Recocido VS Prensado isostático en caliente: ¿qué tratamiento térmico usar en impresión 3D?
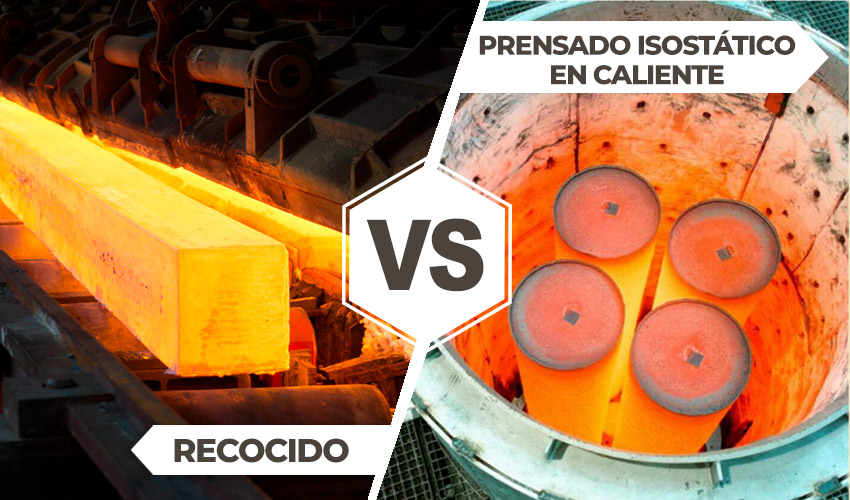
A medida que la fabricación aditiva sigue industrializándose, el postratamiento es cada vez más importante. A través de esta etapa crítica, los usuarios pueden mejorar las piezas, haciéndolas más fuertes y densas o incluso dándoles propiedades específicas. De esta forma se aseguran de que puedan ser utilizadas para aplicaciones finales avanzadas. De todos los distintos tipos de postratamiento, uno de los más importantes para la impresión 3D por lecho de polvo, especialmente en el caso de los metales, es el tratamiento térmico.
Pero, ¿qué tratamiento térmico es adecuado para una pieza? ¿Cómo funciona? Para responder a estas preguntas, hemos querido analizar dos procesos de tratamiento térmico muy utilizados: el prensado isostático en caliente (HIP) y el recocido.
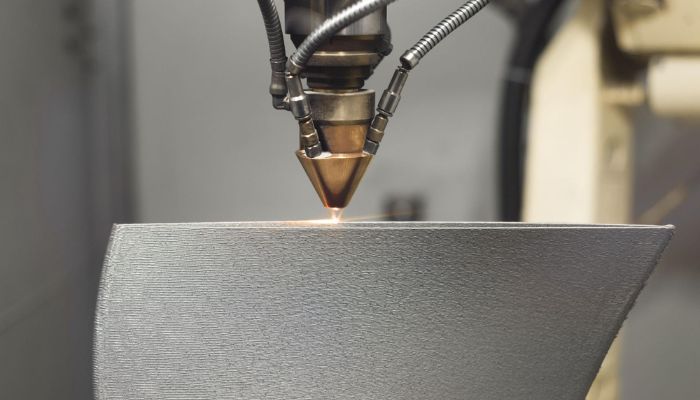
Una pieza de metal creada con fabricación aditiva. (Créditos: Industrial Metal Service)
Ambos procesos son compatibles con tecnología de metal, como LPBF, EBM, inyección aglutinante, DED e incluso inyección de nanopartículas. También pueden utilizarse con cerámicas y polímeros, aunque en distinta medida. Tienen muchas ventajas, como el refuerzo de los materiales, la facilidad para trabajar con ellos y la mejora de sus propiedades. Básicamente, estas dos técnicas optimizan los componentes, pero sus procesos y resultados difieren.
¿Cómo funcionan el HIP y el recocido?
Para entender las diferencias y similitudes entre el HIP y el recocido, a continuación, explicaremos y compararemos cada proceso. En primer lugar, el recocido es un tratamiento térmico que consiste en calentar metales, vidrio, cerámica o polímeros y dejar que el material se enfríe lentamente para eliminar las tensiones internas. Este proceso altera las propiedades físicas, y a veces químicas, de un material, aumentando su ductilidad y reduciendo su dureza para que sea más fácil trabajar con él.
El HIP, por su parte, consiste en exponer una pieza a una combinación de altas temperaturas y presiones de gas para eliminar la porosidad de los materiales metalúrgicos. También puede aumentar la densidad de muchas cerámicas, convirtiéndolas en componentes totalmente densos.
Recuerde que la «I» de HIP significa isostático. Esto se refiere al gas, que se aplica isostáticamente, lo que significa que ejerce presión por igual en todas las direcciones sobre un material. El resultado es una fuerza uniforme alrededor del objeto. Al igual que el recocido, el HIP mejora las propiedades mecánicas y la trabajabilidad del material. El proceso también puede unir materiales distintos para fabricar piezas únicas.
El proceso de recocido
El recocido se lleva a cabo, como es de esperar, en un horno de recocido. Éstos varían en función de las necesidades de los materiales y del coste, pero en general pueden calentarse entre 300°C y 1.000°C (para los modelos de gama más alta). La temperatura en el horno debe controlarse cuidadosamente, por lo que a menudo se recomiendan estos hornos de recocido. Sin embargo, si cumple los requisitos de temperatura, teóricamente podría utilizarse cualquier horno que alcance la temperatura adecuada.
El recocido consta de tres etapas, todas ellas determinadas por parámetros de temperatura que dependen del tipo de material utilizado. Para llevar a cabo el recocido, es fundamental conocer el material y sus requisitos de temperatura.
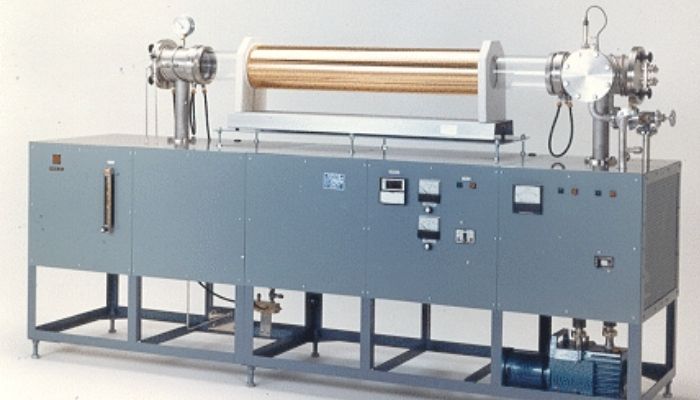
Un horno de recocido. (Créditos: Thermcraft)
1. Etapa de recuperación
En la primera fase del recocido, la temperatura del material se eleva por encima de la de cristalización para que los átomos tengan energía para moverse. El movimiento de los átomos ayuda a redistribuir y erradicar las dislocaciones (irregularidades dentro de una estructura cristalina), sobre todo en los metales. Esto hace que el metal sea más deformable y, por tanto, más dúctil. El mismo efecto puede producirse en la cerámica, pero en menor medida. En general, esta etapa alivia las tensiones internas del material.
2. Etapa de recristalización
A medida que el material sigue calentándose, acaba alcanzando la fase de recristalización. Esta se produce a una temperatura lo suficientemente alta para la recristalización, pero aún por debajo del punto de fusión. Aquí se forman y crecen nuevos granos sin deformación, que reemplazan el espacio dejado por las dislocaciones anteriores.
3. Etapa de crecimiento de los granos
Una vez completada la recristalización, la pieza puede empezar a enfriarse, entrando en la etapa de crecimiento de grano. A medida que se enfría, se desarrollan y crecen nuevos granos. Sin embargo, el crecimiento de estos granos no es aleatorio. Se controla en función de la velocidad de enfriamiento y de la atmósfera en la que se enfría.
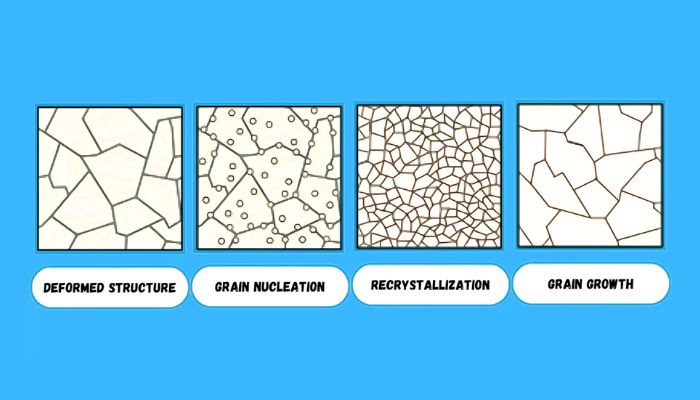
Representación gráfica de lo que les ocurre a las moléculas durante el recocido. (Créditos: MechDaily)
Dependiendo del material, el recocido puede durar desde cuatro horas hasta un día entero. Además, hay que tener en cuenta que existen varios tipos de recocido. Aunque no es una lista exhaustiva, algunos de los más utilizados son el recocido total o completo, el recocido isotérmico, el recocido de esferoidización, el recocido por difusión y el alivio de tensiones.
Las piezas impresas en 3D, o las fabricadas con materiales adecuados, pueden beneficiarse de todos estos procesos. A la hora de decidir entre distintos tipos de recocido, el material y la aplicación serán factores determinantes.
El prensado isostático en caliente
El proceso de HIP consiste en cargar las piezas en un recipiente de contención de alta presión y exponerlas a una temperatura y una presión de gas isostáticas elevadas. ¿Cómo de altas? La temperatura puede llegar a los 2.000°C y la presión a unos 310 MPa, aproximadamente la misma que la de la Fosa de las Marianas, a 11.000 m de profundidad en el Océano Pacífico. Esto hará que el material se contraiga, manteniendo su forma inicial hasta que los poros del interior desaparezcan, densificando la pieza. El proceso se utiliza ampliamente para aliviar tensiones en componentes sinterizados, fundidos y fabricados aditivamente.
El argón es el gas presurizador más utilizado para el proceso. En particular, el argón es un gas inerte, por lo que no hará reaccionar químicamente al material. El tipo de metal utilizado también puede minimizar los efectos de una reacción química. Algunos sistemas utilizan el bombeo de gas asociado para alcanzar el nivel de presión necesario. Estos gases se aplican uniformemente al objeto y se mantienen durante un tiempo determinado.
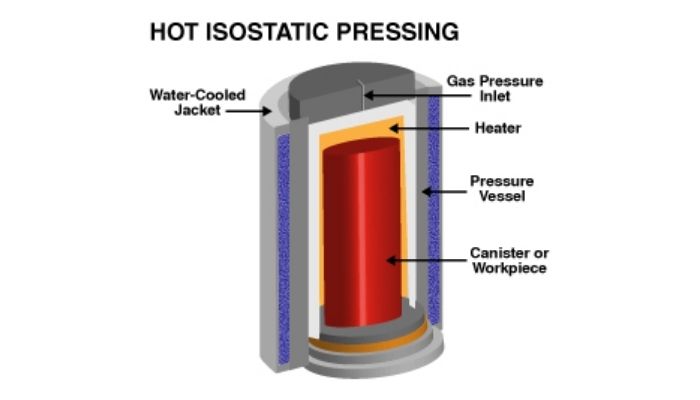
Créditos: Metal Powder Industries Federation
Los niveles de temperatura y presión del gas, así como la duración del ciclo, vienen determinados por el tipo de material utilizado y las propiedades deseadas del producto final. Los ciclos pueden durar de ocho a doce horas o días. El proceso confiere a las piezas una microestructura uniforme, lo que mejora sus propiedades.
En cuanto a los procesos de impresión 3D, Hiperbaric, líder en prensado isostático en caliente, señala que el HIP puede combinarse fácilmente con la fusión láser por lecho de polvo y el EBM para obtener piezas superiores. También son compatibles la inyección de aglutinante, el DED, la extrusión de metal y la inyección de metal (como la tecnología nanoparticle jetting).
Compatibilidad de materiales para HIP y recocido
Ya lo hemos mencionado brevemente, pero el HIP y el recocido se solapan en lo que respecta a los materiales. En concreto, ambos procesos pueden utilizarse con diversos metales. Además, no parece haber restricciones en cuanto a los metales que pueden utilizarse en ambos procesos.
El recocido es compatible tanto con materiales amorfos como cristalinos. Como tal, puede utilizarse para metales refractarios, aleaciones y acero, entre otros. El acero inoxidable se señala como uno de los materiales más utilizados para piezas recocidas, pero también se encontramos el bronce, el aluminio, el cobre y el latón.
En el HIP, todos los metales parecen ser compatibles. Esto significa que también funciona con la mayoría de los procesos de impresión 3D de metal y sus materiales asociados. Incluso puede utilizarse con metales difíciles de trabajar, como las superaleaciones de níquel y las aleaciones de titanio.
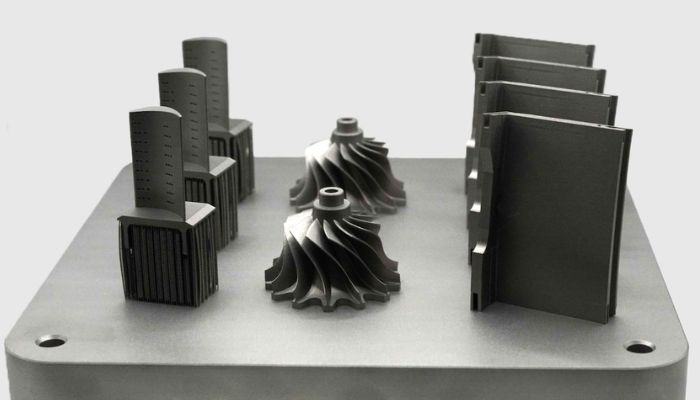
Ejemplo de superaleación de níquel impresa en 3D. (Créditos: Alloyed Aubert & Duval)
Sin embargo, los metales no son los únicos materiales compatibles. Las piezas de cerámica también se pueden postratar con HIP o recocido. Siempre que se respeten las propiedades del material, todas las cerámicas serían compatibles con cualquiera de los dos procesos.
El recocido destaca por su compatibilidad con la mayoría de los polímeros. Dado que el recocido no implica presión, sino que está relacionado con cambios de temperatura, muchos polímeros utilizados en la fabricación aditiva pueden ser recocidos. De hecho, el recocido se ha citado a menudo como una forma de mejorar la resistencia de las piezas de ABS. Otros materiales estándar que no tienen las mejores propiedades, como las piezas de PLA y PETG, están siendo recocidos cada vez más incluso por los fabricantes. Este no es necesariamente el caso del HIP.
El prensado isostático en caliente de polímeros es un área menos desarrollada, especialmente en la fabricación aditiva. Sin embargo, algunos investigadores han descubierto que, si se baja la temperatura, en un proceso conocido como warm isostatic pressing (WIP), materiales como el nylon o el HPP pueden postratarse con este método. Sin embargo, normalmente se trataría de un caso atípico, sobre todo teniendo en cuenta el coste del HIP en comparación con el recocido. Este método es más adecuado para aplicaciones y materiales industriales.
Beneficios y limitaciones de ambas técnicas
Aunque el recocido y el HIP implican procesos diferentes, las ventajas son similares. Ambos mejoran la ductilidad y eliminan las imperfecciones del material, ya sean poros (HIP) o dislocaciones dentro de la estructura cristalina (recocido). El recocido y el HIP eliminan esencialmente los defectos y las tensiones internas y mejoran la homogeneidad microestructural y las propiedades del material. Los dos procesos permiten también consolidar los pasos, ya que muchas piezas impresas en 3D requieren de todos modos un tratamiento térmico para reducir las tensiones residuales.
El recocido, al hacer que las moléculas migren dentro de la microestructura, elimina las tensiones que puedan haberse introducido durante el conformado del material. El proceso también evita la formación de grietas y mejora la maquinabilidad. Además, al rectificar las dislocaciones de la red cristalina del metal, mejora su conductividad eléctrica y sus propiedades magnéticas. El recocido permite manipular con precisión un material para obtener los rasgos deseados mediante el calentamiento y el enfriamiento selectivos y, por tanto, obtener el tipo de grano deseado, lo que influye en las propiedades físicas del material.
El HIP es excelente para aumentar la densidad de un material porque el proceso forma uniones metalúrgicas entre distintos materiales mediante la unión por difusión. Estas mejoras son fundamentales para aplicaciones que requieren gran resistencia y fiabilidad. El método también puede reparar defectos en un material. Por ejemplo, una pieza metálica con un agujero interior podría someterse a HIP, de modo que el agujero se rellena con material comprimido. En general, tanto el HIP como el recocido pueden ayudar a minimizar el desperdicio porque pueden mejorar el material existente, asegurando que durará más y reduciendo la necesidad de adquirir más material.
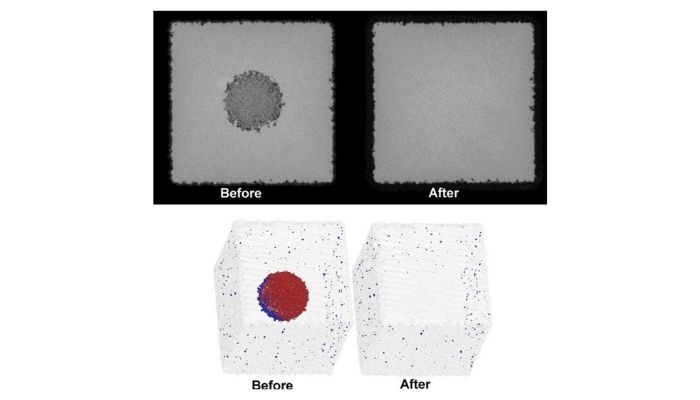
Representación del antes y el después de un material sometido a HIP. (Créditos: Science Direct, A. du Plessis a b, E. Macdonald)
Una desventaja tanto del prensado isostático en caliente como del recocido es el tiempo que se tarda en completar el proceso. Ambos métodos pueden tardar más de 24 horas, y el HIP en particular puede que hasta varios días. Por supuesto, ambas tecnologías también suponen un gasto añadido. Requieren costes iniciales para equipos y operarios cualificados, y luego necesitan grandes cantidades de energía para el calor. El recocido también puede implicar un enfriamiento forzado, lo que supone aún más energía. Para ambos métodos, el tiempo y el coste dependerán en gran medida del material que se utilice y del tamaño de la producción.
Por último, ambos procesos pueden afectar a las dimensiones finales de una pieza, lo que no es necesariamente una desventaja, pero sí algo a tener en cuenta. El recocido puede provocar un cambio en las dimensiones porque se modificará la microestructura del material, y esto también puede ocurrir con el HIP porque el material se está comprimiendo. El grado de cambio dependerá de factores como el material utilizado y los parámetros del proceso.
Entonces, ¿cuándo el recocido y el HIP no son la solución? Si tus piezas no requieren propiedades mecánicas mejoradas, puede que no merezca la pena pagar por estos procesos. El HIP, en particular, puede no ser adecuado si tienes una pieza con cavidades internas o canales intrincados que podrían colapsarse debido a la presión. El HIP es ideal cuando se desea que una pieza sea densa, por lo que si se trata de una pieza de fabricación aditiva que ya es totalmente densa (como una pieza de fusión de lecho de polvo láser de alta calidad), no sería necesario.
Aplicaciones del HIP y el recocido
En términos de aplicaciones, la más importante para ambos es el postratamiento general como forma de mejorar las propiedades del material en las piezas. Esto significa que, técnicamente, tanto el recocido como el prensado isostático en caliente podrían utilizarse en cualquier sector en el que las propiedades del material sean importantes. Aunque es necesario mencionar que, mientras que el HIP es relativamente inaccesible salvo a nivel industrial, el recocido puede realizarse mucho más fácilmente, lo que lo abre a un público más amplio.
Sin embargo, también hay sectores específicos en los que estos métodos de postratamiento se utilizan habitualmente. El HIP, por ejemplo, se utilizó por primera vez en un entorno comercial en la industria aeroespacial. Más concretamente, se usó para fabricar álabes de turbinas de motores a reacción. Por supuesto, en aquel momento no se trataba de piezas impresas en 3D.
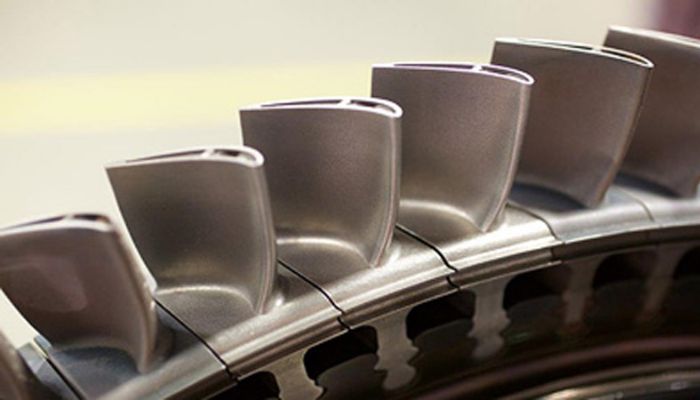
Turbina impresa en 3D. (Créditos: Siemens)
Si nos fijamos en el uso del HIP cuando se combina con la impresión 3D, hay muchos sectores en los que se observan beneficios. Por ejemplo, en el sector médico, el HIP y la tecnología L-PBF pueden utilizarse para crear prótesis de cadera y rodilla utilizando aleaciones de titanio. En el sector aeroespacial, se utilizan superaleaciones de níquel con L-BPF para álabes de turbina y CoCR para inyectores de combustible. El HIP también está presente en el sector de la automoción, ya que permite una mayor confianza en las piezas impresas en 3D. Esencialmente en cualquier lugar donde las garantías contra poros y grietas internas, a menudo presentes en las piezas impresas en 3D, serían importantes, así como la mejora de las propiedades de fatiga gracias a la eliminación de las concentraciones de tensión.
El recocido puede encontrarse en industrias similares, ya que mejora la ductilidad, elimina tensiones y reduce la dureza de los materiales. También se puede reducir la fragilidad de los metales y mejorar sus propiedades magnéticas. Por tanto, las aplicaciones en las que éstas se valoran son las que mejor encajan.
Las industrias clave para el recocido son la médica, la aeroespacial, la automovilística y la de equipos semiconductores. En el sector aeroespacial, se utiliza habitualmente para componentes de aeronaves y puede emplearse de forma similar para paneles de carrocería en el sector de fabricación de automóviles. Mientras tanto, en medicina, puede utilizarse para dispositivos médicos como implantes ortopédicos, ya que puede ser útil para formar aleaciones y metales biocompatibles con la resistencia y durabilidad requeridas. Por último, como el recocido puede mejorar la conductividad eléctrica, puede ser útil en la industria electrónica para fabricar semiconductores o células solares.
Fabricantes y precios
Para completar el recocido, no se necesita necesariamente un horno. A veces, los hornos estándar, como los de laboratorio, son adecuados, especialmente para proyectos a pequeña escala o de bricolaje, en los que no es necesaria una precisión extrema, sobre todo con polímeros. Sin embargo, en los casos en los que se necesita una gran precisión, puede ser necesario un horno de recocido específico. Entre los fabricantes de hornos de recocido se encuentran Precons, Gasbarre Products y CM Furnaces.
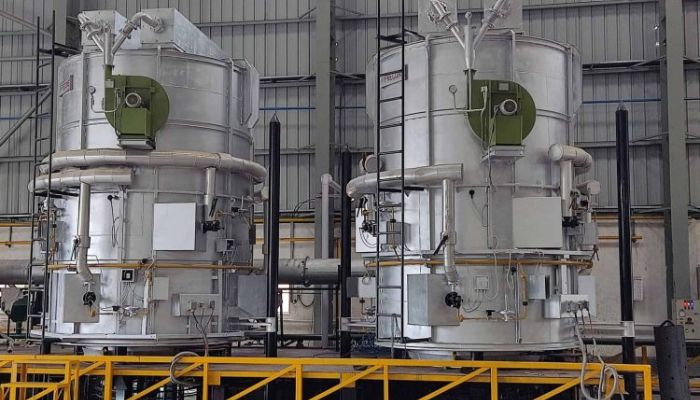
Hornos de recocido Bell. (Créditos: Precons)
A diferencia del recocido, el HIP requiere máquinas especializadas. Por ello, puedes recurrir a un servicio o comprar una máquina por ti mismo mismo. Algunos fabricantes destacados son Bodycote, Kobe Steel, Aalberts, Quintus y ESPI.
El coste del recocido y el HIP dependerá de varios factores, como el material que se utilice, la escala de su producción, los requisitos de cada aplicación y si queremos subcontratar el servicio o realizar el tratamiento internamente.
Para el recocido, los hornos de laboratorio suelen tener un precio inicial de 500$, y los hornos de recocido industriales pueden costar desde 3.000$ y hasta 100.000$. Las máquinas de prensado isostático en caliente tienen un precio similar. Las pequeñas cuestan unos 7.000$, mientras que las grandes pueden costar cientos de miles de dólares o más.
¿Qué piensas de la comparativa entre el recocido y el HIP? Deja tus comentarios en nuestras redes sociales: Facebook, LinkedIn y Youtube. Sigue toda la información sobre impresión 3D en nuestra Newsletter semanal.
*Foto de portada: Recocido (Créditos: Aria) VS HIP (Créditos: ThermalProcessing.Com)