Mejorando el rendimiento de aplicaciones energéticas gracias a la impresión 3D de metal
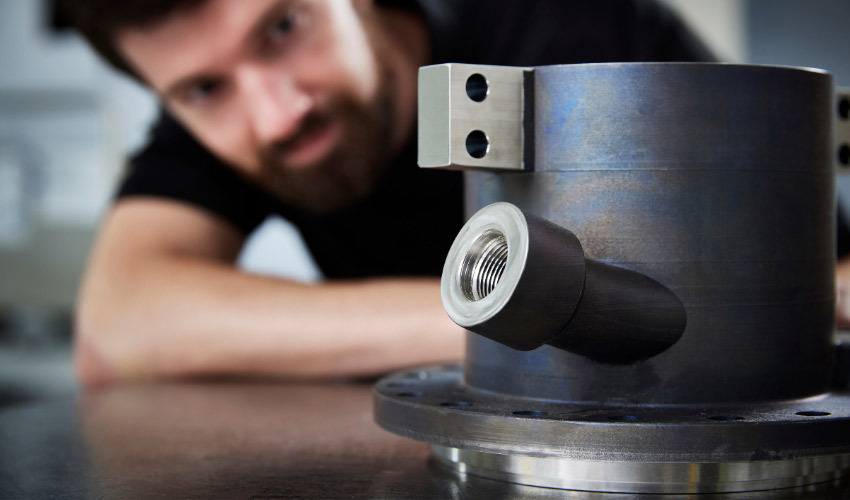
La fabricación aditiva de metal se utiliza cada vez más para desarrollar la próxima generación de turbomáquinas. Este concepto engloba las máquinas que transfieren energía entre un rotor y un fluido, incluidas tanto turbinas como compresores. Para producir diseños innovadores en este campo, sin tener que lidiar con ciclos de desarrollo largos y costosos, las empresas están invirtiendo en nuevas tecnologías. Como tal, Mohawk Innovative Technology integró recientemente la tecnología de metal de VELO3D en el diseño de su compresor para un proyecto de energía solar concentrada (CSP) patrocinado por el Departamento de Energía de EE. UU. (DOE). Fabricar el compresor con métodos tradicionales, como la fundición y la fabricación de moldes, habría llevado unas 20 semanas y habría costado más de 90.000 dólares. En cambio, Mohawk logró una pieza, de principio a fin, en tiempos de entrega más cortos, y por un precio 2,5 veces menor, gracias al rendimiento de la impresión 3D de metal.
En 1994, los cofundadores Jim Walton y el Dr. Hooshang Heshmat combinaron su experiencia aeroespacial y metalúrgica para formar Mohawk Innovative Technology Inc. La compañía desarrolla tecnología de rodamientos libres de aceite, incorporada en componentes sofisticados para energía, defensa, aeroespacial y otras industrias. Después de algunos proyectos exitosos, como el desarrollo de un compresor centrífugo hecho de metal fundido para un sistema de transporte de hidrógeno, calificaron para un nuevo proyecto patrocinado por el DOE.
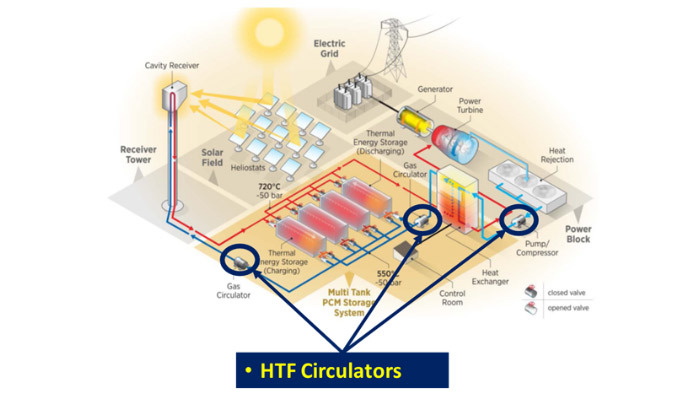
Diagrama de un sistema de energía solar concentrada (CSP), con circuladores de transferencia de calor (HTF) que incluiría carcasas de compresor similares a la diseñada por Mohawk Innovative Technology para la EERE del Departamento de Energía de EE. UU. Premio de la Oficina de Tecnología de Energía Solar (SETO) número DE ‐ EE0008374 | Créditos: DOE
En este proyecto, debían diseñar circuladores de transferencia de calor para un sistema de energía solar concentrada (CSP) que sería competitivo con la generación de energía convencional. En algunas situaciones, los sistemas CSP utilizan espejos para reflejar y concentrar la luz solar en un receptor, donde la luz se recoge y se convierte en energía térmica utilizada para producir electricidad. En este caso, la energía térmica estaba en forma de CO2 supercrítico (s-CO2), que es el estado fluido del CO2 (cuando el CO2 se mantiene a su temperatura y presión críticas o por encima de ella). Bajo presiones extremadamente altas, el s-CO2 tiene la densidad del líquido pero la viscosidad del gas. Esto lo convierte en un conductor ideal para el calor y la energía, proporcionando mucha más potencia que el vapor. También es capaz de comprimirse a través de intercambiadores de calor y almacenarse en tanques para las necesidades de energía en las horas más altas. Por ello, Mohawk comenzó a diseñar una carcasa de compresor, específicamente orientada a s-CO2. Además, su tecnología de cojinetes sin aceite encajaba perfectamente dado que el aceite es reactivo con s-CO2 y causa corrosión.
“Nuestro objetivo era ayudar a reducir el coste de la maquinaria y hacer que fueran más rentables. Un solo compresor para un sistema CSP de 100 megavatios puede costar entre $7 y $20 millones, por lo que existe una oportunidad real para que la innovación en el diseño respalde la energía alternativa. Cuando el DOE comenzó a buscar formas de abordar los desafíos del s-CO2 en las plantas de energía solar concentrada, sabíamos que podíamos brindar algunas respuestas”, explica Walton.
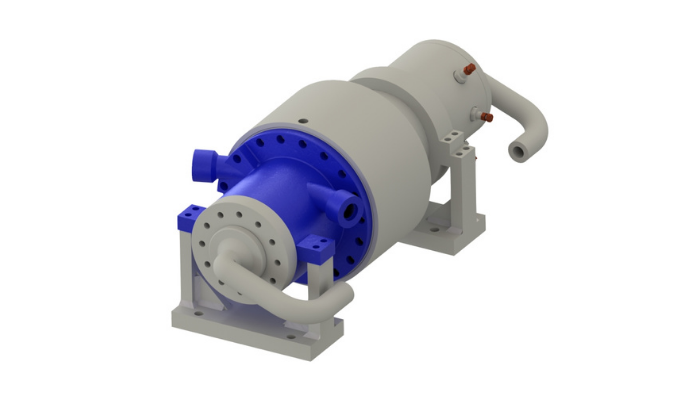
Modelo CAD de un circulador HTF para un sistema CSP diseñado por Mohawk. La parte en azul es la carcasa del compresor que se imprimió en 3D con la impresora Sapphire de VELO3D | Créditos: Mohawk Innovative Technology
La geometría compleja lleva a repensar el material y la fabricación
La carcasa no solo tenía que soportar un eje que girara libremente, también tenía que incorporar volutas (canales curvos) que proporcionaran una entrada y descarga de s-CO2 a alta velocidad a través del compresor. El ingeniero jefe, José Cordova, explica: “Para brindar tanta funcionalidad en un diseño de compresor convencional, se hubiera requerido combinar tres partes separadas. Es más, dadas las presiones sobre el s-CO2 que fluye a través de este sistema y las temperaturas extremas (de 50 a 550 ° C) a las que está sometido, sabíamos que teníamos que usar una superaleación a base de níquel como Inconel, que es difícil de lanzar”. Por lo tanto, el equipo se dio cuenta rápidamente de que no podrían fabricar esta pieza con los métodos tradicionales. Incluso los métodos de impresión 3D existentes crearían asperezas, comprometiendo la eficiencia.
Así, Mohawk decidió asociarse con VELO3D, empresa dedicada a la fabricación aditiva de metal sin soporte basada en la fusión láser de lecho de polvo (LPBF). Después de realizar pruebas de tracción exitosas en espacios en blanco de Inconel impresos en 3D, el Dr. Heshmat dio el visto bueno al proyecto. El ingeniero de aplicaciones de VELO3D, Gene Miller, explica: “Había muchos ángulos desafiantes que normalmente requerirían estructuras de soporte, lo que solo añaden compromisos al diseño y al rendimiento de la impresión 3D con metal. Nuestra tecnología proporciona la capacidad de imprimir en ángulos de cero grados sin soportes, y eso demostró ser una necesidad con las volutas internas”. Con la impresión 3D, también pudieron crear un diseño único compuesto, en lugar de combinar tres partes.
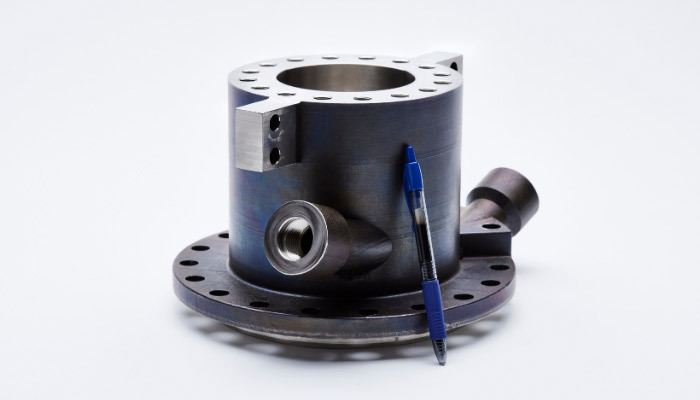
Parte de la carcasa del compresor impresa en 3D con el sistema Sapphire de VELO3D, utilizando su tecnología de fabricación aditiva de metal sin soportes.
El flujo de trabajo de VELO3D
Para configurar el diseño para la impresión 3D, el archivo se incorporó al software Flow de preimpresión de VELO3D. Una vez que se configuró en el software CAD, la pieza de Inconel se imprimió en aproximadamente 3 días y medio en el sistema Sapphire de Duncan Machine Products (el fabricante contratado para este proyecto). Además, el software Assure de VELO3D monitoreó e informó aspectos críticos en tiempo real, indicando mediciones fuera de lo nominal. El software captura puntos de datos relevantes, junto con el análisis de tendencias, en un informe de construcción integral que brinda a los usuarios información clave. Los resultados son esenciales para ganar confianza en el proceso de fabricación aditiva, razón por la cual VELO3D ha puesto énfasis en el desarrollo y la mejora de esta solución de software.
¿El futuro de las tecnologías sostenibles?
Los ingenieros de Mohawk explicaron que estaban entusiasmados con el potencial de la fabricación aditiva y creen que puede tener un gran impacto en su negocio para el futuro. Walton comenta: “La impresión 3D nos abre nuevos mercados y encaja perfectamente porque nuestra especialidad son las máquinas personalizadas. Definitivamente abre la puerta a nuevas oportunidades para la creación de prototipos rentables, así como la fabricación de piezas para sistemas personalizados”. De hecho, los ingenieros fueron capaces de no comprometer la intención del diseño, innovar más rápido y reducir los costes de fabricación, al tiempo que aumentaron el rendimiento con la impresión 3D de metal. Para obtener más información sobre la tecnología y las aplicaciones de VELO3D, puedes visitar su sitio web oficial.
Este material se basa en el trabajo respaldado por la Oficina de Eficiencia Energética y Energía Renovable (EERE) del Departamento de Energía de EE. UU. Con el número de premio de la Oficina de Tecnología de Energía Solar (SETO) DE ‐ EE0008374.
*Créditos foto de portada: Ryan Askew, ingeniero de aplicaciones en VELO3D, con la parte de la carcasa del compresor impresa en 3D de Mohawk para el proyecto del sistema de energía solar concentrada del DOE.
¿Qué piensas de la impresión 3D de metal para mejorar el rendimiento de aplicaciones energéticas? Deja tus comentarios en nuestras redes sociales: Facebook, Twitter, Youtube y RSS. Sigue toda la información sobre impresión 3D en nuestra Newsletter semanal.