produzione, oltre alla possibilità di creare parti complesse rispetto ai metodi più tradizionali. Inoltre, come appena menzionato, un vantaggio importante che si può riscontrare con questa tecnologia, a patto che si utilizzino fibre continue, è che consente di controllare il processo di deposizione e di decidere dove e come posizionare il rinforzo per i pezzi finali.
Se ci concentriamo sui vantaggi delle fibre corte e continue come rinforzi nella stampa 3D, possiamo trovare alcuni punti in comune. Entrambi i tipi di fibre offrono una resistenza meccanica superiore rispetto alle plastiche non rinforzate. In particolare, migliorano la rigidità del materiale e ne aumentano la resistenza alla fatica e agli urti. Inoltre, le fibre come quelle di carbonio sono molto leggere, il che contribuisce a contenere il peso dei pezzi in cui questo gioca un ruolo fondamentale. Allo stesso modo, le fibre corte e continue presentano alcune limitazioni. Ad esempio, la necessità di attrezzature di stampa 3D specifiche per produrle. Inoltre, ci sono molti aspetti da considerare quando si lavora il materiale composito, come l’adesione tra la fibra e la matrice plastica, che può rappresentare una sfida.
D’altra parte, ci sono alcuni aspetti su cui i due tipi di fibre si differenziano. Il principale limite delle fibre corte rispetto alle fibre continue è che forniscono un rinforzo meno efficace. Questo perché l’orientamento e la distribuzione delle fibre corte lungo il composito sono più casuali, mentre le fibre continue sono costanti. Pertanto, l’effetto di rinforzo con le fibre corte è meno pronunciato, il che potrebbe non essere sufficiente per le applicazioni che richiedono un’elevata resistenza. Tuttavia, un vantaggio fondamentale dei compositi a fibra corta è che sono più facili da lavorare e generalmente più economici di quelli a fibra continua, il che li rende più accessibili. Inoltre, le fibre corte possono essere utilizzate con una più ampia varietà di materiali plastici, consentendo un’elevata flessibilità di progettazione.
Applicazioni
La scelta tra fibra continua e corta, così come la matrice polimerica, dipenderà dal tipo di applicazione e dalle prestazioni richieste. Le fibre continue sono ideali per applicazioni che richiedono elevata resistenza e rigidità, mentre le fibre corte sono più adatte a progetti che richiedono facilità di lavorazione e costi inferiori. Per questo motivo, le fibre continue sono più comunemente utilizzate per i componenti strutturali in settori avanzati, come quello automobilistico (rinforzi del telaio o componenti interni) o aerospaziale (strutture di supporto e componenti degli aerei). Possono anche essere implementate in prodotti di consumo che richiedono un’elevata resistenza, come biciclette o attrezzature sportive. D’altra parte, i compositi a fibra corta stampati in 3D sono comunemente utilizzati anche per produrre prototipi. Vengono spesso utilizzati anche per parti nell’industria dell’imballaggio, nella robotica, nei prodotti di consumo e in altri componenti che non richiedono un’alta resistenza alla trazione.
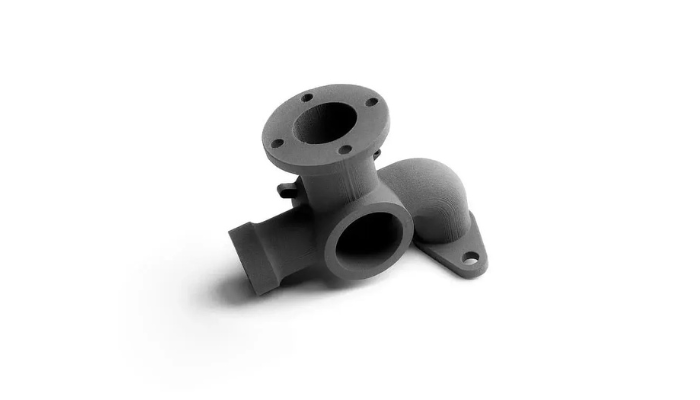
Pezzo realizzato in peek fibra di carbonio. (Crediti: Weerg)
Produttori e prezzi
Le soluzioni di stampa 3D per compositi di fibra corta e continua, pur non essendo numerose come quelle per polimeri standard e metalli, sono abbastanza varie spaziando da bracci robotici, a stampanti industriali, fino a soluzioni desktop. Tra i fornitori di soluzioni per la stampa 3D di fibre continue, Markforged offre la tecnologia Continuous Fiber Fabrication (CFF) e una serie di soluzioni desktop e industriali. Queste sono in grado di stampare compositi in PLA, TPU, Nylon bianco, Onyx™ e ULTEM rinforzati con fibra di carbonio, kevlar o fibra di vetro. Anche Anisoprint offre soluzioni per la stampa 3D con fibra continua tramite la tecnologia Composite Fiber Co-extrusion (CFC). Le soluzioni desktop offrono un’ampia flessibilità nella scelta dei materiali con un sistema aperto, mentre la soluzione industriale ProM IS 500 è compatibile con plastiche ad alte prestazioni come PEI, PEEK, PEKK e altre. Altre aziende che forniscono soluzioni di stampa 3D in fibra continua sono Continuous Composites o CEAD che offre una soluzione LFAM.
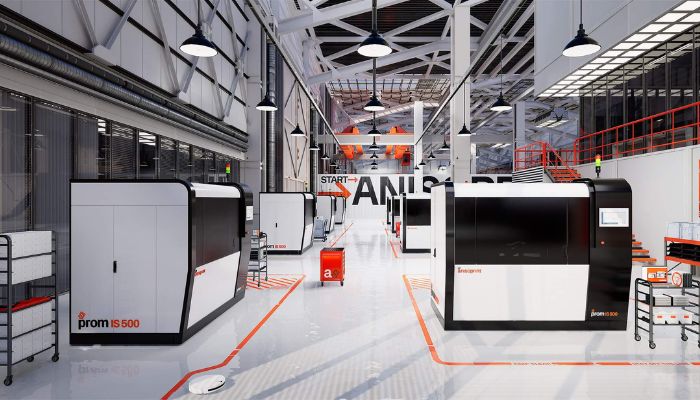
Crediti: Anisoprint
Inoltre, come menzionato, sono sempre di più le startup che studiano e brevettano nuovi processi di stampa 3D di compositi a fibra continua, tra queste troviamo Moi Composits, SphereCube, Fabheads, 9T Labs e Arevo.
Vale la pena menzionare che non esistono soltanto tecnologie per il rinforzo con fibra continua durante il processo di produzione. Ad esempio, la startup spagnola Reinforce 3D ha ideato la tecnologia CFIP (Continuous Fibre Injection Process) per il rinforzo delle parti con fibre continue nella fase di post-processing, successiva alla produzione additiva.
Per quanto riguarda i produttori di stampanti 3D per compositi a fibre corte troviamo principalmente produttori di macchine FFF capaci di processare materiali ad alte prestazioni rinforzati con fibra di carbonio o altre fibre. Tra questi vi sono Roboze, Stratasys, 3ntr, miniFactory, BigRep, WASP o Creality (la lista non è esaustiva).
Se guardiamo ai prezzi, la principale differenza è legata alla tipologia di macchina utilizzata. Sia per la stampa 3D di fibre corte che continue il prezzo è generalmente elevato per le soluzioni industriali poiché si tratta di materiali che richiedono condizioni di stampa particolari, come alte temperature per l’ugello, la camera ecc. Le macchine desktop per la stampa 3D di compositi a fibra corta possono avere un prezzo che parte dai 400€, mentre quelle per la stampa 3D a fibra continua partono dai 9.000€ circa. Per quanto riguarda le soluzioni industriali, non sempre i produttori rendono pubblici i prezzi, che possono arrivare a svariate centinaia di euro a seconda del processo e della dimensione. In tal caso, è possibile richiedere preventivi direttamente tramite i siti web ufficiali.
Utilizzi i compositi a fibra corta o continua per la stampa 3D? Faccelo sapere lasciando un commento sui nostri social Facebook e LinkedIn. Trovi tutti i nostri video sul nostro canale YouTube! Non dimenticare di iscriverti alla nostra Newsletter settimanale per ricevere tutte le notizie sulla stampa 3D direttamente nella casella di posta!