Los implantes impresos en 3D más sorprendentes de la medicina
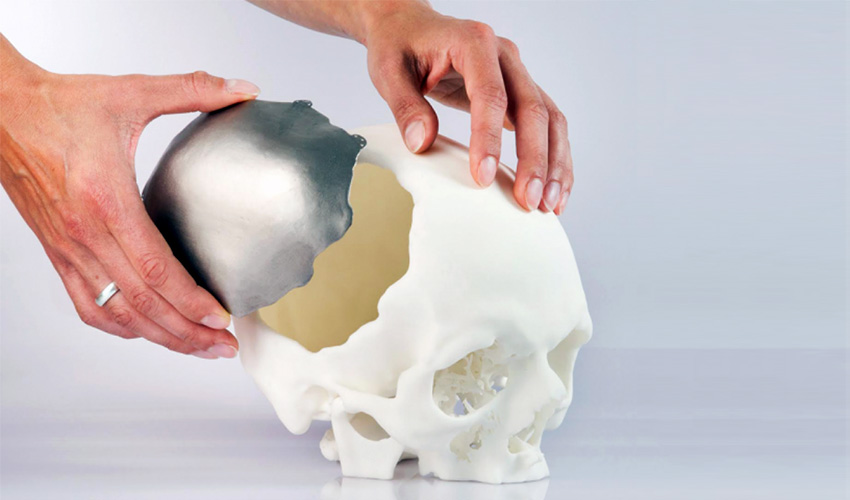
Uno de los grandes beneficiados con la llegada de las tecnologías de fabricación aditiva ha sido el sector médico. Gracias a la facilidad para desarrollar modelos únicos para cada paciente, por fin nos estamos acercando a la llamada: medicina personalizada. Cuando hablamos de implantes sabemos que es un tema muy delicado, ya que es la introducción de un elemento externo al cuerpo del paciente, reemplazando algo que no está funcionando o para el tratamiento de alguna enfermedad. Al ser algo externo debe estar hecho a medida para cumplir con los requerimientos de cada persona, por ello la fabricación aditiva ha caído como anillo al dedo en estos desarrollos. Para entender el panorama actual en el desarrollo de implantes, el equipo de 3Dnatives ha realizado una selección con algunos de los implantes más sorprendentes impresos en 3D. Estos son implantes que ya han sido aprobados o implantes que aún están en fase de investigación.
Impresión 3D de huesos para el oído
El martillo, el yunque y el estribo son tres huesos ubicados en nuestro oído, siendo los más pequeños del cuerpo humano porque no crecen después del nacimiento. Por tanto, su forma, tamaño y posición son muy importantes para el correcto funcionamiento del oído. Sin embargo, a veces estos huesos se rompen y necesitan ser reemplazados. Esto es lo que sucedió en Sudáfrica, donde a un paciente se le implantaron huesos de titanio impresos en 3D después de un accidente de coche. Tras el escaneo 3D de su oído medio, el equipo de cirujanos detrás de la operación pudo modelar un implante a medida, que luego se imprimió en una máquina de fusión láser de lecho de polvo. El titanio fue el material utilizado en este caso por su biocompatibilidad y resistencia.
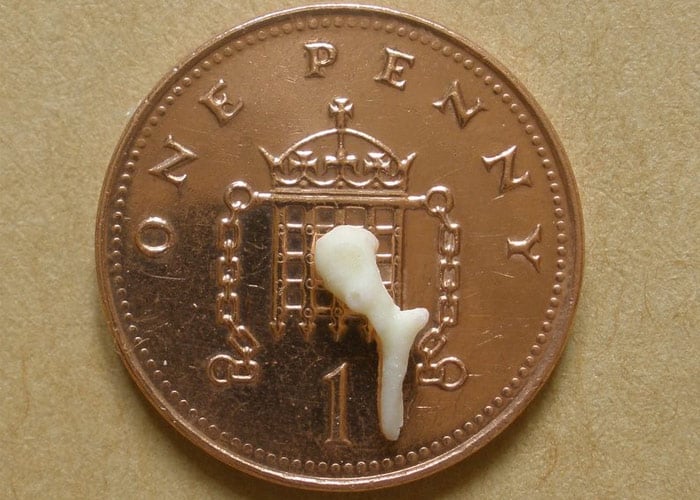
Esta imagen muestra un huesecilllo real de nuestro oído que fue fabricado nuevamente gracias a la impresión 3D.
Implante de mandíbula tras retirar un tumor
Anelia Myburgh, es una mujer australiana de Melbourne que mejoró su calidad de vida gracias a las tecnologías de fabricación aditiva. Debido a un tumor maligno ubicado en su mandíbula y dientes, los doctores se vieron forzados a extirparlo, lo cual provocó una desfiguración en el rostro de la mujer al perder más del 80% de la mandíbula. El caso de de Myburgh llevó al cirujano maxilofacial George Dimitroulis a explorar las posibilidades de la fabricación aditiva para la creación de modelos personalizados. Así, creó un implante de mandíbula con un marco de titanio capaz de incorporar injertos de hueso. Tras más de 5 horas de cirugía y varios meses de recuperación, podemos afirmar que la operación fue todo un éxito y los avances en esta tecnología devolvieron a Anelia la seguridad y confianza en su vida.
La caja torácica creada por Renishaw
Debido a un cáncer en el pecho, el galés de 71 años Peter Maggs se sometió a una operación de 8 horas para la extirpación del tumor. En el proceso quirúrgico se extrajeron tres costillas y parte de su esternón, por lo que los médicos buscaron una forma de reemplazar las partes que faltaban. Para ello, recurrieron a la fabricación aditiva de metal, concretamente a las soluciones de la empresa Renishaw, con el fin de crear un modelo de caja torácica de alta calidad y biocompatibilidad. El cirujano cardiotorácico Ira Goldsmith explicó que uno de los principales beneficios de utilizar una prótesis impresa en 3D es que puede personalizarse y adaptarse por completo al paciente. Y así lo demostró, ofreciéndole a Maggs una solución rápida y eficiente.
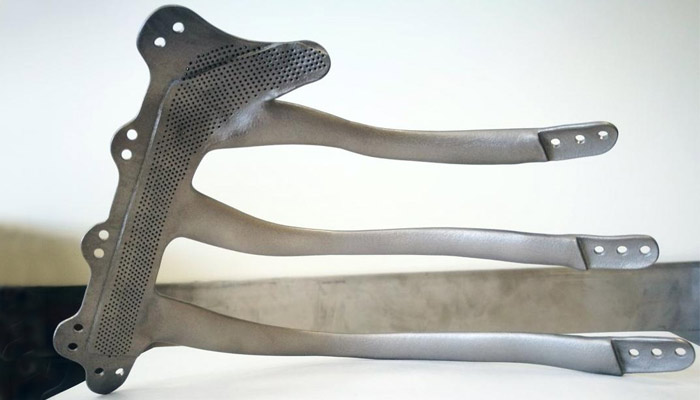
Créditos: Renishaw
Válvulas cardíacas de silicona
Recientemente hemos visto ejemplos de implantes para modelos originalmente hechos con tejido orgánico. Este es el caso de una prótesis de válvula cardíaca bioinspirada, que se hizo con silicona impresa en 3D. Creadas tras una colaboración entre un equipo de investigadores del ETH Zurich y la empresa sudafricana Strait Access Technologies, estas válvulas cardíacas se crearon como una forma de reemplazar las válvulas en una población cada vez más anciana. Los investigadores decidieron crear la válvula con silicona, ya que es compatible con el cuerpo humano. Además, mediante el uso de la impresión 3D, podrían hacer una válvula que se adapte más al paciente. Cabe señalar que, aunque los resultados iniciales fueron prometedores, estiman que pasarán otros 10 años antes de que estas válvulas puedan estar realmente en el mercado.
Los implantes restauradores de AB Dental
AB Dental utiliza la sinterización selectiva por láser (SLS) para crear sistemas de implantes personalizados. Así pretende revolucionar la tecnología y las aplicaciones en el campo oral-maxilofacial. El sistema de la empresa permite a los médicos planificar tratamientos de restauración dentales y faciales con más precisión en comparación con los métodos tradicionales. La compañía ofrece varios implantes restauradores impresos en 3D para pacientes, incluyendo el aumento del techo del seno, la reparación del hueso orbitario y un implante subperióstico para maxilares reabsorbidos.
Una retina artificial de carbono impresa en 3D
Además de utilizar la impresión 3D en la traumatología, también se puede implementar en las retinas. En este caso, un ingeniero australiano desarrolló una retina artificial impresa en 3D hecha de carbono para ayudar a las personas a ver de nuevo. El Dr. Matthew Griffith de la Universidad de Sydney hizo un gran avance cuando se dio cuenta de que un cuerpo es solo un semiconductor basado en carbono, como un ordenador. Con esta idea, determinó que podía replicar un ojo creando un dispositivo de carbono (y por lo tanto totalmente biocompatible) que absorbía la luz y luego creaba una carga electrónica, exactamente como un ojo. Además, gracias a la impresión 3D, le fue totalmente posible diseñar él mismo esta retina artificial. Aunque el dispositivo aún no está terminado y ni siquiera se someterá a estudios clínicos hasta los próximos años, Griffith tiene la esperanza de que sea útil para los pacientes que han perdido la vista. Espera incluso que permita la restauración de la visión a color que a día de hoy no es posible.
Particle3D imprime implantes óseos
Con el lema de marca registrada «We Print Bone», Particle3D fue fundada en 2014 por un profesor y dos estudiantes de ingeniería médica con el objetivo de desarrollar una nueva solución para reemplazar huesos destruidos o extirpados quirúrgicamente. En la actualidad, Particle3D sigue desarrollando implantes óseos personalizados para cada paciente basados en la propia tomografía computarizada o resonancia magnética del paciente. Esto da como resultado implantes impresos en 3D que proporcionan una arquitectura interna única similar al hueso que contiene micro y macro porosidades, al igual que el hueso real.
Un implante para combatir la osteoartritis y el dolor articular
En humanos y perros, encontramos una pequeña capa de cartílago que preserva las superficies de las articulaciones y permite que los huesos se muevan correctamente. Con el tiempo, este cartílago se descompone, lo que produce osteoartritis y, por lo tanto, dolor en las articulaciones. Para combatir esto, investigadores de la Universidad Estatal de Carolina del Norte desarrollaron un implante textil que contiene cartílago derivado de las células madre del paciente. Este tipo de implantes, parcialmente impresos en 3D, han sido probados con éxito en un grupo de perros con problemas de cadera. Este grupo se dividió en dos, y una parte recibió el implante y la otra no. Aquellos perros que recibieron el implante recuperaron toda su potencial movilidad en los 4 meses tras la operación.
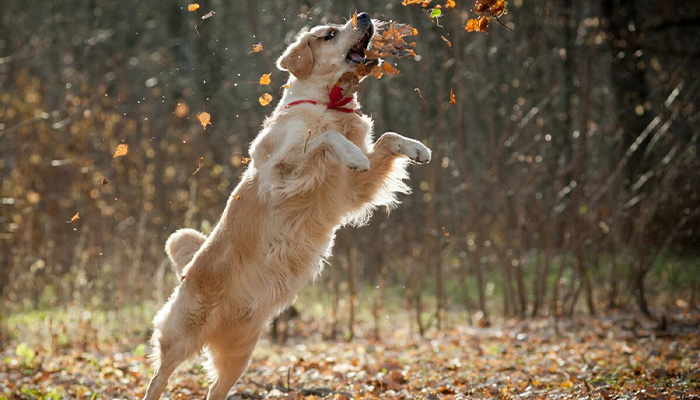
Créditos de las fotos: Deposiphoto
El implante craneal impreso en 3D más grande del mundo
La startup Arcomedlab ha logrado la proeza de crear el mayor implante craneal del mundo mediante impresión 3D. Desde su creación, Arcomedlab ha tratado más de 600 casos clínicos reales, especializándose en la reconstrucción craneal con implantes personalizados, así como en reconstrucciones faciales. Además, han llevado a cabo diversos procedimientos complejos de planificación quirúrgica. En la actualidad, la startup es capaz de reconstruir por completo el cráneo de pacientes de todas las edades, así como cualquier estructura ósea facial, utilizando las tecnologías de impresión 3D FDM y SLA con fines médicos. Gracias a estos avances tecnológicos, están ampliando los límites de la medicina reconstructiva y ofreciendo soluciones innovadoras adaptadas a las necesidades específicas de cada paciente.
El proyecto de investigación ELAINE
En el proyecto de investigación ELAINE (implantes eléctricamente activos), investigadores de la Universidad de Rostock trabajan en el desarrollo de estructuras bioactivas de sustitución ósea. Actualmente se utilizan implantes de titanio, pero son difíciles de adaptar a las condiciones anatómicas del cuerpo y además pueden aflojarse con facilidad, lo que acarrea problemas a largo plazo. Para superar estas dificultades y tratar mejor los defectos óseos, los científicos se centran en la fabricación aditiva. Están desarrollando implantes eléctricamente activos que se comportan de forma similar a las estructuras óseas naturales y se basan en la fisiología del hueso. El material que utilizan es titanato de bario, una cerámica piezoeléctrica que libera iones cuando entra en contacto con fluidos corporales. El proceso LCM utilizado (fabricación de cerámica basada en la litografía) pertenece a la familia de las técnicas de fotopolimerización. En este proceso, los polímeros se cargan con partículas piezocerámicas y se colocan en la impresora, donde se crea una estructura de filigrana mediante fotopolimerización. Esto confiere al material su biocompatibilidad. La impresión 3D también ofrece la ventaja de poder fabricar implantes personalizados. El proyecto está aún en fase de investigación y es posible que los implantes se utilicen clínicamente dentro de unos diez años.
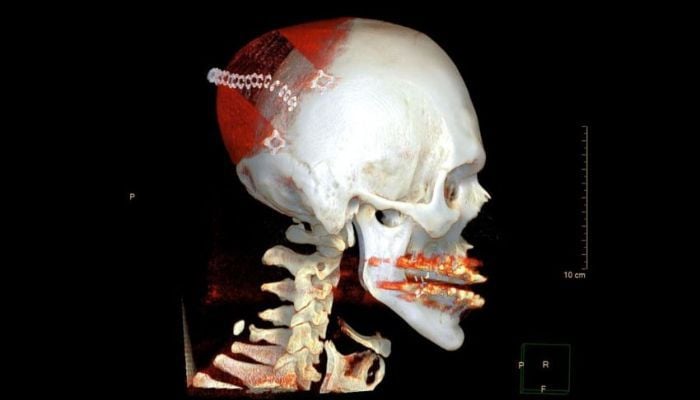
En el futuro, la impresora 3D podría fabricar implantes más grandes, por ejemplo para reconstruir el cráneo. Créditos: Universidad de Salzburgo
El injerto nasal bioimpreso «MyBone»
Una colaboración entre el Hospital Universitario de Toulouse, el Instituto Claudius Regaud y la empresa belga CERHUM permitió reconstruir con éxito la nariz de una paciente de cáncer mediante impresión 3D en 2022. El procedimiento consistió en la creación de un implante biocerámico personalizado, denominado «MyBone», que imita el hueso humano y favorece la osteointegración y la osteoconductividad. Tras un escaneo detallado de la cara de la paciente, el implante se imprimió en 3D mediante estereolitografía. Colocado inicialmente en el antebrazo de la paciente para favorecer la vascularización y colonización celular, proceso en el que las células crecen en la estructura del implante, la nariz se trasplantó después a la cara de la paciente, donde se conectó a sus vasos sanguíneos mediante microcirugía. Este método proporcionó un alto nivel de biocompatibilidad y durabilidad, al tiempo que redujo el riesgo de infección y la necesidad de futuras sustituciones. La intervención permitió trasplantar con éxito una nariz totalmente funcional y estéticamente agradable, lo que pone de relieve el potencial de la impresión 3D en las cirugía reconstructivas mayores.
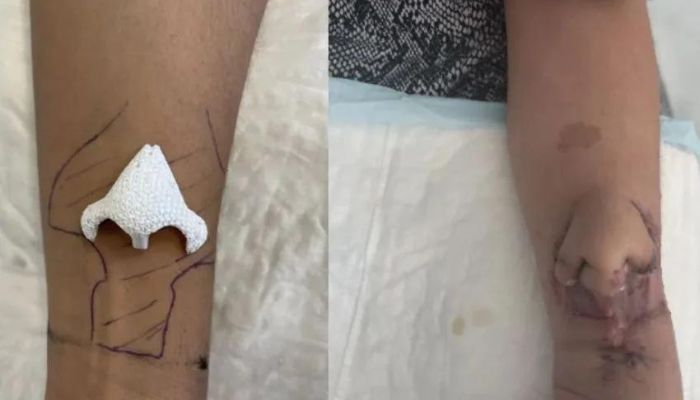
Créditos: Hospital Universitario de Toulouse
BellaSeno: implantes mamarios impresos en 3D
La empresa BellaSeno fabrica implantes mamarios de policaprolactona, un material de sutura muy utilizado en el sector sanitario, mediante impresión 3D. Estos implantes mamarios impresos en 3D son adecuados para personas que padecen cáncer de mama u otras enfermedades mamarias y se utilizarán en el futuro en cirugía reconstructiva y plástica. BellaSeno ha desarrollado una solución de impresión 3D que admite materiales clínicamente compatibles. Los implantes deberían absorberse por completo en cinco años y ser sustituidos por células grasas del organismo. Tras las diez primeras pruebas en pacientes, los resultados muestran valoraciones positivas. Las pacientes expresaron su satisfacción y los implantes 3D presentaban un buen perfil de seguridad. Los cirujanos también valoran favorablemente los implantes impresos en 3D.
Un implante para reparar el cartílago de la rodilla
La misión de Nanochon es facilitar la sustitución y reparación del cartílago en pacientes que sufren lesiones de rodilla. Para lograr este objetivo, la empresa está utilizando la tecnología de impresión 3D, en particular la técnica de extrusión, para crear un implante que sustituya al cartílago dañado o perdido. El dispositivo, denominado Chondrograft™, está fabricado con un innovador material compuesto biocompatible que favorece la regeneración del tejido. El Chondrograft™ se produce de forma aditiva mediante el proceso de fabricación de filamentos fundidos, utilizando el material compuesto patentado de Nanochon. Lo que diferencia a este implante es su estructura única: además de su microestructura visible, presenta una porosidad sub-micrónica. Tras el tratamiento posterior, esta característica hace que el implante sea más flexible y maleable, al tiempo que mantiene su integridad estructural.
El implante de médula ósea de Matricelf
En 2022 la empresa israelí de medicina regenerativa, Matricelf, probó con éxito implantes de médula espinal impresos en 3D. Los implantes se probaron en ratones con parálisis crónica prolongada y los resultados mostraron un 80% de éxito en la recuperación de la capacidad de caminar. La tecnología que ha desarrollado Matricelf comienza con una biopsia tomada del tejido del epiplón del paciente. La biopsia del epiplón se somete a un proceso de descelularización patentado que da lugar a la formación de un hidrogel termorresistente, mientras que las células madre pluripotentes inducidas (iPSC) se reprograman a partir de células maduras del paciente. La experimentación ex vivo de las iPSC dentro del hidrogel termorresistente conduce a la generación de implantes neurales funcionales y específicos para cada paciente, capaces de unir el tejido medular lesionado. Aunque solo se conocen pruebas en ratones, los científicos confían en que estos implantes podrían cambiarle la vida a miles de personas con lesiones medulares en todo el mundo, causadas principalmente por accidentes de tráfico, caídas y deportes. Las investigaciones continúan y están en proceso de solicitud de patente en EE. UU. y Europa para lograr implantarlos en humanos.
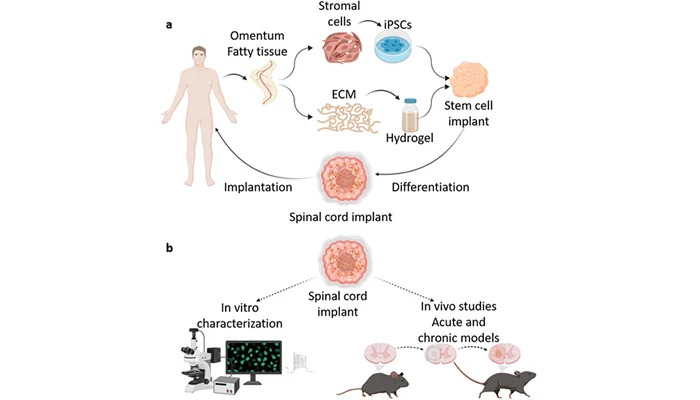
Créditos: Matricelf
El reemplazo de tobillo impreso en 3D
El Centro de Reconstrucción de Extremidades de la Universidad Macquarie ha mejorado notablemente la cirugía de sustitución de tobillo gracias al uso de implantes impresos en 3D, que ofrecen un alivio significativo y la recuperación de la movilidad a pacientes con artritis grave de tobillo o deterioro articular inducido por traumatismos. Estos implantes, fabricados con materiales sintéticos como la hidroxiapatita, imitan la estructura ósea natural y facilitan la osteointegración, garantizando la durabilidad a largo plazo y reduciendo el riesgo de complicaciones postoperatorias. A diferencia de las fusiones y prótesis de tobillo tradicionales, que limitan la movilidad y pueden provocar más problemas articulares, estos implantes de sustitución impresos en 3D preservan el movimiento de la articulación y alivian el dolor. El procedimiento, dirigido por los cirujanos ortopédicos Dr. Tim O’Carrigan y Dr. Mustafa Alttahir desde 2022, se basa mucho menos en la inserción de tornillos de tobillo y la eliminación de cartílago articular, lo que resulta en una recuperación más rápida con una mayor movilidad.
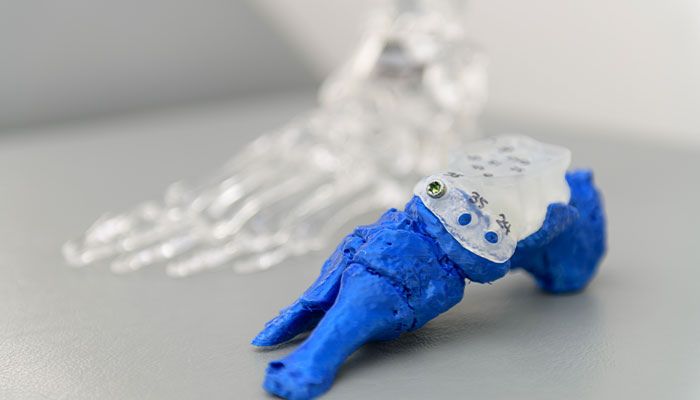
Créditos: Universidad Macquarie
Primer cráneo impreso en 3D para un niño
A finales de 2023, Félix, un niño de 10 años, sufrió un accidente en el que un trozo de metal le golpeó la cabeza y se le incrustó en el cráneo. Esto le redujo la visión e, incluso después de una operación de urgencia, su cráneo estaba prácticamente destruido. Los médicos del Hospital Regional de Salzburgo imprimieron en 3D la calvaria (parte superior del cráneo). El reto era que los médicos no conocían el estado previo del cráneo y solo podían orientarse con imágenes de TAC. A pesar de ello, consiguieron completar el implante de la calvaria a partir de PEEK en cinco días e insertarlo en una operación. Es la primera vez que se utiliza un implante fabricado con una impresora 3D en un niño. El implante de PEEK no debería causarle ningún problema y debería permanecer en su cuerpo durante muchos años. El implante solo tendrá que ser sustituido por un modelo más grande cuando el niño crezca.
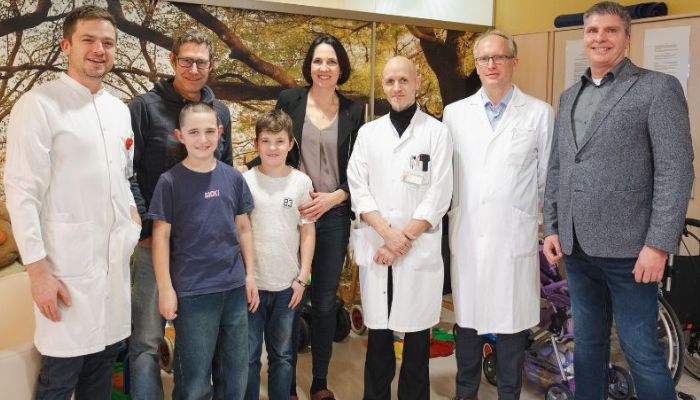
Félix (con camiseta azul), rodeado de su familia y los médicos de SALK, recibió un casquete PEEK impreso en 3D tras un accidente. (Créditos: Salk / Leon Bernhofer)
¿Qué piensas de los implantes impresos en 3D para la medicina personalizada? Deja tus comentarios en nuestras redes sociales: Facebook, Twitter, Youtube y RSS. Sigue toda la información sobre impresión 3D en nuestra Newsletter semanal.
[…] Fuentes: 3Dnatives […]