La UMA analiza y estudia el comportamiento del acero en la impresión 3D
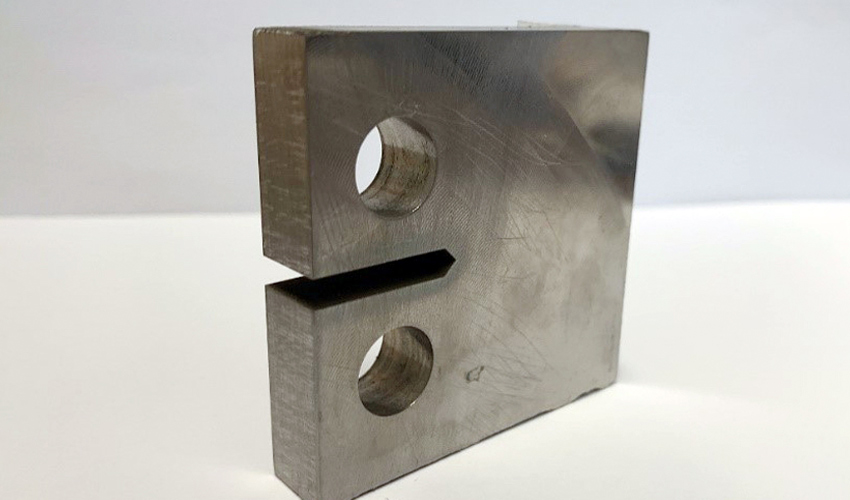
Un equipo de investigadores en la Universidad de Málaga (UMA) han llevado a cabo un estudio exhaustivo sobre los materiales utilizados en la fabricación aditiva. En concreto, el grupo de la UMA ha observado el comportamiento del acero, así como sus defectos internos a la hora de usarlo en la impresión 3D. Uno de los puntos focales del estudio se centra en el análisis los poros formados tras la fabricación, así como en la definición de otros parámetros, como son la esfericidad, la relación de aspecto, la superficie, el volumen, etc. El proyecto ha sido publicado en la revista Materials, donde se recogen los resultados obtenidos a partir de dicha investigación. Gracias a esto, se ha conseguido entender mejor el comportamiento y la resistencia de varios metales desarrollados a partir de este método de fabricación.
Por lo general, los materiales utilizados en la fabricación aditiva son o bien duros y resistentes, o bien maleables y dúctiles. Sin embargo, el acero es un metal que tiene muy buena dureza y resistencia, además de ser maleable. Por esta razón, a menudo se encuentra conformado de aleaciones, ideales en muchas aplicaciones en las que los requerimientos son extremos, como la aeronáutica y la automoción. Aun así, el equipo de la UMA ha querido ir un paso más y estudiar el comportamiento del acero cuando se combina con las nuevas tecnologías, como es la impresión 3D.
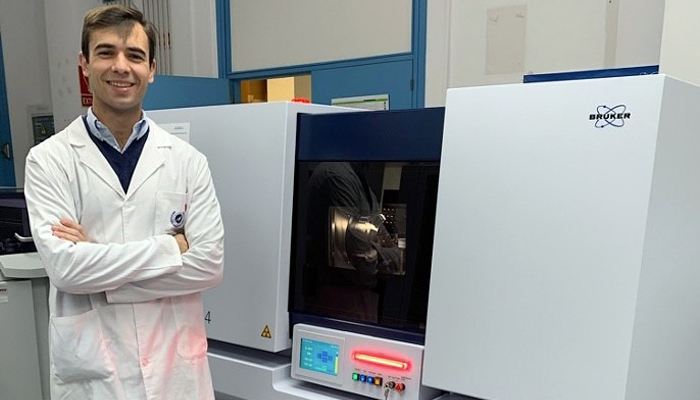
Pablo Moreno Cerezo, uno de los autores de la investigación, junto al equipo de tomografía axial computarizada (TAC).
El acero y la impresión 3D en el punto de mira de la UMA
En la creciente industria de fabricación aditiva, determinar con exactitud cómo afecta la tecnología a las propiedades de las piezas, es un aspecto clave. Los investigadores realizaron un estudio que relaciona la resistencia a la fractura por fatiga con la porosidad interna que presenta el metal impreso en 3D. El análisis del acero fue posible gracias a la tomografía computarizada de rayos X (XCT). Con esto, lograron visualizar y cuantificar la porosidad interna de las muestras típicamente empleadas en pruebas de resistencia mecánica. El doctor Pablo López Crespo, investigador de Departamento de Ingeniería Civil, de Materiales y Fabricación, señala: “Gracias a este método, se superan los inconvenientes de otras técnicas convencionales 2D, ya que estas proporcionan únicamente mediciones superficiales y, por tanto, información incompleta”.
Los expertos analizaros las distintas direcciones de impresión mediante espectroscopía de rayos X, microscopía electrónica de barrido y metalografía. A través de un equipo de tomografía axial computarizada (TAC) visualizaron la distribución interna en los metales. De esta forma observaron los poros que hay en el interior de la pieza para poder así medir su forma y tamaño. Los resultados mostraron que la gran mayoría de los poros se generan por gases atrapados en el proceso de fabricación. Al mismo tiempo descubrieron que esta porosidad podría reducirse si la impresión del material se realizaba en unos ángulos concretos. Así, los poros se minimizaban en caso de imprimir el acero a 0º o a 90º, pero no a 45º, ya que esta inclinación aumentaba el volumen de poros y, por ende, las probabilidades de fractura.
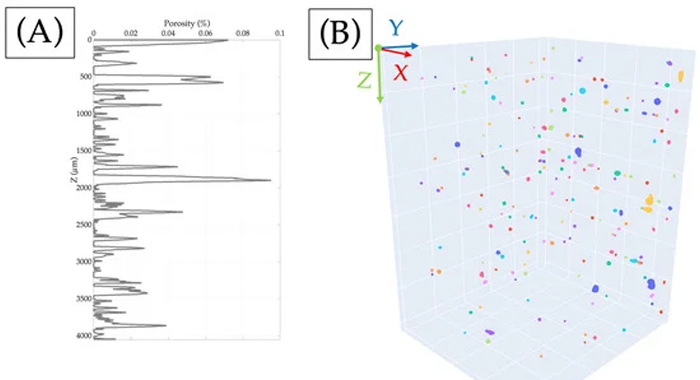
Distribución de poros en el interior de la probeta de acero.
Gracias a este análisis, se ha conseguido una imagen completa de la porosidad interna del acero y de otros metales. «Consideramos que este avance debe traducirse tanto en el ámbito académico como en el industrial en un impulso de cara a optimizar la calidad del material y ampliar sus aplicaciones de alta exigencia que se demandan en este sector», concluye López Crespo. Puedes encontrar más información sobre el estudio, aquí.
¿Qué piensas del estudio de la UMA sobre el acero en la impresión 3D? Deja tus comentarios en nuestras redes sociales: Facebook, Twitter y Youtube. Sigue toda la información sobre impresión 3D en nuestra Newsletter semanal.
*Créditos de todas las fotos: UMA