La Universidad Johns Hopkins aplica el aprendizaje automático para la tecnología L-PBF
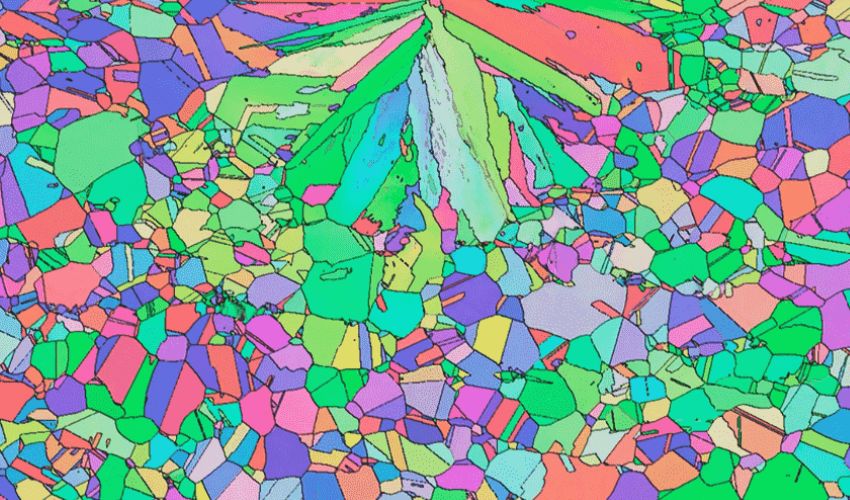
Investigadores del Laboratorio de Física Aplicada (APL) de la Universidad Johns Hopkins han desarrollado un nuevo enfoque que integra la impresión 3D con el aprendizaje automático, concretamente para la fusión láser por lecho de polvo (L-PBF). En esencia, el modelo les permite crear simulaciones útiles para verificar la producción de materiales creados mediante LPBF. El aprendizaje automático, o machine learning, forma parte de una rama de la inteligencia artificial y puede aplicarse en diversos campos, desde el médico hasta el aeroespacial.
La técnica ideada por los investigadores permite predecir qué microestructura se formará en la superficie de impresión gracias a las mediciones realizadas en una única capa de polvo. Para ello, los investigadores recurrieron a la modelización y simulación computacionales. Estas predicciones del objeto que se creará permiten intervenir a tiempo en caso de errores. De este modo, no solo se ahorra tiempo, materiales y costes, sino que también podría aumentar el rendimiento de los materiales fabricados mediante la tecnología L-PBF.
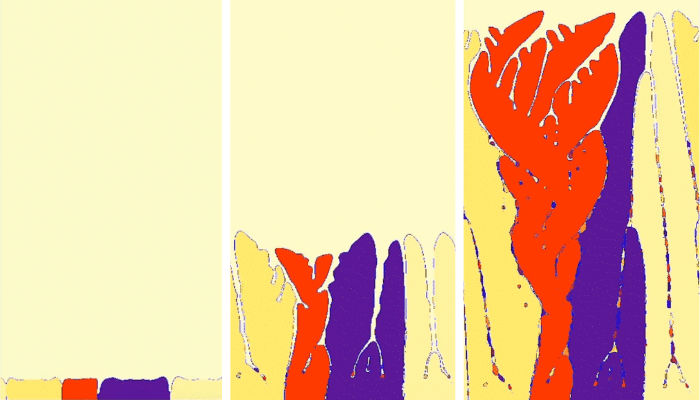
Esta imagen muestra el proceso de predicción de la microestructura, que se consigue analizando el impacto de la velocidad de enfriamiento y el gradiente de temperatura en la orientación y el tamaño del grano.
Este estudio forma parte de un trabajo más amplio que se está llevando a cabo en el Laboratorio de Física Aplicada de la Universidad Johns Hopkins centrado en el uso de la inteligencia artificial para acelerar el descubrimiento de nuevos materiales para entornos extremos. Morgan Trexler, el coordinador del programa de Ciencia de Materiales Extremos y Multifuncionales del APL en el Área de Misión de Investigación Exploratoria y Desarrollo, comentó: «Anticipamos que este nuevo enfoque será extremadamente impactante para ayudar a diseñar y comprender la formación de materiales durante los procesos de fabricación aditiva, y esto encaja en nuestra estrategia global centrada en acelerar el desarrollo de materiales para la seguridad nacional».
¿Por qué utilizar el aprendizaje automático para la tecnología L-PBF?
En la fusión láser por lecho de polvo las capas de polvo metálico se funden mediante un láser de alta potencia para crear objetos tridimensionales capa a capa. Esta tecnología es útil para producir piezas metálicas resistentes y de geometrías complejas. Sin embargo, como los polvos son diferentes entre sí y, por tanto, tienen sus propias características, las condiciones de procesamiento pueden sufrir muchas variaciones, empezando por los ajustes del láser, así como por las interacciones entre las distintas partículas de polvo. Como resultado, las propiedades de los objetos que se imprimen pueden variar enormemente.
Para llevar a cabo esta aplicación, el equipo de investigadores dirigido por Li Ma, ingeniera jefe del APL, utilizó un modelo de dinámica de fluidos computacional (CFD) para medir con precisión los cambios de temperatura y las velocidades de enfriamiento durante el proceso de impresión en relación con la orientación y el tamaño del grano. La dinámica de fluidos computacional (CFD) es una disciplina que emplea simulaciones por ordenador para predecir el comportamiento de los flujos de materiales, basándose en las leyes de conservación de la masa, el momento y la energía. Este enfoque innovador permite no solo predecir la microestructura de la pieza antes de imprimirla, sino también estimar las propiedades mecánicas del material y el rendimiento físico de la pieza acabada.
Ali Ramazani desarrolló el primer modelo de formación microestructural de campo de fases integrando los resultados obtenidos del modelo CFD. Este enfoque mejoró la precisión y la validez de las simulaciones. Sin embargo, su contribución, aunque significativa, no fue suficiente para resolver todos los problemas de recopilación de datos. En efecto, la producción de un solo componente mediante la tecnología L-PBF implica millones de interacciones entre el polvo y el láser, lo que requiere una enorme cantidad de tiempo de cálculo y, por tanto, hace que la simulación de cada pequeña sección sea extremadamente compleja.
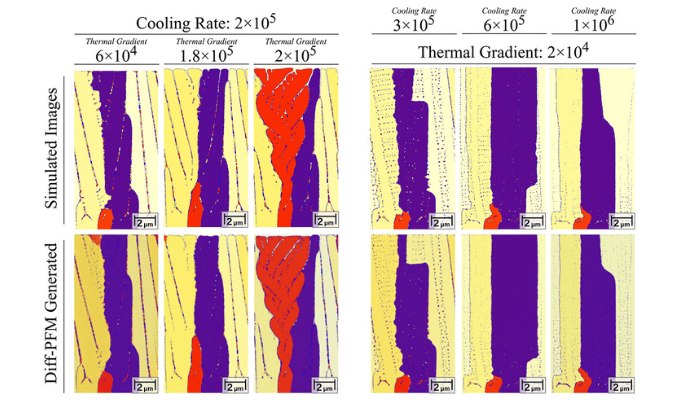
En esta imagen, los resultados del modelo de campo de difusión probabilístico del APL se compararon con los resultados de la simulación. El modelo del APL detecta con precisión la formación de microestructuras y el crecimiento de grano observados en los resultados simulados.
El avance fue obra de Hudson Liu, un estudiante de bachillerato en la Gilman School de Baltimore y alumno en prácticas en el marco del programa del APL llamado: Student Program to Inspire, Relate, and Enrich (ASPIRE). Liu teorizó un modelo de aprendizaje automático que reduciría en gran medida la necesidad de realizar costosas simulaciones. Liu integró varios modelos de aprendizaje automático preexistentes para desarrollar lo que el equipo llama un «modelo de campo probabilístico de difusión». Este modelo genera imágenes basadas en la velocidad de enfriamiento y el gradiente térmico de la impresión L-PBF, cuantificando los cambios de temperatura en función de parámetros como la distancia entre el punto de impacto del láser y el metal sólido circundante.
Según Hudson Liu, «la principal ventaja de utilizar un modelo es su rapidez. Nuestro modelo puede aproximar en segundos o minutos lo que llevaría horas en una simulación», y añadió: “Esto permite a los investigadores explorar rápidamente una amplia gama de parámetros y a un coste mucho menor”. El modelo se validó mediante análisis microscópicos del material L-PBF. El entrenamiento del programa de aprendizaje automático requirió más de 400 simulaciones realizadas en el APL.
Perspectivas de futuro
El equipo de investigación ya está trabajando para entrenar nuevos modelos utilizando datos de vídeo, lo que permitirá predecir microestructuras tanto en 3D como en 2D. Con el tiempo, será posible hacer predicciones de las microestructuras de componentes más grandes y analizar los resultados de más pasadas de láser.
Pero eso no es todo. El proyecto, que surgió gracias a la financiación interna de la universidad, ha sido objeto de interés por parte del Instituto de Investigación de Tecnología Espacial (STRI) de la NASA, que desearía aplicarlo para sus propios servicios. Según Li Ma, «la NASA quiere modelos validados que le ayuden a predecir lo que ocurrirá en una construcción y cómo funcionará la pieza posterior, sin necesidad de costosos experimentos. Así que este enfoque es valioso, sobre todo si pensamos en la fabricación aditiva en la Luna o en el espacio, donde la experimentación resulta tan cara que es prácticamente imposible». Por lo tanto, no nos sorprenderá que en un futuro próximo oigamos hablar de las aplicaciones que se desarrollan en este laboratorio no solo en los viajes espaciales de la NASA, sino también en otros ámbitos.
¿Qué opinas del uso del aprendizaje automático para la tecnología L-PBF? Deja tus comentarios en nuestras redes sociales: Facebook, LinkedIn y Youtube. Sigue toda la información sobre impresión 3D en nuestra Newsletter semanal.
*Foto de portada: la imagen muestra la microestructura de la superaleación a base de níquel reforzada por precipitación utilizada para validar el modelo del APL y su predicción de la velocidad de enfriamiento (créditos: ASM International 2024)