Formnext 2024 mette in luce le applicazioni e il potenziale della stampa 3D nel settore aerospaziale
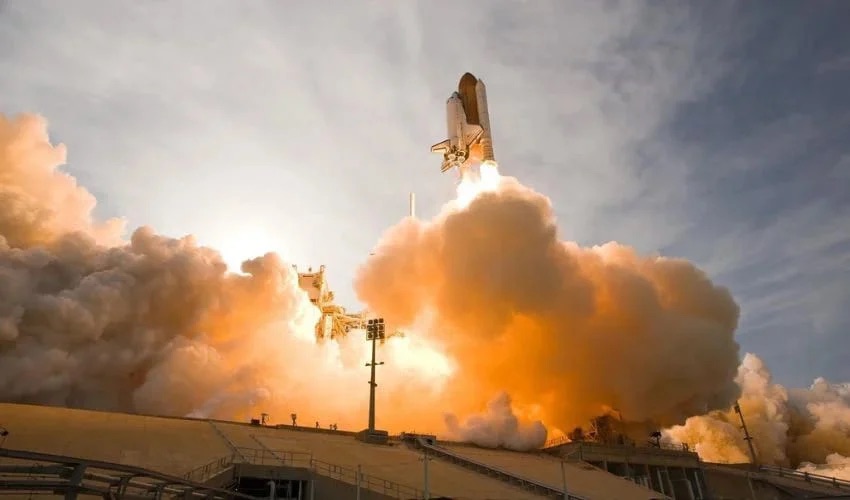
Formnext 2024 ha offerto ancora una volta una panoramica delle tendenze del settore della produzione additiva e delle ultime innovazioni. L’anno scorso abbiamo visto numerose applicazioni nel settore automobilistico e iniziative per migliorare la sostenibilità. Quest’anno si è assistito a un’impennata delle tecnologie di stampa 3D in metallo e delle innovazioni legate alle applicazioni spaziali. Questo sviluppo si è riflesso direttamente negli stand degli espositori, dove sono stati presentati numerosi casi d’uso concreti e stampanti 3D dedicate. È stato anche ampiamente trattato nel programma della fiera, con diverse conferenze e presentazioni dedicate alla lavorazione dei metalli e alla produzione additiva per il settore spaziale. Abbiamo già esplorato le applicazioni in metallo evidenziate a Formnext, ora è il momento di esaminare il ruolo crescente della stampa 3D nel settore aerospaziale e di presentare alcune delle lezioni apprese dalla fiera.
Nel settore spaziale, la stampa 3D svolge un ruolo fondamentale nella produzione di componenti per i veicoli spaziali. In particolare, viene utilizzata per progettare parti essenziali come gli elementi di propulsione dei razzi, le camere di combustione, le teste degli iniettori e i sistemi di pompaggio. Un altro importante campo di applicazione è la produzione di strutture direttamente nello spazio. Queste sono talvolta realizzate con materiali disponibili in loco, come la regolite marziana o lunare.
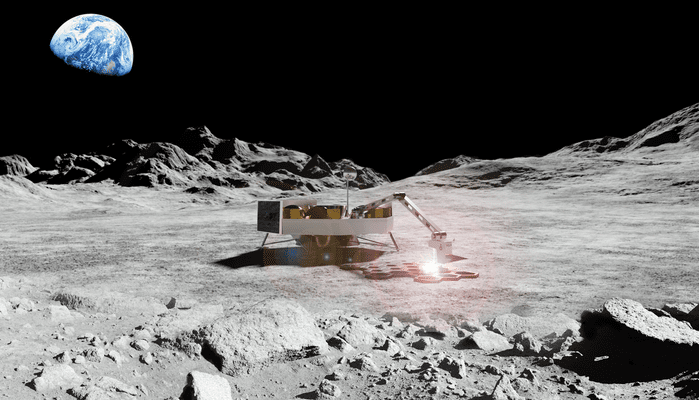
Crediti fotografici: ICON
La stampa 3D consente di creare progetti complessi e interconnessi. Nel caso dei motori a razzo, ad esempio, consente di integrare i condotti di raffreddamento in un’unica fase di produzione. Numerose applicazioni dimostrano che le parti prodotte con la stampa 3D possono migliorare le prestazioni, grazie soprattutto all’uso di materiali su misura con proprietà specifiche che soddisfano i requisiti esatti dell’industria. Questi vantaggi non si limitano ai componenti dei veicoli spaziali, ma si estendono anche alle strutture prodotte direttamente nello spazio.
Processi di stampa 3D per lo spazio e sfide esistenti
LPBF rimane attualmente il processo di stampa più utilizzato, anche se la tecnologia DED sta guadagnando popolarità grazie alla sua capacità di riparare parti esistenti. The Exploration Company, ad esempio, si sta concentrando sulla LPBF, con l’intenzione di adottare la DED entro il 2025. Da parte sua, l’azienda tedesca Ponticon produce sistemi DED industriali ad alta velocità. Il suo processo è stato utilizzato per rivestire il motore dell’Ariane 6.
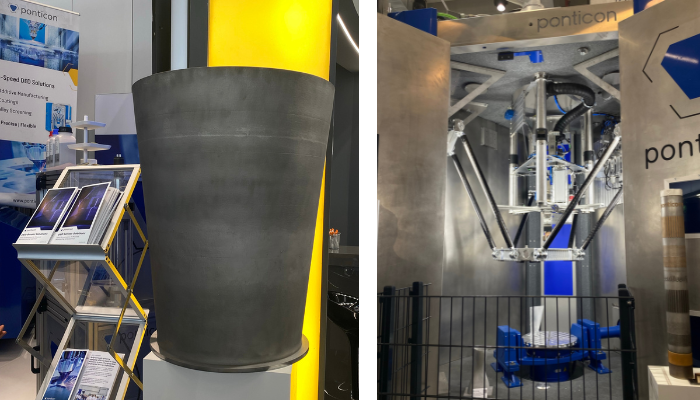
Esempio di una parte aerospaziale stampata in 3D nello stand Ponticon (foto: 3Dnatives)
Inoltre, con il processo DED, gli utenti non devono più rimuovere la polvere dal pezzo, operazione particolarmente complessa quando sono incorporati canali interni. Se la polvere rimane intrappolata all’interno, impedisce la circolazione dei liquidi, che potrebbe portare alla fusione o addirittura all’esplosione del motore. Inoltre, la complessità dei pezzi rimane una sfida importante. “Stampare 100 canali di raffreddamento in un pezzo con uno spessore di parete di soli 4 mm è una vera sfida”, spiega Maximilian Strixner di The Exploration Company, l’azienda dietro Nyx, una capsula spaziale modulare e riutilizzabile.
Un’altra sfida importante è rappresentata dai costi. Ciò è dovuto principalmente all’elevato costo dei materiali, che devono avere caratteristiche specifiche. Nella sua presentazione, Tobias Stiggen di Ponticon GmbH ha sottolineato che quasi due terzi del costo totale della carenatura per il motore dell’Ariane 6 erano attribuibili ai materiali. Al contrario, il costo del sistema di stampa Ponticon utilizzato in questo esempio è stato relativamente contenuto.
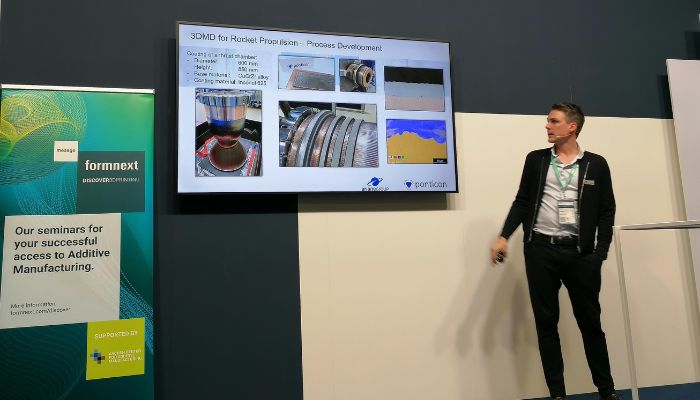
Tobias Stiggen spiega i vantaggi della tecnologia DED per la propulsione dei razzi (foto: 3Dnatives)
Un’altra spiegazione dei costi elevati risiede nell’enfasi posta sulla produzione di parti leggere e ad alte prestazioni. Alla conferenza “Qualificazione dei materiali per la produzione di massa di parti aerospaziali e automobilistiche stampate in 3D”, Bill Bihlman di SAE International ha sottolineato che le parti aerospaziali costano circa dieci volte di più di quelle utilizzate nell’industria automobilistica.
Materiali ad alte prestazioni per le applicazioni spaziali
Sebbene il costo sia un fattore determinante, le prestazioni e la resistenza dei materiali rimangono priorità assolute. Per questo motivo, nel settore spaziale viene utilizzata un’ampia gamma di metalli e leghe, oltre a nuovi materiali e compositi. Ad esempio, The Exploration Company predilige le leghe di rame per la loro conducibilità termica e le leghe a base di nichel per la loro resistenza meccanica e chimica. SAE, dal canto suo, utilizza leghe, alluminio e titanio per la produzione di pezzi in piccole serie.
Per la produzione nello spazio, si utilizzano principalmente materiali convenzionali o compositi. Ad esempio, il Concordia Aerospace Robotics Lab raccomanda un composito a base di PEEK e regolite. Questo materiale soddisfa i requisiti della NASA in materia di emissioni di gas di scarico e offre una buona resistenza alle radiazioni e alle sostanze chimiche. Inoltre, l’incorporazione del regolite nel PEEK ha permesso di ridurre i costi, come dimostrano i risultati. Incorporando il 50% di regolite nel PEEK, i costi si sono dimezzati.
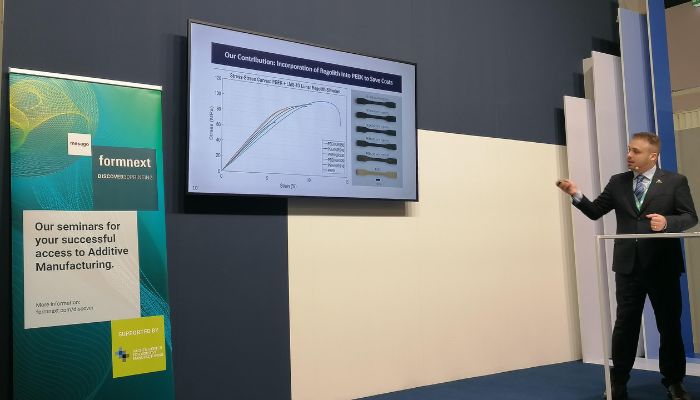
Mohammad Azami del Concordia Aerospace Robotics Lab
Anche il silicone comincia a fare la sua comparsa anche nel settore aerospaziale. Alla fiera di quest’anno è stata dedicata una presentazione dal titolo “Trasformare l’aerospazio attraverso la stampa 3D di silicone e compositi flessibili”. Julien Barthes di 3Deus Dynamics ha presentato il suo processo di stampa 3D con polvere di silicone e ha spiegato come l’azienda sviluppa nuovi materiali compositi flessibili durante il processo di stampa.
Uno dei principali vantaggi di questo metodo è che il silicone tradizionalmente stampato a iniezione può essere utilizzato anche per la stampa 3D, senza generare rifiuti, poiché la polvere riciclata può essere riutilizzata. Julien Barthes ha inoltre sottolineato che è possibile modificare il materiale durante la stampa, rendendo possibile la produzione di un pezzo con due texture distinte e proprietà meccaniche specifiche, incorporando al contempo geometrie complesse. “È possibile aggiungere polvere durante il processo di stampa, manipolare il materiale e creare compositi direttamente durante la produzione”, conclude.
Guardare al futuro
Quest’anno a Formnext sono state presentate anche alcune innovazioni entusiasmanti, come Ariane 6: il più grande motore a razzo al mondo stampato in metallo, opera di Eplus3D e LEAP 71. Ma non solo. Come già detto, rimangono anche alcune sfide da affrontare.
La produzione additiva nel settore spaziale offre un enorme potenziale che rimane in gran parte inutilizzato. Produzione di parti leggere, geometrie complesse e uso di nuovi materiali ad alte prestazioni che rendono i razzi più veloci, più efficienti e più durevoli: è certo che nel prossimo futuro sentiremo parlare sempre più spesso di stampa 3D nello spazio!
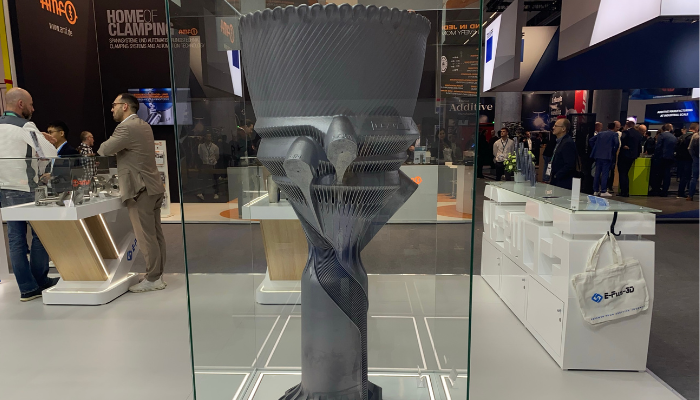
A Formnext 2024, Eplus3D e LEAP 71 hanno presentato il motore a razzo stampato in metallo più grande del mondo. (Crediti fotografici: LEAP 71)
Cosa ne pensi della stampa 3D per applicazioni aerospaziali? Faccelo sapere lasciando un commento qui sotto o sui nostri canali social Facebook, Linkedin e YouTube! Non dimenticare di iscriverti alla nostra Newsletter settimanale per ricevere tutte le notizie sulla stampa 3D direttamente nella casella di posta!