Schneider Electric y los beneficios de la impresión 3D DLP para crear piezas de repuesto

Schneider Electric es una empresa europea fundada en 1836, que opera a nivel mundial. Su sede en Wuhan, China, se dedica, entre otras cosas, al desarrollo y fabricación de interruptores de aire. Recientemente integraron la fabricación aditiva en su actividad para dar solución a la falta de stock en la cadena de suministro para piezas de repuesto y utillaje. Fue en el departamento de gestión de instalaciones de Schneider Electric donde apostaron por adoptar la tecnología de impresión 3D con la máquina Shape 1, de la empresa RAYSHAPE, que les permitió la fabricación de estas piezas de forma más rápida y barata. De esta forma, y desde hace más de 5 meses, Schneider Electric está aprovechando todas las ventajas que ofrece este innovador método de impresión 3D de resina.
En la industria manufacturera, las piezas de repuesto no son elementos que se fabriquen en series largas, por lo que cualquier fallo en la cadena de suministro puede afectar a toda la industria a gran escala. Aquí entra en juego la impresión 3D que, frente a otros métodos de fabricación tradicional, es un sistema mucho más rápido y barato a la hora de producir un elemento único o una serie corta. Además, con el añadido de los nuevos materiales avanzados que se están desarrollando en la industria, esto ya no es un impedimento para que las empresas la adopten en su actividad. De hecho, esto último era un aspecto importante para Schneider, ya que la mayoría de sus aplicaciones requieren materiales de alta tenacidad, pero con una precisión dimensional adecuada. Para ello, recurrieron al fabricante chino RAYSHAPE, dedicado al desarrollo de soluciones de impresión 3D DLP profesionales, incluyendo máquinas, materiales y soluciones de postratamiento.
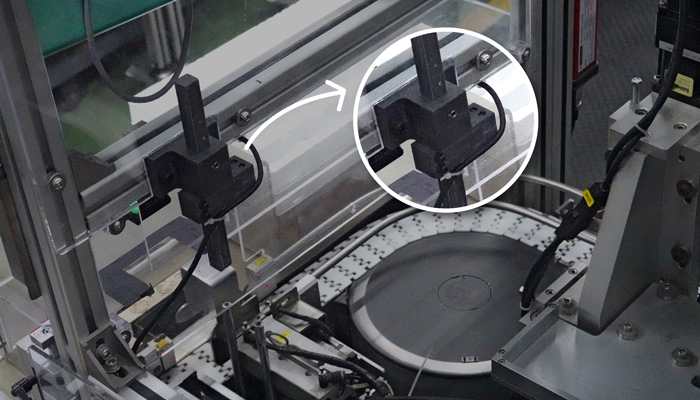
Schneider Electric ha integrado la impresora 3D Shape 1 de RAYSHAPE en su actividad. | Créditos: RAYSHAPE
Ventajas de la adopción de la impresión 3D DLP
Al integrar la fabricación aditiva de resina en su actividad, Schneider recortó tiempos de la cadena de colaboración, que requiere de ingenieros, proveedores y responsables de compras para obtener la pieza final. Gracias a la impresora 3D Shape 1 de RAYSHAPE, los ingenieros pudieron resolver el problema mediante el diseño y la impresión en 3D de las piezas de repuesto. A diferencia del mecanizado CNC, que es un método que requiere más esfuerzo y tiempo, la impresión 3D es una tecnología con la que los ingenieros de primera línea pueden resolver los problemas que surjan en el mismo día. Además, una de las grandes ventajas de esta tecnología es que puede fabricar las piezas en un solo proceso y en horas no laborales, por lo que se puede dar solución a los problemas de forma instantánea.
La Shape 1 es una impresora 3D de escritorio capaz de imprimir a velocidades de hasta 50mm de altura/hora con alta precisión, lo que significa que se pueden crear múltiples alturas de 10 cm al mismo tiempo. Con un volumen de impresión de 192 × 108 × 300 mm, la máquina permitió crear varias piezas impresas en 3D en unas tres horas gracias a toda la amplitud de la tecnología DLP de fotocurado. Para cumplir los requisitos en términos de materiales, RAYSHAPE recomendó a Schneider Electric utilizar la resina Pro 10. Este fotopolímero cuenta con una dureza Shore de 86D y un rendimiento mecánico equilibrado en cuanto a alta resistencia a la tracción, alta resistencia a la flexión, menor índice de deformación y baja fluencia.
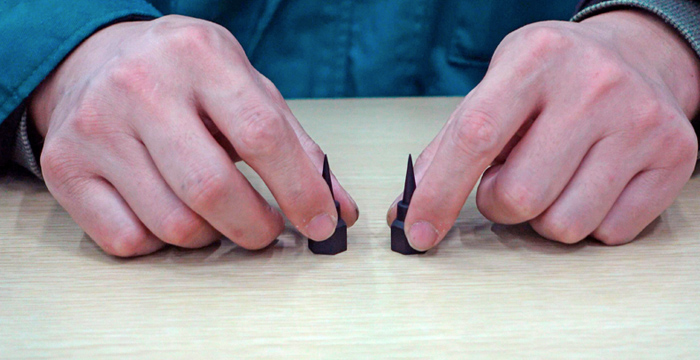
La tecnología de impresión 3D DLP permitió crear piezas de repuesto de forma más rápida y barata. | Créditos: RAYSHAPE
La ventaja competitiva de la fabricación aditiva ha ayudado a los ingenieros a tener el control de los procesos y revitalizar la pasión por la innovación tecnológica. La actividad se vuelve más eficiente, profunda y matizada. El ritmo de las líneas de producción se vuelve más manejable, los problemas dejan de ser urgentes y se resuelven eficazmente. En términos de inversión, el equipo de Schneider Wuhan afirma que llegó a imprimir en 3D más de 110 piezas en cinco meses, lo que les permitió reducir los costes en un 80% y fabricar el doble de lo que hubieran podido con otros métodos. Esto supone unas cifras muy positivas si se comparan con el mecanizado CNC. Con la impresión 3D pudieron recuperar la inversión a partir de la creación de la pieza número 100. Si quieres conocer más de cerca cómo la tecnología de RAYSHAPE permitió acelerar los procesos productivos de Schneider, puedes visitar su sitio web aquí.
¿Qué piensas de la implementación por parte de Schneider Electric de la tecnología DLP de RAYSHAPE para crear piezas de repuesto? Deja tus comentarios en nuestras redes sociales: Facebook, Twitter, Youtube y RSS. Sigue toda la información sobre impresión 3D en nuestra Newsletter semanal.
*Créditos foto de portada: RAYSHAPE