Unilever y Serioplast utilizan la impresión 3D para fabricar botellas de plástico
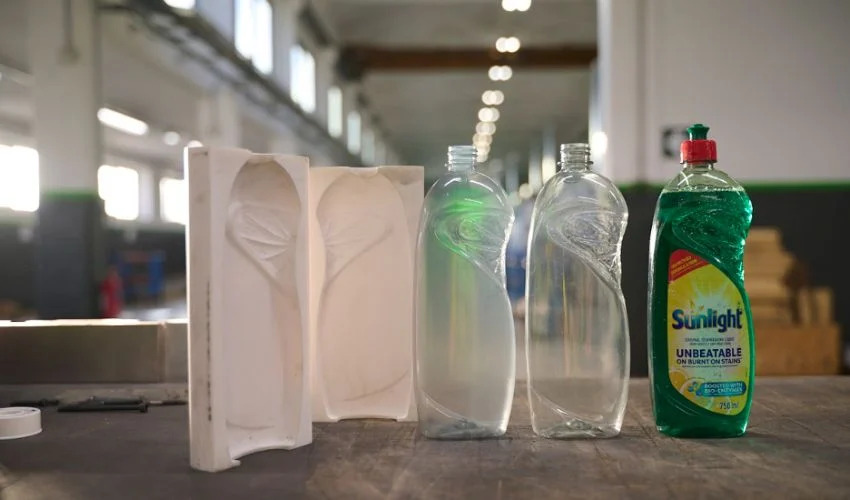
Un sector del que se habla poco y en el que en los últimos años hemos observado un crecimiento en el uso de la impresión 3D, es el de los envases. Con un mercado valorado en 1,210 millones de dólares en 2023, según Future Market Insights, en los últimos años grandes marcas, como L’Oréal o Pepsi, han optado por procesos de fabricación aditiva. Incluso la multinacional Unilever, que ha utilizado la impresión 3D de resina de Formlabs para fabricar moldes para sus botellas de plástico.
Si el nombre de Unilever no te resulta familiar, basta con decir que es una de las mayores empresas de bienes de consumo del mundo: hacen productos de uso cotidiano, que van desde el cuidado personal hasta los productos de limpieza, alimentos y mucho más. Por citar solo algunas de las marcas de Unilever, pensemos en Svelto, Magnum, Dove, Knorr, etc., con productos disponibles en más de 190 países. Sin embargo, el sector de los bienes de consumo de alta rotación se caracteriza por una competencia feroz, por lo que Unilever busca constantemente formas de innovar, entre ellas la iniciativa de utilizar la impresión 3D para las botellas de plástico.
Para ello, la empresa colaboró con Serioplast Global Services, una de las principales empresas asociadas de Unilever. Serioplast, fundada en 1974 en Seriate, Italia, y que ahora opera en todo el mundo, es una empresa que produce envases de plástico rígido para los actores más importantes del mercado de bienes de consumo.
Stefano Cademartiri, CAD & Prototyping Owner de Unilever, explica: «Una empresa de bienes de consumo como Unilever necesita estar en el mercado lo antes posible o antes que sus competidores. Tenemos que ofrecer a los consumidores el mejor producto al mejor precio en el menor tiempo posible. La impresión 3D nos ayuda a acelerar este proceso».
¿Cómo utiliza Unilever la impresión 3D para fabricar botellas?
Tradicionalmente, la producción de una simple botella de plástico lleva mucho más tiempo del que uno podría imaginar. Diseñar el producto, hacer los moldes y fabricarlo mediante una combinación de moldeo por inyección, estirado y soplado, suele llevar meses. Los moldes se fabrican tradicionalmente en metal mediante mecanizado CNC, lo que requiere equipos especializados, software CAM y mano de obra cualificada. La producción de herramientas piloto metálicas suele subcontratarse y conlleva plazos de cuatro a ocho semanas y costes que oscilan entre 2000 y más de 20 000 euros, según la complejidad de la pieza.
Al integrar la impresión 3D en el proceso, el tiempo se reduce drásticamente, ya que un molde impreso en 3D puede completarse en tan solo dos días, así, las pruebas piloto se reducen a tan solo dos semanas, todo ello con unos costes significativamente más bajos. Flavio Migliarelli, director de diseño de I+D de Serioplast Global Services, explica: «Con el molde impreso en 3D, podemos ahorrar hasta un 70% de tiempo y un 90% en costes en comparación con el molde estándar. Antes, [los clientes] tenían que esperar hasta 12 semanas para un solo proyecto, ahora podemos hacer cinco».
En este caso, se combinan los métodos tradicionales con la impresión 3D. Concretamente, los moldes se fabrican con la impresora 3D Form 3L de Formlabs y resina Rigid 10K, que permite obtener moldes precisos con un acabado superficial liso. El uso de la tecnología SLA también ha ayudado a Unilever y Serioplast a integrar más detalles en las botellas, con logotipos y otros detalles finos.
Una vez creado el molde, las botellas se fabrican mediante moldeo por soplado, en este caso moldeo por estirado-soplado (SBM), que se utiliza habitualmente para crear envases de PET transparentes de alta calidad. Las aplicaciones de la combinación de estas tecnologías incluyen la comprobación temprana de aspectos de la línea de producción gracias a la similitud de las botellas con el producto final, la validación del proceso SBM y la preforma PET y la aceleración de la creación de prototipos.
Con un único molde fabricado en 3D con resina Rigid 10K, se produjeron unas 200 unidades sin comprometer el molde. La calidad global de las botellas obtenidas es comparable estética y funcionalmente a la de una producción estándar, hasta el punto de que pueden someterse a pruebas de consumo. «La experiencia del equipo combinada con la tecnología de impresión 3D de Formlabs nos permitió desarrollar una solución de producción industrial personalizada para satisfacer las necesidades del cliente», concluyó Mirco Paltrinieri, Brand Manager de Formlabs en SolidManufacturing.
¿Qué opinas del uso que Unilever y Serioplast hacen de la impresión 3D para producir botellas de plástico? Deja tus comentarios en nuestras redes sociales: Facebook, Twitter y Youtube. Sigue toda la información sobre impresión 3D en nuestra Newsletter semanal.
*Créditos de todas las fotos: Formlabs