Specialized optimiza la comodidad de los sillines de bicicleta con impresión 3D
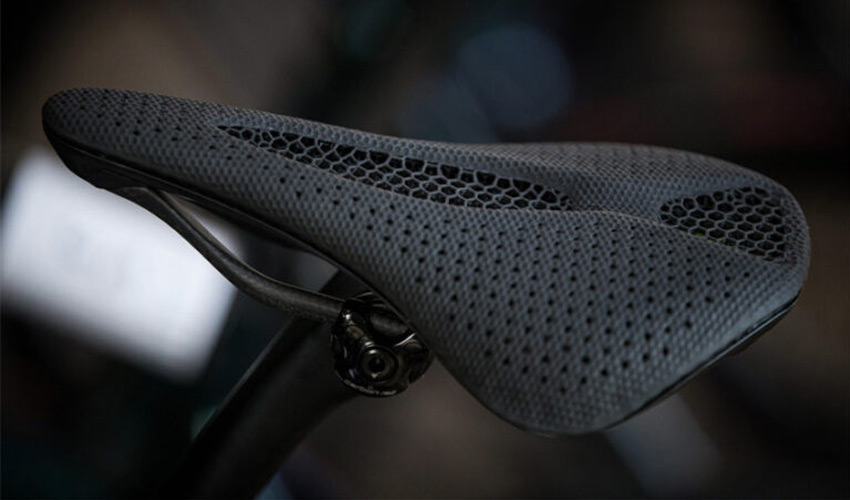
El sillín es una de las partes más importantes de una bicicleta, y juega un papel clave en la comodidad del ciclista en todos los niveles. Para los fabricantes de componentes para bicicletas, el desafío es diseñar un sillín que pueda maximizar el rendimiento del ciclista al tiempo que brinda comodidad y estabilidad. Es por eso que Specialized Bicycle Components Inc, comúnmente conocido como Specialized, se asoció con Carbon para crear el primer sillín de bicicleta impreso en 3D. El fabricante californiano anunció la disponibilidad comercial de este nuevo producto el pasado verano. Con una compleja estructura de malla elastomérica que supera las limitaciones de la espuma, el sillín S-Works Power con tecnología Mirror mejora el rendimiento, la protección y la comodidad del ciclista. Nos reunimos con Garrett Getter, gerente de productos especializados, y Emma Boutcher, gerente de productos asociada, para obtener más información sobre la integración de tecnologías de impresión 3D en su proceso de producción.
3DN: ¿Puedes presentarte y explicar tu conexión con la impresión 3D?
Garrett: Hola, soy el gerente de producto de sillines en Specialized Bicycle Components. Descubrí la impresión 3D mientras desarrollaba S-works Power Saddle con tecnología Mirror. Fui el manager detrás de este sillín desde su principio. Solo comencé a trabajar en este proyecto uno o dos meses después de unirme a Specialized.
Emma: Hola, mi nombre es Emma y soy directora asociada de productos en Specialized. Estudié ingeniería, por lo que incluso antes de unirme a Specialized tuve todo tipo de experiencias con la impresión 3D. Me asignaron un puesto técnico y tuve la oportunidad de utilizar la impresión 3D por primera vez para la creación de prototipos de sillines. Después de adquirir esta experiencia, pude comenzar la fabricación preliminar de lo que ahora se ha convertido en un sillín optimizado.
3DN: ¿Por qué Specialized eligió la tecnología 3D para diseñar sillines?
Emma: Para cuando Garrett se unió al equipo, Specialized ya había intentado probar la teoría del uso de compuestos elastoméricos de carbono para hacer un sillín de bicicleta. Lo que ahora es la parte impresa en 3D del sillín era, tradicionalmente, espuma. Es cierto que ha habido crecientes mejoras en este con diferentes materiales, pero han alcanzado un tope en términos de lo que pueden hacer y cómo las formas pueden ser específicas y dirigidas. Con la impresión 3D convirtiéndose en una herramienta para la producción en masa, no solo para la creación de prototipos, pensamos que sería una excelente opción para ser un reemplazo viable a la espuma. Luego hubo muchas pruebas, ajustes y muchas iteraciones de los modelos.
3DN: ¿Cuáles son las ventajas de la fabricación aditiva en estas aplicaciones?
Garrett: Los beneficios reales de la tecnología de impresión 3D para nuestras aplicaciones comienzan con la libertad de diseño y la velocidad de iteración. Para hacer grandes sillines de bicicleta, es muy importante que tengamos la capacidad de iterar rápidamente. Dadas estas dos oportunidades que ofrece la fabricación aditiva, esto es un sueño hecho realidad. Uno de los mayores desafíos en la actualidad, con las espumas tradicionales, es el tiempo que lleva iterar. Tienes una muestra del producto, le pides al ciclista que lo pruebe, recibes comentarios y luego le pides a la fábrica que haga un cambio, ya sea la densidad o la forma de la espuma. Estas dos etapas del proceso de producción pueden llevar mucho tiempo. Con la impresión 3D, puedes hacer todo esto mucho más rápido. La fabricación aditiva nos permite acelerar el desarrollo de productos de una manera que nunca antes habíamos experimentado.
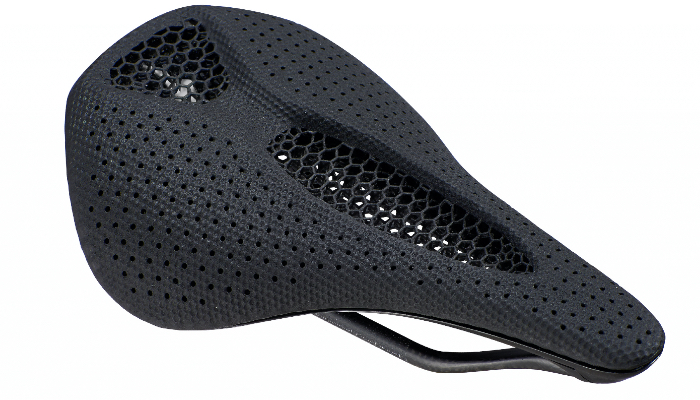
Créditos: Specialized
Otra ventaja es que, incluso durante la fase de prueba del producto, tenemos un sillín que ya está bastante cerca de la versión final, mucho antes del lanzamiento real del producto. Tradicionalmente, nuestro proceso de creación de prototipos no ha sido tan preciso. Hoy, gracias a la impresión 3D, incluso cuando todavía estamos en la fase de prototipos, ya tenemos una representación muy precisa del producto final, de hecho tenemos un modelo listo para la producción en masa.
Emma: Con el modelo del sillín final pudimos comenzar a dividirlo por zonas. Al diseñar y manipular una estructura de celosía con un nivel de detalle tan pequeño, podemos lograr una mayor precisión de áreas y diferentes densidades, porque en un sillín no buscamos uniformidad en toda la longitud del sillín, que suele ser el caso de un sillín de espuma. Por lo tanto, gracias a la impresión 3D, podemos crear, en un mismo modelo, varias zonas diferentes en términos de densidad y conformidad, para brindar apoyo al ciclista donde lo necesita.
3DN: ¿Qué desafíos enfrentó tu equipo al diseñar el producto?
Garrett: Para nosotros, la impresión 3D es un arma de doble filo, porque esta tecnología ofrece posibilidades y potencial ilimitados, ¡y se puede hacer mucho con ella! Sin embargo, intentar crear un buen producto a partir de muchas ideas diferentes puede resultar difícil. Hemos realizado una serie de iteraciones en un corto período de tiempo, y el desafío es realizar un seguimiento de lo que está cambiando y asegurarse de que se está yendo en la dirección correcta.
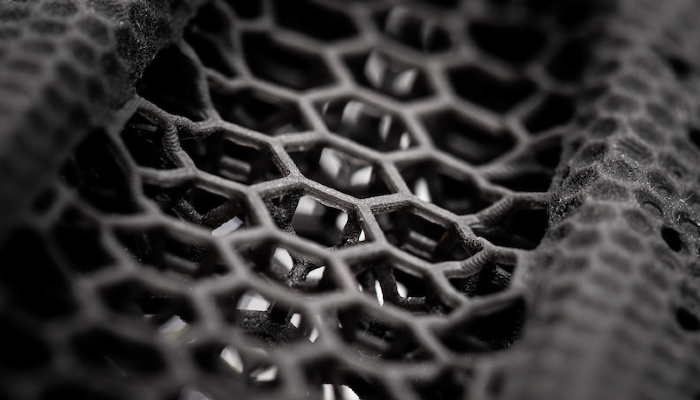
La estructura del sillín | Créditos: Specialized
3DN: ¿Puedes contarnos más sobre la colaboración con Carbon?
Emma: Hemos optado por asociarnos con Carbon para obtener acceso a materiales y procesos de impresión 3D de alta tecnología. Además, ya contaban con una red que podría ayudarnos a incrementar la producción. También tienen excelentes capacidades de diseño interno. Carbon estaba tan interesado en crear un gran producto como nosotros. Me encanta la forma en que invierten en el diseño de productos utilizando sus impresoras 3D y materiales.
3DN: ¿Cuál es tu visión de la impresión 3D en el campo de la producción de sillines?
Garrett: Intentamos constantemente encontrar nuevas formas de personalizar el producto. Fuimos los primeros en establecer una correlación entre la morfología del ciclista y el ancho del sillín. Fue el primer paso en el negocio de la producción de sillines personalizados, ya que este producto permite adaptarse al físico de una persona. Creemos que la personalización más progresiva será el futuro de la ergonomía del sillín, y la impresión 3D sin duda jugará un papel clave en ese sentido.
3DN: ¿Una última palabra para nuestros lectores?
Garrett: Si no pensáramos que la tecnología de impresión 3D brindaría grandes beneficios a los usuarios, no lo haríamos. Pero la impresión 3D en realidad mejora la experiencia de conducción, la hace más cómoda y segura, según las muchas críticas que hemos recibido sobre nuestro sillín de bicicleta impreso en 3D, y es por eso que creemos en esta tecnología. Creamos este producto con el objetivo de reducir la presión de los glúteos, por eso hemos desarrollado sillines con diferentes densidades y partes anatómicas, y el resultado es que la gente está más feliz en la bicicleta. Eso es todo lo que podíamos esperar.
¿Qué piensas de Specialized y su uso de la impresión 3D? Deja tus comentarios en nuestras redes sociales: Facebook, Twitter, Youtube y RSS. Sigue toda la información sobre impresión 3D en nuestra Newsletter semanal.