Carbon: materiali più innovativi e sostenibilità nell’Additive Manufacturing
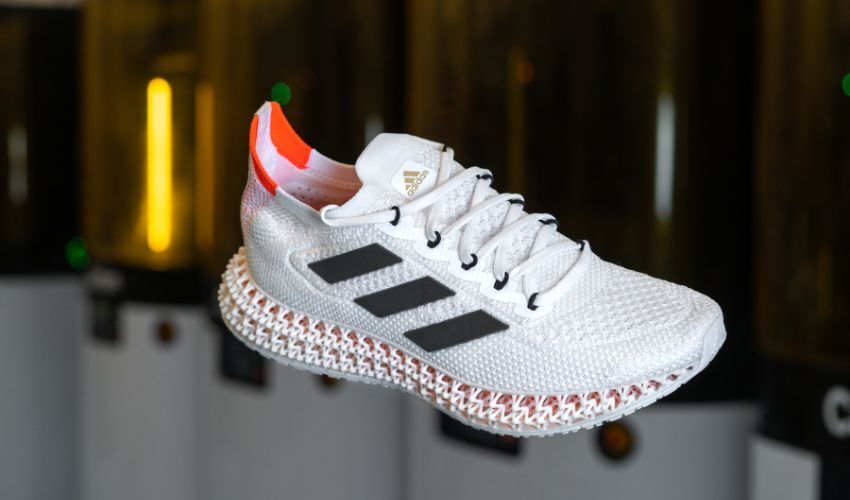
Quando Carbon è stata fondata nel 2013, ha deciso di cambiare radicalmente lo sviluppo e la manifattura dei prodotti grazie alla sua tecnologia di stampa a fotopolimerizzazione ad alta velocità, Digital Light SynthesisTM (DLS). L’azienda ha continuato ad avere successo poiché brand come Adidas, Ford Motor Company, Becton Dickinson Company e molti altri sfruttano la piattaforma Carbon DLS™ per fornire prodotti di qualità migliore in minor tempo. La rivoluzione sembra essere solo all’inizio. Oltre a migliorare continuamente la propria tecnologia, l’azienda si concentra sullo sviluppo di materiali innovativi e supporta il settore per renderlo complessivamente più sostenibile. Abbiamo incontrato Jason Rolland, vicepresidente senior del dipartimento materiali di Carbon, per sapere di più su come funzionano la tecnologia e i materiali e, naturalmente, sull’impegno dell’azienda per un mondo più rispettoso dell’ambiente.
3DN: Può presentarsi?
Certamente, mi chiamo Jason Rolland, guido il team del Dipartimento Materiali di Carbon e sono in azienda da oltre otto anni. Ho iniziato a lavorare molto presto per loro, eravamo otto dipendenti e ora siamo oltre 500 collaboratori; è stato bello guardare l’azienda crescere e vedere tutte le tecnologie che è stata in grado di sviluppare. Mi sono laureato in chimica dei polimeri presso la Virginia Tech e ho poi svolto un dottorato di ricerca nello stesso ambito all’Università della Carolina del Nord a Chapel Hill. È lì che ho incontrato Joseph DeSimone, il mio tutor di dottorato che, in seguito, mi ha portato in Carbon. Joe è uno dei cofondatori di Carbon, mi ha fatto conoscere subito la tecnologia dell’azienda e mi ha reclutato per creare la piattaforma e il team che si occupa dei materiali. Prima di questa esperienza, ero un novellino nel campo della stampa 3D ed è stato entusiasmante vedere in azione questa nuova tecnologia e capire dove poter arrivare con il suo potenziale.
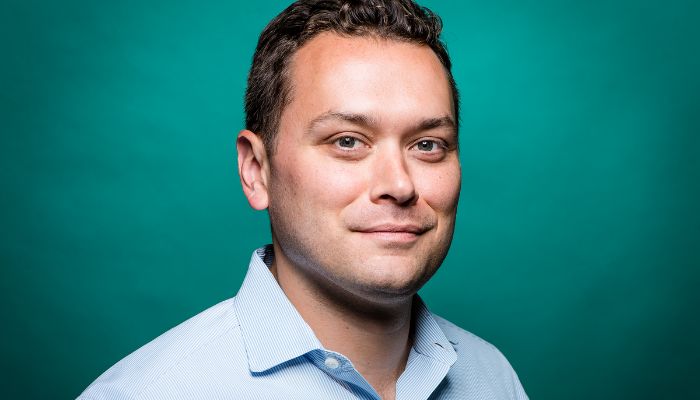
Jason Rolland, SVP Materiali, Carbon
3DN: Può raccontarci qualcosa in più su Carbon e sulla tecnologia DLS?
Sin dalle origini, in Carbon ci siamo concentrati sulla produzione della stampa 3D su larga scala. Per fare ciò, la velocità di stampa e le prestazioni dei materiali erano i due problemi principali che dovevamo affrontare. Le stampanti 3D sono piuttosto lente, indipendentemente dalla tecnologia che si utilizza, e questo aspetto incide sul costo di ciascun parte stampata, poiché impedisce di produrre volumi elevati. Per affrontare questo problema, abbiamo sviluppato la tecnologia Digital Light SynthesisTM (DLS). Con la sua applicazione, siamo stati in grado di aumentare notevolmente la velocità di stampa.
Per avere un’idea più precisa, per le nostre macchine abbiamo un piano di stampa configurato in modo simile a una macchina DLP (Digital Light Processing) con impostazione bottom-up. Al suo interno, è presente un serbatoio che contiene la resina e alla base di questo è posizionata una lastra, in basso si trova il sistema di proiezione digitale. L’innovazione chiave è stata capire l’importanza dell’ossigeno. La permeabilità dell’ossigeno attraverso la base del serbatoio può generare un sottile strato di resina non polimerizzata che è quindi costantemente presente in tutta la costruzione e che, a sua volta, riduce moltissimo le forze di adesione e aumenta la velocità di stampa.
Attraverso l’uso di questo materiale permeabile all’ossigeno alla base del serbatoio, è effettivamente possibile garantire che la polimerizzazione avvenga proprio su quell’interfaccia, polimerizzandosi al di sopra. In questo modo, è possibile avere sempre un sottile strato liquido che riduce le forze di adesione e che consente di stampare molto più velocemente. Ad oggi, con determinati tipi di geometrie, siamo in grado di stampare 10 volte più velocemente rispetto alle tradizionali stampanti 3D. Per questo abbiamo iniziato a pensare seriamente allo sviluppo dei materiali.
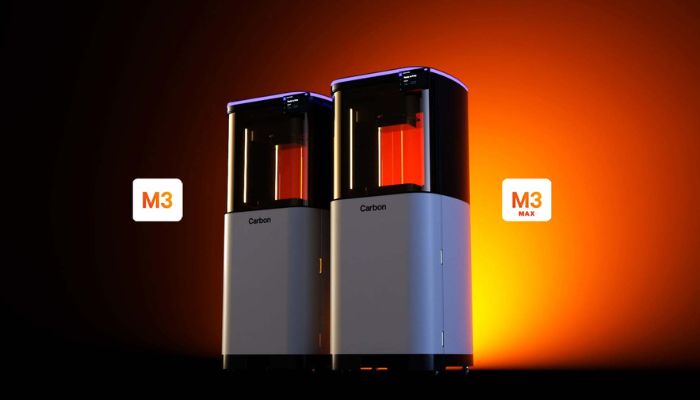
L’ultimo lancio di Carbon è stato quello delle stampanti della serie M, la M3 e la M3 Max.
3DN: Volendo approfondire questo punto, cosa può dirci sullo sviluppo dei materiali Carbon?
Ci siamo resi conto che, per consentire ai clienti di portare le applicazioni in produzione, avevamo bisogno di materiali che fossero alla pari con quelli utilizzati durante i processi di stampaggio a iniezione o con le schiume. Si è trattato di un problema davvero impegnativo da risolvere, perché disponiamo di una stampante basata sulla chimica a polimerizzazione UV e sulla modellazione della luce a UV, e sappiamo che ci sono solo alcune sostanze chimiche compatibili con questa tecnologia. Sono necessarie infatti determinate funzionalità alle estremità delle catene polimeriche. Abbiamo quindi pensato che questo aspetto fosse piuttosto limitante in termini di proprietà e formulazioni che potevamo realizzare. Per affrontare il problema, abbiamo creato alcuni sistemi di materiali a doppia polimerizzazione, che abbiamo successivamente brevettato. Ciò significa che, invece della semplice chimica a polimerizzazione UV, utilizziamo una combinazione di chimica a polimerizzazione UV e di chimica a polimerizzazione termica.
Le spiego meglio. Con la chimica a polimerizzazione si hanno a disposizione due componenti reattivi (parte A e parte B), ad esempio con la resina epossidica o la resina siliconica. Inoltre, c’è un intero mondo di prodotti chimici a polimerizzazione termica a cui attingere, inclusi anche i poliuretani, la chimica epossidica, i termoindurenti ad alta temperatura e tutti quegli elementi che non sono reattivi ai raggi UV. Abbiamo iniziato a combinare la chimica a polimerizzazione termica con la chimica a polimerizzazione UV, poi abbiamo avviato la produzione di resine con una parte A e una parte B che vengono miscelate appena prima di entrare nella stampante. La stampante attiva i raggi UV permettendo di definire la forma della parte che si sta costruendo e, quindi, intrappola la fase di chimica termica all’interno della parte, in uno stato senza reazione. Il tutto termina con una parte allo stato verde, che viene poi lavata o centrifugata per rimuovere la resina residua prima di passare alla fase di cottura. In questa fase di cottura, attiviamo un processo di chimica termica separata che è stato intrappolato nella rete UV. In questo modo, si ottiene la reazione di entrambi i componenti, che danno poi vita alla parte finale. Questa tecnologia ha ampliato la gamma di materiali disponibili, consentendo una produzione additiva più conveniente in un ambiente manifatturiero e con materiali ad alte prestazioni. Per essere chiari, si tratta di un procedimento molto diverso dall’inondazione UV, che è una fase di finitura comune per la chimica a polimerizzazione UV di una singola parte. In quel caso, ci si limita a polimerizzare ulteriormente la reazione UV iniziale.
3DN: Quanto è importante la sostenibilità per Carbon? Qual è il vostro impegno in questo senso?
La sostenibilità è un argomento davvero importante per noi di Carbon, abbiamo identificato diverse aree chiave in cui possiamo fare progressi. La prima riguarda il problema generale della produzione di rifiuti tossici. Ciò è particolarmente rilevante nel settore della tecnologia di stampa a resina liquida.
L’approccio standard riguarda la stampa della parte gocciolante di resina e la sua immersione in una specie di serbatoio con un solvente come l’alcol isopropilico per lavare via i residui. Si ottiene così una stampa pulita, ma anche un solvente con resina disciolta, e tutto questo deve essere trattato come rifiuto tossico. Questo potrebbe andare bene per piccoli volumi, se si ha intenzione di creare solo prototipi, ma quando entri in produzione hai un grosso problema da risolvere. E non si tratta solo di un problema di sostenibilità, ma anche economico, perché si spreca resina, oltre a generare rifiuti, e tutto questo ovviamente costa caro.
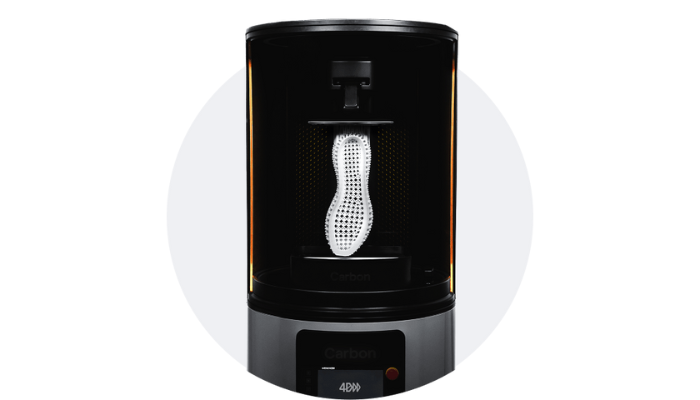
La post-elaborazione di Carbon ha contribuito a ridurre i rifiuti tossici nella creazione di intersuole per Adidas.
In azienda, abbiamo sviluppato una tecnologia di pulizia a rotazione completamente priva di solventi. Ciò si traduce in parti molto più pulite, con uno strato molto sottile di residuo, che viene trattato in post-polimerizzazione. Questo tipo di tecnica viene utilizzata nella produzione ad alti volumi, come i modelli di termoformatura per l’odontoiatria, le intersuole adidas e altre geometrie reticolari. Infatti, per le nostre applicazioni a volumi elevati, prevediamo che nel 2022 questa tecnologia di pulizia a rotazione avrà evitato la generazione di migliaia di tonnellate di rifiuti dannosi. Quando le iniziative economiche e di sostenibilità perseguono gli stessi obiettivi è facile fare progressi, perché si tratta di un’unica soluzione che risolve entrambi i problemi.
Inoltre, per alcune delle nostre resine utilizziamo materie prime di origine biologica o vegetale. Ci sono essenzialmente due fonti principali che coinvolgono le materie prime adatte a produrre tutte le sostanze chimiche nel mondo. Una è il petrolio, tutte le materie plastiche più comuni sono sottoprodotti della raffinazione del petrolio che vengono poi convertiti nei blocchi di costruzione per i polimeri. Tuttavia, lo stesso tipo di blocco può essere costruito anche sfruttando le proprietà della natura, la nostra seconda fonte. Oggigiorno c’è una grande tendenza, nell’industria chimica, a trovare risorse più sostenibili e rinnovabili a base vegetale e finalizzate alla creazione di blocchi per i sistemi polimerici. Una delle nostre aree di interesse è costituita dai poliuretani e i nostri partner hanno creato polimeri che fanno parte della catena complessiva del poliuretano ottenuta dal mais.
In quest’ambito, abbiamo creato una nuova resina chiamata EPU44. Il materiale è costituito per il 40% in peso da materia prima derivata da piante (con conseguente riduzione dell’impronta di CO2). È ad alte prestazioni e ha una viscosità inferiore, dunque è migliore per la stampa. Infatti viene già utilizzata in volumi elevati per produrre le intersuole di adidas. Abbiamo anche un materiale rigido chiamato RPU130 che è ottenuto per il 25% in peso da materiale vegetale ed è ad altissime prestazioni, con elevata stabilità termica e resistenza agli urti. Questi prodotti dimostrano che è possibile avere materiali sostenibili senza sacrificare le prestazioni. Infatti, in questi casi abbiamo anche notato un vantaggio in termini di performance, quando si utilizzano materie prime più sostenibili.
Inoltre, come molte aziende di produzione additiva, abbiamo identificato la leggerezza e la riduzione dei materiali come punti cruciali per la sostenibilità. Per aiutarci a raggiungere questo obiettivo, abbiamo sviluppato un nuovo prodotto software autonomo, chiamato Design Engine. Per usarlo, si può inserire un modello CAD solido, regolare le impostazioni per le proprietà che si desiderano e generare così un modello reticolare in linea con tali requisiti, consentendo l’utilizzo di meno materiale e la costruzione di parti più leggere. Queste caratteristiche contano molto per tantissimi settori, come quello dei trasporti. Se guardiamo all’automotive o all’aerospaziale, ogni grammo eliminato conta in termini di efficienza del carburante, per cui, se riusciamo a realizzare parti robuste ma leggere, si tratta di una vittoria per tutti. È entusiasmante che gli aspetti riguardanti i materiali, il software e l’hardware della nostra attività possano contribuire a rendere più sostenibili i prodotti realizzati con la tecnologia Carbon.
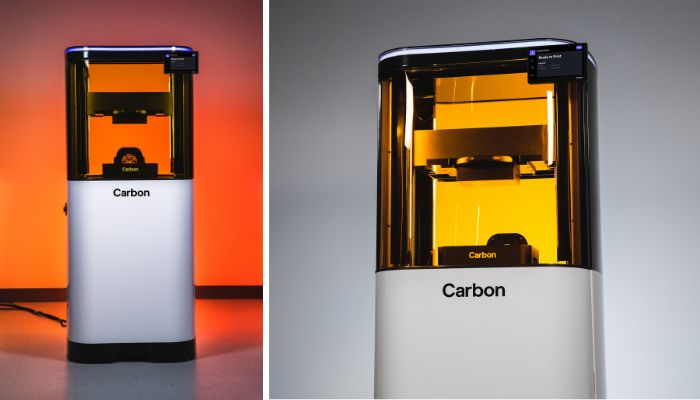
I nuovi materiali più sostenibili di Carbon possono essere utilizzati nelle loro macchine
Il problema finale da risolvere è il riciclaggio: si tratta di una questione impegnativa perché, a livello globale, il flusso di lavoro legato al riciclaggio è molto inefficiente e solo una piccola quantità viene effettivamente riciclata. Sono due le principali tecnologie destinate al riciclaggio. La prima riguarda il metodo di riciclaggio meccanico più tradizionale. In questo processo, una parte scartata viene pulita, tritata e miscelata con materia prima vergine, tipicamente a una concentrazione intorno al 5-10%, e lavorata allo stato fuso per formare una nuova parte. Si tratta di una tecnica che serve allo scopo, ma è molto inefficiente. Inoltre pone diversi problemi, in quanto ogni volta che si riscalda il polimero, le catene si accorciano e perdono alcune proprietà meccaniche, quindi c’è solo un certo numero di cicli che possiamo eseguire prima che il materiale riciclato non performi più. Tuttavia ci stiamo impegnando seriamente a migliorare in quest’ambito. Ad esempio, le intersuole adidas possono essere tagliate a pezzi e quindi venire inserite in un estrusore per essere trasformate in una nuova forma. Circa l’80% delle proprietà meccaniche viene mantenuto attraverso questo processo.
E poi c’è anche il riciclaggio chimico. Si tratta di un processo interessante, perché invece di sminuzzare un materiale e di rifonderlo, questo passaggio può essere eseguito attraverso un processo chimico in cui la catena polimerica viene decompressa e i monomeri utilizzati per costruirlo vengono rigenerati. Ciò consente quindi la generazione di un polimero riciclato con tutte le sue proprietà. In fase di ricerca e sviluppo, abbiamo creato resine in cui possiamo recuperare il 50% del materiale di partenza eseguendo un processo di riciclaggio chimico. Il materiale ricavato può quindi essere utilizzato in un lotto successivo di resina e si ottiene così un sistema a ciclo chiuso. Attualmente stiamo cercando partner per questo progetto e sicuramente ci saranno altri aggiornamenti nei prossimi anni.
Infine, stiamo anche cercando di ridurre i rifiuti derivanti dall’imballaggio, esattamente come facciamo con la produzione ad alto volume; le dimensioni del contenitore in realtà contano molto in termini di quantità di rifiuti generati.
3DN: E la produzione additiva? In che modo diventa sostenibile?
La produzione additiva rende possibile la manifattura locale, i produttori possono realizzare ciò di cui hanno bisogno, dove e quando serve, e questa possibilità aiuta a ridurre i costi di trasporto e la conseguente impronta di CO2. Durante il covid, abbiamo appreso che le catene di approvvigionamento sono ottimizzate in base ai costi, non in base all’efficienza e alla velocità di produzione delle parti, e questo può condurre a scarsità di prodotto e ad altri problemi.
Inoltre, con la produzione tradizionale, è necessario un magazzino pieno di parti stampate a iniezione che devono essere controllate in base a temperatura e umidità. E tutto questo avviene con un ampio dispendio di energia. Infine, spesso gli ordini avvengono per eccesso perché si cerca di prevedere ciò di cui si ha bisogno e le quantità in più vanno sprecate. In alternativa, si potrebbe avere un magazzino pieno di stampanti 3D e produrre parti su richiesta, invece di cercare di prevedere complicate catene di approvvigionamento. Inoltre, come abbiamo detto poco fa, la produzione additiva consente di utilizzare meno materiale e quindi di rendere il pezzo più leggero.
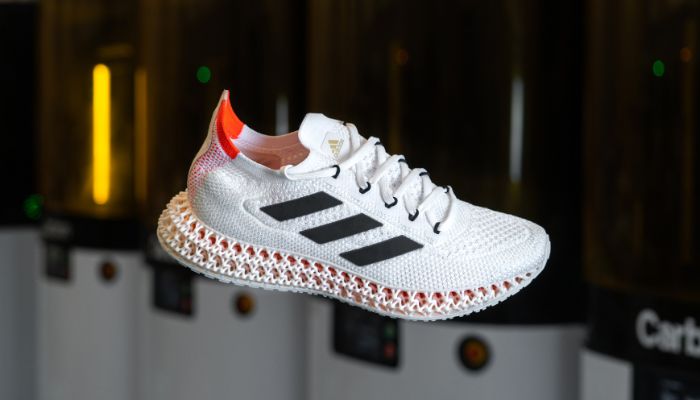
I metodi più sostenibili di Carbon hanno avuto un ruolo nello sviluppo dei prodotti adidas
3DN: Un ultimo commento per i nostri lettori?
Penso che la produzione additiva sia più importante che mai in questo periodo storico. Soprattutto quando parliamo delle sfide legate alla catena di approvvigionamento, che tutti devono affrontare. In particolare, uno degli aspetti che stiamo spingendo è come trovare modi per realizzare prodotti più velocemente. L’approccio di Carbon consiste nel lavorare con designer e maker dallo stadio iniziale dell’idea fino alla produzione, per disporre di un insieme comune di processi e materiali da utilizzare durante tutto il ciclo di sviluppo. Puoi trovare altre informazioni su di noi e sui nostri progetti QUI.
Che cosa pensi dell’approccio di Carbon allo sviluppo dei materiali e alla sostenibilità? Condividi la tua opinione nei commenti qui sotto o con la comunità di 3Dnatives sui nostri social Facebook, Twitter e Linkedin . Trovi tutti i nostri video sul nostro canale YouTube!
*Tutti crediti foto: Carbon